As industrial facilities and power plants seek cleaner, more cost-effective, and fuel-flexible solutions, traditional boiler systems—such as pulverized coal or grate-fired units—often fall short in terms of emission control, fuel adaptability, and efficiency. In contrast, Circulating Fluidized Bed (CFB) boilers offer a modern solution with significant operational and environmental benefits. However, without understanding these advantages, industries may miss the opportunity to improve performance and reduce lifecycle costs.
The main advantages of a Circulating Fluidized Bed (CFB) boiler over traditional boilers include superior fuel flexibility, lower NOx and SO₂ emissions, improved combustion efficiency, reduced operating temperatures, and enhanced load-following capability. CFB boilers can burn a wide range of fuels—such as coal, biomass, and industrial waste—while maintaining consistent performance. Their unique fluidization and recirculation system allows for complete combustion, better heat distribution, and lower environmental impact.
For industries aiming to modernize their steam or power generation systems, CFB technology provides a future-ready platform that balances performance, efficiency, and sustainability.
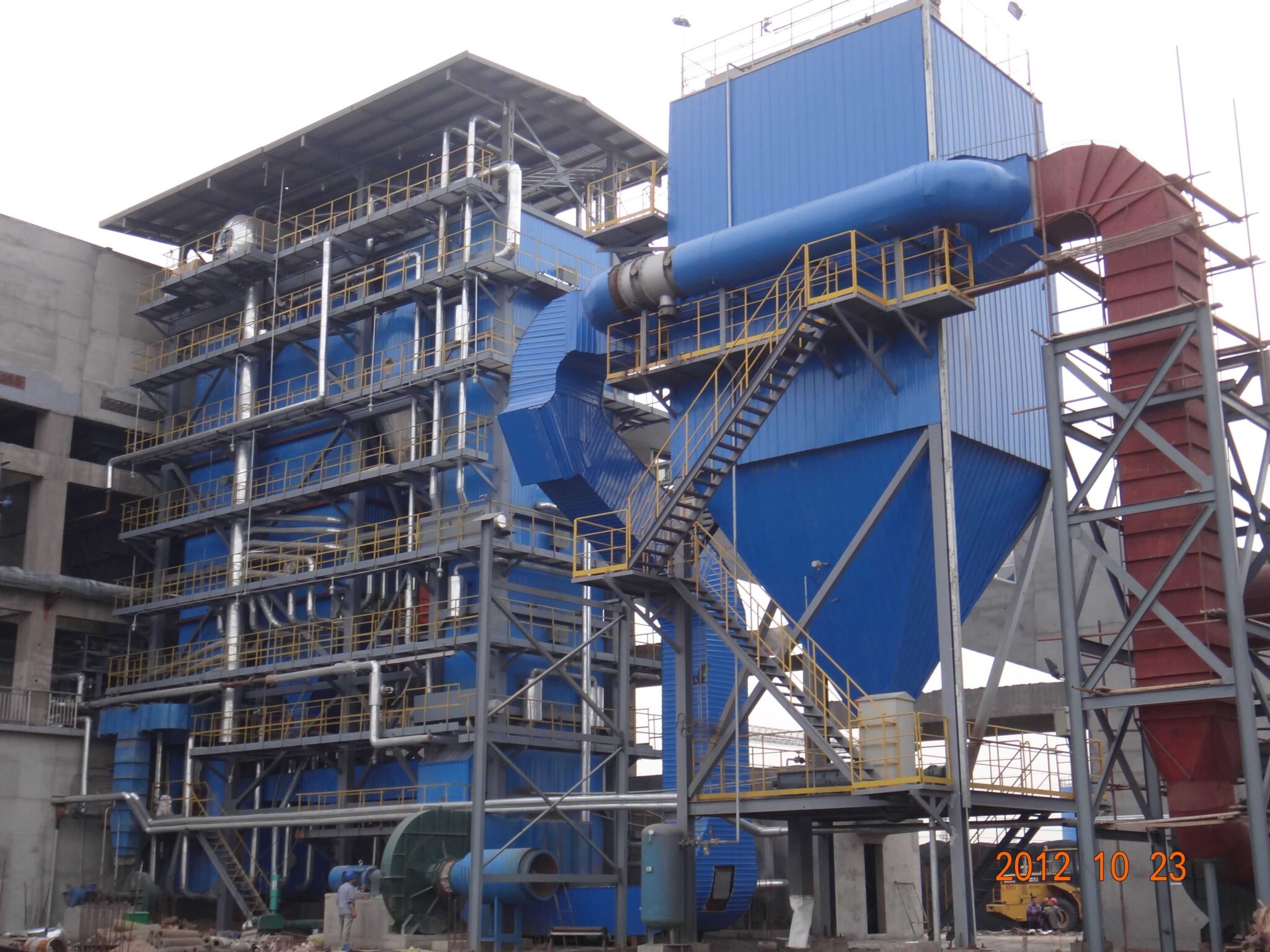
How does a CFB boiler provide superior fuel flexibility compared to traditional boilers?
Fuel cost, availability, and composition can fluctuate significantly over time—posing a serious challenge to industrial boiler operators reliant on conventional systems designed for a single type of fuel. Traditional pulverized coal or oil-fired boilers require uniform fuel quality and strict operating conditions, making it difficult to switch fuels without performance penalties or equipment modifications. In contrast, the Circulating Fluidized Bed (CFB) boiler is engineered to burn a wide range of fuels efficiently and cleanly, making it one of the most fuel-flexible combustion technologies available in industrial and utility-scale applications.
A CFB boiler provides superior fuel flexibility compared to traditional boilers by utilizing a fluidized combustion process that can efficiently burn a wide range of low-grade, high-moisture, and variable-composition fuels—including coal, biomass, petroleum coke, industrial waste, and RDF (refuse-derived fuel). The system’s ability to maintain uniform bed temperatures, accommodate diverse particle sizes, and adjust air/fuel ratios dynamically allows it to switch between fuels without major hardware changes, ensuring consistent efficiency, stable emissions, and continuous operation under varying fuel conditions.
This unique capability allows plant operators to respond to market fuel fluctuations, reduce operating costs, and utilize locally available or waste-derived energy sources without compromising performance or compliance.
What Makes CFB Boilers Fuel-Flexible?
Design Feature | Fuel Flexibility Contribution |
---|---|
Fluidized Bed Combustion | Allows thorough mixing of air and fuel for even combustion |
Wide Temperature Range (800–900°C) | Prevents slagging and enables use of high-ash, low-reactivity fuels |
High Solids Recirculation | Extends residence time for complete burn of low-grade fuels |
Multi-fuel Feeders | Supports simultaneous or alternating feeding of different fuels |
Integrated Limestone Injection | Enables in-furnace sulfur capture from high-sulfur fuels |
Unlike traditional combustion systems, CFB boilers do not require fine pulverization or oil atomization. Fuels can be coarse, wet, variable in calorific value, or heterogeneous, and still burn efficiently within the fluidized environment.
