Selecting the right industrial oil-fired boiler involves more than just sizing and cost—fuel type and combustion properties play a critical role in determining overall system performance, efficiency, and emissions. Many buyers overlook the importance of fuel characteristics, which can result in inefficient combustion, increased maintenance needs, or even premature boiler failure. To ensure your boiler meets both operational and regulatory requirements, it’s vital to match the boiler design with the correct fuel type and combustion strategy.
Fuel types and combustion characteristics directly affect your choice of industrial oil-fired boiler by influencing burner design, combustion chamber sizing, thermal efficiency, emissions output, and maintenance requirements. Different oils—such as light diesel, heavy fuel oil, or bio-oil—vary in viscosity, calorific value, sulfur content, and ignition temperature. These variables determine the type of burner required, atomization method, preheating needs, and flue gas treatment systems. Selecting the wrong boiler-fuel match can compromise efficiency, increase emissions, and escalate operational costs.
To make a smart decision, it’s essential to understand how fuel properties interact with boiler design and combustion systems. Here’s what you need to know.
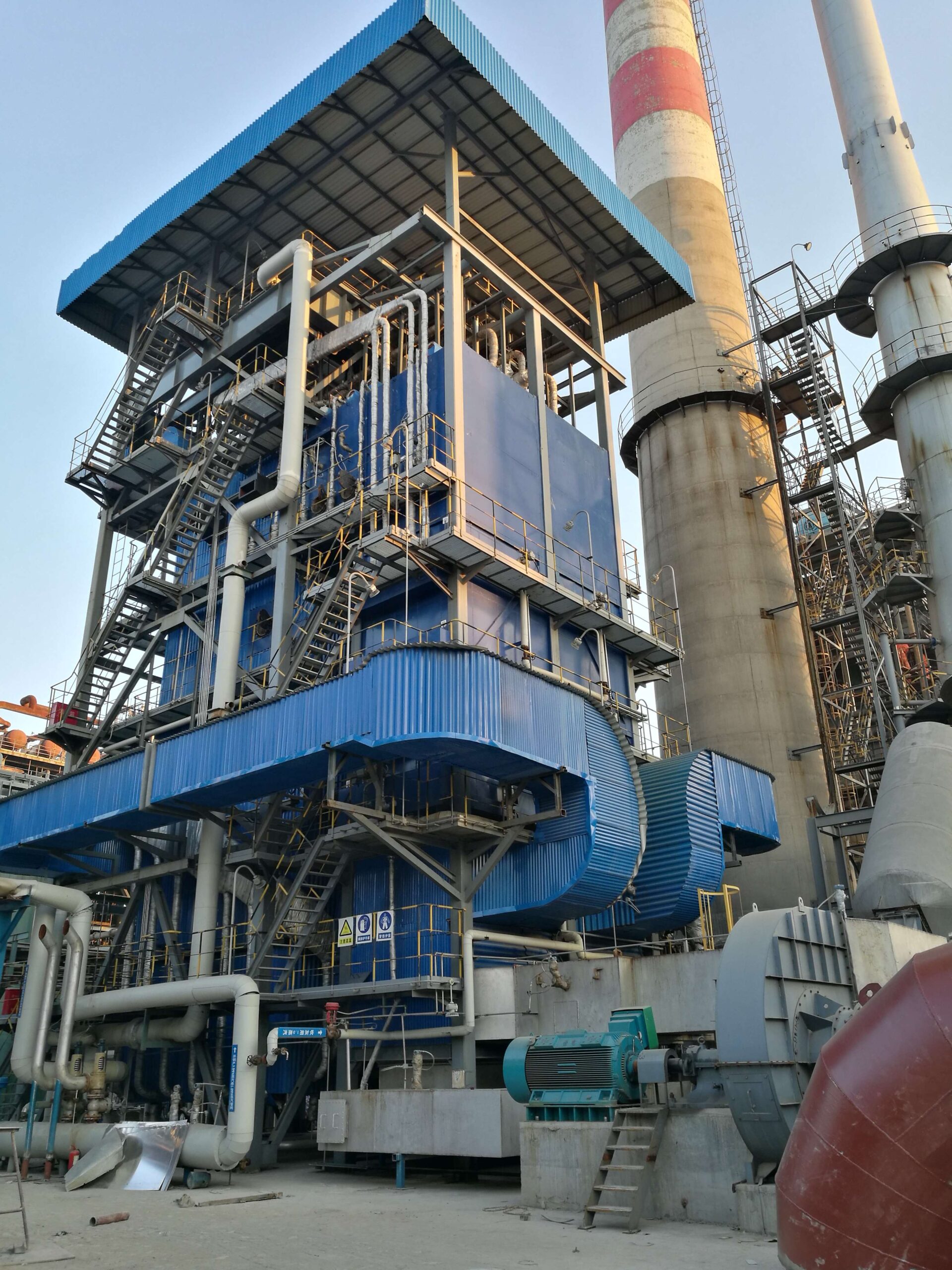
What are the most common fuel types used in industrial oil-fired boilers?
Fuel selection plays a central role in the design, performance, and efficiency of industrial oil-fired boilers. The choice of fuel affects not only the boiler’s thermal capacity and combustion characteristics but also startup behavior, emissions profile, maintenance frequency, and cost-effectiveness. Industrial facilities must consider availability, viscosity, energy content, and regulatory compliance when choosing the optimal oil type for their boiler systems.
The most common fuel types used in industrial oil-fired boilers include diesel (No. 2 fuel oil), heavy fuel oil (No. 5 and No. 6), light fuel oil, kerosene, marine fuel oil, and bio-based oils such as biodiesel and pyrolysis oil. Each fuel type differs in viscosity, sulfur content, calorific value, and handling requirements. Diesel and light fuel oils are easier to ignite and cleaner-burning, while heavy fuel oils are cheaper but require preheating. Biodiesel offers renewable advantages but has storage and temperature limitations.
Below is a comprehensive guide to each major fuel type commonly used in oil-fired boiler systems.
🔹 1. Diesel (No. 2 Fuel Oil)
Also known as light fuel oil, diesel is one of the most widely used fuels in mid-sized industrial boilers.
Parameter | Value |
---|---|
Calorific Value | ~10,000–10,200 kcal/kg |
Sulfur Content | Low (<0.5%) |
Flash Point | 52–65°C |
Viscosity (40°C) | 2–4 cSt |
Advantages:
Easy to handle and ignite
Minimal preheating required
Low ash and soot
Widely available globally
Best For:
Hospitals, manufacturing plants, and remote industrial facilities with intermittent load.
🔹 2. Heavy Fuel Oil (HFO – No. 5 and No. 6 Oil)
Heavy fuel oils are residual products from crude oil distillation and are the most economical per unit of energy but challenging to use.
Parameter | Value |
---|---|
Calorific Value | ~9,600–9,800 kcal/kg |
Sulfur Content | Medium to high (0.5–3.5%) |
Flash Point | ~60°C |
Viscosity (50°C) | 100–500 cSt (requires preheating) |
Advantages:
Lowest cost per energy unit
High energy density
Suitable for high-capacity boilers
Limitations:
Requires preheating (to ~100–130°C)
Produces more soot, ash, and sulfur dioxide
Needs heavy-duty burners, fuel pumps, and filters
Best For:
Power plants, large cement and steel industries with continuous operation.
