What Are the Main Advantages of an Industrial Gas-Fired Boiler Over Traditional Boilers?
Industrial operations demand heating systems that deliver high efficiency, reliability, and environmental compliance. Traditional boilers—especially those powered by coal or oil—often struggle with higher emissions, complex maintenance, and limited automation. In contrast, gas-fired boilers have emerged as a preferred solution due to their clean-burning nature, advanced technology integration, and operational flexibility. For industries focused on energy efficiency and sustainability, understanding the advantages of gas-fired boilers is critical for making the right investment.
The main advantages of an industrial gas-fired boiler over traditional boilers include higher thermal efficiency, significantly lower emissions, cleaner combustion, reduced maintenance, faster startup, and advanced automation compatibility. Gas-fired systems also support greater fuel consistency and combustion control, making them ideal for industries aiming to reduce their carbon footprint while achieving stable and cost-effective heat generation.
For industries seeking a balance of performance, compliance, and operational simplicity, gas-fired boilers offer a superior alternative to conventional systems. Let’s explore their benefits in more detail.
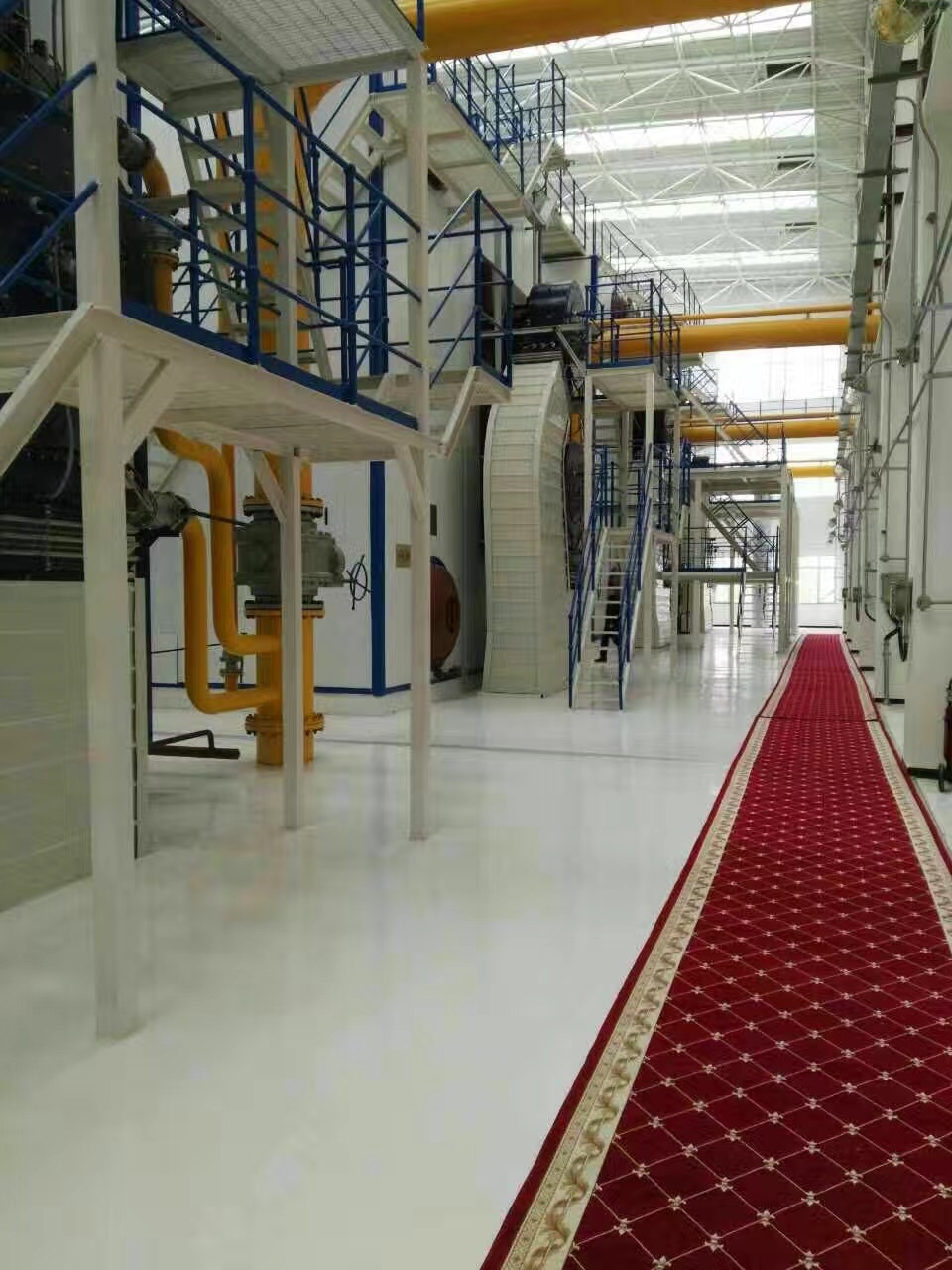
How do gas-fired boilers achieve higher thermal efficiency than traditional systems?
In modern industrial and commercial settings, achieving high thermal efficiency is not only about reducing energy costs—it’s essential for environmental compliance, operational competitiveness, and system sustainability. Traditional boiler systems, particularly those using coal, biomass, or outdated oil technologies, often lose a substantial portion of energy through hot flue gases and incomplete combustion. By contrast, gas-fired boilers, especially those equipped with condensing technology, are designed to extract more usable heat from the same amount of fuel—resulting in superior thermal performance, reduced emissions, and lower operational costs.
Gas-fired boilers achieve higher thermal efficiency than traditional systems by utilizing clean-burning fuels (like natural gas), optimizing air-to-fuel ratios through automated controls, and recovering latent heat from water vapor in flue gases via condensing technology. These features allow modern gas-fired systems to reach efficiency levels of 90–98%, compared to 70–85% for conventional boilers. The combination of complete combustion, advanced heat exchangers, and intelligent control ensures minimal energy waste and maximum steam or hot water output per unit of fuel.
This makes gas-fired boilers especially advantageous in industries where efficiency, responsiveness, and emissions control are top priorities.
Key Technologies That Improve Thermal Efficiency in Gas-Fired Boilers
Feature | Efficiency Contribution |
---|---|
High-efficiency burners | Ensure complete combustion and low excess air |
Condensing heat exchangers | Recover latent heat from water vapor in exhaust gases |
Modulating burners and controls | Adjust output to match demand and minimize cycling losses |
Oxygen trim and feedback loops | Maintain optimal air-fuel ratios in real time |
Low flue gas temperatures | Reduce stack heat loss and improve heat recovery |
Condensing Technology: The Core Efficiency Booster
In traditional boilers, flue gas exits at 150–250°C, carrying away unrecovered latent heat from water vapor formed during combustion. In a condensing gas-fired boiler, the flue gas is cooled below the dew point (~55°C), causing the water vapor to condense and release additional heat, which is captured by a secondary heat exchanger.
