Selecting the correct capacity and size of an industrial gas-fired boiler is critical to ensuring operational efficiency, cost savings, and long-term performance. However, many companies either oversize their systems—leading to unnecessary fuel consumption and cycling losses—or undersize them, which can cause system strain, production delays, or failure to meet peak demand. Without a thorough evaluation of your facility’s heating load and operating profile, choosing the wrong boiler size can result in significant financial and functional drawbacks.
The capacity and size of an industrial gas-fired boiler you need depend on your facility’s total heat or steam demand (typically measured in BTU/hr, kg/hr, or MW), peak load requirements, operating pressure, seasonal variations, and system efficiency. Proper sizing involves analyzing both steady-state and peak usage loads, the boiler turndown ratio, and any plans for expansion. Oversizing leads to energy waste, while undersizing can compromise production. A professional boiler sizing assessment ensures the selected boiler matches your actual process requirements.
Choosing the right boiler is not about buying the biggest or the most powerful—it’s about fitting your system to your specific industrial process needs.

What factors influence the capacity requirements for an industrial gas-fired boiler?
Determining the correct capacity for an industrial gas-fired boiler is a crucial part of system design, impacting everything from operational efficiency and fuel economy to reliability, emissions, and overall cost of ownership. While it’s tempting to simply match capacity to current thermal demand, industrial boilers must be sized to accommodate a dynamic set of operational, technical, and environmental variables. Gas-fired boilers, in particular, offer advanced control and high efficiency—but only when properly matched to the application’s needs.
The capacity requirements for an industrial gas-fired boiler are influenced by several factors, including total process steam or hot water demand, operating pressure and temperature, type and variability of load, burner and boiler efficiency, gas calorific value, system heat losses, modulation capabilities, redundancy needs, and anticipated future expansion. Accurate boiler sizing involves evaluating both average and peak demand, the characteristics of gas supply infrastructure, and safety or regulatory margins to ensure optimal performance under varying load conditions.
Let’s examine these influencing factors in depth to guide proper boiler capacity selection.
🔹 1. Total Thermal Load Demand (Steam or Hot Water)
The primary driver of boiler capacity is the total amount of heat or steam required by the industrial process, building system, or equipment it serves.
Application Area | Common Boiler Output Requirements |
---|---|
Food & Beverage Processing | 500–20,000 kg/h (steam) or 200–1,000 kW (hot water) |
Textile Manufacturing | 2,000–10,000 kg/h |
Chemical Plants | 5,000–50,000 kg/h |
HVAC or District Heating | 300–2,000 kW (hot water) |
Formula for hot water boilers:
Q (kW) = Flow rate (kg/s) × 4.18 × ΔT (°C)
Formula for steam boilers:
Boiler Output (kg/h) = Total steam load ÷ Efficiency
Accurate demand profiling is critical—both for continuous and batch processes.
🔹 2. Operating Pressure and Temperature Requirements
High-pressure or superheated applications require more energy per unit of steam, which affects capacity.
Pressure Level | Impact on Boiler Output |
---|---|
Low (up to 10 bar) | Standard sizing (660–700 kcal/kg) |
Medium (10–25 bar) | Requires more capacity due to higher enthalpy |
High (>25 bar) | Requires larger combustion and heat exchange areas |
For hot water systems, ΔT (temperature rise) drives capacity. A 60°C → 90°C rise requires more output than 40°C → 70°C.
🔹 3. Boiler and Burner Efficiency
Modern gas-fired boilers offer efficiencies from 88% up to 98%, especially when condensing technology is used.
Efficiency Level | Capacity Adjustment Needed |
---|---|
Low (85–88%) | Higher input required to meet output |
Medium (89–92%) | Closer match to process demand |
High (93–98%) | Reduced size or fuel input |
Efficiency directly influences the input-output relationship—affecting both fuel use and boiler capacity planning.
🔹 4. Type of Gas and Calorific Value
Different gas types deliver different energy content, which changes how much fuel is needed to generate a certain output.
Gas Type | Typical Calorific Value (kcal/m³) |
---|---|
Natural Gas (CH₄) | 8,300–9,500 |
Biogas (60% CH₄) | 5,000–6,500 |
LPG | 10,000–11,000 |
Hydrogen-rich gas | 9,500–12,000 (varies) |
If using low-CV biogas, boiler capacity must increase to maintain desired output.
🔹 5. Load Variation and Process Type
Boilers must handle both peak and average loads effectively.
Process Type | Load Pattern | Capacity Impact |
---|---|---|
Continuous Process | Steady, predictable | Size close to average load |
Batch Process | Sudden peaks and dips | Oversize slightly or use modulation |
Seasonal Building Load | Fluctuates with outdoor temp | Consider modular or condensing systems |
Include 10–25% buffer in capacity if large peak fluctuations are expected.
🔹 6. System Heat Losses
Account for thermal losses in:
Pipework (long runs or poorly insulated lines)
Blowdown and venting
Radiation losses from boiler surfaces
Water treatment inefficiencies
Loss Type | Estimated Impact on Capacity |
---|---|
Blowdown | 2–5% of steam generation |
Distribution Loss | 5–10% in large networks |
Safety Buffer | 5–10% for redundancy and reliability |
Total extra capacity needed can range from 10–20%.
🔹 7. Turndown Ratio and Modulation Capability
Gas-fired boilers often include modulating burners with turndown ratios of 5:1 to 10:1.
Turndown Ratio | Capacity Planning Role |
---|---|
High (8:1 or 10:1) | Supports precise output control at low loads |
Low (3:1 or 4:1) | May require multiple boilers for flexibility |
If a boiler will regularly operate at partial load, high turndown is essential to avoid short cycling and efficiency loss.
🔹 8. Redundancy and Safety Planning
Industries with critical process heating may size boilers based on N+1 redundancy, meaning one additional unit is included for backup.
Redundancy Strategy | Boiler Sizing Implication |
---|---|
No Redundancy | One unit sized for full demand |
N+1 Strategy | Two or more units covering full load |
Modular Redundancy | 3–4 smaller boilers sharing load |
This improves uptime and allows for maintenance without process disruption.
🔹 9. Future Expansion
If production increases are planned, boilers should be sized with headroom or modularity in mind.
