Selecting the proper capacity and size for an industrial coal-fired boiler is essential to achieving efficient heat output, fuel economy, and long-term operational stability. Many companies unknowingly install over- or under-sized boilers, which leads to issues such as energy waste, insufficient steam supply, frequent cycling, or premature wear and tear. Without a detailed evaluation of your actual process requirements, choosing the wrong size can severely impact productivity and operating costs.
The capacity and size of an industrial coal-fired boiler you need depend on your facility’s steam or hot water demand (typically measured in tons/hour or BTU/hr), peak load conditions, operating pressure, process duration, fuel type, and thermal efficiency. The ideal boiler capacity should align with the maximum load with an appropriate safety margin—while factoring in seasonal variation and possible future expansion. Proper sizing also considers combustion efficiency, fuel quality, and system integration to ensure performance and compliance.
To avoid costly mistakes, a data-driven and customized boiler sizing strategy is key. Let’s walk through what you need to consider.
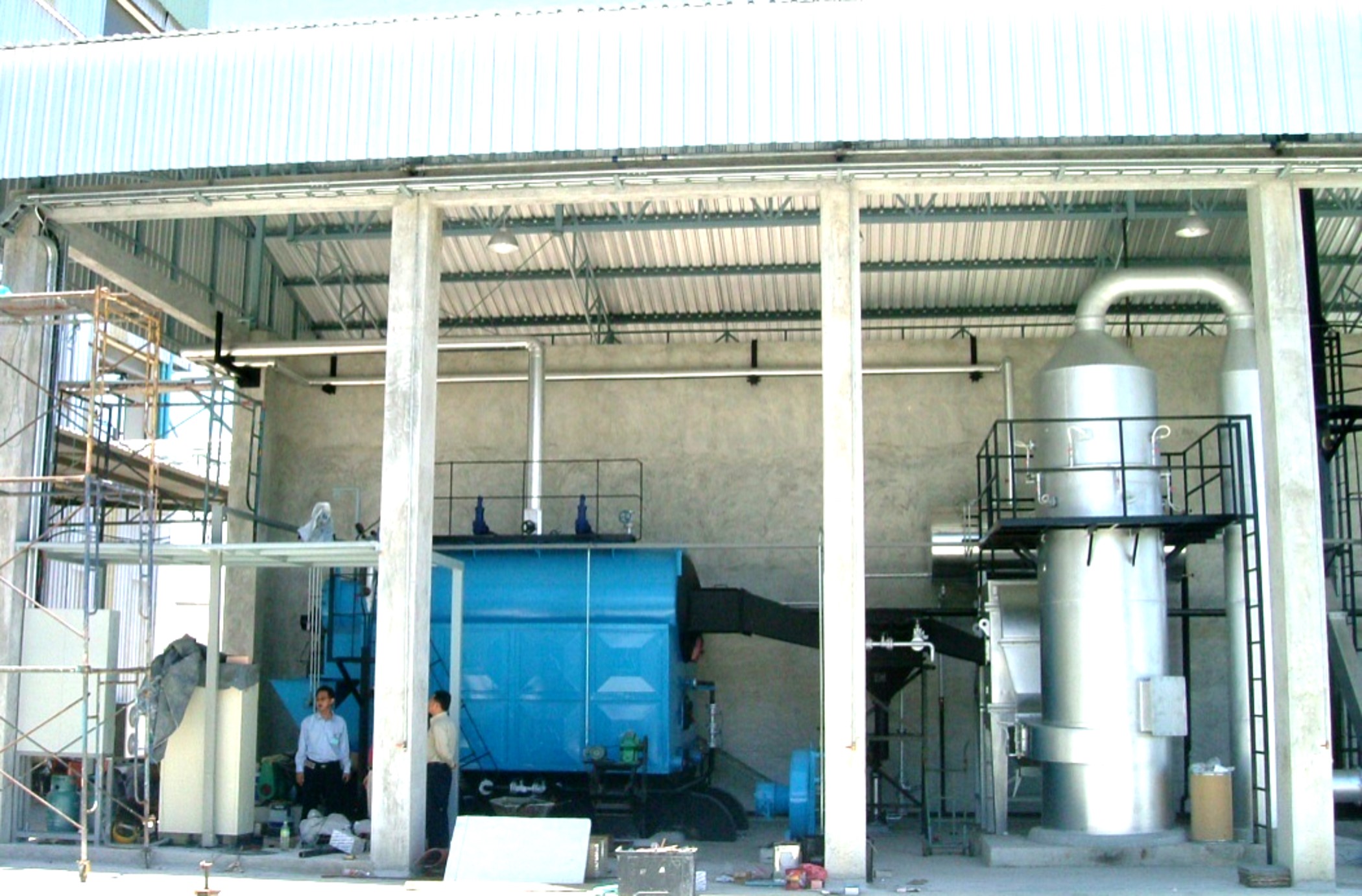
What are the main factors influencing the capacity requirements of a coal-fired boiler?
Coal-fired boilers remain critical in heavy industries and thermal power generation due to their ability to deliver high-pressure, high-volume steam reliably. However, sizing a coal-fired boiler isn’t as simple as matching output to current demand. Instead, engineers must consider a comprehensive set of technical, operational, and environmental factors. These determine how much steam or thermal energy the boiler must generate, how efficiently it can do so, and how well it integrates into the broader energy system of the plant.
The main factors influencing the capacity requirements of a coal-fired boiler include the total steam or thermal load demand, type and calorific value of coal used, combustion efficiency, operating pressure and temperature, load variability, system losses, ash handling requirements, emission control technology, and future expansion plans. Accurate sizing must align boiler capacity with real-world demand while accounting for fuel characteristics, process dynamics, and regulatory constraints to ensure reliable and efficient performance.
Let’s examine each of these factors in technical depth.
🔹 1. Total Steam or Heat Load Demand
The most fundamental input to boiler capacity sizing is the required steam output.
Application | Typical Steam Load Requirements |
---|---|
Thermal power generation | 100–1,000 TPH |
Steel manufacturing | 50–300 TPH |
Chemical processing | 10–100 TPH |
Paper and pulp industry | 5–50 TPH |
Formula for required steam output:
Boiler Capacity (kg/h) = ∑ Process Steam Demands + Turbine Load + Heating Load
The output should cover peak loads and maintain stable pressure and temperature under fluctuating demands.
🔹 2. Coal Calorific Value (Heating Value)
Different types of coal deliver different energy per kilogram, affecting how much is needed to meet the thermal load.
Coal Type | Calorific Value (kcal/kg) | Capacity Impact |
---|---|---|
Bituminous (high-rank) | 6,000–7,200 | Higher efficiency, smaller fuel input |
Sub-bituminous | 5,000–6,000 | More volume needed for same output |
Lignite | 3,500–4,500 | Requires larger furnace and fuel feed |
Anthracite | 7,000–8,000 | High energy, harder to ignite |
Low-grade coal requires larger fuel-feeding systems, more air, and larger furnace volume to achieve the same output.
🔹 3. Combustion Efficiency
Coal combustion is complex and depends on:
Fuel-air ratio
Bed or furnace temperature
Residence time
Moisture and volatile matter in coal
Efficiency Type | Range (%) | Notes |
---|---|---|
Stoker boilers | 70–80% | Simple, lower efficiency |
Pulverized coal (PC) | 85–90% | High combustion efficiency |
Circulating fluidized bed (CFB) | 86–92% | Good for low-grade coal and mixed fuels |
Boiler capacity must account for actual net efficiency, not theoretical values.