Heat Recovery Process:
Natural gas (primarily methane) combusts to form CO₂ and H₂O vapor.
Condensing section cools exhaust gas, recovering latent heat of vaporization.
This extra heat is transferred to the incoming feedwater.
Parameter | Non-Condensing Boiler | Condensing Gas Boiler |
---|---|---|
Flue Gas Exit Temp | 180–250°C | 40–65°C |
Efficiency (Higher Heating Value) | 80–88% | 90–98% |
Stack Loss | 15–20% | 4–7% |
Combustion Efficiency and Burner Control
Modern gas-fired boilers use premix or fully modulating burners that deliver precise fuel-air mixtures for efficient combustion. These systems minimize unburned hydrocarbons and excess air, two major sources of efficiency loss in traditional systems.
Burner Type | Description | Efficiency Benefit |
---|---|---|
Modulating Burners | Adjust flame size to match load | Reduces on-off cycling |
Low-NOx Premix Burners | Mix air and fuel before ignition | Ensures cleaner, more complete burn |
Oxygen Trim Controls | Monitor flue gas O₂ and adjust air flow | Maintains ideal combustion ratio |
Integrated Economizers and Heat Exchangers
Most modern gas-fired boilers are equipped with economizers, which recover heat from flue gas to preheat feedwater. This reduces the load on the boiler’s main heat exchanger and increases net efficiency.
Component | Role in Efficiency Improvement |
---|---|
Primary Heat Exchanger | Transfers combustion heat to water or steam |
Secondary Condensing Heat Exchanger | Recovers latent heat from flue gas |
Feedwater Economizer | Preheats incoming water to reduce burner load |
Together, these systems reduce the amount of energy required to bring feedwater to boiling point, which is one of the most energy-intensive stages in steam production.
Efficiency vs Load Profile
Unlike traditional systems, which lose efficiency at partial loads, gas-fired boilers maintain high performance across a wide turndown range.
Load Condition | Traditional Boiler Efficiency | Gas-Fired Boiler Efficiency |
---|---|---|
100% Load | 80–85% | 95–98% (condensing) |
50% Load | 65–75% | 90–95% (with modulating control) |
25% Load | 55–65% | 88–92% (minimal cycling loss) |
Environmental and Cost Benefits
Metric | Traditional Boiler | Gas-Fired Condensing Boiler |
---|---|---|
CO₂ Emissions (kg/GJ) | ~95–100 | ~50–55 |
Fuel Use per Output Unit | Higher | ~10–20% lower |
Maintenance Frequency | More (due to fouling/soot) | Less (clean combustion) |
NOx Emissions | High (requires SCR/SNCR) | Low with low-NOx burner |
Operating Cost | Higher (per kWh of heat) | Lower due to high efficiency |
Real-World Example: Gas-Fired Upgrade in Textile Factory
A textile dyeing facility replaced three aging 3 TPH coal-fired boilers with two 2.5 TPH condensing natural gas-fired boilers.
Results:
Thermal efficiency improved from 78% to 94.2%
Fuel cost dropped by 18% annually
Boiler room floor space reduced by 30%
CO₂ emissions reduced by 21%
The system was integrated with a central control platform and supported variable steam demand, making it ideal for the factory’s production cycles.
Summary: Why Gas-Fired Boilers Are More Thermally Efficient
Efficiency Driver | Description |
---|---|
Complete Combustion | Clean-burning fuel with minimal unburned waste |
Condensing Heat Recovery | Captures latent heat from exhaust gas |
Advanced Burner Modulation | Matches output with demand without cycling |
Flue Gas Heat Utilization | Economizers and preheaters reduce energy losses |
Low Excess Air Operation | Minimizes dilution and stack temperature |
Gas-fired boilers, especially condensing models, maximize every calorie of input energy. Their high turndown capability, low emissions, and simplified controls make them the standard for high-efficiency industrial heating and steam systems in the 21st century.

In what ways do gas-fired boilers reduce emissions compared to coal or oil boilers?
In industrial and commercial heating, environmental compliance is no longer optional—it’s a critical requirement. Emissions from boiler systems are a primary source of air pollutants such as sulfur dioxide (SO₂), nitrogen oxides (NOx), carbon monoxide (CO), particulate matter (PM), and carbon dioxide (CO₂). Traditional boilers that burn coal or oil are major contributors to these emissions, often requiring complex and expensive after-treatment systems. Gas-fired boilers, by contrast, offer a fundamentally cleaner combustion profile, reducing air pollution significantly at the source.
Gas-fired boilers reduce emissions compared to coal or oil boilers by producing significantly lower levels of particulate matter, sulfur dioxide, and carbon dioxide due to the cleaner-burning nature of natural gas. Advanced combustion technologies and low-NOx burners in gas systems further minimize nitrogen oxide formation, while the absence of solid combustion residues eliminates ash and heavy metal pollution. This makes gas-fired boilers inherently more environmentally friendly, often eliminating the need for costly emission control equipment required in coal or oil systems.
This clean combustion advantage not only meets today’s environmental standards but also future-proofs facilities against tightening air quality regulations.
Comparative Emissions: Gas vs. Coal vs. Oil
Emission Type | Coal-Fired Boiler | Oil-Fired Boiler | Gas-Fired Boiler |
---|---|---|---|
Particulate Matter (PM) | High (fly ash, soot) | Moderate (some soot, heavy oils) | Very low (negligible) |
Sulfur Dioxide (SO₂) | High (1–3% sulfur coal) | Moderate (varies by oil type) | Very low (<0.01%) |
Nitrogen Oxides (NOx) | High (thermal and fuel NOx) | Moderate (with proper control) | Low (with low-NOx burners) |
Carbon Monoxide (CO) | Moderate (incomplete burn) | Moderate | Low (complete combustion) |
Carbon Dioxide (CO₂) | Very high (highest carbon content) | High | Lower (per energy unit) |
Heavy Metals & Toxins | Mercury, lead, arsenic | Trace amounts (especially in heavy oils) | None |
Chart: Emissions per GJ of Heat Produced
Emissions (g/GJ)
|
| Coal Oil Gas
| PM ██████ ███ █
| SO₂ ██████ ███ █
| NOx █████ ███ ██
| CO ███ ██ █
| CO₂ ██████ ████ ███
Why Natural Gas Burns Cleaner
Natural gas, primarily methane (CH₄), is a hydrocarbon with:
High hydrogen-to-carbon ratio, producing more water vapor and less CO₂
No sulfur or ash content, eliminating SO₂ and particulate emissions
Stable molecular structure, enabling near-complete combustion
These properties give gas-fired boilers a distinct emission advantage at the chemical level.