Growth Anticipated | Sizing Strategy |
---|---|
None | Match current demand + 10% margin |
Moderate (2–5 yrs) | Add 20–30% buffer or install 2 units |
High/Uncertain | Choose scalable modular boiler system |
Real-World Case: Beverage Bottling Plant
Current steam demand: 4,500 kg/h
Anticipated growth: +25% in 2 years
Efficiency: 91%
Blowdown & system losses: 12%
Modulating gas burner: 6:1 turndown
Sizing Calculation:
(4,500 kg/h ÷ 0.91) = 4,945 kg/h
4,945 × 1.12 (for losses) = 5,538 kg/h
+25% for expansion → ~6,923 kg/h → Rounded up to 7 TPH
Installed: 2 × 4 TPH gas-fired boilers, staged control with DCS
Result: High efficiency at low load + redundancy + future scalability
Summary: Key Factors for Sizing a Gas-Fired Boiler
Sizing Factor | Role in Capacity Determination |
---|---|
Total Steam/Heat Demand | Primary sizing input |
Operating Pressure/Temp | Affects energy per unit output |
Fuel Calorific Value | Adjusts input volume for energy delivery |
Boiler Efficiency | Impacts required input/output balance |
Process Load Profile | Drives modulation or multi-unit system need |
System Losses | Increases capacity to meet actual usable output |
Modulation Capability | Enhances performance at variable loads |
Redundancy Requirements | May require additional units |
Growth/Expansion Planning | Influences oversizing or modular design |
By factoring in these variables, industries can select a right-sized gas-fired boiler system that delivers reliable performance, optimal efficiency, and long-term scalability, all while supporting emissions targets and operational flexibility.
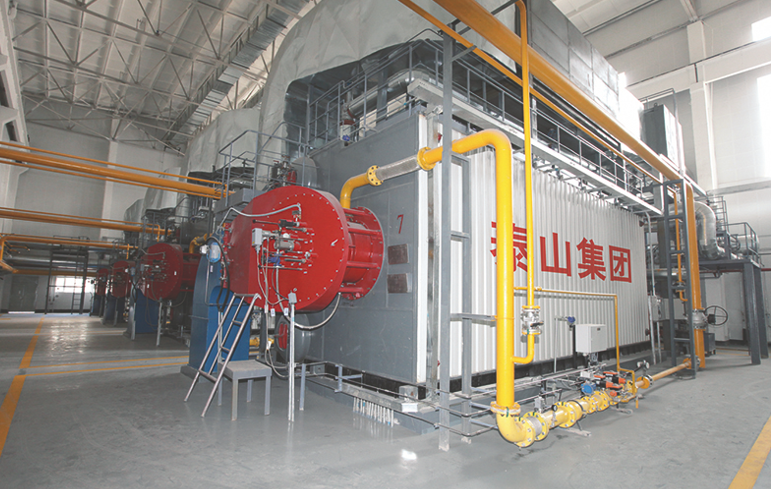
How do you calculate gas boiler size based on steam or hot water load?
Choosing the correct gas boiler size is fundamental for achieving optimal energy efficiency, cost-effectiveness, and reliable performance in industrial operations. A boiler that’s too small won’t meet peak demand, causing process disruptions. One that’s too large may cycle excessively and waste fuel. The right size must be carefully calculated based on the actual thermal load—either steam or hot water—required by your processes or heating systems.
Gas boiler size is calculated based on the required steam or hot water load using thermodynamic principles. For steam systems, the boiler size is determined from the total mass flow rate of steam (in kg/h or TPH) required by the application, adjusted for boiler efficiency and system losses. For hot water systems, the required thermal output is calculated in kilowatts (kW) or BTU/hr using the flow rate and temperature rise, then adjusted for boiler efficiency. Safety margins and potential future expansion are also factored in to ensure robust performance under varying operating conditions.
Here’s a step-by-step guide for accurately calculating gas boiler size based on steam or hot water demand.
🔹 A. Gas Boiler Sizing for Steam Load
Step 1: Determine Steam Demand (kg/h or TPH)
Sum up the steam requirements of all process equipment and heating points.
Example:
Pasteurizer: 1,800 kg/h
Cleaning system: 700 kg/h
Heat exchanger: 2,000 kg/h
Total Steam Load = 4,500 kg/h
Step 2: Adjust for Boiler Efficiency
Boilers are not 100% efficient. Adjust the steam output to account for combustion and radiation losses.
Formula:
Boiler Size (kg/h) = Total Steam Load ÷ Boiler Efficiency
Assume: Boiler efficiency = 90% (0.90)
4,500 ÷ 0.90 = 5,000 kg/h
Step 3: Account for System Losses
System losses include:
Blowdown (2–5%)
Piping heat loss (5–10%)
Startup inefficiencies
Add 10–15% extra:
5,000 × 1.10 = 5,500 kg/h → Rounded to **5.5 TPH**
✅ Final Boiler Size: 5.5 TPH steam output capacity
If growth is expected, size to 6–7 TPH or use modular boilers.
🔹 B. Gas Boiler Sizing for Hot Water Load
Step 1: Determine Water Flow Rate and Temperature Rise
Hot water load depends on the volume of water to be heated and the desired temperature increase.
Formula:
Q (kW) = m × Cp × ΔT
Where:
Q = Boiler output (kW)
m = Flow rate in kg/s or L/s
Cp = Specific heat of water = 4.18 kJ/kg°C
ΔT = Temp rise (°C)
Example:
Water flow: 15,000 liters/hour = 4.17 L/s ≈ 4.17 kg/s
Inlet temp: 40°C
Outlet temp: 90°C
ΔT = 50°C
Q = 4.17 × 4.18 × 50 = 872.6 kW
Step 2: Adjust for Boiler Efficiency
Assume efficiency = 92%
Net boiler size = 872.6 ÷ 0.92 = 948.5 kW
Step 3: Add Losses and Margin
For safety and variation:
948.5 × 1.10 = 1,043.4 kW → Rounded to **1,050 kW**
✅ Final Boiler Size: 1,050 kW hot water output capacity
Modular units can be installed in stages (e.g., 2 × 525 kW)
🔹 Quick Reference Sizing Table
Boiler Application | Common Input Unit | Sizing Method |
---|---|---|
Steam Generation | kg/h or TPH | Total steam load ÷ efficiency × 1.1 |
Hot Water Supply | kW or BTU/hr | Q = Flow × 4.18 × ΔT ÷ efficiency × 1.1 |
🔹 Real-World Example: Textile Factory
Steam Load: 6,000 kg/h
Boiler Efficiency: 91%
System Losses: 12%
Expansion Planned: +15% in 3 years
Calculation:
6,000 ÷ 0.91 = 6,593
6,593 × 1.12 = 7,384
7,384 × 1.15 (expansion) = 8,492 → Final size: 8.5 TPH
Recommended Setup:
2 × 4.5 TPH gas-fired modular boilers for flexibility and redundancy
Summary: Steps to Calculate Gas Boiler Size
Step | Action |
---|---|
1. Measure Load | Calculate total steam or hot water demand |
2. Adjust for Efficiency | Divide by boiler thermal efficiency |
3. Include Losses | Add 10–15% for system heat loss and blowdown |
4. Plan for Growth | Add buffer or install modular units for expansion |
5. Select Boiler Capacity | Round up to next standard size or configure multiple units |
Properly sizing your gas boiler ensures maximum efficiency, safe operation, and optimal lifecycle costs—delivering the right amount of thermal energy exactly when it’s needed.