🔹 3. Kerosene
Kerosene is a clean-burning, low-viscosity distillate fuel often used in smaller or backup boilers.
Parameter | Value |
---|---|
Calorific Value | ~10,200 kcal/kg |
Sulfur Content | Very low (<0.1%) |
Flash Point | 38–60°C |
Viscosity | ~1.5–2.5 cSt |
Advantages:
Clean combustion
No sludge or wax formation
Stable over time
Limitations:
Higher cost
Limited availability in some regions
Best For:
Backup boilers, lab and pharma heating systems, and cold environments.
🔹 4. Marine Fuel Oil (IFO 180 / IFO 380)
Intermediate Fuel Oils (IFO) are blends of heavy fuel and distillates designed for marine engines and large stationary boilers.
Parameter | Value |
---|---|
Calorific Value | ~9,800 kcal/kg |
Sulfur Content | Typically 0.5–1.5% |
Viscosity | 180–380 cSt @ 50°C |
Advantages:
Cheaper than pure distillates
Acceptable for high-output, long-running boilers
Best For:
Shipping ports, marine terminals, and heavy industrial boiler systems.
🔹 5. Biodiesel (FAME – Fatty Acid Methyl Esters)
A renewable fuel derived from vegetable oils or animal fats, biodiesel is increasingly used for sustainability-focused applications.
Parameter | Value |
---|---|
Calorific Value | ~8,800–9,200 kcal/kg |
Sulfur Content | None |
Flash Point | >100°C |
Viscosity | ~4–5 cSt |
Advantages:
Renewable and biodegradable
Very low emissions (NOₓ and SO₂)
Compatible with modified LFO burners
Limitations:
Susceptible to oxidation and microbial growth
May solidify at low temperatures
Needs fuel conditioning and heating systems
Best For:
Eco-conscious industries, government buildings, or green-certified operations.
🔹 6. Pyrolysis Oil (Bio-oil)
A byproduct of biomass pyrolysis, this liquid fuel is still emerging as an alternative to fossil oils.
Parameter | Value |
---|---|
Calorific Value | ~5,000–6,000 kcal/kg |
Water Content | High (15–30%) |
Viscosity | High, varies with composition |
Advantages:
Renewable and carbon-neutral
Produced from agricultural/wood waste
Limitations:
Low stability and corrosiveness
Requires advanced combustion control
Not yet widely commercialized
Best For:
Pilot projects, R&D facilities, or biomass-integrated boiler systems.
Comparative Summary Table
Fuel Type | CV (kcal/kg) | Viscosity | Preheating Required | Cost Trend | Emissions Profile |
---|---|---|---|---|---|
Diesel (LFO) | 10,000 | Low | No | Medium | Low sulfur, clean burn |
HFO (No. 6) | 9,800 | Very High | Yes (~130°C) | Low | High SO₂, soot |
Kerosene | 10,200 | Very Low | No | High | Very clean |
Marine Oil (IFO) | 9,800 | High | Yes (~90–110°C) | Medium | Moderate sulfur, dense ash |
Biodiesel | 8,800 | Moderate | Sometimes | High | Renewable, very low SO₂ |
Pyrolysis Oil | 5,000–6,000 | High | Yes | Variable | Renewable, experimental |
Summary: Choosing the Right Fuel for Industrial Oil-Fired Boilers
Selection Criteria | Fuel Recommendations |
---|---|
Low cost & high capacity | HFO, Marine Oil |
Clean combustion | Diesel, Kerosene, Biodiesel |
Renewable energy | Biodiesel, Pyrolysis Oil |
Low maintenance | Diesel, Kerosene |
Fuel flexibility | Crossover burners for LFO/HFO or bio-oils |
Choosing the appropriate fuel type ensures your industrial oil-fired boiler operates with maximum efficiency, reliability, and compliance—whether the goal is economic operation, emission reduction, or renewable integration. Fuel compatibility should be assessed alongside burner design, local regulations, and operational demand for a fully optimized system.
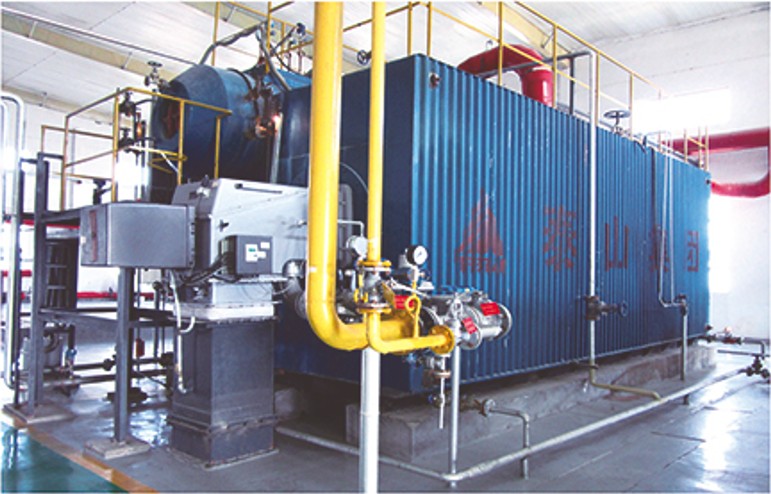
How does fuel viscosity influence burner selection and atomization methods?
![Oil-fired boiler burner system showing fuel viscosity impact on atomization and burner selection]
Prompt: Industrial oil-fired boiler burner system diagram illustrating different atomization methods and fuel viscosity impacts including rotary cup, pressure jet, steam-assisted, and mechanical atomization + fuel heating system and viscosity meters + modern boiler room environment + highly technical and analytical mood + bright lighting
When designing or operating an industrial oil-fired boiler, fuel viscosity is a decisive factor in burner selection and atomization method. Viscosity determines how easily fuel flows, sprays, and mixes with air—directly affecting combustion efficiency, flame stability, soot formation, and emissions. Using the wrong burner for a particular fuel viscosity can result in poor atomization, incomplete combustion, excessive soot and corrosion, and higher operating costs.
Fuel viscosity influences burner selection and atomization methods because it affects the fuel’s flow behavior and atomization performance. Low-viscosity fuels such as diesel or kerosene can be atomized with pressure-jet or air-assisted burners, while high-viscosity fuels like heavy fuel oil require preheating and specialized atomization methods such as steam-assisted or rotary cup burners. Correct matching ensures fine fuel droplets, complete combustion, reduced emissions, and stable flame control.
Below, we explore the relationship between fuel viscosity, burner type, and atomization technique in technical detail.