Property | Gas (CH₄) | Oil (C10–C20+) | Coal (C135H96O9NS) |
---|---|---|---|
Hydrogen-to-Carbon Ratio | ~4:1 | ~2:1 | ~0.7:1 |
Sulfur Content | Negligible | 0.1–2% | 0.5–3% |
Ash Content | 0% | Traces (in heavy oils) | 5–20% |
Specific Emission Reductions with Gas
1. Particulate Matter (PM)
Gas-fired boilers produce near-zero PM, as combustion leaves no solid residue.
Coal and heavy fuel oil produce fly ash, soot, and unburned carbon particles.
2. Sulfur Dioxide (SO₂)
Natural gas contains no sulfur, so it does not generate SO₂.
Coal and high-sulfur oils may require scrubbers or desulfurization units to comply with regulations.
3. Nitrogen Oxides (NOx)
Gas systems use low-NOx burners, flue gas recirculation (FGR), or staged combustion to minimize NOx.
Coal systems require Selective Catalytic Reduction (SCR) or SNCR to achieve similar results.
NOx Control Comparison | Gas-Fired Boiler | Coal/Oil Boiler |
---|---|---|
Base NOx Emissions | Low (with premix burners) | High |
Control Equipment Needed | Minimal (often internal) | Extensive (SCR, SNCR) |
Maintenance | Low | High |
4. Carbon Dioxide (CO₂)
For each GJ of energy, natural gas emits ~50–55 kg CO₂, compared to 90–100 kg for coal.
This represents a 40–45% CO₂ reduction—key for meeting decarbonization goals.
Maintenance and Compliance Implications
Factor | Gas-Fired Boiler | Coal/Oil-Fired Boiler |
---|---|---|
Stack Cleanup Equipment | Often not required | Mandatory (ESP, baghouse, scrubber) |
Emission Monitoring System | Simple (NOx and O₂ sensors) | Complex (multi-gas CEMS) |
Permitting and Inspections | Easier | Stringent |
Operating Cost (for emissions) | Lower (fewer components) | Higher (chemical reagents, filter bags) |
Real-World Example: Food Processing Plant Conversion
A food processing plant in Southern Europe converted its 5 MW oil-fired boiler to a gas-fired condensing unit.
Before (Oil):
SO₂ emissions: 350 mg/Nm³
PM: 75 mg/Nm³
NOx: 180 mg/Nm³
After (Gas):
SO₂: <10 mg/Nm³
PM: <5 mg/Nm³
NOx: 95 mg/Nm³ (with low-NOx burner)
Result:
Compliant with EU IED standards
Eliminated use of external scrubber system
Reduced air permit complexity and insurance premiums
Summary: Clean-Burning Advantages of Gas-Fired Boilers
Emission Type | Reduction with Gas (vs. Coal/Oil) |
---|---|
Particulate Matter | 90–99% |
Sulfur Dioxide | 99–100% |
Nitrogen Oxides | 30–60% (with advanced burners) |
Carbon Dioxide | 20–45% per GJ of heat |
Heavy Metals | Eliminated |
Gas-fired boilers represent the cleanest combustion option among fossil fuels, offering superior environmental performance with minimal post-treatment requirements. For industries aiming to reduce their environmental footprint, simplify compliance, and align with net-zero targets, switching to gas-fired systems is a strategic and impactful step forward.
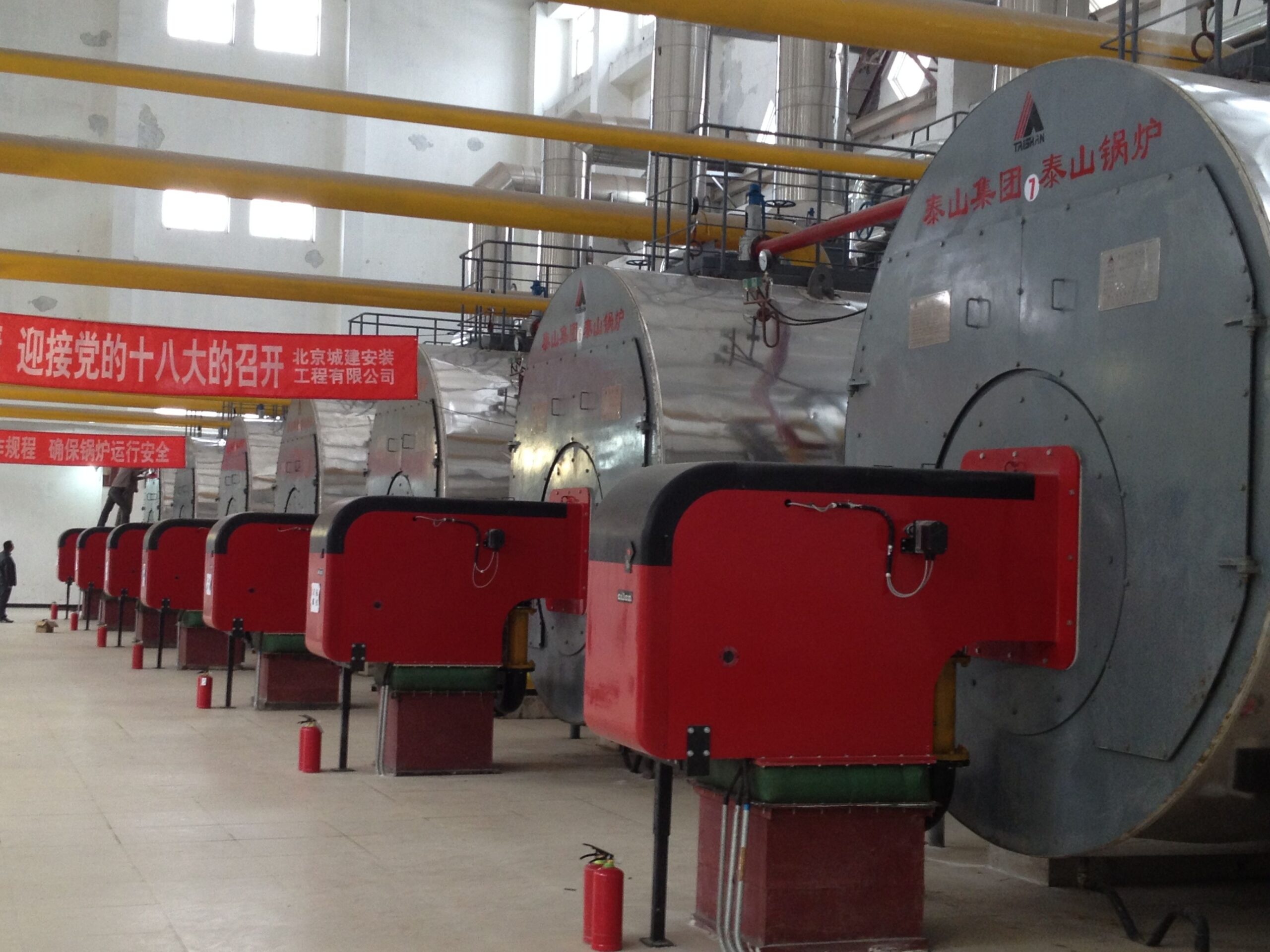
How does cleaner combustion in gas boilers impact system longevity and maintenance?