Common Fuels Used in CFB Boilers
Fuel Type | Typical Use in CFB Boiler |
---|---|
Bituminous/Sub-bituminous Coal | Baseline fuel in many CFB power plants |
Lignite | Low-cost, high-moisture coal burned without drying |
Petroleum Coke | High-sulfur, high-energy byproduct fuel |
Biomass (wood chips, agri-waste) | Co-fired or 100% fired in CFB with low emissions |
Sewage Sludge / MSW / RDF | Waste-to-energy plants using CFB for recovery |
Peat and Torrefied Biomass | Used in fuel-diverse or carbon-neutral projects |
Comparison: Fuel Flexibility of Boiler Types
Boiler Type | Fuel Flexibility Rating | Fuel Type Limitations |
---|---|---|
CFB Boiler | ★★★★★ | Can burn diverse solids, sludges, waste, mixes |
Pulverized Coal (PC) Boiler | ★★☆☆☆ | Requires dry, fine coal |
Oil-Fired Boiler | ★☆☆☆☆ | Specific to clean liquid fuels |
Gas-Fired Boiler | ★☆☆☆☆ | Limited to methane or LPG |
Grate-Fired Biomass Boiler | ★★☆☆☆ | Can burn biomass, but limited fuel variation |
The CFB’s ability to co-fire multiple fuels—such as coal with biomass or waste materials—makes it uniquely adaptive in real-world energy scenarios.
Fuel Switching: Operational Stability and Control
CFB boilers can adjust to new fuels without shutdown, thanks to their dynamic combustion control and robust design:
Fuel Property Variation | CFB Boiler Response |
---|---|
Moisture Content ↑ | Longer combustion residence time balances energy |
Calorific Value ↓ | Higher feed rate and bed recirculation compensate |
Ash Content ↑ | Non-slagging temperature avoids deposit issues |
Particle Size Variation | Fluidized bed maintains even combustion |
Advanced Distributed Control Systems (DCS) monitor bed temperature, air flow, fuel feed rate, and cyclone performance, automatically adapting combustion parameters.
In-Furnace Emissions Control with Variable Fuels
Fuel flexibility does not compromise environmental compliance in a CFB boiler:
Emission Type | In-Furnace Control Method | Benefit When Fuel Changes |
---|---|---|
SO₂ | Limestone injection (CaCO₃) reacts with sulfur | Controls sulfur even in high-sulfur fuels |
NOx | Low-temperature combustion limits thermal NOx | No SCR needed in most cases |
Particulates | Cyclone and ESP/baghouse systems | Handles ash from varied fuel types |
This built-in emissions management makes CFB boilers suitable for waste-to-energy, biomass co-firing, and low-grade coal use without additional post-combustion scrubbers.
Real-World Case Study: Multi-Fuel Industrial CFB Plant
A 150 MW industrial utility in Eastern Europe installed a CFB boiler to replace aging oil and coal systems. The goal was to reduce fuel costs and comply with EU emissions regulations.
Fuels Used:
60% Lignite
25% Biomass (wheat straw, wood waste)
15% RDF and plastics
Results:
Maintained >88% boiler efficiency across fuel variations
NOx emissions under 180 mg/Nm³ without SCR
SO₂ reduced by 92% via limestone dosing
Fuel cost reduced by 37% in first year
This demonstrates how multi-fuel capability lowers costs, enhances flexibility, and supports sustainable operations.
Summary: Fuel Flexibility Benefits of CFB Boilers
Advantage Category | CFB Boiler Performance |
---|---|
Fuel Variety | Burns solid, liquid, wet, dry, low-grade, and waste fuels |
Cost Optimization | Enables use of cheaper or on-site fuels |
Resilience to Fuel Supply Issues | Easily switches fuels during market disruptions |
Emissions Compliance | Built-in SOx and NOx control across fuel types |
Sustainability | Supports biomass, waste-derived fuels, and carbon targets |
The CFB boiler’s unmatched fuel flexibility makes it an ideal solution for industries facing volatile fuel markets, regulatory pressure, and sustainability mandates. It enables efficient, continuous energy generation—no matter the fuel source.
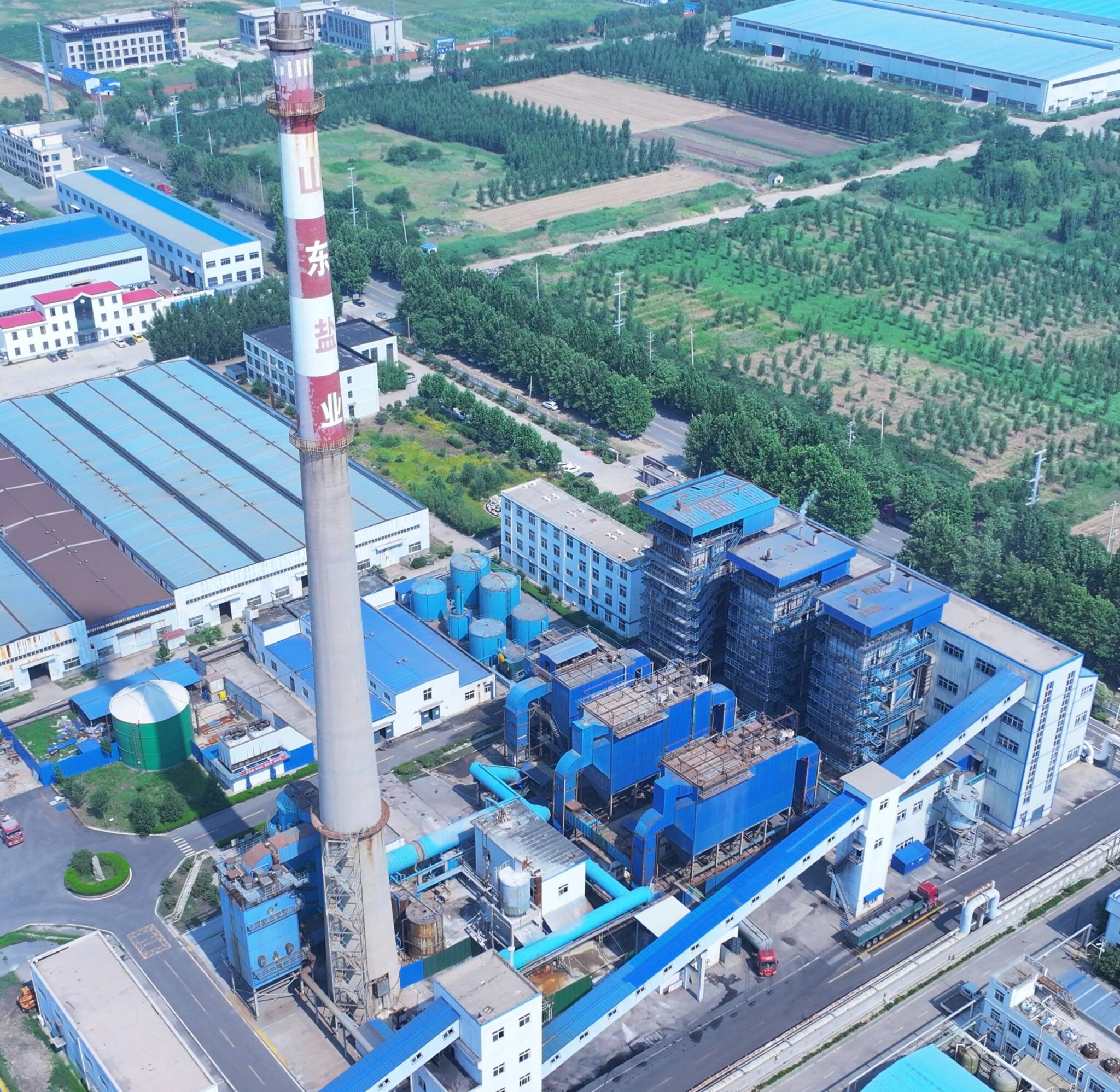
In what ways do CFB boilers achieve lower emissions than conventional systems?