🔹 4. Operating Pressure and Temperature
High-pressure applications (e.g., power plants) require more energy per kg of steam, thus influencing boiler design and size.
Operating Pressure | Steam Enthalpy (kcal/kg) | Capacity Adjustment |
---|---|---|
10 bar (low) | ~660 | Baseline |
25 bar (medium) | ~700–740 | +5–10% |
60+ bar (high) | ~780–820 | +10–15% |
Higher operating conditions = higher heat requirement per kg of steam.
🔹 5. Steam Load Variability and Peak Demand
Most processes have variable steam demand. The boiler must be sized for:
Peak demand (to avoid shortfall)
Turndown (to avoid cycling)
Load Type | Sizing Implication |
---|---|
Continuous Load | Match average + 10% |
Intermittent Load | Oversize or use buffer systems |
Seasonal Load | Consider modular or dual-fuel units |
Short cycling during low-load can reduce efficiency and lifespan.
🔹 6. System Losses and Safety Margins
Always include margins for:
Radiation/convection losses (1–3%)
Blowdown losses (2–5%)
Pipeline heat loss (up to 10%)
Recommended buffer: Add 10–15% over calculated demand to size the boiler adequately.
🔹 7. Ash Generation and Handling Requirements
Coal combustion produces 10–35% ash by weight, depending on fuel quality. High-ash coal requires:
Impact Area | Capacity Planning Relevance |
---|---|
Ash Handling Equipment | Must match firing rate |
Furnace Design | Larger grate or bed area |
Sootblower Frequency | More frequent cleaning needed |
If ash clogs heat exchange surfaces, heat transfer efficiency drops, requiring higher nominal capacity.
🔹 8. Flue Gas and Emission Control Systems
Scrubbers, ESPs (Electrostatic Precipitators), or bag filters may affect:
Flue backpressure
Heat recovery
Overall fuel-to-output ratio
Control Device | Capacity Impact |
---|---|
SCR (NOx reduction) | Requires flue gas temperature control |
FGD (SO₂ control) | May increase energy input due to parasitic load |
ESP/Baghouses | Add resistance, impact stack draft |
Sizing must consider parasitic energy loads and draft losses.
🔹 9. Fuel Feeding and Storage Capacity
Boiler output is tied to the rate at which coal can be fed and burned.
Fuel System Element | Sizing Consideration |
---|---|
Conveyor/feeders | Must match TPH and coal type |
Bunker/silo capacity | Should cover 8–24 hours of operation |
Pulverizer/grinder | Needed for PC and CFB systems |
Underfeeding limits output; overfeeding risks unburned fuel and emissions.
🔹 10. Anticipated Future Expansion
Most industrial operations scale over time. Consider:
Expansion Type | Sizing Strategy |
---|---|
0–10% growth (3–5 years) | Add 15–20% buffer |
20%+ growth expected | Install modular units or N+1 boilers |
Utility integration | Allow space for CHP or turbine tie-ins |
Avoiding future capacity shortfalls prevents costly retrofitting or downtime.
🔹 Real-World Example: Cement Plant
Steam Requirement: 20 TPH
Coal Type: Sub-bituminous (5,200 kcal/kg)
Efficiency: 87% (CFB boiler)
System Losses: 10%
Expansion Plan: +30% in 5 years
Calculation:
Adjusted Output =
20 TPH × 1.10 (losses) = 22 TPH
Expansion Margin =
22 TPH × 1.30 = 28.6 TPH
Final Size Selected: 30 TPH CFB boiler with scalable header and ash handling system
Summary: Main Factors Affecting Coal-Fired Boiler Capacity
Factor | Capacity Influence |
---|---|
Steam or Heat Load | Sets base requirement for boiler sizing |
Coal Type & Calorific Value | Determines energy per kg, affects fuel volume needed |
Combustion Efficiency | Influences fuel-to-output conversion ratio |
Operating Pressure/Temperature | Affects enthalpy and total energy demand |
Load Variability | Drives turndown needs or buffer sizing |
System Losses | Adds 10–15% over calculated demand |
Ash Content & Handling | Influences furnace size and heat exchanger cleaning |
Emission Controls | Adds parasitic loads, affects draft and output |
Fuel Feeding Capacity | Determines max sustainable combustion rate |
Future Expansion | Requires margin or modular design |
Selecting the correct capacity for a coal-fired boiler means going beyond raw demand and designing for fuel behavior, emissions systems, process dynamics, and growth. This approach ensures reliable, efficient, and regulation-compliant performance over the entire lifecycle of the boiler system.
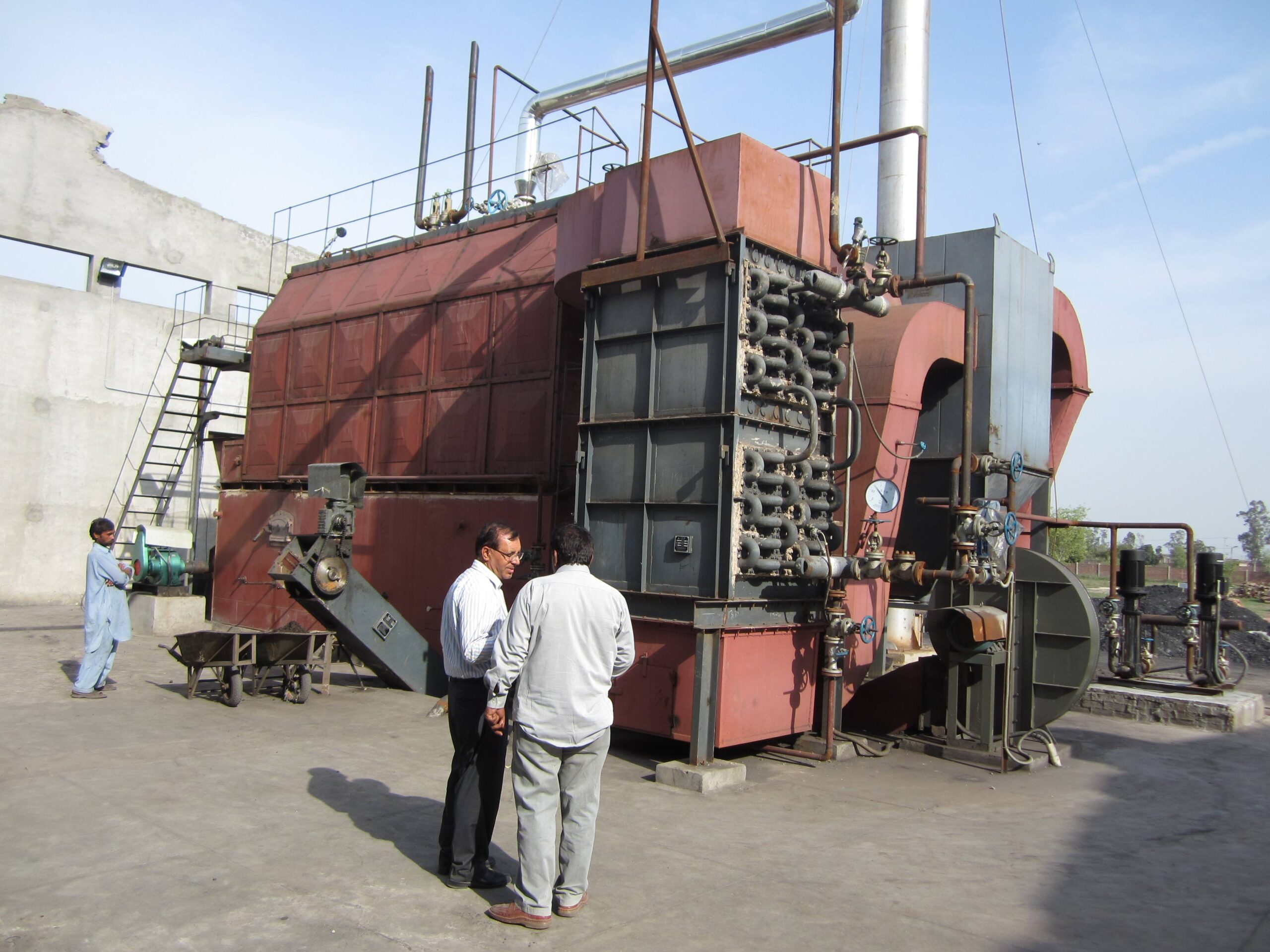
How do you calculate the required size based on steam or thermal load?