In industrial and commercial boiler operations, equipment longevity and maintenance frequency are vital to cost control and system reliability. Traditional boilers that burn coal, oil, or biomass often suffer from fouling, corrosion, and abrasive deposits due to incomplete or dirty combustion. This results in increased maintenance effort, more frequent shutdowns, and shortened component life. In contrast, gas-fired boilers—especially those burning natural gas—provide an inherently cleaner combustion process, resulting in less contamination, fewer mechanical stresses, and longer-lasting, more dependable boiler systems.
Cleaner combustion in gas boilers significantly improves system longevity and reduces maintenance needs by minimizing soot formation, preventing corrosive residue buildup, and reducing thermal stress on components. Natural gas combustion produces negligible particulate matter, virtually no ash, and low sulfur content, which keeps heat exchanger surfaces, burners, and flue passages cleaner for longer periods. This leads to fewer maintenance cycles, less wear on critical parts, extended operational life, and lower lifecycle costs.
By ensuring that internal surfaces stay clean and system parameters remain stable, gas-fired boilers become more reliable, predictable, and cost-effective across years of operation.
Key Impacts of Clean Combustion on System Durability
Area Affected | Impact of Cleaner Combustion in Gas Boilers |
---|---|
Heat Exchangers | Remain free of soot and slag, preserving heat transfer rates |
Burners | Less coking, easier ignition, longer lifespan |
Flue Gas Path | No ash deposition, reduced corrosion risks |
Boiler Tubes | Less scaling and fouling, minimizing overheating |
Fans and Dampers | Lower dust loading, reducing wear and imbalance |
Sensors and Controls | Cleaner atmosphere preserves sensor accuracy |
Comparison of Combustion Byproducts
Combustion Byproduct | Coal-Fired Boiler | Oil-Fired Boiler | Gas-Fired Boiler |
---|---|---|---|
Soot and Carbon Deposits | High (requires regular removal) | Moderate (especially with heavy oil) | Negligible |
Ash and Slag | Very high (solid residue) | Trace amounts | None |
Sulfuric Acid Mist | High (needs neutralization) | Moderate | Minimal (low S content) |
Corrosive Compounds | Chlorides, sulfates | Varies by oil grade | Very low |
Natural gas contains no ash-forming components and burns with a blue flame—indicating complete combustion with minimal residue.
Maintenance Frequency and Time Comparison
Maintenance Activity | Coal/Oil-Fired Boiler | Gas-Fired Boiler |
---|---|---|
Soot Blowing | Daily to weekly | Rarely needed |
Tube Cleaning | Monthly or quarterly | Semi-annually or annually |
Burner Inspection/Service | Monthly | Every 6–12 months |
Flue Gas Cleaning | Routine | Minimal |
Downtime for Cleaning | 2–4 weeks/year | <1 week/year |
Cleaner combustion means less frequent maintenance interventions, saving labor and reducing downtime.
Longer Component Lifespan
Gas-fired boilers experience less mechanical and chemical stress, which extends the life of key components:
Component | Lifespan in Coal/Oil Boiler | Lifespan in Gas Boiler |
---|---|---|
Burner Assembly | 3–5 years | 7–10+ years |
Refractory Lining | Wears due to slag and flame impingement | Minimal wear (cooler flame zones) |
Boiler Tubes | Risk of pitting and scaling | Reduced corrosion and erosion |
Flue Stack Internals | Corrosion from SO₂/acid dew | Clean flue reduces replacement rate |
Real-World Case Study: Commercial Laundry Facility
A laundry plant switched from an oil-fired to a natural gas-fired condensing boiler (2.5 TPH capacity):
Before:
Weekly burner cleaning
Quarterly firetube brushing
Annual tube replacement due to corrosion
2–3 days of maintenance downtime/month
After:
Annual burner check
Semi-annual visual inspection
Zero internal cleaning required after 1 year
Less than 1 day/year in downtime
Result: Maintenance cost savings of over 40% annually and increased equipment availability.
Impacts on Boiler Control and Efficiency
Clean combustion also improves control stability:
System Element | Gas Boiler Benefit |
---|---|
O₂ Sensors | Unaffected by soot, maintain calibration |
Temperature Probes | Less exposure to corrosive deposits |
Flow Meters | No particulate-induced clogging |
Combustion Controls | Respond precisely to clean flame patterns |
This ensures better real-time efficiency management and safer operation over long intervals.
Summary: Maintenance and Longevity Advantages of Gas-Fired Boilers
Advantage Area | Gas Boiler Contribution |
---|---|
Fouling and Cleaning | Minimal fouling means less frequent cleaning |
Component Durability | Less corrosion, erosion, and thermal stress |
Maintenance Intervals | Extended—typically 1 or 2 times/year |
Operational Availability | Higher uptime due to fewer cleaning shutdowns |
Sensor and System Reliability | Clean environment extends life of controls and instruments |
The clean-burning nature of gas-fired boilers directly translates into longer-lasting, lower-maintenance systems. For industries that value uptime, predictive maintenance, and long equipment life cycles, natural gas combustion is the most efficient and sustainable choice among fossil fuel technologies.

Why are gas-fired boilers faster and easier to operate than conventional models?
In high-demand industrial and commercial environments, operational speed and ease of use are critical. Boilers that take hours to start up, require manual tuning, or demand constant monitoring not only delay production but also increase labor costs and the risk of system faults. Traditional coal- and oil-fired boilers typically rely on complex fuel-handling equipment, manual ignition, and extensive warm-up procedures. In contrast, gas-fired boilers are designed for simplicity, speed, and automation, making them far more responsive and user-friendly.