In an era where industrial emissions are under intense scrutiny, boiler systems must not only deliver energy efficiently but also minimize their environmental footprint. Conventional combustion technologies—such as pulverized coal (PC) boilers, oil-fired systems, or even basic biomass furnaces—often struggle to meet strict regulatory standards without costly post-combustion treatment systems. Circulating Fluidized Bed (CFB) boilers, however, are inherently designed for cleaner combustion, offering multiple mechanisms for reducing pollutants at the source rather than relying solely on end-of-pipe solutions.
CFB boilers achieve lower emissions than conventional systems by utilizing low-temperature combustion (800–900°C), in-furnace sorbent injection for sulfur capture, staged air supply to limit NOx formation, and high-efficiency particulate removal via cyclones and fabric filters. This integrated design minimizes the generation of NOx, SO₂, CO, and particulate matter directly in the combustion chamber, significantly reducing the need for external emission control systems and ensuring compliance with stringent air quality regulations.
This in-furnace control approach makes CFB technology not only environmentally superior but also cost-effective and operationally streamlined.
Breakdown of Emission Reductions in CFB Boilers
Pollutant Type | Conventional Boiler Issue | CFB Boiler Solution |
---|---|---|
Nitrogen Oxides (NOx) | Formed at high combustion temps (>1,300°C) | Lower combustion temp (~850°C) + staged air injection |
Sulfur Dioxide (SO₂) | Requires post-treatment scrubbers | Limestone added in furnace captures sulfur directly |
Particulate Matter (PM) | Unburned ash or fly ash escapes stack | High-efficiency cyclones and ESPs remove up to 99.9% |
Carbon Monoxide (CO) | Caused by uneven combustion | Long fuel residence time ensures complete combustion |
Heavy Metals & Toxics | Released from burning waste or poor-quality coal | Captured with fly ash or bound in sorbents inside the bed |
1. Low-Temperature Combustion: NOx Reduction
CFB boilers operate at 800–900°C, significantly below the flame temperatures found in PC or oil-fired systems.
Factor | Conventional Boiler | CFB Boiler |
---|---|---|
Peak Flame Temperature | ~1,400–1,600°C | ~850°C |
NOx Formation Mechanism | Thermal and fuel NOx | Mostly suppressed |
Typical NOx Emissions | 300–600 mg/Nm³ | <150 mg/Nm³, often <100 |
How it works:
Thermal NOx (produced at high temperatures) is nearly eliminated.
Staged air (primary + secondary) delays oxidation of nitrogen in fuel.
No need for Selective Catalytic Reduction (SCR) in most applications—saving capital and operating cost.
2. In-Furnace Desulfurization: SO₂ Control
Instead of relying on flue gas scrubbers downstream, CFB boilers inject limestone or dolomite (CaCO₃) directly into the combustion chamber.
Reaction:
CaCO₃ → CaO + CO₂
CaO + SO₂ → CaSO₃ → CaSO₄
Feature | Benefit |
---|---|
Limestone Injection Ratio | ~1.5:1 molar (Ca:S) |
Desulfurization Efficiency | 85–95% in-furnace |
SO₂ Emissions | Often <100 mg/Nm³ with no scrubber required |
Sorbent Type | Limestone, quicklime, dolomite |
This embedded sulfur control simplifies plant design and avoids large wet or dry flue gas desulfurization (FGD) units.
3. Particulate Capture via Cyclones and Bag Filters
CFB boilers produce fine ash particles, but their high gas-solid interaction and downstream dust collection systems ensure minimal particulate escape.
Control Device | Efficiency |
---|---|
Primary Cyclone Separator | 85–90% |
Electrostatic Precipitator (ESP) | Up to 99.9% |
Fabric Filter / Baghouse | Up to 99.95% |
Final PM Emissions | <10 mg/Nm³, often <5 mg/Nm³ |
Plus, the fluidization process enhances combustion uniformity—reducing unburned carbon and minimizing particulate generation at the source.
4. Complete Combustion and CO Control
CFB boilers offer longer fuel residence time than conventional units, ensuring even slow-burning fuels combust completely.
Parameter | Conventional Boiler | CFB Boiler |
---|---|---|
Fuel Residence Time | 1–2 seconds | 5–10 seconds (with recirculation) |
CO Formation Risk | Higher (uneven burn) | Lower (complete burnout) |
Typical CO Emissions | 50–100+ mg/Nm³ | <50 mg/Nm³ (even with biomass) |
Long combustion time = cleaner burn = lower CO = higher combustion efficiency.
5. Multi-Fuel and Waste Fuel Emission Control
CFB boilers excel at burning:
Biomass
Petroleum coke
RDF (Refuse-Derived Fuel)
Sewage sludge
Waste coal
These fuels often contain chlorine, heavy metals, or volatile organics. In a CFB system:
Volatile metals are captured in fly ash
Chlorine reacts with added sorbents (e.g., kaolin or lime)
Organic toxins are destroyed due to long exposure in oxidizing atmosphere
This makes CFB boilers ideal for waste-to-energy and industrial co-firing under strict emission limits.
Real-World Example: Biomass Co-Fired CFB Plant
A 300 MW CFB plant in Scandinavia co-fires wood waste, peat, and refuse-derived fuel.
Emission Results:
Pollutant | Measured Level | Regulatory Limit (EU) |
---|---|---|
NOx | 85 mg/Nm³ | 150 mg/Nm³ |
SO₂ | 50 mg/Nm³ | 200 mg/Nm³ |
Particulate | 6 mg/Nm³ | 20 mg/Nm³ |
CO | 20 mg/Nm³ | 100 mg/Nm³ |
All without external SCR or FGD systems—just in-furnace control and cyclones.
Summary: How CFB Boilers Achieve Low Emissions
Emission Type | CFB Reduction Mechanism | Result Compared to Conventional Systems |
---|---|---|
NOx | Low combustion temp + staged air | Up to 80% less than PC boilers |
SO₂ | In-bed limestone injection | Up to 95% captured in-furnace |
Particulates (PM) | Cyclone + ESP/filters + clean burn | <10 mg/Nm³, no visible smoke |
CO | Long residence + complete combustion | Low CO even with waste fuels |
Toxics/Heavy Metals | Captured with ash or sorbents | Suitable for waste-burning compliance |
CFB boilers are not only efficient and versatile—they are also environmentally advanced systems that meet or exceed global emission standards without complex or expensive end-of-pipe controls. For industries seeking a cleaner, more sustainable combustion solution, CFB technology leads the way.