🔹 1. What Is Fuel Viscosity and Why It Matters
Viscosity is a measure of a fluid’s resistance to flow. In fuel oils, viscosity affects:
How fuel travels through pumps, valves, and nozzles
How well it atomizes into fine droplets at the burner tip
How it mixes with air to create a combustible mixture
Fuel Type | Viscosity (cSt @ 50°C) |
---|---|
Kerosene | 1–2 |
Diesel (No. 2) | 2–4 |
Marine Oil (IFO 180) | 180 |
Heavy Fuel Oil | 200–500+ |
Biodiesel | 4–6 |
High viscosity = poor atomization unless heated or mechanically broken down
🔹 2. Atomization: The Critical Step in Combustion
Atomization is the process of breaking liquid fuel into fine droplets, ensuring rapid vaporization and combustion. The smaller the droplets:
The larger the surface area
The faster and more complete the combustion
The lower the emissions and soot
Droplet Size Range | Combustion Performance |
---|---|
<50 microns | Optimal, clean combustion |
50–100 microns | Acceptable, moderate emissions |
>100 microns | Poor, incomplete combustion |
The viscosity of the fuel affects how easily droplets can be formed.
🔹 3. Burner Types and Matching Viscosity
🔸 A. Pressure Jet Burner (Pressure Atomizing)
Uses a high-pressure fuel pump to force fuel through a small orifice
Creates a spray cone pattern
| Best For | Fuels with viscosity < 20 cSt (e.g., diesel, LFO) | | Limitations | Ineffective with thick fuels or high flow rates |
🔸 B. Air or Steam Atomizing Burner
Uses compressed air or steam to assist fuel break-up
Adjustable droplet size and spray angle
| Best For | Medium to high viscosity fuels (20–150 cSt) | | Advantages | Improved atomization control, lower burner fouling| | Drawback | Requires auxiliary air or steam systems |
🔸 C. Rotary Cup Burner
Uses a rotating disc or cup to fling the fuel into droplets by centrifugal force
Suitable for very high viscosity fuels
| Best For | Heavy fuel oil, IFO, or blends >200 cSt | | Advantages | Excellent for multi-fuel systems, steady flame | | Drawback | Mechanical complexity and higher maintenance |
🔸 D. Twin-Fluid Burner (Air + Fuel)
Combines low-pressure fuel with high-velocity air to atomize
Used where high turndown and variable fuel quality is expected
| Best For | Mixed viscosity, bio-oils, or waste oils | | Notes | Flexible but depends on clean compressed air |
🔹 4. Fuel Preheating to Reduce Viscosity
For heavy oils, preheating is mandatory to:
Reduce viscosity to atomizable levels (typically <30 cSt)
Prevent nozzle clogging and ensure smooth fuel delivery
Minimize incomplete combustion and soot formation
Target Temperature | Viscosity Goal for Atomization |
---|---|
~100–130°C | 10–25 cSt |
Preheaters may be electric, steam-jacketed, or inline heat exchangers.
🔹 5. Fuel System Configuration by Viscosity
Viscosity Level | System Features |
---|---|
Low (<10 cSt) | Simple pumps, pressure-jet burner, no preheater |
Medium (10–100 cSt) | Steam-assisted atomizer, fuel heaters, filters |
High (100–500+ cSt) | Rotary cup burner, dual heaters, heated storage tanks |
🔹 6. Real-World Burner Selection Examples
Application | Fuel Type | Viscosity | Burner Type | Atomization Method |
---|---|---|---|---|
Backup Boiler (Hospital) | Diesel | 3 cSt | Pressure Jet | Mechanical |
Steel Mill Boiler | HFO No. 6 | 350 cSt | Rotary Cup | Centrifugal |
Port Utility Boiler | IFO 180 | 180 cSt | Steam Atomizing | Twin Fluid |
Renewable Facility | Biodiesel | 5 cSt | Air Atomizing | Pneumatic |
Summary: How Viscosity Affects Burner and Atomization Selection
Fuel Viscosity | Atomization Strategy | Suitable Burner Types |
---|---|---|
Low (<10 cSt) | Pressure only | Pressure jet, mechanical atomizers |
Medium (10–100 cSt) | Assist with air/steam | Steam/air-assisted burners |
High (>100 cSt) | Preheat + centrifugal force | Rotary cup, heavy oil dual burners |
Choosing the right burner and atomization method based on fuel viscosity ensures efficient combustion, reliable startup, low maintenance, and environmental compliance. It also protects the boiler from soot fouling, coking, and heat transfer losses, extending system lifespan and operational performance.
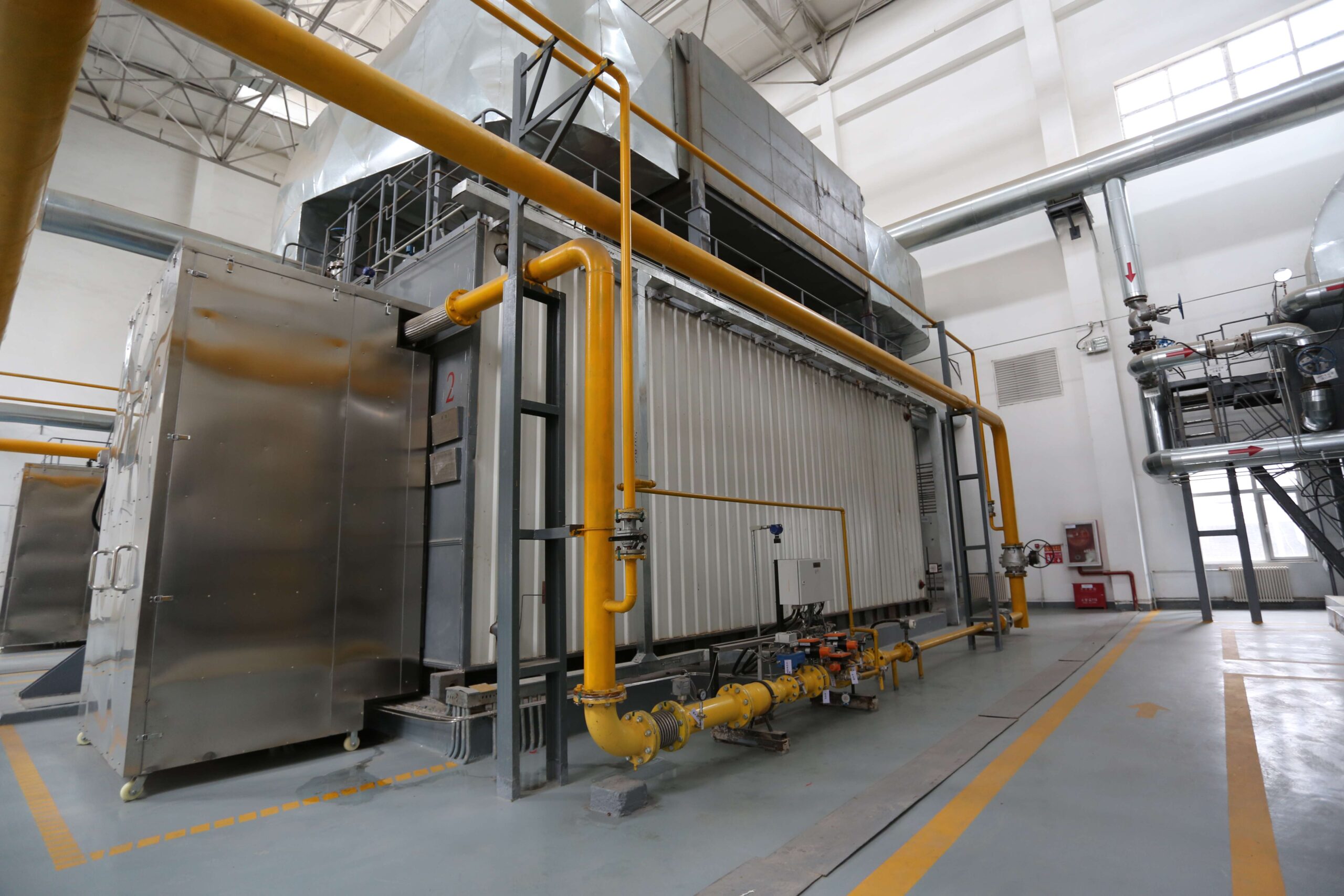
Why does calorific value matter when determining boiler efficiency and capacity?