Gas-fired boilers are faster and easier to operate than conventional models due to their automatic ignition systems, clean-burning fuel, simplified startup processes, and fully integrated digital controls. Unlike coal or heavy-oil boilers, gas systems eliminate the need for manual fuel handling, long warm-up times, and soot management. With modulating burners, programmable control panels, and remote monitoring, gas boilers can achieve full operation in under 30 minutes and adjust dynamically to load demands with minimal operator input.
These features make gas-fired boilers especially suitable for facilities that require flexible, low-labor, high-uptime thermal systems.
Key Operational Advantages of Gas-Fired Boilers
Feature | Operational Benefit |
---|---|
Instantaneous ignition | No manual lighting or prolonged warm-up cycles |
Fully modulating burners | Smooth and automated load response |
Digital control panels | Simple user interface for operators |
No fuel prep or handling | No conveyors, crushers, or pumping systems needed |
Low startup time | Fast to pressure and temperature |
Cleaner combustion | No ash, no soot—less need for maintenance during operation |
Startup Time Comparison
Boiler Type | Typical Cold Start Time | Warm Start Time |
---|---|---|
Gas-Fired Boiler | 10–30 minutes | 5–15 minutes |
Oil-Fired Boiler | 30–60 minutes | 15–30 minutes |
Coal-Fired Boiler | 1.5–3 hours | 45–90 minutes |
Biomass Boiler | 1–2 hours | 30–60 minutes |
Gas-fired systems can reach full steam output quickly thanks to:
Pre-programmed startup sequences
Rapid burner ignition via spark or flame ionization
Quick heat transfer through clean heat exchangers
Pre-purged fuel lines and pilot-less ignition systems
User-Friendly Control Interfaces
Modern gas-fired boilers are equipped with integrated touchscreen HMIs or PLC-based interfaces that provide:
Real-time status of pressure, temperature, and burner status
Automated scheduling (start/stop based on time or load)
Safety interlocks and fault alerts
Remote access via SCADA or IoT
This automation reduces the skill level and manual effort required to operate the boiler.
Interface Feature | Operator Benefit |
---|---|
Touchscreen dashboards | Easy-to-read metrics and controls |
Auto-start programs | Hands-free operation at shift start |
Alert systems | Prevents faults before they escalate |
Remote monitoring | Access and adjust from off-site locations |
Burner Modulation and Load Matching
Gas-fired burners often support turndown ratios up to 10:1, allowing the boiler to respond to fluctuating steam or hot water demands without cycling.
Comparison Metric | Conventional Boiler | Gas-Fired Boiler |
---|---|---|
Turndown Ratio | 2:1 to 4:1 | 5:1 to 10:1 |
Cycling Frequency | Higher | Lower (modulating control) |
Operator Adjustments | Frequent (manual valves) | Minimal (auto adjustment) |
Less cycling means:
Lower thermal stress
Improved fuel efficiency
Longer component life
Reduced Complexity and Operator Workload
Operating Requirement | Traditional Models | Gas-Fired Boilers |
---|---|---|
Fuel Handling | Manual feed, ash removal | None—piped gas supply |
Ignition | Manual or staged | Instant, auto-sequenced |
Combustion Adjustment | Manual dampers or valves | Automatic via sensors |
Startup Checklist | Dozens of items | Few automated checks |
Supervision Needed | Full-time operator | Minimal (often remote) |
Gas boilers can even be networked with Building Management Systems (BMS) for fully integrated energy control across entire facilities.
Case Example: Retrofit in a Food Processing Plant
A food packaging facility replaced a 4 TPH coal-fired boiler with a 3.5 TPH fully modulating gas boiler with smart controls.
Results:
Startup time reduced from 2 hours to 18 minutes
Operator time cut by 65%
Load matching improved steam stability
Enabled unattended night operation via remote alarm system
Summary: Operational Simplicity of Gas-Fired Boilers
Area of Operation | Gas Boiler Advantage |
---|---|
Startup Speed | Fast ignition, minimal warm-up |
User Interface | Intuitive touchscreen or PLC control |
Burner Control | Fully modulating with precise load tracking |
Labor Requirements | Low—no ash or fuel handling |
System Integration | Easy to tie into plant automation platforms |
Gas-fired boilers offer a combination of speed, simplicity, and smart control unmatched by traditional boiler systems. For facilities seeking minimal disruption, high responsiveness, and reduced operating overhead, they are the go-to solution for modern thermal energy needs.
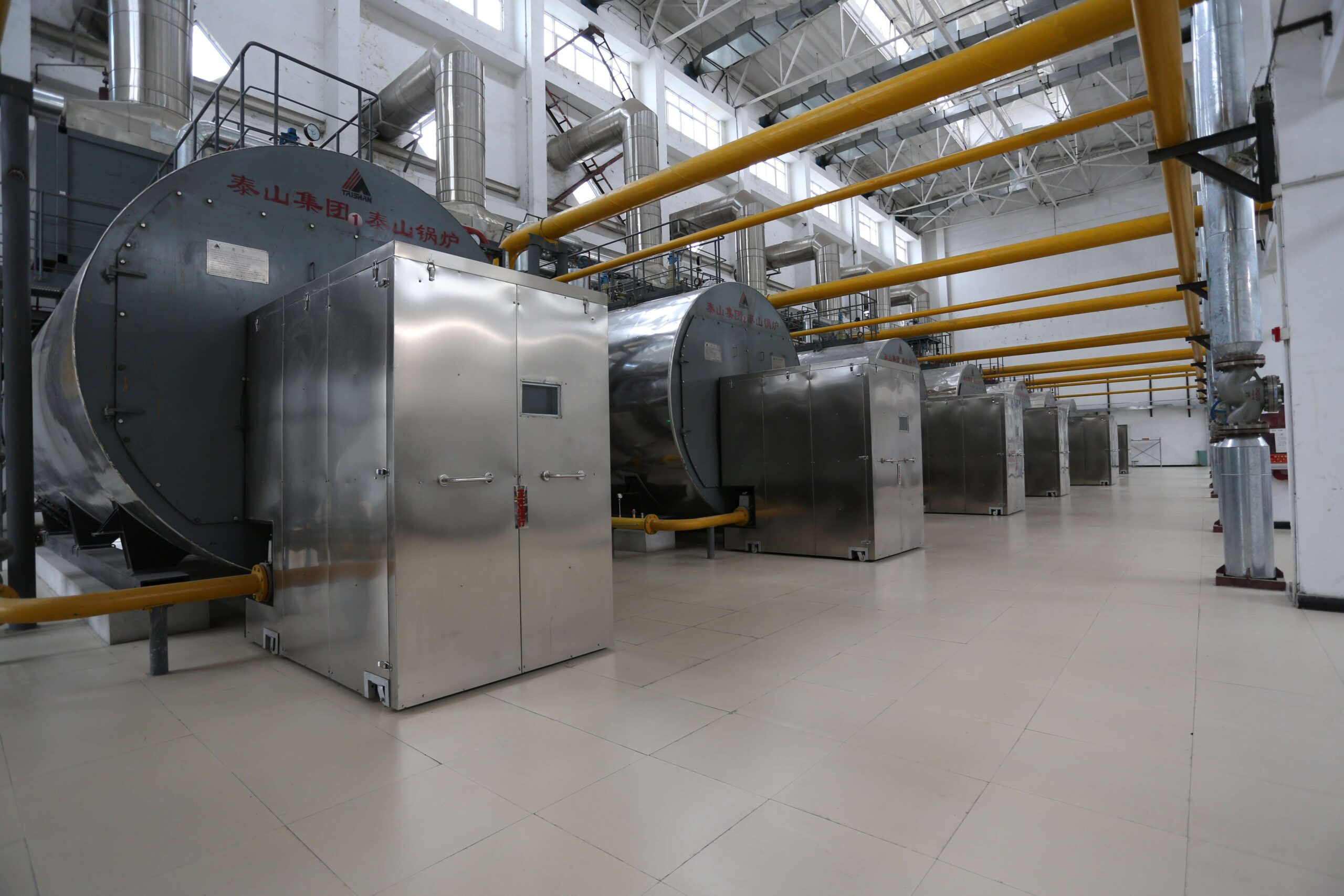
What role does automation play in enhancing gas-fired boiler performance?