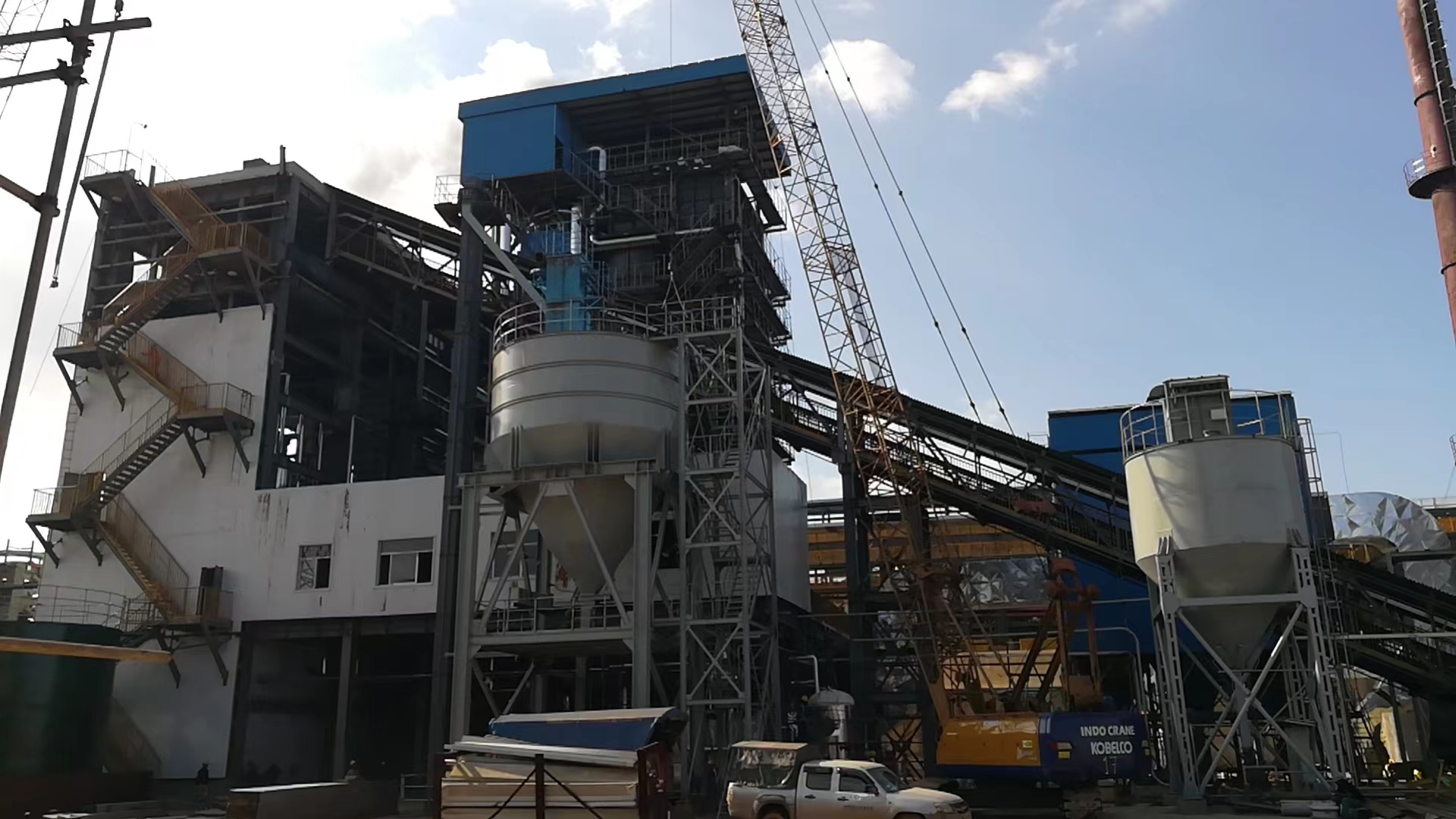
How does the fluidized bed design improve combustion efficiency and heat transfer?
Maximizing combustion efficiency and heat transfer is essential for any industrial boiler system—especially when burning challenging fuels like low-grade coal, biomass, or waste. Traditional combustion systems often suffer from poor fuel-air mixing, hotspots, incomplete burn, and inefficient heat exchange. This leads to fuel waste, higher emissions, and uneven thermal loads. Enter the fluidized bed design, the foundation of Circulating Fluidized Bed (CFB) and Bubbling Fluidized Bed (BFB) boilers, which transforms how fuel is burned and how heat is extracted.
The fluidized bed design improves combustion efficiency and heat transfer by suspending solid fuel particles in a turbulent, high-velocity stream of air, which ensures uniform temperature distribution, excellent fuel-air mixing, prolonged residence time, and intense contact between hot gases, ash particles, and heat transfer surfaces. This results in complete combustion of even difficult fuels, minimized unburned carbon losses, and exceptionally efficient heat extraction to steam or water systems—making fluidized bed boilers highly efficient, clean, and fuel-flexible.
This principle not only enhances performance but also enables the use of diverse, low-cost fuels with consistent energy output and reduced emissions.
How the Fluidized Bed Works
In a fluidized bed, air is forced upward through a bed of inert material (usually sand, ash, or limestone). When air velocity exceeds the minimum fluidization velocity, the bed behaves like a boiling liquid—lifting and suspending fuel particles in a dynamic, turbulent state.
Component | Function |
---|---|
Air Distributor Plate | Evenly introduces high-pressure primary air from below |
Bed Material | Transfers heat and stabilizes combustion (e.g., sand, ash) |
Fuel Feed System | Introduces solid, liquid, or slurry fuel into the bed |
Cyclone Separator | Captures and recirculates unburned particles for re-burning |
Heat Exchange Surfaces | Extracts thermal energy into water/steam circuits |
Combustion Efficiency Benefits
1. Excellent Fuel-Air Mixing
Continuous movement of particles ensures that fuel, air, and hot bed material are evenly mixed.
No need for pulverized fuel—even coarse, wet, or variable-size particles can combust fully.
Efficiency Factor | Traditional Boiler | Fluidized Bed Boiler |
---|---|---|
Fuel-Air Contact | Limited (laminar flow) | Excellent (turbulent flow) |
Mixing Uniformity | Uneven | High |
Flame Control | Flame zones/hotspots | Uniform combustion zone |
2. Longer Fuel Residence Time
Fuel particles remain suspended and recirculated in the bed for 5–10 seconds, compared to 1–2 seconds in conventional combustion.
Allows complete burnout of volatile matter and char.
Enables the combustion of low-reactivity fuels like petcoke, sewage sludge, and biomass.
3. Lower Combustion Temperature
CFBs operate at 800–900°C, below ash fusion points:
Prevents slagging and fouling of heat surfaces.
Limits thermal NOx formation while maintaining full combustion efficiency (>98%).
4. Auto-Thermal Stability
The bed stores thermal energy, acting as a thermal flywheel:
Maintains combustion during load fluctuations.
Reduces instability from fuel moisture or quality variation.
Heat Transfer Efficiency Advantages
1. Enhanced Convection and Radiation
Fluidized particles rub against heat exchanger surfaces, improving convective heat transfer.
Suspended particles and flue gases transfer radiative heat uniformly across the furnace.
Heat Transfer Mode | Enhancement in Fluidized Bed Design |
---|---|
Convection | Turbulence increases surface heat exchange rate |
Radiation | Even temperature and particle coverage improve absorption |
Bed Material Contact | Solids conduct heat directly to surfaces |
2. Immersed Surface Area in Furnace
Unlike conventional boilers, many CFB units embed heat exchange tubes directly into the combustion bed, accelerating transfer:
Evaporator tubes
Superheaters
Reheaters
This direct contact reduces boiler size for a given output and increases thermal efficiency.
3. Recirculation for Heat Utilization
The cyclone separator captures and recycles hot particles back to the bed:
Recaptured energy increases combustion zone temperature without extra fuel.
Fuel particles that missed complete combustion are reburned.