When selecting or designing a boiler—whether for steam generation, hot water production, or thermal energy—the calorific value (CV) of the fuel is one of the most important parameters to consider. The CV directly affects how much energy the fuel can provide, how efficiently it burns, and what kind of combustion system is needed to convert that fuel into usable heat. If the calorific value is misunderstood or neglected during boiler specification, it can lead to undersized or oversized equipment, poor thermal efficiency, and excessive fuel consumption.
Calorific value matters when determining boiler efficiency and capacity because it quantifies the amount of energy available per unit of fuel, influencing how much fuel is required to meet a specific thermal output. Higher-calorific fuels produce more energy with less volume or mass, enabling smaller fuel feeding systems and more compact combustion chambers, while lower-calorific fuels require higher input rates and larger boilers to deliver the same output. This directly affects boiler sizing, fuel consumption rates, heat transfer surface area, and operating efficiency.
Here’s a detailed exploration of the relationship between calorific value, boiler efficiency, and system capacity.
🔹 1. What Is Calorific Value (CV)?
Calorific Value is the amount of heat energy released when a unit mass (or volume) of fuel is completely combusted under standard conditions.
CV Types | Description |
---|---|
Gross CV (GCV) | Includes latent heat of vaporization of water |
Net CV (NCV) | Excludes the heat carried away in water vapor (real-world) |
Unit | Common Measures |
---|---|
kcal/kg (solid/liquid) | Coal, oil, biomass |
MJ/kg or kJ/kg | SI units for all fuels |
BTU/lb | US customary unit |
🔹 2. How CV Affects Boiler Capacity Sizing
To deliver a specific amount of thermal energy, the required fuel input depends on the calorific value:
Formula:
Required Fuel Input (kg/h) = Boiler Heat Load (kcal/h) ÷ CV (kcal/kg)
Example:
Heat Load: 12,000,000 kcal/h
Fuel A CV = 6,000 kcal/kg → Fuel Required = 2,000 kg/h
Fuel B CV = 3,000 kcal/kg → Fuel Required = 4,000 kg/h
🔸 Implications of Lower CV:
Higher fuel volume or mass per hour
Larger fuel feeder and storage
Bigger furnace to ensure combustion time
Higher flue gas volume → bigger fans and stack
🔹 3. Impact on Boiler Efficiency
Boiler Efficiency = (Useful Heat Output ÷ Fuel Heat Input) × 100
If the fuel has a lower calorific value, the boiler must:
Burn more fuel to generate the same amount of heat
Handle more ash, moisture, or volatile matter
Potentially lose more heat in flue gases or unburned residue
High CV Fuels (e.g., diesel, natural gas):
Burn cleanly with high flame temperature
Achieve 90–95% thermal efficiency with proper design
Require smaller combustion chambers
Low CV Fuels (e.g., biomass, RDF, lignite):
Result in more incomplete combustion and stack losses
Yield 70–85% efficiency unless optimized (e.g., CFB technology)
Require air staging, larger beds, and better heat recovery systems
🔹 4. Fuel Types and Their Calorific Values
Fuel Type | Gross CV (kcal/kg) | Efficiency Consideration |
---|---|---|
Natural Gas | ~9,300–9,600 | High efficiency (>92%) |
Diesel Oil | ~10,000–10,200 | Very efficient, clean burn |
Bituminous Coal | ~6,000–7,000 | Medium CV, high ash risk |
Lignite | ~3,000–4,500 | Low CV, requires large boiler size |
Biomass (wood chips) | ~2,500–4,000 | Moisture-sensitive, needs drying |
RDF | ~2,000–4,500 | Inconsistent composition |
🔹 5. Heat Transfer and Emissions Impact
High CV fuels produce higher flame temperatures, improving heat transfer but may increase NOₓ formation.
Low CV fuels often have high moisture or ash, leading to:
Slower combustion
More fouling of heat exchangers
More particulate emissions
Need for larger ESPs or baghouses
🔹 6. Boiler Design Adjustments Based on CV
CV Category | Design Requirement |
---|---|
High CV | Compact furnace, pressure atomizers |
Medium CV | Standard-sized bed and air system |
Low CV | Larger combustion chamber, extended residence time, fuel pre-drying |
CFB and fluidized bed boilers are ideal for low CV fuels, providing better combustion efficiency at lower flame temperatures and handling variable fuel quality.
🔹 7. Real-World Example: Cement Plant Boiler
Steam Demand: 40 TPH
Efficiency: 88%
Required Thermal Output = 40,000 × 740 = 29.6 million kcal/h
Fuel Used | CV (kcal/kg) | Fuel Rate Required (kg/h) |
---|---|---|
Bituminous Coal | 6,800 | 4,353 kg/h |
Lignite | 4,000 | 7,400 kg/h |
Biomass | 3,200 | 9,250 kg/h |
Conclusion: Low-CV fuels increase required fuel throughput by 2× or more, impacting size, feeding systems, emissions, and O&M costs.
Summary: Why Calorific Value Is Essential in Boiler Design
Aspect Influenced | Calorific Value Impact |
---|---|
Fuel Input Rate | Higher CV = less fuel per hour |
Combustion Chamber Size | Lower CV = longer combustion time → larger furnace |
Burner Type and Setup | Low CV may need dual fuel or staged air |
Emissions and Fouling | Lower CV = more ash and unburned residue |
Overall Efficiency | Efficiency drops if low CV fuel isn’t handled properly |
Selecting and sizing a boiler without knowing the calorific value of the fuel is like building a car without knowing the engine size. To ensure optimal thermal performance, fuel economy, and environmental compliance, the CV must be factored into every stage of boiler design, operation, and fuel management strategy.