In today’s industrial landscape, where energy efficiency, emission control, and operational uptime are critical KPIs, relying on manual boiler management is no longer viable. Traditional systems that require constant operator intervention are prone to human error, inefficiency, and delayed fault response. Gas-fired boilers, especially when integrated with advanced automation systems, offer a transformative performance advantage—enabling intelligent control, real-time diagnostics, and optimized fuel utilization. Automation doesn’t just simplify operation; it maximizes boiler efficiency, reliability, and regulatory compliance.
Automation plays a central role in enhancing gas-fired boiler performance by continuously optimizing combustion conditions, regulating output in real-time, reducing fuel consumption, and ensuring consistent steam or hot water generation. Through programmable logic controllers (PLCs), digital sensors, modulating burners, and SCADA or IoT platforms, automation minimizes manual intervention, prevents performance drift, and extends equipment life. The result is a highly responsive, energy-efficient, and low-maintenance system tailored to modern industrial demands.
Let’s explore how automation influences every key operational aspect of a gas-fired boiler—from ignition and modulation to monitoring and maintenance.
Core Functions of Automation in Gas-Fired Boilers
Automation Function | Impact on Boiler Performance |
---|---|
Combustion Control | Maintains optimal air-fuel ratio for maximum efficiency |
Burner Modulation | Adjusts flame output based on real-time demand |
Temperature & Pressure Regulation | Prevents overshoot, improves steam/hot water stability |
Startup and Shutdown Sequencing | Ensures safe and fast transitions |
Fault Detection and Alerts | Enables predictive maintenance and immediate troubleshooting |
Remote Monitoring & Diagnostics | Reduces operator dependency, allows 24/7 oversight |
Burner Modulation and Efficiency Optimization
Gas-fired boilers use fully modulating burners that can operate at varying firing rates (typically 10:1 turndown), controlled automatically based on real-time feedback from sensors.
Sensor Input | Automated Response |
---|---|
Steam pressure drop | Increases burner firing rate |
Flue gas temperature rise | Adjusts combustion air to reduce heat loss |
Excess O₂ detection | Fine-tunes air dampers to avoid fuel waste |
This precise modulation prevents unnecessary on-off cycling (common in staged systems), which improves:
Fuel efficiency (up to 98%)
Equipment longevity
Combustion stability
Real-Time Monitoring and Smart Control
Modern gas-fired boilers are equipped with:
Temperature and pressure transmitters
Oxygen and CO₂ sensors in the flue gas
Water level and flow rate meters
Heat exchanger surface thermocouples
These sensors feed into a central PLC or DCS, which continuously adjusts boiler operation to maintain optimal conditions.
Monitored Parameter | Control Action Taken Automatically |
---|---|
Drum water level | Modulates feedwater valve or pump |
Flue O₂ concentration | Trims excess air via burner fan or dampers |
Return water temperature | Adjusts burner to avoid overshoot |
Combustion chamber pressure | Manages draft fans to stabilize flame behavior |
Safety Sequencing and Alarm Management
Safety is a top priority in any combustion system. Automated gas-fired boilers follow multi-step logic sequences during startup and shutdown to prevent unsafe conditions.
Automated Safety Interlocks Include:
Flame sensor failure = burner shutdown
Low water level = lockout with alarm
Overpressure = safety valve activation + alarm
High flue gas temperature = shutdown to prevent exchanger damage
Operators are alerted through alarms, display messages, or SMS/email notifications, ensuring swift response.
Remote Access and Predictive Maintenance
With SCADA, IoT dashboards, or cloud-based monitoring platforms, operators and engineers can:
View real-time performance from off-site
Access trend data for predictive maintenance
Receive alerts for anomalies or efficiency loss
Monitor multiple boiler systems across facilities
Feature | Maintenance Benefit |
---|---|
Runtime data logging | Identifies component wear or drift over time |
Condition-based servicing | Reduces unnecessary shutdowns and over-servicing |
Early fault detection | Prevents unplanned downtime |
Maintenance scheduling | Allows proactive planning and spares readiness |
Case Study: Industrial Laundry Plant with Smart Gas Boiler
An industrial laundry in the UK installed a 2 TPH gas-fired condensing boiler with full PLC automation and IoT remote monitoring.
Results:
Efficiency rose from 86% to 94.7% due to continuous air-fuel optimization
Reduced operating staff from 3 shifts to 1 part-time technician
Enabled night and weekend operation with automatic load adjustment
Detected burner degradation 10 days before failure using trend data
Conclusion: Automation paid for itself within 18 months through reduced labor and energy savings.
Integration with Building and Energy Management Systems
Gas-fired boiler automation supports full plant integration:
Synchronizes with HVAC or CHP systems
Manages multiple boilers via lead-lag control
Optimizes fuel use during peak tariff periods
Aligns with building energy management systems (BEMS)
This holistic energy control reduces operational costs and improves sustainability metrics.