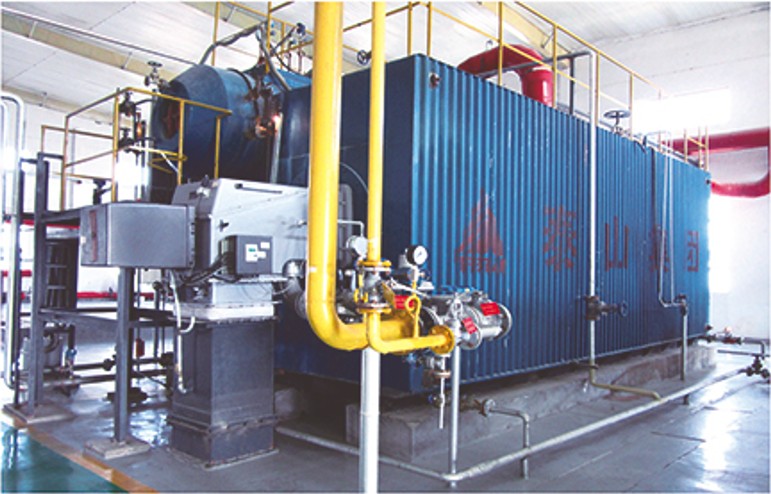
What is the difference between input capacity and output efficiency in boiler selection?
When selecting a boiler, two key specifications are frequently discussed but often misunderstood: input capacity and output efficiency. While these terms are related, they represent fundamentally different aspects of boiler performance. Confusing them can lead to incorrect sizing, poor fuel efficiency, excessive operating costs, or an inability to meet process demands. Understanding the distinction helps ensure a system that is accurate, cost-effective, and energy-efficient.
Input capacity refers to the amount of fuel energy supplied to the boiler, typically measured in kilowatts (kW), BTU/hr, or megajoules (MJ), while output efficiency represents the percentage of that input energy that is effectively converted into usable heat or steam. Input is the raw energy entering the system, whereas output efficiency defines how much of that energy is successfully delivered to the process. Proper boiler selection must consider both values to ensure the unit meets thermal demand without wasting energy.
Below is a detailed comparison to clarify how these parameters influence boiler specification and performance.
🔹 What Is Input Capacity?
Definition:
Input capacity is the maximum amount of energy a boiler can consume in the form of fuel (gas, oil, biomass, etc.) per unit of time.
Parameter | Description |
---|---|
Measured In | kW, BTU/hr, kcal/h, or MJ/h |
Determined By | Burner size, fuel flow rate, combustion power |
Purpose | Indicates boiler’s energy intake capability |
Example | A boiler rated at 1,000 kW input burns fuel that provides 1,000 kW of energy per hour |
Key Point: Input capacity does not represent usable heat—just the energy entering the system.
🔹 What Is Output Efficiency?
Definition:
Output efficiency (thermal efficiency) is the percentage of input energy that is successfully converted into usable steam or hot water.
Parameter | Description |
---|---|
Measured As | Percentage (%) |
Typical Range | 85–98% depending on boiler type |
Represents | Fuel-to-steam or fuel-to-heat conversion rate |
Formula |
Efficiency (%) = (Useful Output Energy ÷ Input Energy) × 100
Example:
Input: 1,000 kW
Efficiency: 90%
Output = 0.90 × 1,000 = 900 kW of usable heat
🔹 Key Differences at a Glance
Feature | Input Capacity | Output Efficiency |
---|---|---|
What It Measures | Energy in (fuel supply) | Energy out (usable thermal energy) |
Units | kW, BTU/hr, MJ/h | Percentage (%) |
Role in Sizing | Sets upper fuel consumption limit | Determines real heat/steam output |
Impact on Costs | Affects fuel demand | Affects energy bill per unit of output |
Example Use Case | Choosing fuel piping, burner specs | Selecting boiler based on heat demand |
🔹 Why Both Matter in Boiler Selection
✔️ Input Capacity:
Ensures adequate combustion and burner sizing
Needed for selecting fuel supply lines and regulators
Prevents fuel starvation at peak loads
✔️ Output Efficiency:
Ensures the boiler meets actual process heating demands
Determines fuel consumption per unit of output
Drives operational cost and carbon footprint
🔹 Real-World Example: Manufacturing Plant
Steam Requirement: 6,000 kg/h
Enthalpy per kg steam (at 10 bar): ~660 kcal/kg
Total Output Energy Needed:
6,000 × 660 = 3,960,000 kcal/h ≈ 4,600 kW
If boiler efficiency = 92%
Required Input:
4,600 ÷ 0.92 = 5,000 kW input capacity
Conclusion:
Select boiler with input capacity ≥5,000 kW
It will deliver 4,600 kW usable steam at 92% efficiency
🔹 Boiler Types and Their Efficiencies
Boiler Type | Typical Efficiency Range (%) | Notes |
---|---|---|
Fire Tube (non-condensing) | 80–88 | Standard for low to mid-pressure systems |
Water Tube | 85–92 | Better at higher pressure & temperatures |
Condensing Gas Boiler | 92–98 | Highest efficiency at low return temps |
Summary: Input Capacity vs. Output Efficiency
Comparison Area | Input Capacity | Output Efficiency |
---|---|---|
Definition | Maximum energy the boiler consumes | Portion of that energy turned into output |
Unit | kW, BTU/hr, MJ/h | % (0–100%) |
Importance in Sizing | Needed for fuel system design | Needed to meet heating/steam load |
Impact on OPEX | Defines fuel volume required | Drives how much energy is wasted or used |
Informs Selection | Fuel input rating | Actual thermal output rating |
By understanding and correctly applying both input capacity and output efficiency, you can select a boiler that meets your process needs, minimizes fuel costs, and complies with energy efficiency goals—ensuring high performance and sustainability over the long term.