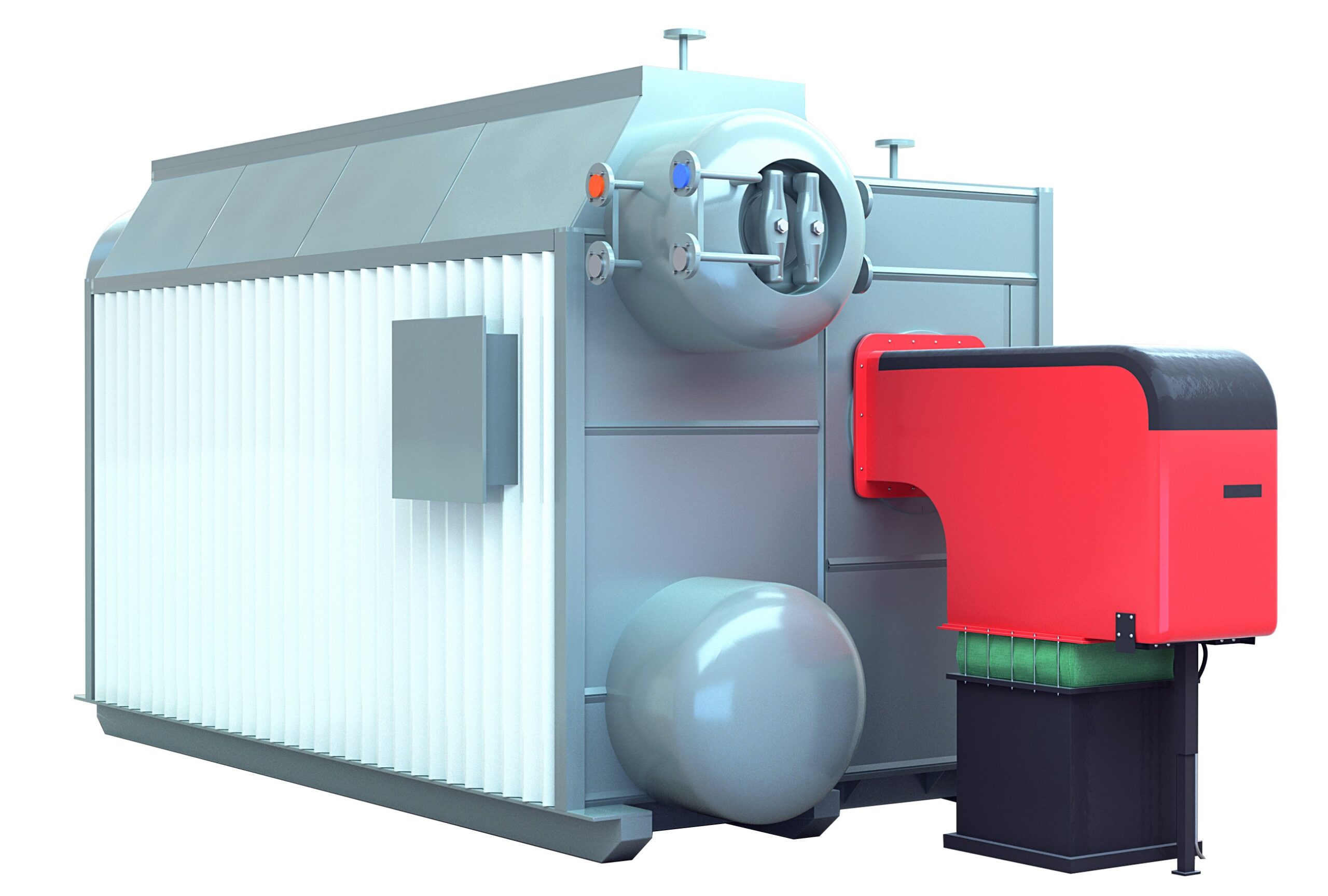
How does sulfur content affect emissions and flue gas treatment requirements?
In any industrial boiler system, especially those burning oil or coal-based fuels, the sulfur content of the fuel has a direct and significant impact on the type and complexity of emissions control systems required. High sulfur content results in greater emissions of sulfur oxides (primarily SO₂ and SO₃), which are regulated pollutants due to their contribution to acid rain, respiratory illness, and corrosion of downstream equipment. To comply with environmental standards and protect equipment, facilities must implement flue gas treatment systems matched to the sulfur levels of the fuel.
Sulfur content affects emissions by increasing the concentration of sulfur dioxide (SO₂) and sulfur trioxide (SO₃) in the flue gases. Higher sulfur content requires more advanced flue gas treatment systems such as wet or dry scrubbers, sorbent injection, or flue gas desulfurization (FGD) units. It also influences material selection for ducting, corrosion control measures, and operational cost. Lower sulfur fuels reduce these demands, simplify the emissions system, and support easier compliance with air quality regulations.
Let’s explore how sulfur content influences emissions, equipment design, and compliance requirements in depth.
🔹 1. What Happens to Sulfur During Combustion?
When sulfur-containing fuels are burned, sulfur reacts with oxygen to form:
Reaction Type | Chemical Equation | Description |
---|---|---|
Primary (SO₂) | S + O₂ → SO₂ | 95–98% of sulfur forms SO₂ |
Secondary (SO₃) | 2SO₂ + O₂ → 2SO₃ | <5% forms SO₃ under excess O₂ or catalyst presence |
These gases exit the combustion chamber with the flue gas. When cooled and mixed with water vapor, they form sulfurous (H₂SO₃) or sulfuric acid (H₂SO₄)—corrosive and hazardous substances.
🔹 2. Sulfur Content by Fuel Type
Fuel Type | Typical Sulfur Content (%) |
---|---|
Ultra-low sulfur diesel (ULSD) | <0.05% |
Light fuel oil (LFO) | 0.1–0.5% |
Heavy fuel oil (HFO) | 1.5–4.5% |
Petroleum coke | 3.0–6.0% |
Coal (Bituminous) | 0.5–2.5% |
Biodiesel | ~0% |
🛢️ Higher sulfur fuels = higher SO₂ output = more treatment required
🔹 3. SO₂ Emission Calculation Based on Sulfur Content
Formula:
SO₂ (kg/h) = Fuel Flow (kg/h) × Sulfur Content (%) × 2
Example:
Fuel Flow: 2,000 kg/h
Sulfur Content: 2%
SO₂ = 2,000 × 0.02 × 2 = 80 kg/h
This translates to:
Over 1,900 kg/day of SO₂, requiring strict mitigation
🔹 4. Flue Gas Treatment Systems Required for High Sulfur Fuels
Sulfur Level | Required Emissions Controls |
---|---|
<0.1% | No desulfurization needed; basic stack monitoring |
0.1–1.0% | Dry sorbent injection, fuel switching, low-sulfur blending |
1.0–2.5% | Spray dryer absorbers, semi-dry FGD, limestone injection |
>2.5% | Wet FGD (scrubber towers), gypsum production, corrosion control |
🔹 5. Desulfurization Technologies Overview
🔸 A. Dry Sorbent Injection (DSI)
Injects powdered lime or sodium bicarbonate into flue gas
Simple, low capital cost
Removes up to 70% SO₂
🔸 B. Spray Dryer Absorber (SDA)
Atomizes lime slurry into flue gas stream
SO₂ absorbed and collected as dry salt
80–90% removal efficiency
🔸 C. Wet Flue Gas Desulfurization (WFGD)
Recirculating limestone or magnesium hydroxide slurry
High efficiency (>95%) SO₂ removal
Byproduct: gypsum (used in construction)
Treatment Method | SO₂ Removal Efficiency | CAPEX/Complexity |
---|---|---|
DSI | 40–70% | Low |
SDA | 70–90% | Medium |
WFGD | 90–99% | High |
🔹 6. System Design Considerations for High Sulfur Operation
Design Area | Consideration |
---|---|
Ducting Materials | Use acid-resistant steel or coatings |
Stack Design | Ensure acid dew point is avoided |
Water Treatment | Capture sulfuric acid from wet scrubbers |
Sootblower Frequency | Higher due to sulfur deposits |
Fan Size | Must overcome pressure drops in scrubbers |
🔹 7. Environmental and Regulatory Implications
Regulation Zone | Typical SO₂ Limit (mg/Nm³) |
---|---|
EU (IED Directive) | 200–400 mg/Nm³ |
US (EPA NSPS) | 1.2 lb/MMBtu (~300 mg/Nm³) |
China GB Standards | ≤200 mg/Nm³ (strict zones) |
Non-compliance risks:
Heavy fines
Operational shutdowns
Permit loss and reputational damage
🟩 Switching to low-sulfur fuels or installing FGD units is mandatory in many jurisdictions for HFO or coal systems.