Summary: Why Automation Is Essential for Modern Gas Boilers
Performance Area | Automation Contribution |
---|---|
Combustion Efficiency | Continuously optimized air-fuel ratio |
Output Stability | Real-time modulation ensures steady temperature/pressure |
Safety Assurance | Prevents faults through interlocks and sequenced control |
Maintenance and Uptime | Reduces downtime with predictive alerts |
Operator Load | Minimizes manual intervention and labor dependency |
Data and Diagnostics | Enables energy audits and performance optimization |
Automation transforms gas-fired boilers into smart, self-regulating thermal systems that outperform conventional models in every aspect—from energy savings to operational resilience. For industries aiming to future-proof their thermal infrastructure, automation isn’t optional—it’s essential.
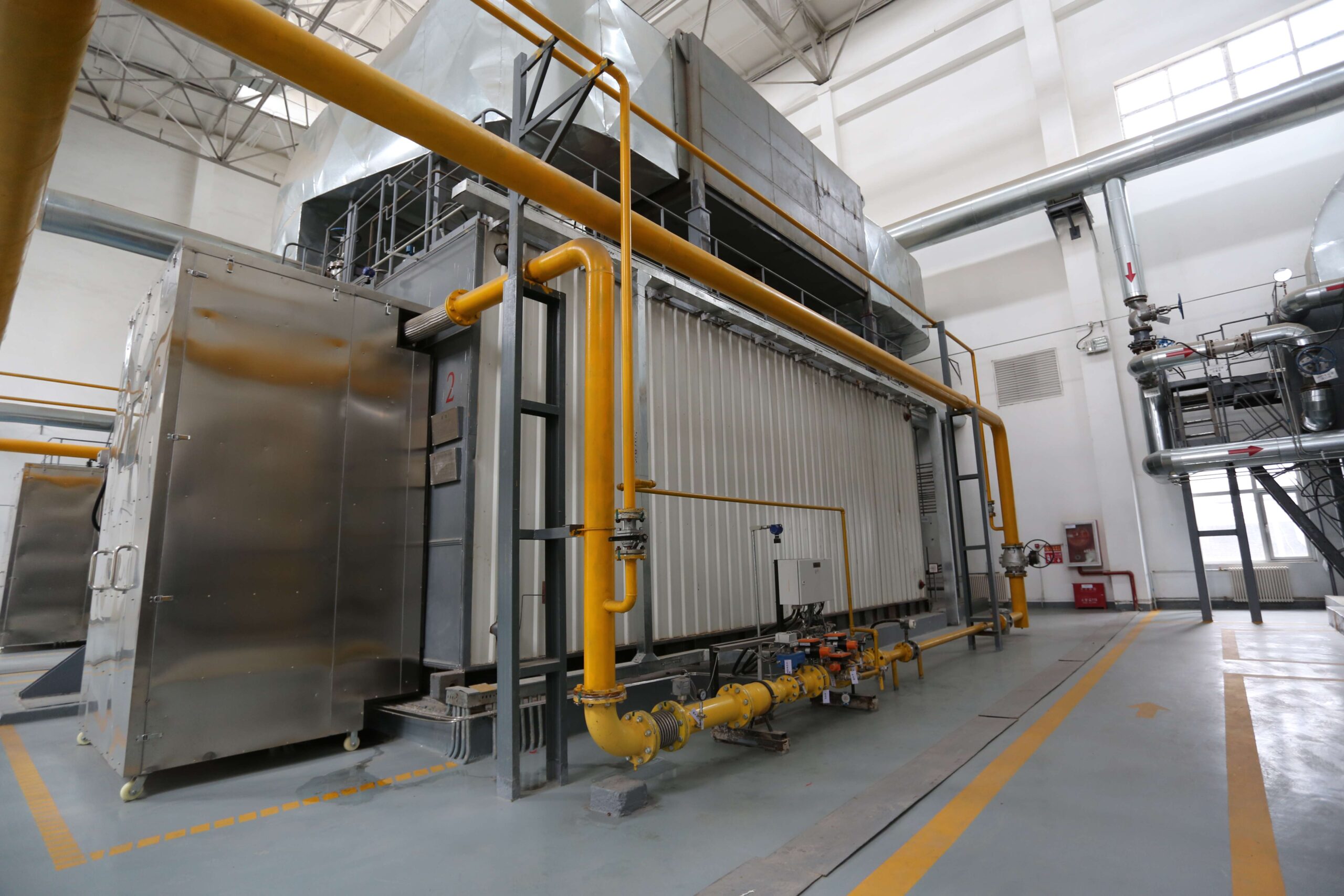
How do gas-fired boilers support industrial sustainability and regulatory compliance?
Industries across the globe face mounting pressure to cut greenhouse gas emissions, minimize pollutants, and comply with evolving environmental regulations. In this context, energy-intensive systems like boilers are under scrutiny—not only for their fuel efficiency but for their overall impact on air quality and sustainability goals. Gas-fired boilers, powered primarily by natural gas or low-carbon alternatives, are increasingly recognized as a cleaner, more compliant, and forward-looking solution that helps businesses align with both regulatory and environmental benchmarks.
Gas-fired boilers support industrial sustainability and regulatory compliance by producing significantly lower emissions—including NOx, SO₂, CO₂, and particulate matter—compared to coal and oil-fired systems, while offering high thermal efficiency, fuel flexibility, and compatibility with advanced control and monitoring systems. Their cleaner combustion profile reduces the need for complex emission controls and allows industries to meet strict air quality standards, carbon reduction targets, and green certification requirements with greater ease and lower cost.
Let’s break down how gas-fired boiler systems help industries meet sustainability objectives and regulatory mandates.
Emissions Profile: A Cleaner Baseline
Compared to conventional boilers, gas-fired systems offer substantially lower environmental impact, starting with the combustion process itself.
