Introduction to Biomass Boilers
Biomass fuel boilers, also known as biomass heating systems, use renewable biofuel to produce heat and hot water. Biofuel, typically wood pellets, chips, or logs, offers a cost-effective alternative to electricity, oil, and gas, making these boilers ideal for year-round use. Biomass fuel provides economic, environmental, and social benefits, including cost savings, fossil fuel conservation, and reduced CO₂ and NOx emissions.
Types of Biomass Fuel
Common biomass fuels include wood logs, chips, and pellets, along with agricultural waste, animal byproducts, and household waste. While wood pellets and chips can be fed automatically into the furnace, logs require manual loading. Biomass is recognized for being environmentally friendly, releasing minimal pollution during combustion.
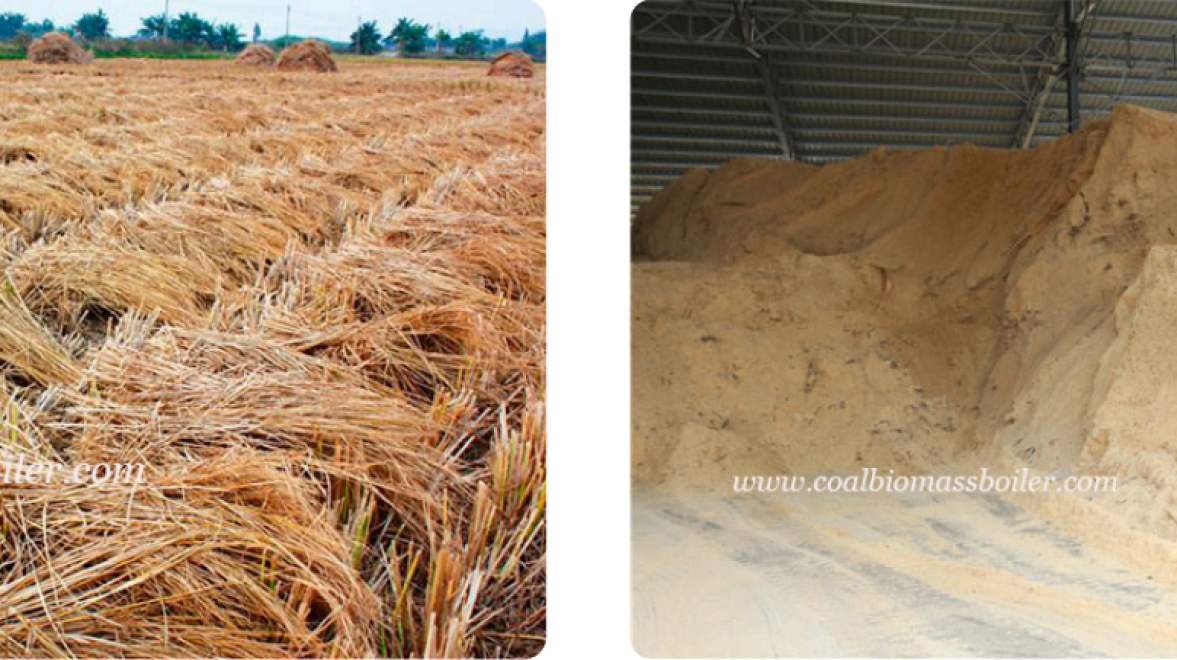
Key Operational Procedures
1.Boiler Operation Adjustment
- Ensure the evaporation rate aligns with the rated value, meeting steam turbine requirements.
- Monitor and maintain stable steam pressure, temperature, and water levels to ensure safety.
- Optimize combustion for improved efficiency and fuel savings.
2.Water Level Control
Washing the Water Gauge
- Open the blowdown valve to flush the steam pipe, water pipe, and glass tube.
- Close the water-side valve, and wash the steam pipe and gauge glass.
- Alternate between steam and water-side valves, ensuring each section is thoroughly cleaned.
- After washing, confirm that the water level rises quickly and fluctuates. If the rise is slow, repeat the process. Operators must wear protective gloves and avoid facing the gauge directly during washing.
Water Level Adjustment
- Keep the water level at the center line of the gauge, with acceptable fluctuations within ±30mm.
- The water supply rate should remain steady to prevent overfilling. Water levels beyond ±50mm are considered out of limits and require immediate adjustment.
- Regularly monitor the gauge, performing daily cleaning and calibration to ensure accuracy.
3.Steam Pressure and Temperature Management
- Rated steam pressure: 4.1 MPa, with a fluctuation range of ±0.05 MPa. Any deviation beyond these limits requires immediate action and communication with the shift supervisor.
- Normal steam temperature: 385°C, with an acceptable fluctuation range of ±5–10°C.
- Adjust combustion intensity and desuperheating water flow gradually to stabilize steam parameters. Sudden adjustments can disrupt operations.
4.Combustion Adjustment
- Regulate fuel input and air volume based on load changes to maintain stable steam production.
- Distribute fuel evenly across the grate to prevent uneven combustion and reduce the risk of coking. Ensure the fire spreads uniformly across the furnace bed.