🔹 Real-World Example: Oil-Fired Power Plant
Boiler Capacity: 50 TPH
Fuel: Heavy fuel oil (3.5% sulfur)
SO₂ output = 50 × 700 kcal/kg × 0.035 × 2 = ~2,450 kg/day
Emissions target: ≤200 mg/Nm³
Solution:
Installed WFGD system
Achieved 98.7% SO₂ reduction
Qualified for low-emission subsidies and green certification
Summary: Why Sulfur Content Matters in Flue Gas Treatment
Sulfur Content (%) | SO₂ Emissions Impact | Flue Gas Treatment Required |
---|---|---|
<0.1% | Minimal SO₂ | No scrubber, basic monitoring only |
0.1–1.0% | Moderate SO₂ | Dry injection or blending |
1.0–2.5% | High SO₂ | Semi-dry SDA or dual-stage scrubbers |
>2.5% | Very high SO₂ | Full wet FGD, corrosion protection |
Understanding and planning for fuel sulfur content during boiler selection or system design is essential for regulatory compliance, equipment longevity, and environmental stewardship. Choosing low-sulfur fuels or properly engineering the desulfurization systems ensures your industrial boiler remains efficient, legal, and operationally sound in an emissions-regulated world.
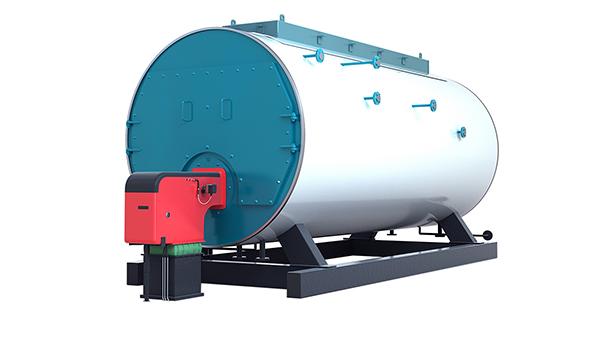
What combustion adjustments are needed when switching to bio-oil or alternative fuels?
With the global push toward decarbonization and renewable energy integration, many industrial facilities are switching from fossil-based fuels to bio-oils or alternative liquid fuels. While this transition offers environmental and regulatory advantages, it also introduces challenges related to fuel behavior, combustion stability, and equipment compatibility. Bio-oils—such as biodiesel, pyrolysis oil, and waste-derived liquids—often have different chemical compositions, viscosities, flash points, and energy densities, which necessitate precise combustion system adjustments to maintain efficiency, safety, and emissions compliance.
When switching to bio-oil or alternative fuels, combustion system adjustments are required to address differences in fuel viscosity, calorific value, combustion characteristics, and emissions profile. These adjustments include burner reconfiguration or replacement, atomization method modification, fuel preheating or conditioning, air-fuel ratio tuning, flame detection calibration, and integration of emissions controls such as soot blowers or condensate separators. Proper system adaptation ensures complete combustion, stable flame, minimal fouling, and regulatory compliance.
Here’s a detailed breakdown of the combustion adjustments needed when transitioning to bio-oil or other non-traditional fuels in industrial boilers.
🔹 1. Understand the Characteristics of the New Fuel
Fuel Property | Impact on Combustion System |
---|---|
Viscosity | Affects pump design, atomization quality |
Calorific Value (CV) | Changes required fuel feed rate and burner sizing |
Water Content | Influences ignition stability and soot formation |
Oxygen Content | Alters stoichiometric air requirement |
Flash Point | Impacts ignition temperature and preheating needs |
Ash or Char Residue | May cause fouling, coking, or burner blockage |
Common Bio-Oil Values (Indicative):
Fuel Type | CV (kcal/kg) | Viscosity (cSt @ 50°C) | Water Content (%) | Flash Point (°C) |
---|---|---|---|---|
Biodiesel (FAME) | 8,800–9,200 | 4–6 | <0.1 | >100 |
Pyrolysis Oil | 4,000–6,000 | 15–50+ | 15–30 | ~100 |
Waste Oil Blends | 7,000–9,500 | Highly variable | 1–10 | 60–120 |
🔹 2. Burner System Adjustments
Burners must match the fuel’s flow properties and combustion characteristics.
🔸 A. Atomization Method Adjustment
Bio-oils often require air or steam atomization for finer droplet size.
High-viscosity fuels may need rotary cup burners or dual-fluid systems.
Atomization Type | Best For Fuels With… |
---|---|
Pressure Jet | Low viscosity (e.g., biodiesel) |
Steam/Air Assist | Medium to high viscosity |
Rotary Cup | High viscosity or unrefined bio-oils |
🔸 B. Fuel Preheating and Conditioning
Lower CV fuels need greater volume for same output
High viscosity bio-oils need preheating to ~60–120°C for proper flow
Emulsion fuels may need separators or homogenizers
Component | Adjustment Action |
---|---|
Fuel Heater | Add or recalibrate for new temperature setpoint |
Filters & Strainers | Upgrade to remove char or wax particles |
Pumps | Use positive displacement or screw pumps for thick fuels |
🔸 C. Air-Fuel Ratio and Combustion Tuning
Bio-oils typically contain oxygen within their molecular structure → lower external air needed.