Pollutant | Coal-Fired Boiler | Oil-Fired Boiler | Gas-Fired Boiler |
---|---|---|---|
CO₂ (kg/GJ) | ~94–100 | ~74–76 | ~50–55 |
SO₂ (mg/Nm³) | 300–1500+ | 100–500 | <10 |
NOx (mg/Nm³) | 200–500 | 120–300 | 30–100 (with low-NOx burner) |
Particulate Matter (mg/Nm³) | 100–300 | 40–100 | <5 |
Heavy Metals | Present (e.g., mercury, arsenic) | Traces | None |
This inherently cleaner combustion allows gas-fired systems to meet or exceed global standards such as:
EPA Clean Air Act (USA)
EU Industrial Emissions Directive (IED)
ISO 14001 Environmental Management
BREEAM/LEED Green Building Certifications
Regulatory Advantages
Compliance Area | Gas Boiler Contribution |
---|---|
Air Quality Standards | Easily meets limits for NOx, SO₂, PM, CO |
Greenhouse Gas Reporting | Lower CO₂ output simplifies carbon accounting |
Permitting | Streamlined due to minimal pollution and lower risk factors |
Monitoring Requirements | Often reduced or simplified due to fewer pollutants |
Avoidance of Scrubbers/ESP | Reduces CAPEX and OPEX tied to pollution control systems |
In many jurisdictions, switching to gas-fired systems can exempt a facility from major source thresholds, simplifying compliance obligations and documentation.
Contribution to Industrial Sustainability Goals
1. Carbon Footprint Reduction
Natural gas has the lowest carbon content per unit of energy among fossil fuels. Modern condensing gas boilers can reach thermal efficiencies of 95–98%, further reducing CO₂ emissions per unit of steam or hot water output.
2. Energy Efficiency Gains
System Type | Typical Thermal Efficiency |
---|---|
Traditional Coal Boiler | 70–80% |
Oil-Fired Boiler | 80–88% |
Gas-Fired Condensing | 90–98% |
Higher efficiency = lower fuel use = lower emissions.
3. Cleaner Work Environment
No ash, soot, or unburned carbon:
Improves indoor air quality
Reduces HVAC and equipment contamination
Supports worker safety and health compliance
4. Renewable Gas Compatibility
Gas-fired boilers can often be converted to burn biogas, green hydrogen, or synthetic methane, enabling long-term carbon neutrality.
Renewable Fuel Type | Compatibility with Gas Boilers |
---|---|
Biogas | Yes (with desulfurization) |
Hydrogen (up to 20–30%) | Yes (with burner adjustment) |
Renewable Natural Gas | Fully compatible |
Integration with Digital Monitoring Systems
Gas-fired systems easily integrate with:
Continuous Emissions Monitoring Systems (CEMS)
Building Management Systems (BMS)
Energy Performance Dashboards
Carbon Accounting Software
This real-time transparency supports:
Sustainability Metric | Benefit of Gas Boiler Integration |
---|---|
Carbon Intensity (kg CO₂/MWh) | Direct tracking and reduction planning |
Energy Use per Unit Output | Easy to optimize via burner modulation |
Environmental Audits | Simplified documentation and compliance |
Green Certifications | Contributes to BREEAM, LEED, ISO scores |
Real-World Example: Textile Industry Carbon Reduction
A textile manufacturer in South Asia transitioned from two 3 TPH coal-fired boilers to a single 5 TPH gas-fired condensing boiler with real-time emissions tracking.
Before (Coal):
CO₂: ~5,800 tons/year
NOx: ~200 mg/Nm³
SO₂: ~1,100 mg/Nm³
After (Gas):
CO₂: ~3,150 tons/year
NOx: ~95 mg/Nm³
SO₂: <10 mg/Nm³
Qualified for local green energy grants
Simplified environmental permitting and annual reporting
Summary: The Sustainability and Compliance Edge
Benefit Area | How Gas-Fired Boilers Deliver |
---|---|
Air Pollution Reduction | Drastically lower SO₂, NOx, PM, CO emissions |
Carbon Management | Lower CO₂ output and compatibility with renewable gas |
Compliance Ease | Meets most global standards without extensive retrofits |
Audit and Reporting | Automated tracking through integrated digital platforms |
Certification Support | Contributes toward ISO, LEED, ESG, and net-zero targets |
Gas-fired boilers are not just high-performance heating systems—they are strategic assets for organizations seeking to operate responsibly, reduce environmental impact, and ensure compliance in an era of increasing environmental accountability. For industries aiming to balance productivity with sustainability, they offer a clear and compliant path forward.
🔍 Conclusion
Industrial gas-fired boilers offer a cleaner, more efficient, and technologically advanced solution for modern heat and steam demands. Compared to traditional systems, they deliver superior combustion efficiency, lower emissions, simplified maintenance, and real-time performance control. These advantages not only reduce operational costs but also support industries in achieving sustainability targets and long-term reliability.
📞 Contact Us
💡 Considering a gas-fired boiler for your industrial facility? Our experienced team can help you evaluate your options and implement a system that fits your technical needs, environmental goals, and budget.
🔹 Get in touch today to transform your industrial heating system with gas-fired technology! 🔥♻️
FAQ
Why are industrial gas-fired boilers more efficient than traditional boilers?
Industrial gas-fired boilers offer higher thermal efficiency due to precise combustion control, advanced burners, and modern heat recovery systems, reducing fuel consumption and energy waste.
How do gas-fired boilers help reduce emissions?
Natural gas burns cleaner than coal or oil, emitting significantly lower levels of CO₂, NOx, and particulate matter. Many gas boilers also include low-NOx burners and flue gas treatment technologies.
Are gas-fired boilers cheaper to operate in the long term?
Yes, natural gas is often more cost-effective than other fuels, and gas boilers require less maintenance, resulting in lower overall operational and lifecycle costs.
What makes gas-fired boilers more reliable for industrial applications?
Gas-fired systems have faster startup times, more consistent heat output, and fewer mechanical parts subject to wear, making them ideal for demanding industrial processes.
Do gas-fired boilers support automation and modern control systems?
Absolutely. Industrial gas boilers are compatible with advanced PLC/SCADA control systems, allowing real-time monitoring, automation, and optimization of boiler operations.
References
Gas Boiler Efficiency & Emission Benefits – https://www.energy.gov
Comparison of Fuel-Based Industrial Boilers – https://www.sciencedirect.com
Natural Gas as a Clean Fuel Option – https://www.epa.gov
Operational Costs of Industrial Boilers – https://www.researchgate.net
Modern Industrial Boiler Technologies – https://www.bioenergyconsult.com
Automation in Boiler Systems – https://www.mdpi.com
Low-NOx Burner Technologies – https://www.energysavingtrust.org.uk
Industrial Heating Systems Overview – https://www.iea.org
Gas vs Oil Boiler Comparison – https://www.automation.com
Cleaner Combustion for Industry – https://www.sciencedirect.com
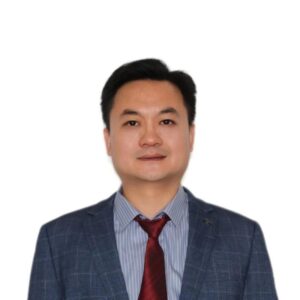