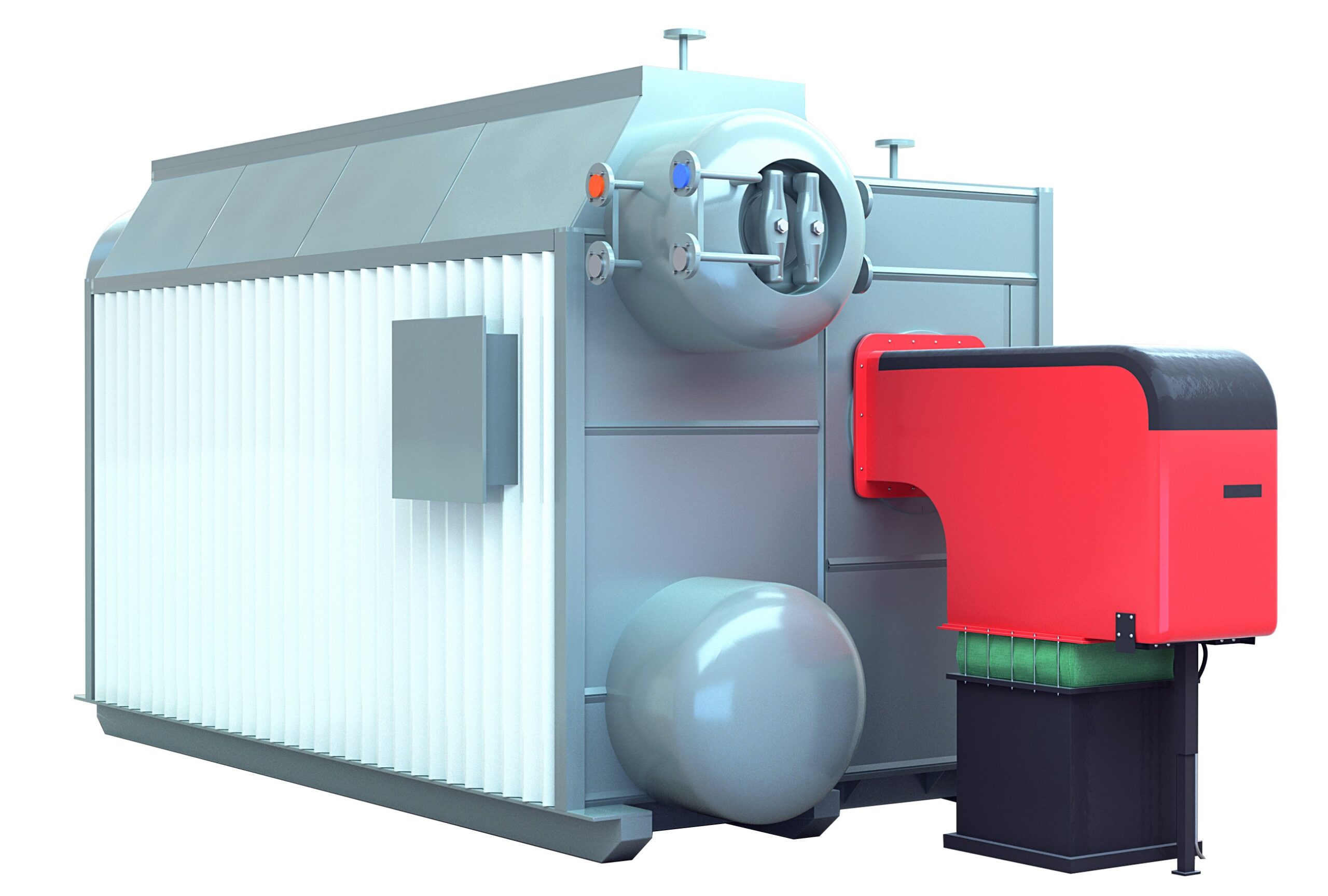
How does the boiler turndown ratio affect sizing and part-load operation?
In real-world industrial applications, thermal demand is rarely constant. Most systems operate at varying loads throughout the day, week, or season. A boiler must be able to match this demand efficiently, or it risks inefficient cycling, wasted energy, and mechanical wear. This is where the turndown ratio becomes a critical specification. It directly affects how well the boiler operates under part-load conditions and how flexibly it adapts to changing thermal requirements. Selecting the right turndown ratio ensures your boiler is not only sized correctly but also optimized for realistic operational behavior.
The boiler turndown ratio affects sizing and part-load operation by determining how far the boiler can reduce its output below maximum capacity while still operating efficiently and stably. A higher turndown ratio allows a boiler to respond to fluctuating loads without frequent on-off cycling, maintaining better fuel efficiency, combustion stability, and operational reliability. It enables proper matching between boiler capacity and actual demand, especially in systems with variable or seasonal load profiles.
Let’s explore how turndown ratio influences boiler performance, especially during partial-load operation.
🔹 What Is Turndown Ratio?
Definition:
The turndown ratio is the ratio between a boiler’s maximum and minimum firing rates—or how much the boiler can modulate its heat output.
Formula:
Turndown Ratio = Maximum Firing Rate ÷ Minimum Stable Firing Rate
Turndown Ratio | Interpretation |
---|---|
10:1 | Boiler can modulate from 100% to 10% load |
5:1 | Operates from 100% to 20% load |
3:1 | Limited to 100% to 33% load |
Example: A 5 TPH boiler with a 5:1 turndown ratio can operate from 5 TPH down to 1 TPH without shutting off.