Correctly sizing an industrial boiler is critical for meeting the thermal or steam energy needs of a process or facility without underperformance or fuel waste. An undersized boiler can lead to process disruptions, pressure instability, and system stress, while an oversized boiler results in short cycling, poor efficiency, and higher capital costs. Sizing should always be based on calculated load demand, taking into account energy conversion efficiency, system losses, safety margins, and potential expansion.
To calculate the required size of a boiler based on steam or thermal load, determine the total heat energy or steam flow required by the process, adjust for the specific enthalpy of steam or hot water, divide by the boiler’s thermal efficiency, and add system losses. For steam boilers, this is typically done in kg/h or tons per hour (TPH), and for hot water systems, in kilowatts (kW) or BTU/hr. Accurate sizing ensures consistent operation and cost-effective performance across all load conditions.
Here’s how to accurately calculate boiler size for steam or hot water (thermal) systems.
🔹 A. Sizing a Boiler for Steam Load
Step 1: Determine Process Steam Demand
Sum all steam-using processes or equipment.
Example:
Heat exchanger: 1,800 kg/h
Cleaning in place (CIP): 700 kg/h
Jacketed vessels: 2,000 kg/h
Total Steam Demand = 4,500 kg/h
Step 2: Account for Enthalpy and Energy Load
Use the specific enthalpy of steam based on operating pressure.
Steam Pressure (bar) | Enthalpy (kcal/kg) | Notes |
---|---|---|
8 bar | ~660 kcal/kg | Saturated steam |
12 bar | ~670–700 kcal/kg | Slightly higher demand |
20+ bar | ~750+ kcal/kg | Requires more energy |
Thermal Energy Load (kcal/h):
Steam Load × Enthalpy = 4,500 × 670 = 3,015,000 kcal/h
Step 3: Adjust for Boiler Efficiency
Typical boiler efficiency: 85–95%
Assume: 90% efficiency (0.90)
Required Input Energy:
3,015,000 ÷ 0.90 = 3,350,000 kcal/h
Step 4: Add System Losses and Margin
Losses include:
Blowdown: 2–5%
Pipe heat loss: 5–10%
Contingency: 5–10%
Loss Margin: 10–15%
3,350,000 × 1.10 = 3,685,000 kcal/h
✅ Final Boiler Size (kg/h):
3,685,000 ÷ 670 = ~5,498 kg/h → Rounded to **5.5 TPH**
Select a 6 TPH boiler or a modular system (e.g., 2 × 3 TPH) for flexibility.
🔹 B. Sizing a Boiler for Hot Water / Thermal Load
Step 1: Determine Flow Rate and Temperature Rise
Parameter | Unit |
---|---|
Flow Rate | L/s or kg/s |
Temperature Rise (ΔT) | °C |
Specific Heat (Cp) | 4.18 kJ/kg°C |
Formula:
Q (kW) = m × Cp × ΔT
Example:
Flow: 15,000 L/hr = 4.17 kg/s
ΔT: 70°C (from 30°C to 100°C)
Q = 4.17 × 4.18 × 70 ≈ 1,223.3 kW
Step 2: Adjust for Boiler Efficiency
Assume: 91% efficiency (0.91)
1,223.3 ÷ 0.91 = 1,344.3 kW
Step 3: Add Safety and System Margin (10%)
1,344.3 × 1.10 = ~1,478.7 kW → Rounded to **1,500 kW**
Choose a 1.5 MW thermal boiler, or split into 2 × 750 kW for flexibility.
🔹 Quick Reference Boiler Sizing Summary
Parameter | Steam Boiler | Hot Water Boiler |
---|---|---|
Load Measurement | kg/h or TPH | kW or BTU/hr |
Energy per Unit | Based on steam enthalpy (kcal/kg) | Based on ΔT and flow |
Formula |
Load × Enthalpy ÷ Efficiency × Loss Factor
|
Flow × 4.18 × ΔT ÷ Efficiency × Loss Factor
| Efficiency Range (%) | 85–95% | 88–98% (condensing) | | Margin for Losses | 10–15% | 10–15% |
🔹 Real-World Example: Paper Mill
Steam Demand: 8,000 kg/h
Operating Pressure: 10 bar (Enthalpy ≈ 660 kcal/kg)
Efficiency: 88%
Loss Margin: 12%
Step-by-Step:
Thermal Load = 8,000 × 660 = 5,280,000 kcal/h
Input Energy = 5,280,000 ÷ 0.88 = 6,000,000 kcal/h
With Losses = 6,000,000 × 1.12 = 6,720,000 kcal/h
Final Boiler Output Needed:
6,720,000 ÷ 660 = 10,181 kg/h → Rounded to 10.5 TPH
✔️ Select a 12 TPH boiler, or 2 × 6 TPH units for redundancy and modulating control.
Summary: Steps to Calculate Required Boiler Size
Step | Description |
---|---|
1. Determine Load | Calculate total steam or hot water demand |
2. Factor Enthalpy or ΔT | Use thermodynamics to convert flow to energy |
3. Adjust for Efficiency | Divide by expected boiler efficiency |
4. Add System Losses | Include heat losses and process margins |
5. Round and Configure | Choose closest higher standard capacity |
Sizing your boiler based on accurate thermal demand ensures reliable performance, fuel efficiency, and system longevity—preventing overdesign or capacity shortfalls and enabling smooth, long-term operation.