Comparison: Heat Transfer Rates
Boiler Type | Typical Heat Transfer Coefficient (kW/m²·K) |
---|---|
Pulverized Coal Boiler | 100–200 |
Oil/Gas-Fired Boiler | 120–180 |
Fluidized Bed Boiler | 300–400+ |
This higher rate means:
Faster response to load changes
Lower fuel consumption
Smaller overall boiler footprint
Real-World Performance Case: Biomass CFB Plant
A biomass CFB boiler (100 MWth) using wood chips and agricultural residues achieved:
Combustion efficiency of >99.1%
Heat transfer efficiency to steam circuit of 92.8%
Bed temperature stability ±10°C under 20% load swings
Steam temperature stability within ±1.5°C
No slagging, minimal fouling, and 5-year tube life—well above average.
Summary: Combustion & Heat Transfer Superiority in Fluidized Beds
Performance Area | Fluidized Bed Boiler Benefit |
---|---|
Fuel-Air Mixing | Uniform, continuous mixing ensures full combustion |
Combustion Completion | High residence time and turbulence yield low unburned carbon |
Temperature Uniformity | Stable bed temperatures improve control and safety |
Heat Transfer Rate | Superior due to turbulence and direct contact |
Load Flexibility | Fast thermal response with thermal buffer effect |
Fuel Versatility | Can burn high-moisture, low-grade fuels cleanly |
The fluidized bed design transforms combustion into a highly efficient, low-emission, and flexible process, enabling boiler systems to adapt to fuel and load variability without sacrificing performance. For industries seeking cost-effective, sustainable thermal energy, it is a proven high-efficiency solution.
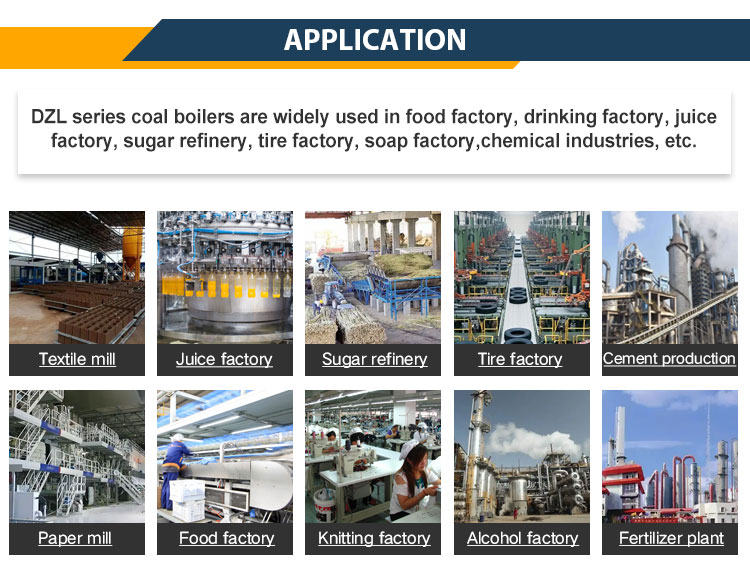
Why do CFB boilers operate more efficiently at lower temperatures?
In conventional boilers—such as pulverized coal or oil-fired systems—high combustion temperatures (often exceeding 1,300–1,500°C) are required to ensure complete fuel burn. However, these elevated temperatures come with significant drawbacks: higher NOx emissions, risk of slagging and fouling, equipment degradation, and reduced fuel flexibility. Circulating Fluidized Bed (CFB) boilers, on the other hand, operate within a lower and more controlled temperature range (typically 800–900°C), and this is not a limitation—it’s a fundamental efficiency-enhancing design feature.
CFB boilers operate more efficiently at lower temperatures because the fluidized bed environment enables complete combustion of a wide range of fuels without needing flame-stabilized high-temperature zones. This moderate and uniform temperature range prevents ash fusion, reduces thermal NOx formation, extends equipment lifespan, and allows better in-furnace heat transfer. The combination of efficient combustion at reduced thermal stress levels leads to high boiler efficiency, lower emissions, and greater operational flexibility—all without the need for costly external pollution control systems.
This innovative low-temperature combustion principle is central to the performance, reliability, and adaptability of CFB technology.
Understanding the CFB Operating Temperature Profile
Temperature Range | System Behavior and Benefits |
---|---|
800–900°C | Optimal combustion temperature for solid fuels in CFBs |
Below 1,000°C | Avoids ash melting, fouling, and slag formation |
Stable Furnace | Heat is evenly distributed across the bed and flue |
Unlike flame combustion zones in PC boilers, where temperatures can spike above 1,400°C, CFB boilers burn fuel within a stable bed of suspended particles, using turbulence and residence time rather than peak temperature to achieve complete burn.
Key Efficiency Advantages of Lower Operating Temperatures
1. Reduced Formation of Nitrogen Oxides (NOx)
High flame temperatures (above ~1,200°C) lead to the formation of thermal NOx, a major pollutant.
Boiler Type | Typical Combustion Temp | NOx Emissions (mg/Nm³) |
---|---|---|
Pulverized Coal | 1,300–1,600°C | 300–500+ |
Oil-Fired | 1,300–1,500°C | 200–400 |
CFB Boiler | 850–900°C | <100 (low-NOx design) |
By operating below this critical NOx formation threshold, CFBs achieve low emissions without SCR or SNCR systems, making the design both clean and cost-efficient.
2. Prevention of Slagging and Fouling
In high-temperature combustion, ash particles can melt and form slag, coating heat transfer surfaces and reducing efficiency.
Condition | PC Boiler | CFB Boiler |
---|---|---|
Ash Fusion | Above 1,200–1,300°C | Avoided at <950°C |
Slag Formation | Common with high-ash coal | Rare in CFB |
Surface Fouling | Requires soot blowing | Minimal in CFB |
Operating below ash fusion temperatures allows CFB boilers to burn high-ash fuels, such as lignite, petcoke, and biomass, without damaging boiler internals or requiring frequent cleaning.
3. Enhanced Heat Transfer Performance
The intense turbulence and fine particle suspension in the fluidized bed create ideal conditions for high-efficiency heat transfer—without needing extreme temperature differentials.
Heat Transfer Mode | Performance in CFB Boiler |
---|---|
Convection | Boosted by particle-to-surface contact |
Radiation | Uniform due to large surface exposure |
Bed Contact | Direct conduction from hot solids |
This efficient heat exchange, even at moderate temperatures, contributes to overall thermal efficiencies of 85–90% or more, especially when combined with economizers and reheaters.
4. Fuel Flexibility and Moisture Tolerance
High temperatures in conventional boilers require dry, consistent fuels. CFBs, thanks to their moderate and stable combustion zone, can:
Burn fuels with high moisture content (up to 50%)
Handle variable calorific values
Mix fuels (coal + biomass + sludge) without destabilizing combustion
This not only improves fuel sourcing flexibility but also supports cost savings and carbon reduction strategies.
5. Lower Mechanical and Thermal Stress
Operating at lower furnace temperatures reduces:
Tube metal creep and fatigue
Refractory degradation
Weld and joint failures
Maintenance Factor | High-Temp Boiler | CFB Boiler (Lower Temp) |
---|---|---|
Tube Replacement Cycle | 3–5 years | 6–10+ years |
Refractory Spalling | Common | Rare |
Component Lifespan | Shorter due to thermal stress | Longer |
This extends boiler life, reduces downtime, and lowers lifecycle maintenance costs.
Real-World Example: Waste-Coal-Fueled CFB Boiler
A 200 MW CFB power plant in Southeast Asia uses low-grade coal with 45% ash content and 30% moisture.