🔹 Why It Matters for Part-Load Operation
✅ High Turndown Ratio:
Boiler stays on longer during low demand
Reduces frequent start/stop cycles
Maintains steady temperature/pressure control
Improves fuel efficiency at partial loads
Minimizes mechanical wear on burner, valves, controls
❌ Low Turndown Ratio:
Boiler cannot match low loads
Cycles on/off repeatedly
Leads to efficiency losses due to purge air, startup fuel waste
Increased emissions during startup/shutdown phases
Greater maintenance and downtime
🔹 Boiler Turndown and Sizing Interaction
When selecting capacity, turndown ratio directly affects how closely you can size the boiler to peak load while still maintaining efficiency at lower loads.
Load Profile | Turndown Ratio Needed | Boiler Sizing Strategy |
---|---|---|
Stable Base Load | 3:1 or 4:1 may suffice | Size boiler near average load |
Variable Load (Batch) | 5:1 to 10:1 recommended | Slight oversize OK with high turndown |
Seasonal/Intermittent | 10:1 or modular preferred | Use multiple smaller boilers or condensing |
🔹 Efficiency vs. Load Curve
The chart below illustrates how turndown affects part-load efficiency:
Load (%) | High Turndown Boiler Efficiency | Low Turndown Boiler Efficiency |
---|---|---|
100% | 91–95% | 90–94% |
50% | 88–92% | 75–85% (due to cycling) |
25% | 85–90% | 65–75% (cycling, heat loss) |
10% | 82–88% | Boiler may shut down |
🔹 Real-World Example: Manufacturing Facility
Peak Steam Load: 6,000 kg/h
Minimum Load (Night): 1,000 kg/h
Turndown Needed:
6,000 ÷ 1,000 = 6:1 turndown
Scenario A: Boiler with 3:1 Turndown
Can only go down to 2,000 kg/h
Must cycle on/off at night
12% energy wasted due to frequent restarts
Scenario B: Boiler with 8:1 Turndown
Stably modulates from 6,000 to 750 kg/h
Smooth operation across all shifts
Improved control, lower fuel usage, less wear
🔹 Turndown Ratio by Boiler Type
Boiler Type | Typical Turndown Ratio | Notes |
---|---|---|
On/Off Fire Tube | 1:1 | No modulation; inefficient at part load |
Dual-Stage Burners | 2:1 or 3:1 | Two output levels only |
Modulating Gas Burner | 5:1 to 10:1 | Ideal for variable load systems |
Condensing Boilers | Up to 15:1 | Excellent for HVAC and seasonal heating |
Modular Boiler Systems | 10:1+ (combined) | Staged firing allows seamless load matching |
🔹 Summary: Turndown Ratio’s Effect on Sizing & Efficiency
Consideration | Impact of Turndown Ratio |
---|---|
Boiler Sizing Flexibility | Higher ratio = closer sizing to peak load |
Part-Load Efficiency | Higher ratio = less cycling, better fuel usage |
Control Stability | Enables smoother pressure/temperature regulation |
Fuel Savings | Reduces purge/startup losses at low load |
Operational Life | Fewer on/off cycles mean less equipment wear |
In conclusion, a high turndown ratio is essential when load variability is present. It allows the boiler to adapt dynamically, ensuring optimal performance across a range of operating conditions, while maximizing efficiency and minimizing mechanical strain. It should be considered a core parameter—alongside capacity, efficiency, and fuel type—when designing and selecting your industrial gas-fired boiler system.
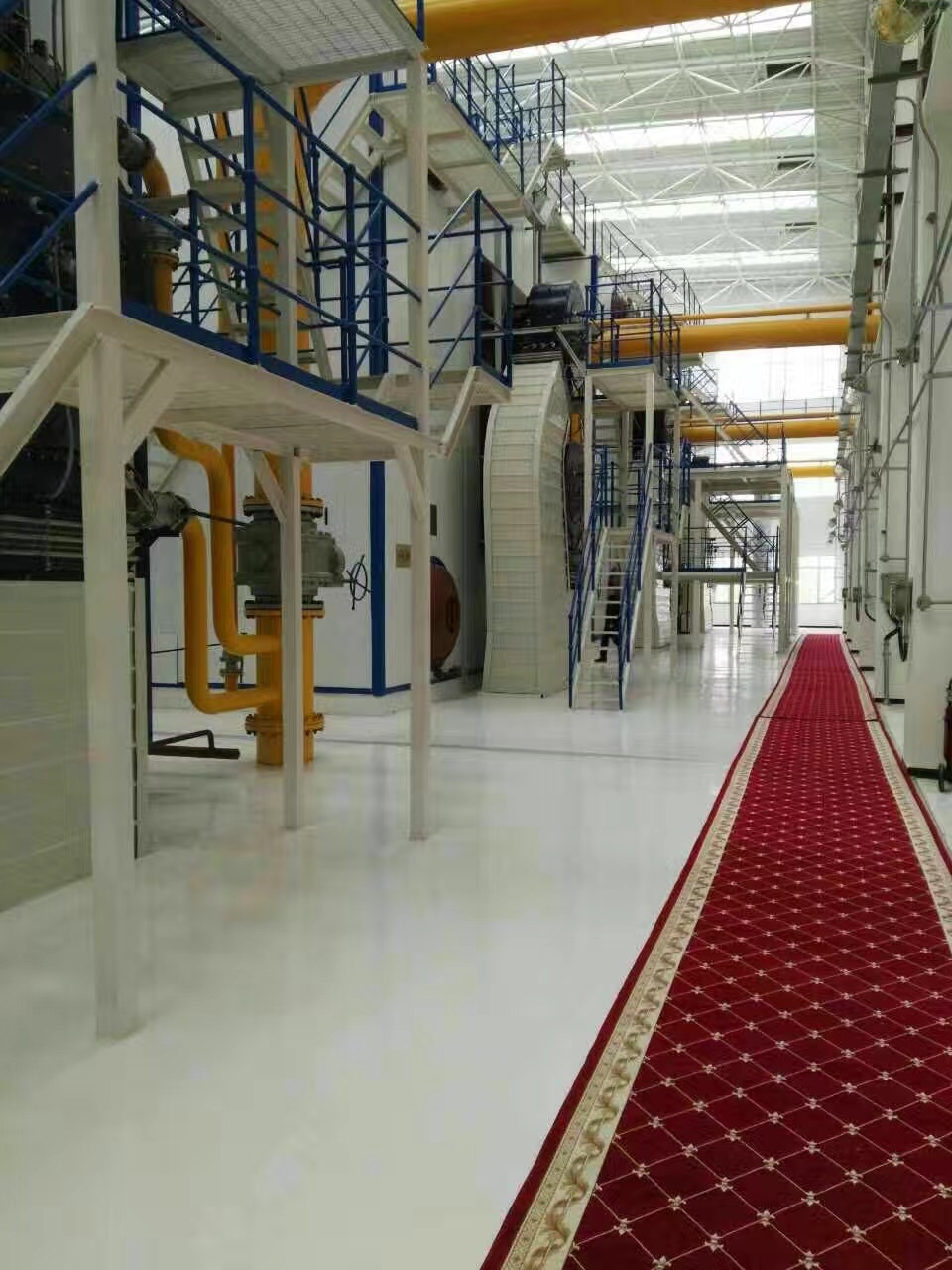
Why is it important to consider future expansion when sizing a boiler?