Reduce excess air to prevent temperature drop
Recalibrate O₂ sensors and combustion curves
Use oxygen trim systems for real-time air control
🔹 3. Combustion Chamber and Flame Monitoring
🔸 A. Flame Shape and Stability
Flame may be shorter and bluer due to high volatiles (e.g., in pyrolysis oil)
Need to verify flame impingement zones to prevent tube overheating
🔸 B. Flame Detection Sensor Calibration
Recalibrate UV/IR detectors for different flame spectra
Bio-oil flames may have weaker IR signatures → sensor false trips
🔹 4. Heat Transfer and Fouling Considerations
Bio-oils with higher ash content or char residues:
Cause fouling on heat exchanger tubes
May produce clinkers or sticky deposits on walls
Require more frequent sootblowing or cleaning cycles
🔧 Install automated sootblowers, especially in pyrolysis oil systems
🔹 5. Emission Control Adjustments
🔸 A. Particulate and Tar Formation
Tar-like compounds in pyrolysis oils → sticky residues in stack
ESPs or baghouse filters may be required
🔸 B. NOₓ and CO Emissions
Adjust burner turndown and flame temperature
Tune staged combustion and flue gas recirculation if applicable
🔸 C. Condensate and Corrosion
Bio-oils produce organic acids → flue gas condensate may corrode stacks
Install condensate neutralizers, upgrade stack lining
🔹 6. Real-World Transition Example
Facility: Pharmaceutical plant
Original Fuel: Diesel (No. 2 Oil)
New Fuel: Biodiesel (B100)
Boiler Output: 4 TPH
Modifications:
Installed fuel preheater (to 80°C)
Switched to air-assisted burner
Retuned O₂ trim system
Replaced flame sensor for broader UV detection
Cleaned soot every 150 hours (vs. 300 hours on diesel)
Result:
92% combustion efficiency maintained
NOₓ reduced by 18%
Annual fuel savings: $14,700 from biofuel subsidies
Summary: Combustion Adjustments for Bio-Oil & Alternative Fuels
Adjustment Area | Required Modifications |
---|---|
Burner Type | Select atomization method based on viscosity |
Fuel System | Preheating, filtering, flow control upgrades |
Air-Fuel Ratio | Reduce excess air, recalibrate combustion controller |
Flame Detection | Upgrade to multi-spectrum UV/IR sensors |
Fouling Management | Add sootblowers, schedule more frequent cleaning |
Emission Controls | Tar filters, stack lining, condensate drain protection |
Transitioning to bio-oil or alternative fuels in industrial boilers can be highly successful and environmentally beneficial—but only when combustion systems are properly adapted to the new fuel’s properties. These adjustments ensure safe, efficient, low-emission operation across the full load range.
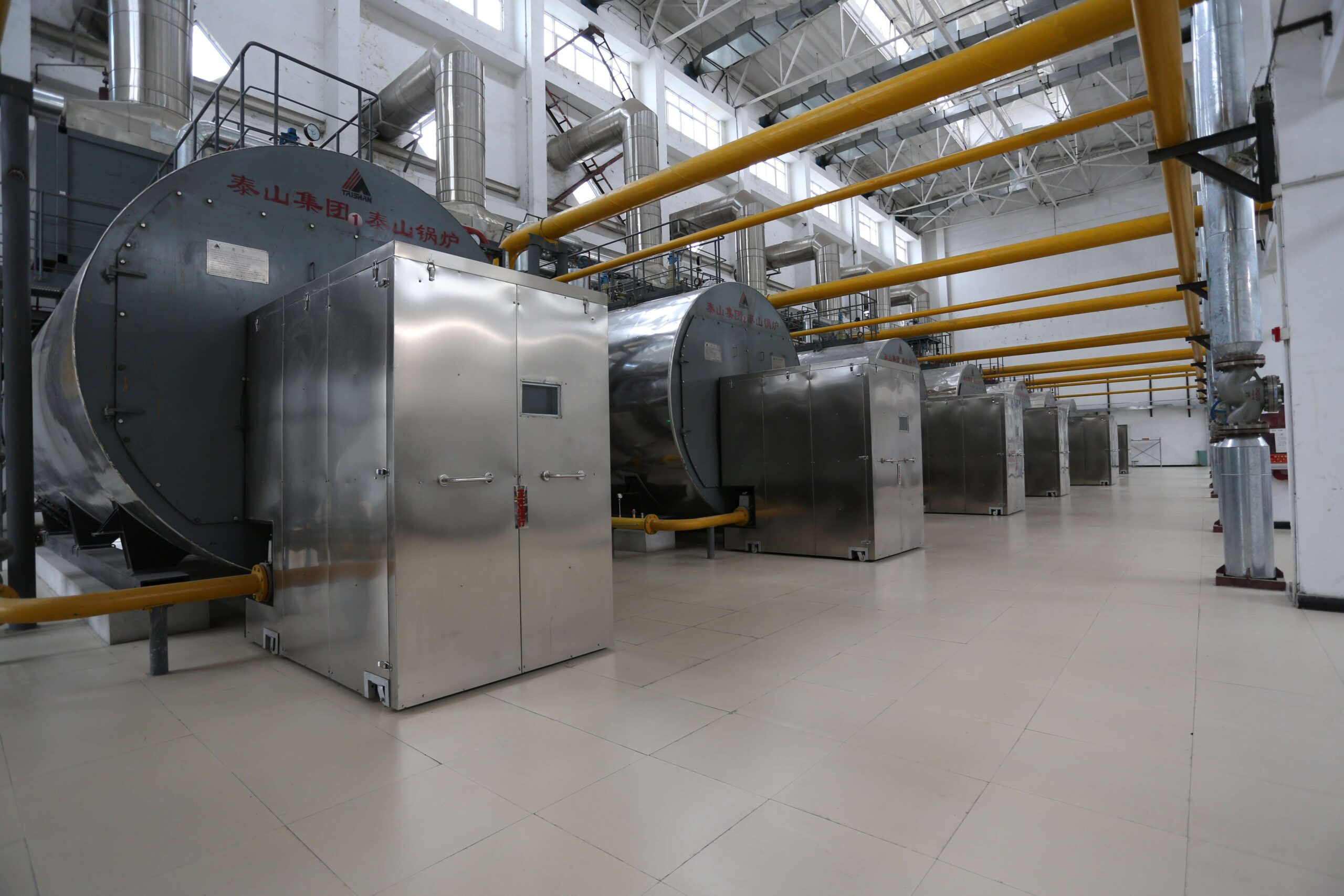
How do fuel characteristics impact maintenance frequency and operational stability?
The characteristics of the fuel used in an industrial boiler—whether it is diesel, heavy fuel oil, biodiesel, pyrolysis oil, or waste-derived blends—have a profound effect on maintenance schedules and operational reliability. Some fuels burn cleanly and consistently, resulting in long intervals between maintenance. Others, due to their high ash, sulfur, or moisture content, can rapidly foul heat exchange surfaces, erode components, or destabilize combustion, leading to frequent shutdowns, unplanned downtime, and elevated O&M costs.
Fuel characteristics impact maintenance frequency and operational stability by influencing soot and ash buildup, corrosion rates, burner wear, deposit formation, and combustion uniformity. Fuels with high sulfur, water content, viscosity, or ash accelerate fouling, cause uneven flame patterns, and corrode internal components, leading to more frequent cleaning, part replacement, and combustion tuning. Cleaner, drier, and more stable fuels extend maintenance intervals and improve system uptime.
Here is an in-depth technical analysis of how key fuel properties influence boiler performance and maintenance needs.