CFB Furnace Conditions:
Operating bed temperature: 870°C
Heat transfer rate: >350 kW/m²·K
Unburned carbon: <1.2%
NOx: <80 mg/Nm³, without external treatment
Despite fuel variability, combustion remained stable, ash did not slag, and tubes remained clean after 18 months, requiring only routine maintenance.
Summary: Why Lower Temperatures in CFB = Higher Efficiency
Advantage Area | Benefit from Lower Temperature Operation |
---|---|
NOx Emission Control | Thermal NOx minimized—no need for SCR |
Ash Management | Prevents slagging, allows burning high-ash fuels |
Heat Transfer Efficiency | Excellent turbulence and surface contact at 800–900°C |
Fuel Flexibility | Tolerates wet, variable, and low-quality fuels |
Boiler Durability | Reduced thermal stress, longer component lifespan |
CFB boilers are engineered to make lower combustion temperature an operational advantage rather than a compromise. Through smart design and fluid dynamics, they extract maximum energy from minimal heat, redefining how industrial combustion systems achieve both efficiency and environmental performance.
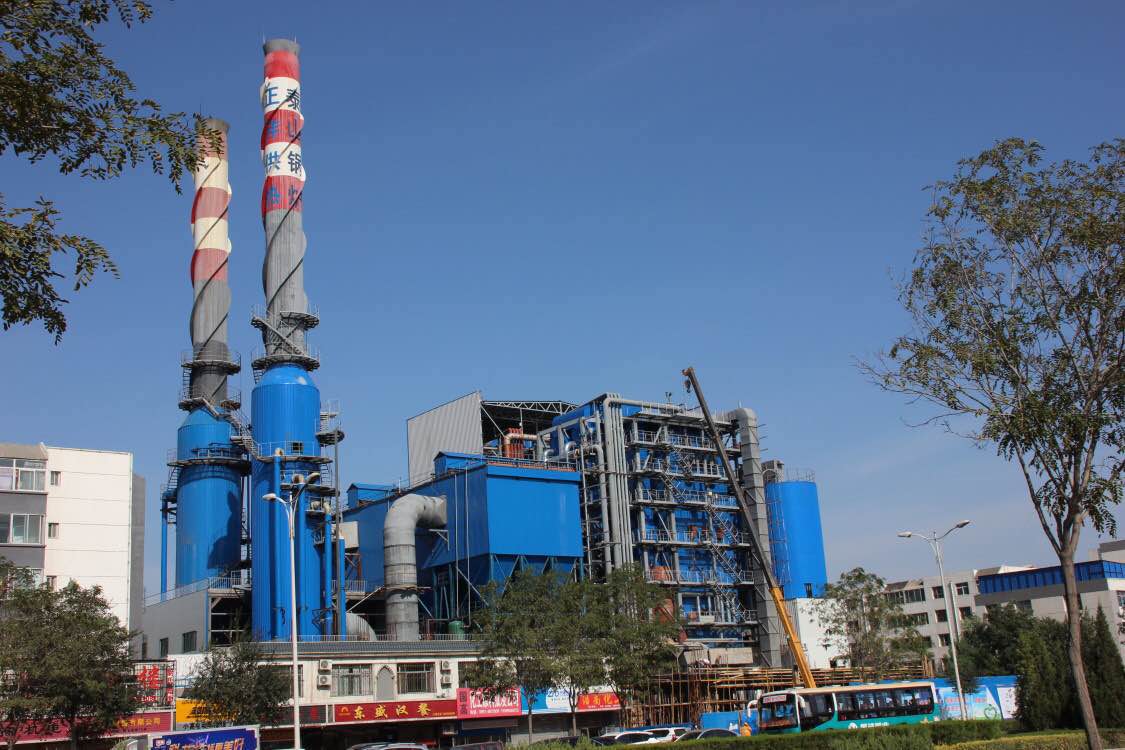
What makes CFB boilers better suited for variable load conditions?
In many industrial and utility applications, thermal demand is not constant. Processes ramp up and down, grid power requirements fluctuate, and seasonal variation affects heating or steam loads. Traditional boiler systems, particularly pulverized coal (PC) or oil-fired boilers, often struggle under these conditions, experiencing efficiency drops, instability, or even flameouts when loads are rapidly changed. In contrast, Circulating Fluidized Bed (CFB) boilers are inherently stable, flexible, and efficient under variable load conditions, making them ideal for dynamic energy environments.
CFB boilers are better suited for variable load conditions because their fluidized combustion environment maintains stable temperatures, ensures consistent fuel-air mixing, and allows for dynamic control of air, fuel, and recirculated solids. The bed’s thermal inertia, wide turndown ratios, and integrated air staging allow for seamless load adjustments without compromising combustion stability or efficiency. This flexibility enables CFB boilers to operate efficiently across a broad range of output levels, minimizing unburned carbon, reducing emissions, and avoiding mechanical stress from frequent cycling.
Let’s explore the engineering and operational features that make CFB boilers a top performer under fluctuating load profiles.
Key Design Features Supporting Load Flexibility
Design Element | Contribution to Load Adaptability |
---|---|
Fluidized Bed Combustion | Maintains uniform temperature and combustion distribution |
Bed Thermal Inertia | Acts as a heat buffer, smoothing sudden load changes |
Cyclone Separator and Return Loop | Enables continuous particle recirculation |
Staged Air Supply | Independently controls combustion zones |
Automated Fuel and Air Modulation | Adjusts firing rate in real-time |
Turndown Ratio Advantage
Turndown ratio is the ratio of maximum to minimum load a boiler can handle while maintaining stable combustion and efficiency.
Boiler Type | Typical Turndown Ratio |
---|---|
Pulverized Coal Boiler | 3:1 to 4:1 |
Oil-Fired Boiler | 4:1 to 6:1 |
CFB Boiler | 5:1 to 10:1 |
This wide load range allows CFB boilers to:
Operate at partial loads without cycling
Ramp up or down gradually or rapidly
Meet base-load, intermediate, or peak-load demands
Thermal Inertia and Bed Stability
The fluidized bed contains a mix of hot ash, fuel particles, and inert material (like sand or limestone), which stores and releases heat gradually.
Load Condition | CFB Response Mechanism |
---|---|
Sudden Load Increase | Hot bed material instantly provides combustion energy |
Sudden Load Drop | Reduced fuel feed, but bed retains thermal balance |
Fuel Quality Variation | Bed compensates by adjusting temperature and residence time |
Result: CFB boilers maintain combustion efficiency >98% even during rapid transitions, without flame instability or cold-end corrosion.
Real-Time Combustion Control
CFB systems use PLC-based or DCS control systems to continuously monitor and adjust:
Primary and secondary airflows
Fuel feed rate
Bed and furnace pressure
Return loop solids circulation
Dynamic Feedback Loop:
Load demand ↑ → Fuel + air ↑ → Cyclone returns more solids → Bed temp stabilizes → Steam output ↑
Load demand ↓ → Fuel + air ↓ → Recirculation slows → Bed temp stabilizes → Steam output ↓
This automation ensures precise control of combustion conditions and heat output at all load levels.
Stable Emissions Under Load Shifts
Unlike conventional boilers that require extra tuning or struggle to meet environmental limits at partial load, CFBs maintain:
Emission Type | CFB Boiler Performance During Load Change |
---|---|
NOx | Controlled via staged air; stays low |
SO₂ | Limestone dosing adjusts dynamically |
CO | Long residence time prevents spikes |
PM (Particulates) | Stable cyclone performance |
No secondary systems (like SCR/SNCR or FGD) need to be bypassed or paused during load changes, ensuring constant regulatory compliance.