When planning a new boiler installation, many project teams focus solely on current heating or steam requirements. While this approach might meet immediate needs, it can lead to major limitations, unexpected costs, and operational bottlenecks down the road. Industrial processes, production facilities, campuses, and even municipal utilities are rarely static—growth is almost inevitable. Whether it’s a new product line, an expanded building, or increased seasonal demand, the boiler system must be ready to adapt. This makes future expansion planning a critical consideration during the sizing and design of any industrial boiler system.
It is important to consider future expansion when sizing a boiler because thermal energy demand often increases over time due to production growth, facility upgrades, or operational scaling. Sizing a boiler to accommodate future needs—either by including additional capacity margin, designing for modular add-ons, or reserving space and utilities—ensures long-term reliability, prevents costly retrofits, avoids equipment overloading, and supports operational flexibility. Proactively planning for expansion allows for better investment efficiency, energy planning, and infrastructure optimization.
Here’s how and why future growth should be factored into your boiler system planning.
🔹 1. Future Demand Is Often Underestimated
Common Expansion Scenarios | Boiler Impact |
---|---|
New production lines or shifts | Increases steam or hot water demand |
Building or facility additions | Extends heating or process network |
Product/process changes | May require higher pressure or temperature |
Seasonal or geographic growth | Peaks demand beyond initial capacity |
Case: A dairy plant designed its boiler for current pasteurization loads but later added a drying unit. The original boiler couldn’t meet both loads simultaneously—leading to downtime and expensive upgrades.
🔹 2. Retrofitting Undersized Boilers Is Costly
If future growth isn’t planned for, businesses may later face:
Boiler replacement or derating
Expensive civil work to expand boiler room
Extended downtime during equipment change
Safety and compliance issues due to overloading
Estimated Retrofit Costs (vs. original oversize or modular design):
Action | Cost Multiplier (vs. planned) |
---|---|
Adding new boiler unit later | 1.5× to 2× |
Boiler room expansion | 2× to 4× |
Upgrading burner or controls | 1.2× to 1.8× |
Planning ahead avoids rework and disruptions.
🔹 3. Boiler Oversizing vs. Modular Scalability
There are two main strategies for expansion readiness:
✅ Option 1: Oversize the Initial Boiler
Pros | Cons |
---|---|
Immediate capacity available | Reduced efficiency at low load |
No additional units required | Higher initial capital cost |
Simple control architecture | Greater space and fuel infrastructure |
✅ Option 2: Use a Modular System
Pros | Cons |
---|---|
Scalable with process demand | Slightly more complex piping |
Higher efficiency at all loads | May require coordinated control |
Easier maintenance (N+1 setups) | Slight increase in footprint |
Best Practice: Combine both—install one unit now, reserve piping and space for more.
🔹 4. Planning Infrastructure for Expansion
Even if additional boilers won’t be installed immediately, design your system to make it “plug-and-play” ready.
Infrastructure Area | Planning Strategy |
---|---|
Boiler Room Floor Space | Reserve 25–50% area for new unit |
Steam Header | Oversize or stub future ports |
Control System | Use PLC with extra I/O for future devices |
Fuel Line & Water Feed | Install valves or tees for expansion branch |
Chimney/Exhaust | Size for multi-boiler flow |
Electrical | Capacity in panels for second unit |
🔹 5. Control and Automation Scalability
When planning for future growth, ensure that automation and control systems can adapt.
System | What to Include |
---|---|
Boiler PLC | Expansion-ready software and hardware |
SCADA Interface | Multi-boiler management capability |
Burner Management System | Modular burner compatibility |
Alarms and Interlocks | Preconfigured zones for added equipment |
🔹 6. Real-World Example: Beverage Processing Plant
Initial Steam Demand: 4,500 kg/h
Forecasted Growth (3 years): 40% increase
Design Strategy: Installed 1 × 6 TPH boiler + space and headers for 1 × 3 TPH unit
Control Panel: Preprogrammed for dual-boiler operation
Outcome:
Phase 1 met demand with efficiency
Phase 2 expansion added new boiler in 48 hours
Avoided $180,000 in retrofit costs
🔹 Summary: Key Expansion Planning Factors in Boiler Sizing
Expansion Factor | Consideration for Boiler System |
---|---|
Projected Load Growth | Add 20–40% capacity margin or modular design |
Facility Layout | Reserve floor space and pipe routing |
Control and Utility Design | Configure for multi-boiler integration |
Redundancy Requirements | Plan for N+1 or backup boiler integration |
Capital Budget Planning | Account for staged investments |
Planning for future expansion ensures your boiler system is future-proof, efficient, and adaptable—allowing your facility to scale production, add new processes, and meet energy demands without costly retrofits or delays. A little foresight during the design phase translates into years of operational and financial benefits.