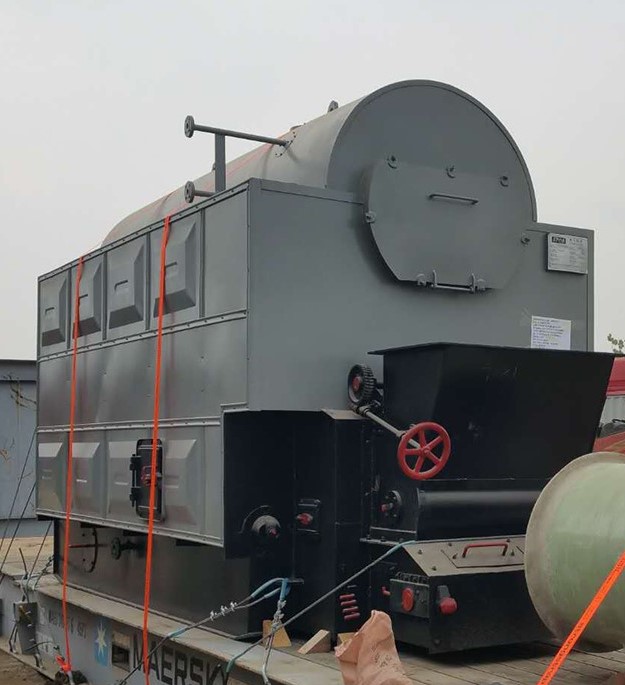
What’s the difference between nominal capacity and actual load utilization?
When evaluating or selecting an industrial boiler, it’s essential to understand the distinction between nominal capacity and actual load utilization. These two concepts reflect very different aspects of a boiler’s performance: one describes its designed potential, while the other describes how it is actually used in daily operations. Ignoring this difference can lead to issues such as inefficiency, excessive cycling, energy waste, or system underperformance.
Nominal capacity refers to the maximum continuous output a boiler is designed to deliver under standard operating conditions, usually expressed in units like kg/h, tons per hour (TPH), or kilowatts (kW). Actual load utilization measures how much of that capacity is actually used during operation, often varying throughout the day or process cycle. While nominal capacity is a fixed manufacturer specification, actual load utilization fluctuates based on real-time process demands, system control strategies, and environmental conditions.
Let’s break down the difference in more detail.
🔹 What Is Nominal Capacity?
Definition:
Nominal capacity is the rated output that a boiler can reliably produce under standard design conditions (pressure, temperature, fuel type, and efficiency) as specified by the manufacturer.
Parameter | Description |
---|---|
Units | kg/h, TPH (steam); kW, MW (thermal) |
Basis | Laboratory-tested, optimal settings |
Set By | Boiler design and certification |
Purpose | Procurement, specification, regulatory compliance |
Example:
A boiler with a nominal capacity of 10 TPH means it is designed to continuously generate 10,000 kg of steam per hour at rated pressure and temperature.
🔹 What Is Actual Load Utilization?
Definition:
Actual load utilization is the real operating output compared to the nominal maximum, expressed either as a percentage or a load profile over time.
Parameter | Description |
---|---|
Units | kg/h, kW, or % of nominal capacity |
Basis | Real-time process requirements |
Varies By | Time of day, production schedule, weather, process cycles |
Purpose | Efficiency tracking, operational optimization |
Example:
If a 10 TPH boiler operates at an average of 6 TPH over a 24-hour period, its actual utilization is 60%.
🔹 Key Differences at a Glance
Feature | Nominal Capacity | Actual Load Utilization |
---|---|---|
Definition | Rated maximum output under standard conditions | Real output based on current demand |
Fixed or Variable | Fixed (design-based) | Variable (demand-based) |
Usage | For sizing and selection | For operational analysis and optimization |
Impact on Efficiency | Sets theoretical maximum | Determines real-world performance |
Relation to Cost | Affects capital investment | Affects operational cost and fuel use |
🔹 Why the Difference Matters
✔️ Over-Sized Boilers (Nominal Capacity >> Actual Load)
Operate far below design load most of the time
Increased cycling and combustion inefficiency
Higher maintenance costs and shorter lifespan
✔️ Under-Sized Boilers (Nominal Capacity << Peak Load)
Struggle to meet peak demands
Frequent overloading and risk of trips
Reduced safety margin and production risk
🔹 Ideal Load Utilization Range for Best Efficiency
Load Range (% of Nominal) | Boiler Efficiency and Performance |
---|---|
80–100% | Highest efficiency and stability |
50–80% | Good efficiency, slight modulation losses |
30–50% | Noticeable efficiency drop, cycling risk |
<30% | Poor efficiency, frequent cycling |
Modern boilers with high turndown ratios (e.g., 8:1 or 10:1) can better maintain efficiency even at low loads.
🔹 Real-World Example: Food Processing Plant
Nominal Capacity: 6 TPH
Average Load (Weekdays): 3.8 TPH (≈63%)
Average Load (Weekends): 2.0 TPH (≈33%)
Problem:
Weekend operation led to cycling and poor fuel efficiency.
Solution:
Upgraded burner system to a 10:1 turndown ratio.
Installed second small modular boiler (2 TPH) for weekend low load.
Result:
15% overall fuel savings
30% reduction in burner maintenance costs
🔹 Summary: Nominal Capacity vs Actual Load Utilization
Comparison Area | Nominal Capacity | Actual Load Utilization |
---|---|---|
Definition | Rated maximum boiler output | Real-world operating output |
Measurement Basis | Laboratory or certification standard | Field-measured operating data |
Flexibility | Fixed | Variable |
Effect on Operations | Sets system limits | Drives efficiency and control needs |
Importance in Design | Ensure sufficient peak capability | Optimize for cost and fuel savings |
Understanding the distinction between nominal capacity and actual load utilization allows engineers and facility managers to select boilers appropriately, design control systems intelligently, and optimize operational strategies—ultimately resulting in a high-efficiency, low-cost, reliable thermal system.
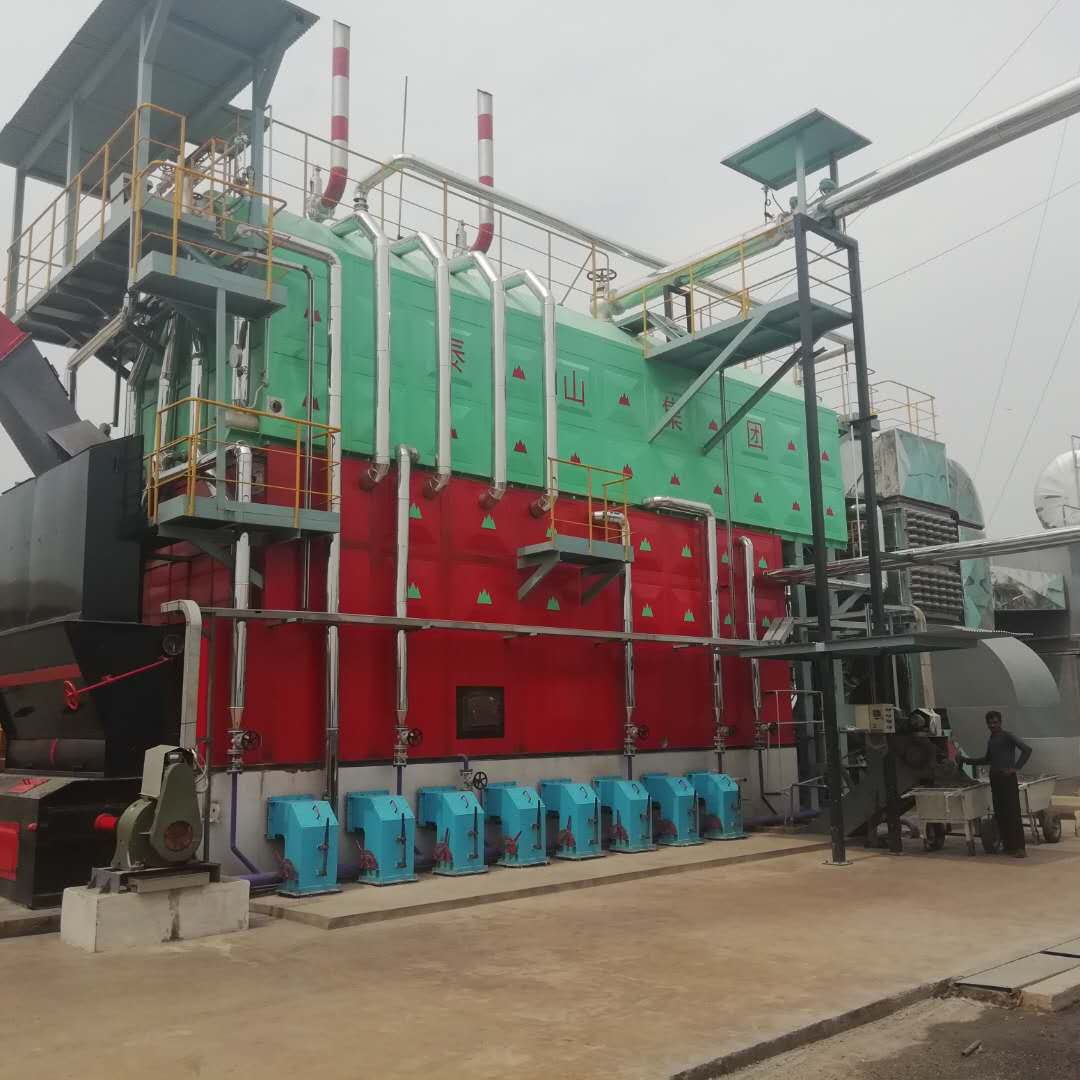
How does fuel quality (calorific value, ash content) affect sizing and efficiency?