Case Study: District Heating CFB Boiler in Variable Operation
A 120 MWth CFB boiler in Northern Europe serves a district heating network with seasonal and hourly demand swings.
Operating Load | System Behavior |
---|---|
100% (Winter Peak) | Full fuel feed and limestone injection |
60% (Spring/Fall) | Reduced air and fuel flow; stable emissions |
30% (Summer Idle Mode) | Operated in low-load mode for hot water only |
Key outcomes:
NOx: maintained <100 mg/Nm³ at all loads
CO: <30 mg/Nm³, even at 30% load
Bed temp fluctuation: ±15°C across full load range
Boiler efficiency loss: only 2.5% between 100% and 30% load
Comparison: Load Handling Performance
Feature | Conventional Boiler | CFB Boiler |
---|---|---|
Minimum Stable Load | ~40–50% | 15–20% |
Load Change Response Time | Slow, prone to overshoot | Fast, stabilized by bed |
Efficiency at Partial Load | Drops sharply | Remains >90% |
Emission Stability | Requires re-tuning | Auto-adjusts dynamically |
Cycling Wear and Tear | High | Low (continuous burn) |
Summary: Why CFBs Thrive Under Variable Loads
Performance Area | CFB Boiler Advantage |
---|---|
Wide Turndown Ratio | 5:1 or more—handles base and peak load efficiently |
Thermal Buffering | Bed acts as heat reservoir for smooth transitions |
Combustion Stability | Maintains flame-free, uniform burn under all loads |
Real-Time Control | Adjusts air, fuel, and recirculation dynamically |
Emission Control | Low and stable across load range |
CFB boilers provide exceptional load-following capability, enabling industrial users and power generators to respond to fluctuating demand without sacrificing efficiency, emissions, or equipment life. For operations with variable loads, seasonal shifts, or cogeneration needs, CFB technology delivers unmatched adaptability and performance.
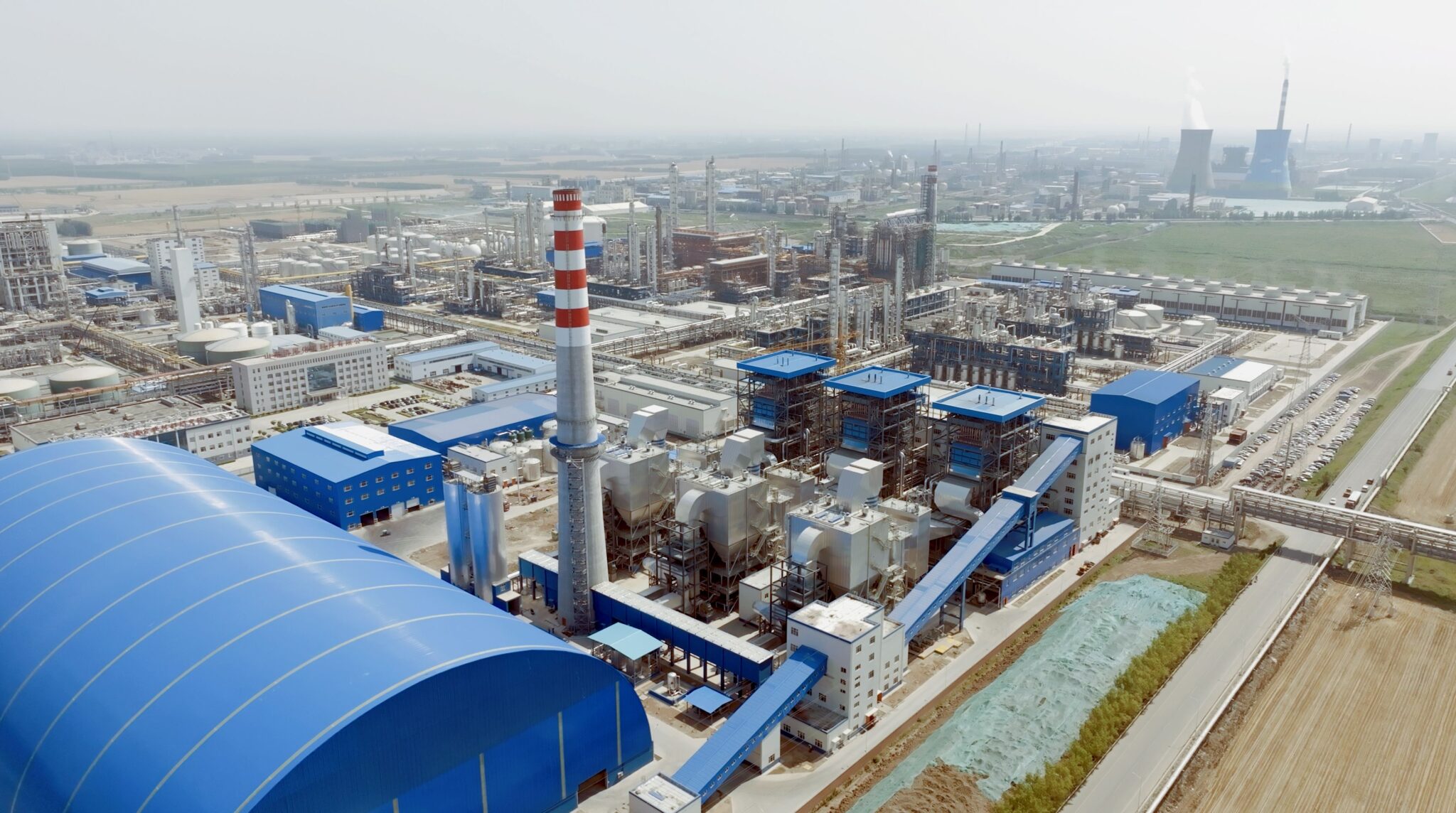
How do CFB systems reduce overall operational and maintenance costs?
![CFB boiler cost-saving operational diagram]
Prompt: Circulating Fluidized Bed (CFB) boiler system showing cost-saving features like in-furnace desulfurization, low-temperature combustion, high-ash fuel compatibility, and minimized fouling + industrial maintenance technician inspecting clean boiler tubes + cost-efficient and sustainable mood + bright industrial lighting
In large-scale industrial and utility energy systems, fuel cost, maintenance downtime, and emissions control expenses are significant contributors to total cost of ownership. Traditional combustion technologies like pulverized coal (PC), oil-fired, or stoker boilers often require complex fuel preprocessing, intensive maintenance cycles, and additional emission treatment systems—leading to high operational expenditures (OPEX) and frequent shutdowns. Circulating Fluidized Bed (CFB) systems, on the other hand, are engineered for fuel flexibility, thermal stability, and in-furnace pollution control, which collectively reduce the total cost burden of energy generation.
CFB systems reduce overall operational and maintenance costs by enabling the use of low-cost, variable-quality fuels, minimizing ash and slag-related fouling, eliminating the need for external emission scrubbers, and reducing thermal stress through low-temperature combustion. These features translate to longer equipment life, reduced maintenance frequency, and lower labor requirements. Additionally, stable combustion and heat transfer lower fuel consumption and support continuous operation with minimal unscheduled downtime.
Let’s break down the specific ways CFB technology achieves superior economic efficiency compared to conventional boiler systems.