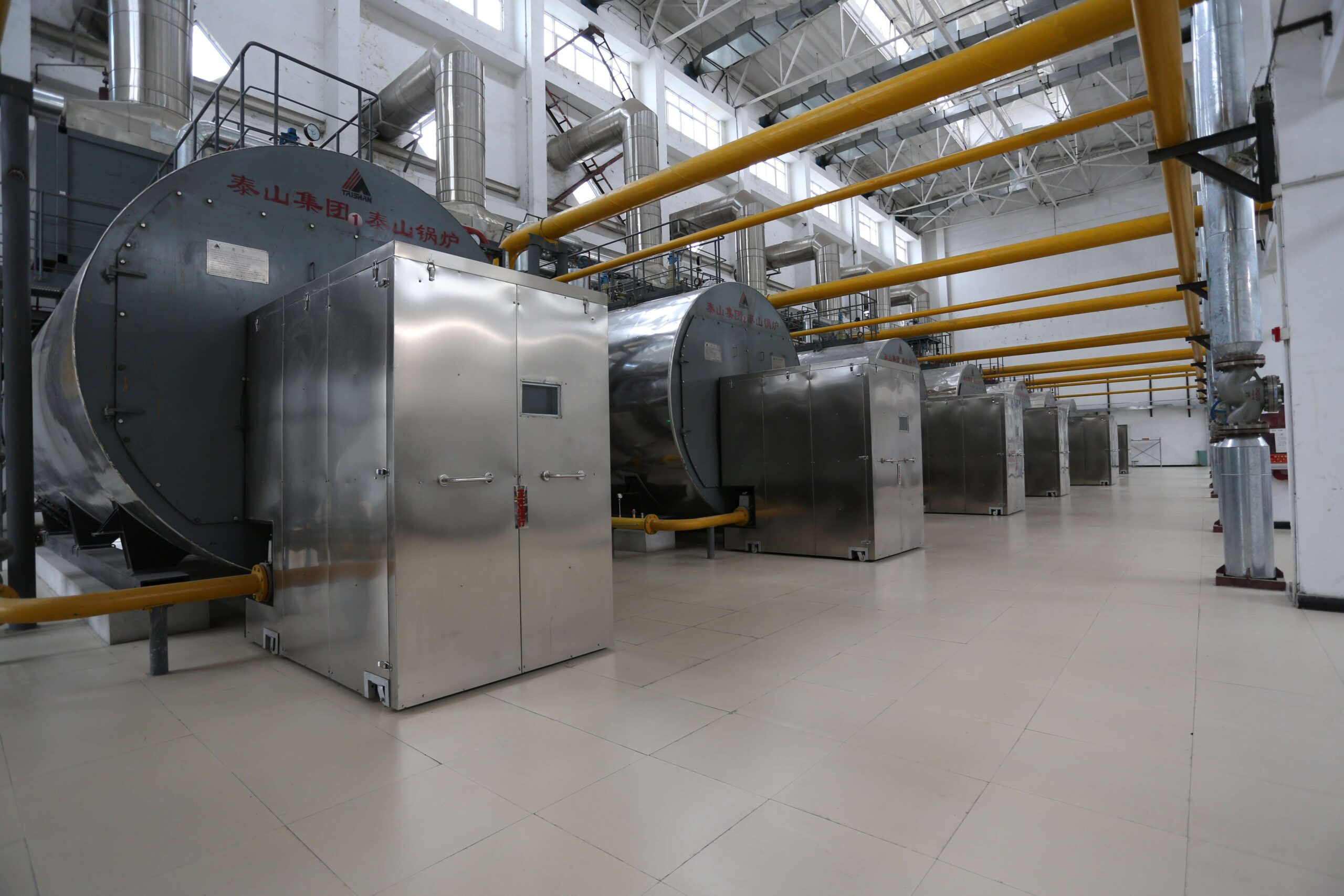
What space and installation constraints should be considered in sizing decisions?
When sizing an industrial boiler, capacity and efficiency are only part of the equation. The physical environment where the boiler will be installed plays a critical role in feasibility, safety, and long-term performance. A system that technically meets thermal demand may still fail in real-world conditions if it doesn’t fit the available footprint, comply with building codes, or allow safe maintenance access. Overlooking spatial and installation constraints during sizing can lead to costly redesigns, delays, code violations, or safety hazards.
Space and installation constraints must be considered during boiler sizing decisions to ensure that the selected system fits the available physical footprint, complies with clearance and ventilation requirements, supports proper piping and flue gas routing, allows safe and convenient maintenance access, accommodates fuel storage and delivery, and aligns with structural load capacities. These factors influence boiler layout, burner configuration, auxiliary equipment placement, and the overall operability of the system.
Here’s a comprehensive guide to the space and installation factors that affect boiler sizing and implementation success.
🔹 1. Footprint and Equipment Dimensions
Each boiler has specific length × width × height dimensions depending on its type and capacity.
Boiler Type | Typical Capacity Range | Approx. Footprint (L × W) |
---|---|---|
Fire-Tube (3 TPH) | 1–6 TPH | ~4.5 m × 2.5 m |
Water-Tube (10 TPH) | 6–25 TPH | ~7–12 m × 3–5 m |
Condensing Gas (1 MW) | 0.5–2 MW | ~2.5 m × 1.2 m |
🧩 Key Point: Ensure the selected boiler size fits comfortably in the designated mechanical room or utility space.
🔹 2. Clearance for Maintenance and Access
Every boiler requires minimum clearance distances for safe operation, inspections, and routine servicing.
Area | Recommended Minimum Clearance |
---|---|
Front (burner side) | 1.5–2.0 meters |
Rear (inspection door) | 1.0–1.5 meters |
Sides | 0.8–1.2 meters |
Top (manway/lift zone) | 1.5 meters |
Insufficient clearance may:
Void manufacturer warranty
Violate fire or building codes
Increase downtime and maintenance difficulty
🔧 Best Practice: Design with removable access zones and unobstructed service paths.
🔹 3. Ceiling Height and Crane Access
The total system height includes:
Boiler shell
Flue outlet
Valves and instruments
Economizer (if present)
Boiler Element | Typical Height Range |
---|---|
Medium fire-tube boiler | 2.5–3.5 meters |
Water-tube boiler | 3.5–5.5 meters |
Chimney connection zone | +0.5–1.5 meters |
Also consider:
Overhead hoist/crane clearance for lifting burner heads, tubes, or manways
Vertical piping and chimney alignment
🔹 4. Structural Floor Load Capacity
Boilers are heavy equipment, especially when water-filled and operating.
Boiler Size | Operating Weight Range |
---|---|
5 TPH fire-tube | 8–12 metric tons |
10 TPH water-tube | 18–25 metric tons |
20 TPH twin-drum | 35–60 metric tons |
🏗️ Ensure the floor structure:
Can support static and dynamic loads
Is designed with vibration dampening if necessary
Accommodates transport/installation paths
🔹 5. Fuel Storage and Delivery
The size of the boiler dictates the type, volume, and location of fuel supply systems.