- Keep the combustion chamber flame golden-yellow, with oxygen levels between 4–6%, and maintain a negative pressure of 10–20 Pa.
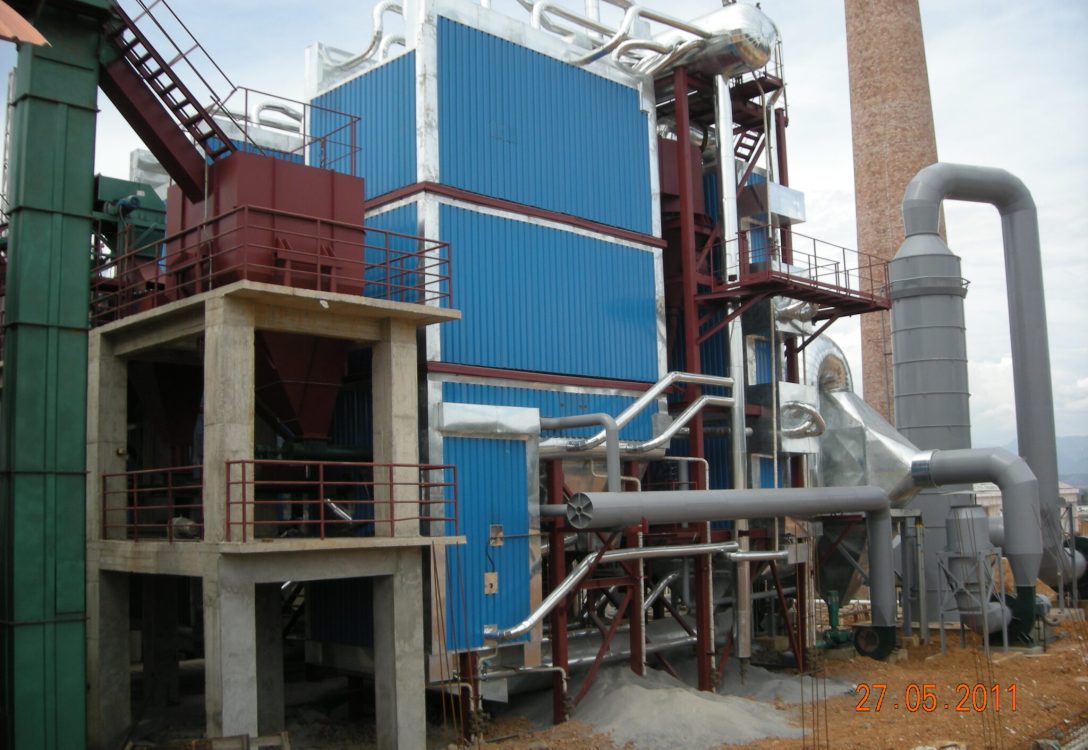
5.Boiler Blowdown Process
Types of Blowdown
- Continuous Blowdown: Removes water with high salt content from the boiler to prevent scaling.
- Intermittent Blowdown: Removes sediment from the water wall headers.
Blowdown Procedure
- Check the discharge valve before initiating blowdown, and raise the water level slightly above normal.
- Open the primary valve first, followed by the secondary valve. Once blowdown is complete, close the secondary valve, then the primary valve, following a gradual sequence to avoid water hammer.
- If pipe vibration occurs, pause blowdown until the issue is resolved. Avoid blowdown when the water level is below normal or when personnel are working near the system.
6.Rotating Machinery Maintenance
- Check for abnormal vibrations, noise, or misalignment. Ensure all protective covers are in place, and anchor screws are tight.
- Lubricate bearings regularly, ensuring oil levels are adequate. Refuel oil levelers once per shift.
- Keep bearing temperatures below 80°C, and verify that cooling water is flowing smoothly.
- Inspect transmission belts to prevent slippage or detachment during operation.
7. Operating and Maintenance of Slag Conveyor
Ensure the motor temperature stays below 80°C, and cooling water flow is stable. Check that the belt is free of red residue, and avoid reverse operation. Maintain proper oil levels by refilling when needed.
8. Maintenance of Slag Belt Conveyor
Make sure rollers are aligned and rotate smoothly. Lubricate the grate governor box and rotating parts as required. Keep the belt clear of residue and monitor the temperature of motors, bearings, and other components. Ensure the transmission belt remains in good condition without misalignment or wear.
9. Operating and Maintenance of Biomass Fuel Boiler
Regularly inspect all key components, including pressurized parts, valves, explosion-proof doors, and structural elements. Address any issues promptly. Follow the maintenance schedule for inspections and testing, log readings accurately, and ensure the operation area remains clean for safe performance.
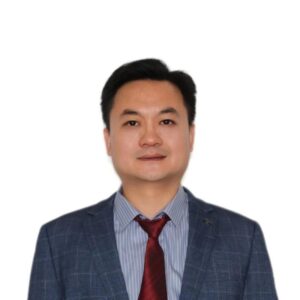