1. Fuel Cost Savings Through Fuel Flexibility
CFB boilers are capable of burning a wide variety of low-cost fuels, including:
Low-grade coal
Lignite
Petroleum coke
Biomass residues
Refuse-derived fuel (RDF)
Industrial sludge and waste
Cost Impact Area | Conventional Boiler | CFB Boiler Benefit |
---|---|---|
Fuel Preprocessing | Pulverizing, drying | Minimal or none (tolerates high moisture) |
Fuel Cost per GJ | Higher-grade fuels only | Uses cheapest available fuels |
Fuel Switching Flexibility | Limited | Seamless with co-firing capability |
Estimated Fuel Savings:
Facilities using CFB boilers report fuel cost reductions of 20–40% when switching from oil or pulverized coal to mixed biomass or waste fuels.
2. Lower Maintenance Frequency and Downtime
CFB systems operate at lower combustion temperatures (800–900°C), preventing slagging and corrosion. This reduces wear and damage to critical components:
Component | Common Maintenance Issue | CFB Mitigation Strategy |
---|---|---|
Boiler Tubes | Slag buildup, erosion | Even heat transfer + clean combustion |
Refractory Lining | Spalling from heat shock | Lower temperature, stable load response |
Superheater Surfaces | Fouling due to ash | Lower particulate carryover, cyclone return |
Air Fans | Dust wear from ash | Lower particulate content + efficient cyclone |
Maintenance Interval Comparison:
System Type | Major Maintenance Cycle | Typical Downtime (Annual) |
---|---|---|
Pulverized Coal | Every 6–12 months | 2–4 weeks |
Oil-Fired | 9–12 months | 1–2 weeks |
CFB Boiler | 18–36 months | <1 week |
3. Reduced Need for External Emissions Controls
CFB boilers incorporate in-furnace sulfur and nitrogen control, eliminating or minimizing the need for expensive post-combustion technologies.
Emission Type | Conventional Control | CFB Control Mechanism |
---|---|---|
SO₂ | Flue Gas Desulfurization (FGD) | Limestone injection in bed |
NOx | Selective Catalytic Reduction (SCR) | Staged air + low-temp combustion |
Particulates | Baghouse or ESP | Cyclone separator + optional baghouse |
Cost Impact:
Control Equipment | Estimated CAPEX/OPEX Reduction |
---|---|
FGD System | Saved 10–15% of total plant CAPEX |
SCR Catalyst | Eliminated $1–3 million lifecycle cost |
Sootblowers and Ash Hoppers | Reduced maintenance hours by 50% |
4. High Availability and Runtime Efficiency
CFB boilers are designed for continuous operation even under fuel or load variability.
Operational Advantage | Cost-Saving Outcome |
---|---|
Stable Combustion | Fewer shutdowns, reduced restart fuel consumption |
Automatic Control Systems | Reduced operator labor and tuning requirements |
High Turndown Ratio (up to 10:1) | Operates efficiently during partial load conditions |
This leads to availability rates of over 95%, which is especially important in baseload or cogeneration plants where interruptions are costly.
5. Simplified Ash Handling and Disposal
Due to the complete combustion and stable bed conditions in CFBs:
Unburned carbon content in ash is <1%
Ash is dry and uniform, making it easier to handle
Reduced slag formation prevents manual cleaning or clinker removal
Some CFB-generated ash is even suitable for use in cement, road base, or agricultural applications, reducing disposal costs.
Case Example: Industrial Utility Plant (Eastern Europe)
A 120 MWth CFB boiler replaced three aging stoker-fired units burning lignite.
Metric | Before (Stoker) | After (CFB Boiler) |
---|---|---|
Fuel Cost (€/MWh) | 18.4 | 12.2 |
Maintenance Days/Year | 30+ | 8 |
SO₂ Removal System Cost | €5.5 million | €0.8 million (limestone only) |
Staff Required per Shift | 4 | 2 |
Annual savings exceeded €1.2 million, with full payback in 4.5 years.
Summary: CFB’s Operational and Maintenance Cost Advantages
Cost Category | How CFB Boilers Reduce Cost |
---|---|
Fuel Procurement | Burns low-cost, locally sourced or waste fuels |
Combustion Efficiency | Complete burn reduces unburned losses |
Maintenance | Fewer shutdowns, longer component life |
Emissions Control | Built-in NOx and SO₂ mitigation |
Labor and Operation | Reduced operator workload through automation |
Ash Disposal | Cleaner, lighter ash requires minimal handling |
By integrating fuel flexibility, low-emission design, and reduced maintenance overhead, CFB systems deliver robust economic performance for industries seeking low-cost, clean, and reliable heat or power generation. For facilities facing fuel price volatility and rising environmental compliance costs, CFB boilers offer a smart, long-term investment.
🔍 Conclusion
Circulating Fluidized Bed boilers offer a next-generation solution for industrial and utility-scale energy production. Compared to traditional boilers, CFB systems deliver better fuel adaptability, cleaner emissions, and more efficient thermal performance. Their ability to burn diverse fuels at lower temperatures with minimal environmental impact makes them ideal for industries focused on sustainable, flexible, and long-term boiler solutions.
📞 Contact Us
💡 Thinking about upgrading to a CFB boiler? Our team of experts can help you assess feasibility, design the right solution, and unlock the full potential of this advanced technology.
🔹 Contact us today to take your boiler system to the next level with CFB technology! 🔄🔥🌱
FAQ
Why are CFB boilers more efficient than traditional boilers?
CFB boilers ensure complete combustion at lower temperatures, resulting in improved thermal efficiency, better heat transfer, and reduced energy losses compared to conventional boilers.
What makes CFB boilers environmentally friendly?
CFB technology naturally reduces NOx emissions due to low combustion temperatures and allows in-bed desulfurization using limestone, significantly cutting SO₂ emissions without costly external scrubbers.
How do CFB boilers offer better fuel flexibility?
CFB boilers can efficiently burn a wide range of low-grade fuels including biomass, coal, petroleum coke, and industrial waste, making them highly adaptable and cost-effective.
Are CFB boilers more cost-effective in the long run?
Yes, their ability to use cheaper fuels, reduced need for external emission control, and high combustion efficiency lower operational and maintenance costs over time.
Do CFB boilers handle variable load demands better?
CFB boilers have excellent load-following capabilities, making them suitable for power plants and industrial applications where energy demand fluctuates frequently.
References
CFB Boiler Technology and Benefits – https://www.energy.gov
CFB vs Traditional Boilers Comparison – https://www.sciencedirect.com
Fuel Flexibility in CFB Combustion – https://www.researchgate.net
Emission Control with CFB Boilers – https://www.epa.gov
High-Efficiency Combustion Systems – https://www.bioenergyconsult.com
Operational Cost of CFB vs Conventional Boilers – https://www.mdpi.com
Desulfurization in CFB Technology – https://www.energysavingtrust.org.uk
CFB Boiler Load Management – https://www.iea.org
Waste-to-Energy Applications of CFB – https://www.automation.com
Future Trends in CFB Boiler Design – https://www.sciencedirect.com
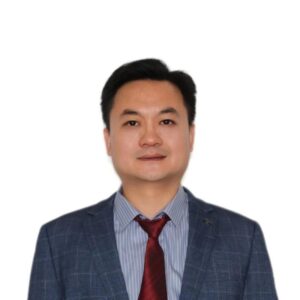