Fuel Type | Storage Considerations |
---|---|
Natural Gas | Pipe size, gas train proximity, regulator room |
Fuel Oil | Bunded tanks, day tanks, fill access |
Biomass | Hopper size, conveyance system |
Ensure:
Safe access for tankers or fuel trucks
Fire safety zoning for flammable liquid storage
Spill containment systems for oil tanks
🔹 6. Ventilation and Combustion Air
Gas and oil boilers require adequate airflow for combustion and cooling.
Capacity Range | Minimum Air Volume Required |
---|---|
1–5 TPH | 2.5–5 m³/min |
6–10 TPH | 6–10 m³/min |
Intake must be:
Unobstructed, sized per burner manufacturer specs
Located away from exhaust points
Protected by louvers or automatic dampers
Also plan for ventilation fans if natural draft is insufficient.
🔹 7. Flue Gas Venting and Chimney Design
The chimney or stack must:
Handle full combustion output volume
Be accessible for cleaning and inspection
Have enough draft or be assisted by fans
Boiler Capacity | Flue Diameter Range (Gas-fired) |
---|---|
1–2 TPH | 300–400 mm |
5 TPH | 500–700 mm |
10+ TPH | 800–1,200 mm |
Consider:
Vertical clearance (typically 3+ meters above roof)
Stack support structure
Horizontal routing for economizers or duct dampers
🔹 8. Piping Layout and Expansion Zones
Steam, feedwater, gas, and blowdown lines must be:
Safely routed
Sized correctly for capacity
Supported with expansion joints
📌 Leave space for:
Steam header branching
Pressure relief valves and drains
Optional water treatment skids or softeners
🔹 9. Utility Interfaces and Control Rooms
Install the boiler near:
Electrical power distribution
Water softening and treatment units
SCADA or control panels
Emergency shutoff zones
Plan control panel placement with:
Sightlines to boiler
Cable trays or conduits
Safety interlock access
🔹 Real-World Case: Food Processing Facility
Need: 5 TPH gas boiler for a new product line
Space Provided: 8 m × 4 m × 5 m
Constraints Identified:
Burner required 1.5 m frontal access
Gas regulator zone needed extra wall space
Flue routed through existing wall chase
Solution:
Selected compact horizontal fire-tube boiler
Shifted boiler by 0.5 m to allow maintenance door swing
Installed low-profile stack with side economizer to fit ceiling
Control system placed on external wall for visibility and access
🔹 Summary: Key Space & Installation Constraints to Consider
Constraint Area | Sizing and Design Consideration |
---|---|
Footprint & Clearance | Ensure fit and safe access for maintenance |
Ceiling & Vertical Limits | Accommodate boiler height, stack, and lifting |
Structural Load | Verify floor strength for boiler and accessories |
Fuel Storage | Allocate room for tanks, regulators, and lines |
Combustion Air & Ventilation | Match with boiler combustion requirements |
Flue Gas Routing | Size and align chimneys or ducts properly |
Piping & Utility Access | Leave room for valves, headers, and insulation |
Control System Interface | Design accessible and expandable automation zones |
By integrating these spatial and installation considerations during the boiler sizing phase, engineers and facility managers can ensure a system that is efficient, safe, maintainable, and adaptable—avoiding unnecessary retrofit costs or safety issues in the future.
🔍 Conclusion
Selecting the correct capacity and size for an industrial gas-fired boiler is essential for optimizing fuel efficiency, maintaining production reliability, and avoiding unnecessary operating costs. By carefully evaluating your facility’s heating demands, efficiency targets, and operational flexibility, you can choose a boiler that delivers precise performance and long-term value. A properly sized system not only enhances energy savings but also ensures compliance, safety, and scalability.
📞 Contact Us
💡 Need expert help calculating your gas-fired boiler capacity? Our engineering team offers custom load analysis and sizing recommendations tailored to your industrial process.
🔹 Get in touch today to size your gas boiler right—efficiently, safely, and smartly! 🔥📐
FAQ
How do you determine the required capacity for a gas-fired boiler?
The required capacity is based on your industrial process steam or heating load. It’s usually measured in tons per hour (TPH) for steam boilers or BTU/hr for hot water systems. Accurate assessment of peak load, operating conditions, and redundancy needs helps in proper sizing.
What are typical capacity ranges for industrial gas-fired boilers?
Gas-fired industrial boilers typically range from 0.5 TPH to over 100 TPH for steam generation and from 0.3 million to 150+ million BTU/hr for hot water applications, depending on industry size and usage.
What factors influence the sizing of a gas-fired boiler?
Key sizing factors include total heat or steam load, process requirements, fuel type, feedwater temperature, pressure demands, system losses, and operational hours. Safety margins and future expansion should also be considered.
Why is proper boiler sizing important?
Oversized boilers lead to cycling losses and higher operational costs, while undersized boilers fail to meet process demands. Proper sizing ensures optimal efficiency, stable performance, and energy savings.
Can a gas-fired boiler be customized for specific industrial applications?
Yes. Custom sizing and configurations are available to match specific pressure ratings, fuel usage, footprint limitations, and control system integrations. Consulting with a boiler expert or manufacturer ensures accurate selection.
References
Boiler Sizing Guidelines for Industry – https://www.energy.gov
Gas-Fired Boiler Design and Capacity Planning – https://www.sciencedirect.com
Steam Demand and Boiler Sizing – https://www.researchgate.net
Industrial Boiler Load Calculation – https://www.bioenergyconsult.com
Gas Boiler Efficiency and Capacity – https://www.epa.gov
BTU/hr and TPH Conversion in Boilers – https://www.energysavingtrust.org.uk
Industrial Heating System Sizing – https://www.mdpi.com
Gas-Fired Boiler Performance Optimization – https://www.iea.org
Modular Boiler System Design – https://www.automation.com
Right-Sizing Boilers for Efficiency – https://www.sciencedirect.com
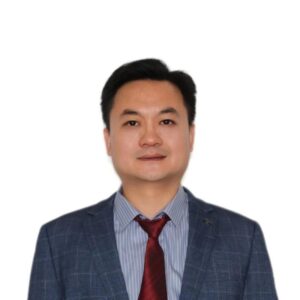