In coal-fired and biomass boiler systems, fuel quality is one of the most critical factors influencing both boiler sizing and operational efficiency. Variations in calorific value (the amount of heat produced per unit of fuel) and ash content (non-combustible residue) affect everything from combustion dynamics and fuel feeding rates to furnace volume and heat exchanger sizing. If these factors are not properly accounted for, the system may suffer from poor performance, high maintenance costs, reduced output, and excess emissions.
Fuel quality directly affects boiler sizing and efficiency because the calorific value determines how much fuel is needed to meet a given thermal load, while ash content impacts combustion efficiency, heat transfer, and the design of ash handling and cleaning systems. Low-calorific fuels require higher fuel feed rates and larger combustion chambers, while high-ash fuels lead to increased slagging, fouling, and maintenance. Therefore, accurate fuel analysis is essential for right-sizing boilers and achieving optimal operational performance.
Let’s examine each component of fuel quality and its direct impact on boiler performance and design.
🔹 1. Calorific Value (CV) and Its Impact on Boiler Sizing
Definition:
The calorific value (also called heating value) measures the energy content in a unit of fuel—typically in kcal/kg or MJ/kg.
Fuel Type | Typical CV (kcal/kg) |
---|---|
Anthracite Coal | 7,000–8,000 |
Bituminous Coal | 6,000–7,200 |
Sub-bituminous Coal | 5,000–6,000 |
Lignite | 3,500–4,500 |
Biomass (Wood Chips) | 2,000–4,500 |
🔸 How CV Affects Sizing:
Lower CV = More fuel volume needed → Larger boiler size
Example:
Steam demand: 10 TPH
Boiler efficiency: 88%
Enthalpy of steam at 10 bar: ~660 kcal/kg
Total energy required = 10,000 × 660 = 6.6 million kcal/h
Required input = 6.6 million ÷ 0.88 = 7.5 million kcal/h
Now, calculate fuel consumption:
Coal Type | CV (kcal/kg) | Fuel Required (kg/h) |
---|---|---|
Bituminous | 6,500 | 7.5 million ÷ 6,500 ≈ 1,154 kg/h |
Lignite | 4,000 | 7.5 million ÷ 4,000 ≈ 1,875 kg/h |
Result:
Lignite needs ~62% more volume than bituminous for the same steam output, which:
Increases fuel feeding system capacity
Requires larger furnace and hopper size
Generates more flue gas volume to handle
🔹 2. Ash Content and Its Impact on Efficiency & Maintenance
Definition:
Ash content refers to the non-combustible mineral residue left after fuel combustion. It varies by fuel source and preparation.
Fuel Type | Typical Ash Content (%) |
---|---|
Bituminous Coal | 5–15% |
Sub-bituminous Coal | 8–25% |
Lignite | 15–30% |
Biomass | 1–7% |
🔸 How Ash Content Affects Efficiency and Design:
Ash Content Impact Area | Consequence for Boiler System |
---|---|
Combustion Efficiency | Ash dilutes fuel, reducing net energy input per kg |
Heat Transfer Surfaces | Fouling reduces convective/radiant heat transfer |
Sootblower/cleaning needs | Increased frequency and automated systems required |
Ash Handling System Size | Larger ash conveyors, silos, and removal infrastructure |
Slagging/Clinker Formation | Increases risk of furnace blockages |
Efficiency loss estimate:
1–2% efficiency drop for every 10% ash increase (if untreated)
🔹 3. Boiler Design Adjustments for Low CV and High Ash Fuels
Design Element | Adjustment Required |
---|---|
Combustion Chamber | Larger volume to maintain temperature |
Fuel Feeders and Conveyors | Higher capacity for more fuel input |
Primary/Secondary Air | Increased airflow to ensure complete combustion |
Heat Exchanger Surfaces | Over-sized to compensate for fouling |
Ash Removal Systems | Larger, more frequent cycles |
Chimney/Ducting | Higher flue gas volume = larger diameter |
🔹 4. Real-World Comparison
Parameter | Bituminous Boiler | Lignite Boiler |
---|---|---|
Fuel CV (kcal/kg) | 6,500 | 4,000 |
Ash Content (%) | 10% | 22% |
Fuel Input (kg/h) | ~1,154 | ~1,875 |
Boiler Efficiency (%) | 88% | 84% (due to slagging) |
Ash Handling Volume | 115 kg/h | 412.5 kg/h |
Maintenance Frequency | Monthly cleaning | Weekly cleaning |
🔹 5. How to Manage Fuel Quality Variability
Strategy | Benefit |
---|---|
Pre-sorting or blending fuel | Improves average CV, reduces ash concentration |
Use of fluidized bed technology | Handles mixed or low-CV fuels efficiently |
Automated ash removal | Minimizes fouling impact on efficiency |
Combustion control systems | Adjust airflow/fuel feed based on real-time input |
Regular fuel testing | Enables proactive operational adjustments |
Summary: Fuel Quality Impact on Sizing and Efficiency
Factor | Low Calorific Value Impact | High Ash Content Impact |
---|---|---|
Boiler Size | Must increase to handle higher fuel volume | Larger furnace and ash removal required |
Fuel Feed Rate | Increased throughput needed | May need denser feed design |
Efficiency | Lower unless combustion is optimized | Reduced due to slagging/fouling |
Maintenance Needs | More ash = more cleaning | Reduced uptime if unmanaged |
Capital Investment | Higher due to oversized components | Higher O&M costs due to wear |
Understanding the impact of fuel calorific value and ash content on your boiler system ensures you select and size the right equipment, maintain consistent efficiency, and optimize long-term costs—regardless of whether you’re using premium fuels or low-grade alternatives.
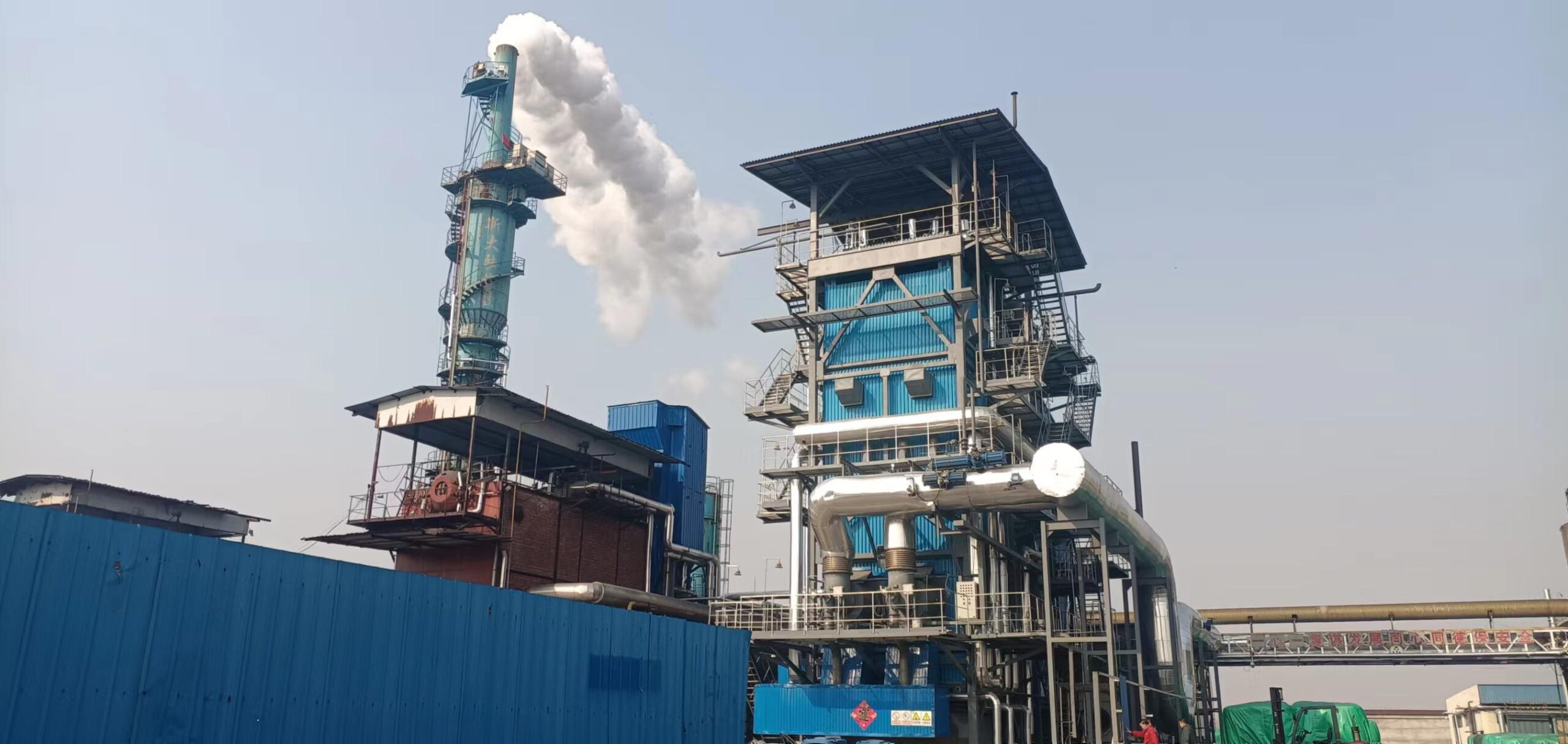
Why should you consider plant layout, space, and future scalability in sizing decisions?
Boiler sizing is not just a question of matching output to steam or thermal demand. It’s a decision that also has major spatial, logistical, and strategic implications. In many cases, a boiler system will be part of a larger industrial ecosystem—interacting with infrastructure such as piping, control rooms, chimneys, electrical panels, fuel storage, and maintenance access routes. Additionally, as facilities grow, thermal demand can increase significantly. Failing to account for layout and scalability early in the design process can lead to costly modifications, space limitations, safety issues, and lost production capacity later.
Considering plant layout, space, and future scalability in boiler sizing decisions ensures that the system fits physically within the facility, allows safe and efficient installation and maintenance, supports process flow and fuel logistics, and enables capacity expansion without costly retrofitting. Proper planning avoids bottlenecks, downtime, and underutilized equipment, while supporting future growth, regulatory compliance, and cost-effective plant operations.
Let’s explore in depth why these non-thermal factors are critical in boiler selection and long-term success.
🔹 1. Plant Layout and Boiler Footprint
Boilers—especially coal, biomass, or multi-fuel units—can be large and heavy, requiring substantial floor area and vertical clearance.
Layout Factor | Importance for Sizing Decisions |
---|---|
Available Floor Space | Determines maximum feasible boiler footprint |
Ceiling Height | Limits economizer, stack, or water drum installation |
Structural Integrity | Must support heavy static/dynamic loads |
Adjacent Systems | Piping, tanks, and electrical panels need clearance |
Oversized boilers may not fit into existing boiler rooms, requiring costly structural upgrades or relocation.
🔹 2. Access for Installation and Maintenance
A boiler must be accessible for:
Burner service and replacement
Manway inspections
Tube cleaning or retubing
Sootblowing equipment access
Emergency shutdown operations
Required Clearance (Typical) | Zone |
---|---|
1.5–2.0 m | Front (burner area) |
1.0–1.5 m | Rear (manhole or water wall) |
0.8–1.2 m | Sides (instrumentation/valves) |
1.5 m+ | Above (for lifting and rigging) |
Inadequate clearance leads to:
Longer downtime
Unsafe service procedures
Voided manufacturer warranties
🔹 3. Piping, Fuel Supply, and Ventilation Layout
Sizing the boiler must also ensure compatibility with:
Steam header routing
Condensate and feedwater lines
Fuel delivery (gas, oil, coal, biomass)
Flue gas paths and chimney location
Combustion air intake and exhaust ventilation
Poor spatial integration of these systems can cause:
Pressure loss in long piping runs
Combustion instability from poor air supply
Fire risk from fuel pipe interference
Code violations for emissions and exhaust routing
🔹 4. Space Allocation for Auxiliary Systems
Many boiler systems require additional components such as:
Auxiliary Equipment | Space Requirement Consideration |
---|---|
Deaerator tank | Elevated mounting or adjacent platform |
Blowdown tank | Must be close to boiler drain zone |
Water treatment skid | Needs access to feedwater inlet lines |
Economizer and air preheater | May extend beyond boiler footprint vertically |
Fuel storage and handling | Hopper, conveyor, silos, or oil tanks |
Sufficient space ensures safe operation, compliance, and maintenance efficiency.
🔹 5. Planning for Future Scalability
One of the most overlooked aspects of boiler sizing is growth readiness. Thermal demand often increases due to:
Production expansion
New process lines
Facility or building extensions
Process changes requiring higher temperature or pressure
Retrofitting capacity later is expensive, disruptive, and may be impossible if space wasn’t reserved.
Scalability Feature | Design Planning Strategy |
---|---|
Room for second boiler | Leave 25–50% space margin in boiler room |
Oversized steam headers | Stub future connection points |
Electrical and I/O ports | Use modular control systems |
Fuel infrastructure | Size tank or line for future load |
Chimney or ductwork | Plan for higher flue volume or parallel unit |
🔹 6. Safety and Regulatory Compliance
Spatial considerations also tie directly into safety.
Safety Element | Space/Layout Implication |
---|---|
Emergency egress | Require unobstructed walkways |
Fire zoning | Flammable fuel tanks require separation zones |
Ventilation and gas purge | Affects combustion safety |
Inspection access | Mandated by codes (e.g., ASME, NFPA, ISO) |
Failing to meet these spatial codes can delay commissioning, raise insurance costs, or void regulatory approval.
🔹 Real-World Case: Automotive Plant Expansion
Initial Setup:
Installed 1 × 10 TPH coal-fired boiler
Boiler room dimension: 12 × 6 m
Full load operations at 70% capacity
Expansion Plan (3 years):
Add 2 more production lines
Estimated steam increase: 6 TPH
Space Constraint:
No space left for second unit
Required wall demolition and new boiler house construction
Retrofit cost: $280,000 vs. $80,000 if space had been reserved
Summary: Why Layout, Space & Scalability Must Guide Sizing
Factor | Risk if Ignored | Benefit if Considered |
---|---|---|
Plant Floor Space | Equipment won’t fit | Smooth installation and expansion |
Maintenance Access | Unsafe or delayed servicing | Lower O&M cost and higher uptime |
Piping/Fuel/Ventilation Paths | Improper function or code violation | Optimized system flow and air balance |
Auxiliary Equipment Room | External installations needed | Compact, efficient boiler system layout |
Future Scalability | Costly retrofits and capacity shortfall | Seamless modular growth |
Regulatory Clearance | Project delays, fines, redesign | Faster commissioning, code compliance |
Properly incorporating plant layout, available space, and future scalability into your sizing decisions ensures your boiler system is physically feasible, cost-effective, safe, and growth-ready—setting the foundation for a highly efficient and adaptable thermal infrastructure.
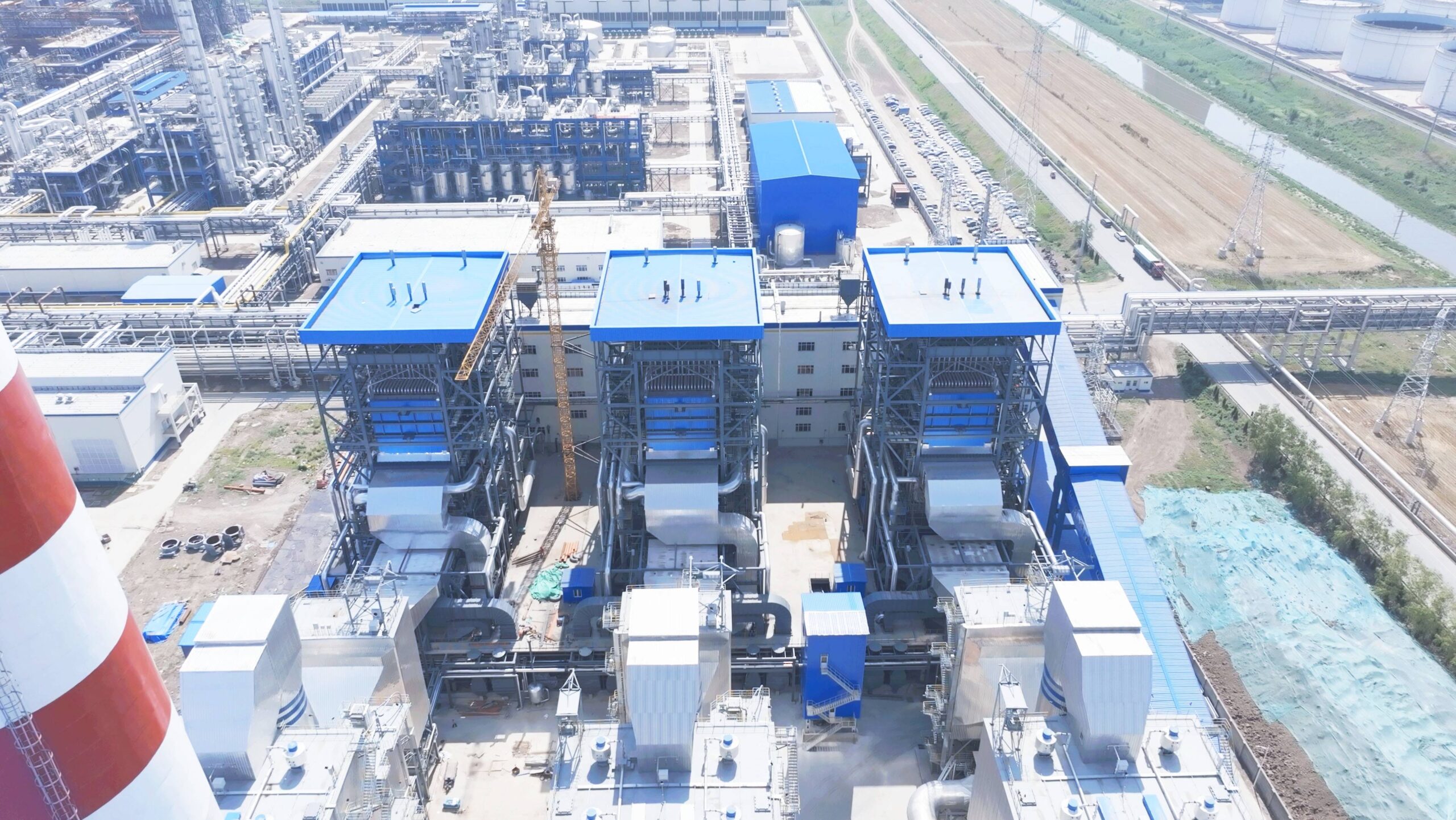
What are the consequences of over-sizing or under-sizing a coal-fired boiler?
Sizing a coal-fired boiler properly is one of the most critical decisions in plant design and energy infrastructure planning. A mismatch between the boiler’s rated capacity and the actual load demand can lead to significant operational, economic, and environmental drawbacks. Whether a system is over-sized or under-sized, the consequences are often long-term, affecting everything from fuel efficiency and emissions to equipment lifespan and system stability.
Over-sizing a coal-fired boiler leads to frequent cycling, poor fuel efficiency, increased emissions, higher initial costs, and underutilized equipment. Under-sizing results in an inability to meet peak steam demand, operational stress, unplanned shutdowns, and production loss. Both cases reduce reliability, compromise safety, and lead to increased total cost of ownership. Proper sizing ensures that the boiler operates within its optimal load range, delivering stable, efficient, and cost-effective steam generation.
Let’s break down the specific consequences of over-sizing and under-sizing in detail.
🔹 Consequences of Over-Sizing a Coal-Fired Boiler
An over-sized boiler is one whose rated capacity significantly exceeds the actual steam or heat demand of the process or facility.
🔸 1. Poor Part-Load Efficiency
Coal-fired boilers are most efficient near their rated load (80–100%).
At low loads, incomplete combustion, inefficient heat transfer, and cooler flue gases reduce efficiency.
Fuel consumption increases per unit of useful steam.
🔸 2. Frequent Cycling
The boiler starts and stops more often to match low demand.
This leads to:
Higher thermal stress on boiler tubes and refractory
More wear on fans, dampers, and feeders
Increased maintenance frequency
🔸 3. High Capital and Operating Costs
Larger boilers cost significantly more to purchase and install.
Infrastructure such as fuel storage, feed systems, and ash handling must be upsized unnecessarily.
Operating a lightly loaded large boiler wastes both fuel and manpower.
🔸 4. Increased Emissions
At partial load, combustion is incomplete, raising CO, NOₓ, and particulate emissions.
Environmental compliance becomes harder to maintain.
Flue gas temperatures may be too low for effective ESP or FGD operation.
🔸 5. System Inertia and Control Difficulty
Larger water/steam volumes cause slower response times.
Control systems struggle to stabilize pressure and temperature at low loads.
Sudden demand changes cannot be tracked smoothly.
🔹 Consequences of Under-Sizing a Coal-Fired Boiler
An under-sized boiler cannot meet the full thermal or steam requirements of the process, especially during peak demand periods.
🔸 1. Inability to Meet Peak Load
During high-demand events, steam pressure drops.
Processes may slow, shut down, or operate unsafely.
Safety systems may trip due to low steam pressure or temperature.
🔸 2. Overloading and Accelerated Wear
Operating above rated capacity:
Overstresses combustion chamber and tubes
Reduces life of refractory and metal surfaces
Increases slagging and fouling
🔸 3. Reduced Reliability
Boiler runs continuously at or beyond limit.
No room for backup or load sharing.
Any fault or degradation leads to immediate production impact.
🔸 4. No Redundancy or Flexibility
The plant cannot adapt to unexpected demand surges.
Seasonal variations or expansion plans become unmanageable.
Maintenance requires shutdown of production if no spare capacity exists.
🔸 5. Higher Per-Unit Fuel Cost
Boilers running over capacity often burn fuel less efficiently.
They may exceed air-fuel ratio limits, causing excess unburned carbon or CO.
🔹 Comparative Table: Over-Sizing vs Under-Sizing
Parameter | Over-Sized Boiler | Under-Sized Boiler |
---|---|---|
Fuel Efficiency | Low at part-load | Drops at over-capacity |
Operational Stress | Increased cycling | Continuous high load = component stress |
Capital Cost | Higher than necessary | Lower upfront but hidden long-term costs |
Maintenance | More frequent due to short cycling | More frequent due to high wear |
Emissions | Elevated at low load | Elevated due to poor combustion control |
System Responsiveness | Slow and sluggish at low demand | Can’t track load changes above design |
Capacity for Growth | Allows for future expansion | Blocks expansion unless reengineered |
Overall Cost of Ownership | High due to inefficiency and O&M | High due to reliability and upgrade costs |
🔹 Real-World Case: Textile Dyeing Plant
Case 1 – Over-Sized Boiler:
Installed: 10 TPH
Actual load: 4.5–6.0 TPH (45–60%)
Results:
18% fuel waste due to low-load operation
Burner maintenance required every 2 months
ROI delayed by 2 years
Case 2 – Under-Sized Boiler:
Installed: 5 TPH
Actual peak load: 6.2 TPH
Results:
Pressure drop during dye cycle led to batch failures
Emergency rental boiler brought in during seasonal demand
Lost production value: $180,000/year
🔹 Best Practice: Right-Sizing Strategy
Step | Description |
---|---|
Load Profiling | Assess average and peak steam demand |
Add Efficiency and Loss Margins | Account for radiation, blowdown, and piping losses |
Use Turndown-Capable Burners | Allows operation across a wider load range |
Design for Modularity | Use multiple smaller boilers to match load fluctuations |
Plan for Expansion | Include 10–25% future demand growth margin |
Summary: Key Consequences of Improper Sizing
Sizing Error | Operational Impact | Financial/Environmental Impact |
---|---|---|
Over-Sizing | Cycling, inefficiency, difficult control | Wasted fuel, higher emissions, delayed ROI |
Under-Sizing | Inadequate capacity, overloading, shutdown risk | Downtime, maintenance spikes, process instability |
Choosing the right size coal-fired boiler—based on careful demand analysis, fuel quality, efficiency modeling, and operational flexibility—is the foundation for a safe, reliable, and cost-effective steam generation system. Avoiding both over-sizing and under-sizing leads to maximum performance, minimum waste, and optimal lifecycle cost.
🔍 Conclusion
Choosing the correct capacity and size for your industrial coal-fired boiler is crucial for maximizing fuel efficiency, ensuring production continuity, and minimizing lifecycle costs. A boiler that is properly matched to your actual demand—considering fuel type, operational cycles, and growth plans—will deliver consistent performance, reduced emissions, and optimal return on investment. Avoid guesswork; base your decision on real-world data and expert analysis.
📞 Contact Us
💡 Need assistance in sizing your coal-fired boiler? Our expert engineers can help you evaluate your load profile, fuel characteristics, and site conditions to design the most suitable system.
🔹 Contact us today for a tailored boiler sizing consultation built around your operation’s needs! ⚙️🔥🛠️
FAQ
How is the capacity of an industrial coal-fired boiler determined?
The capacity is based on the required steam output or thermal load of your industrial process. It’s typically measured in tons per hour (TPH) for steam or million BTU/hr for thermal energy and must align with peak process demand.
What is the typical capacity range for industrial coal-fired boilers?
Industrial coal-fired boilers commonly range from 1 TPH to over 100 TPH in steam production, with hot water systems ranging from several million to over 100 million BTU/hr, depending on application scale.
What factors influence the size of a coal-fired boiler?
Critical factors include steam pressure and temperature requirements, heating surface area, fuel type and quality, boiler efficiency, operating hours, and plant redundancy needs.
Why is accurate sizing of a coal-fired boiler important?
Oversized boilers result in higher capital and operating costs, while undersized systems can’t meet steam demands. Proper sizing ensures energy efficiency, safety, and cost-effective operation.
Can coal-fired boilers be customized for unique industrial needs?
Yes, manufacturers offer tailored solutions based on specific load requirements, coal grades, pressure levels, space constraints, and emission regulations. Custom engineering ensures the best performance and compliance.
References
Coal Boiler Sizing and Design Guide – https://www.energy.gov
Steam Demand in Coal-Fired Systems – https://www.sciencedirect.com
Industrial Boiler Capacity Selection – https://www.researchgate.net
Coal Boiler Performance and Load Calculation – https://www.bioenergyconsult.com
Boiler Efficiency and Output Matching – https://www.epa.gov
Thermal Output Sizing for Industry – https://www.energysavingtrust.org.uk
Coal Combustion and Sizing Metrics – https://www.mdpi.com
Right-Sizing Industrial Coal Boilers – https://www.iea.org
Boiler Customization for Industry – https://www.automation.com
Boiler Design Best Practices – https://www.sciencedirect.com
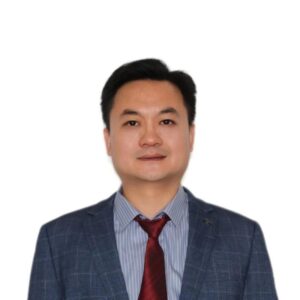