🔹 1. Sulfur Content: Corrosion and Emissions Impact
High sulfur fuels (e.g., HFO, petcoke) release sulfur oxides (SO₂ and SO₃) during combustion. When combined with moisture, these form acidic condensates (H₂SO₄) that corrode metal surfaces, especially in:
Air preheaters
Economizers
Flue ducts and stacks
Sulfur Content (%) | Corrosion Risk | Maintenance Impact |
---|---|---|
<0.1 | Minimal | No special materials or coatings required |
0.5–1.5 | Moderate | Annual stack inspection, corrosion monitoring |
>2.5 | High | Acid-resistant linings, more frequent cleaning |
📌 More sulfur → more corrosion → shorter component lifespan
🔹 2. Ash and Solid Residue: Fouling and Abrasion
Some fuels (coal, RDF, unrefined bio-oils) contain non-combustible minerals that form ash and slag.
Fuel Ash Content (%) | Fouling Behavior | Maintenance Impact |
---|---|---|
<0.1 | Minimal | Occasional cleaning |
0.5–2.0 | Moderate | Tube brushing every few months |
>3.0 | Severe fouling | Weekly sootblowing, slag removal |
Deposits reduce heat transfer, raise stack temperatures, and can block tubes, triggering pressure alarms.
🔧 Boilers running high-ash fuels must be fitted with automated sootblowers and fouling sensors.
🔹 3. Viscosity and Flowability: Fuel System Wear and Atomization
High-viscosity fuels (HFO, pyrolysis oil) can:
Clog filters and strainers
Erode burner tips
Damage fuel pumps if not properly heated
Viscosity (cSt @ 50°C) | Fuel System Impact | Maintenance Frequency |
---|---|---|
<10 | Low wear | Standard preventive service (3–6 months) |
10–100 | Moderate stress | Monthly inspection of lines and nozzles |
>100 | High wear and fouling risk | Weekly heating system check, frequent nozzle cleanouts |
🛢️ Poorly atomized fuel → incomplete combustion → more soot and CO emissions
🔹 4. Water and Moisture Content: Combustion Stability and Corrosion
Bio-oils, pyrolysis oils, and emulsified fuels often contain 5–30% water, affecting:
Flame stability (lower temperature)
Ignition reliability
Increased flue gas condensate, leading to acidic corrosion
Water Content (%) | Stability & Maintenance Effects |
---|---|
<0.5 | Stable flame, low corrosion risk |
1–10 | Occasional flameout, flue condensation checks needed |
>10 | Frequent ignition failure, condensate drain maintenance |
💡 Use fuel dryers, heaters, or centrifuges for high-moisture fuels.
🔹 5. Volatility and Flash Point: Safety and Combustion Control
Fuels with low flash points (e.g., kerosene, light oils) require careful burner management to prevent:
Flashback
Premature ignition
Combustion instability
Flash Point (°C) | Operational Risk | Control System Needs |
---|---|---|
>100 | Low | Normal safety protocols |
60–100 | Medium | Automated ignition and flame safeguards |
<60 | High | Advanced flame monitoring, restricted storage |
⚠️ Volatile fuels require calibrated flame sensors and fine air-fuel control.
🔹 6. Combustion Residue and Coking Tendency
Unrefined or low-quality fuels can leave sticky carbon deposits (coke) on:
Burner tips
Combustion chamber walls
Flue gas recirculation ducts
This requires:
Manual scraping or solvent flushing
Inspection during each shutdown
Shortened overhaul intervals
🧼 Install anti-coking burners and schedule frequent visual inspections for residue-forming fuels.
🔹 7. Maintenance Schedule Comparison by Fuel Type
Fuel Type | Maintenance Intensity | Typical Actions | Inspection Frequency |
---|---|---|---|
Natural Gas | Low | Minimal soot, clean burners | Annual |
Diesel (LFO) | Low to Medium | Nozzle inspection, minor fouling | Every 6 months |
HFO (Heavy Oil) | High | Sootblowing, burner cleaning, acid checks | Weekly to Monthly |
Biodiesel | Medium | Filter replacement, flame sensor tuning | Every 3 months |
Pyrolysis Oil | Very High | Char removal, nozzle coking, condensate drain | Weekly |
RDF or Waste Oils | Very High | Ash removal, corrosion check, slag scraping | Weekly or Daily (as needed) |
🔹 Summary: Fuel Characteristics vs. Boiler Maintenance & Stability
Fuel Characteristic | Maintenance Impact | Operational Stability Impact |
---|---|---|
High sulfur | Corrosion of stack, economizer | Unstable pH in condensate drain |
High ash | Frequent tube fouling | Temperature imbalance, load fluctuations |
High viscosity | Burner wear, pump failures | Poor atomization, flame instability |
High moisture | Flame dropout, acidic condensate | Delayed ignition, condensate corrosion |
High volatility | Flame flashback, burner fouling | Tight control required |
Using cleaner, stable, and well-processed fuels can significantly reduce boiler maintenance costs and increase uptime, while fuels with challenging properties must be matched with appropriate burner technology, fuel conditioning systems, and rigorous maintenance protocols to preserve long-term system reliability.
🔍 Conclusion
The fuel you choose for your industrial oil-fired boiler has a direct impact on its design, efficiency, emissions, and long-term performance. Whether you’re using light diesel, heavy oil, or renewable alternatives, understanding the combustion characteristics and how they influence burner configuration, heat exchange, and emission control is essential. A proper fuel-to-boiler match ensures optimal performance, regulatory compliance, and reduced operating costs.
📞 Contact Us
💡 Unsure which fuel type is best for your industrial boiler? Our technical experts can help you evaluate fuel options and match them with the right boiler design for maximum efficiency and compliance.
🔹 Let us guide you in selecting the ideal oil-fired boiler and fuel combination for your operation! 🛢️🔥✅
FAQ
How do different fuel oil types affect industrial boiler selection?
The type of fuel oil—light oil (e.g., diesel), medium oil, or heavy fuel oil—affects burner design, preheating requirements, storage infrastructure, and overall combustion efficiency. Lighter oils ignite easily and burn cleaner, while heavier oils are more economical but require complex handling.
What are the combustion characteristics of oil-fired boilers?
Combustion depends on fuel viscosity, calorific value, ignition temperature, and air-to-fuel ratio. Complete combustion ensures high efficiency and lower emissions, which varies based on the oil grade and burner performance.
Why is burner compatibility important in oil-fired boiler systems?
Each burner is calibrated for a specific fuel type and flow rate. Using a mismatched burner leads to incomplete combustion, reduced efficiency, and increased emissions or safety risks. Proper burner-fuel pairing is critical for system performance.
Do fuel impurities and quality impact boiler operation?
Yes. High-sulfur or contaminated oils can cause fouling, corrosion, and soot buildup in the combustion chamber and heat exchanger, leading to frequent maintenance and reduced boiler lifespan. High-quality fuel minimizes these risks.
Can oil-fired boilers be adapted for multiple fuel types?
Some industrial oil-fired boilers support dual-fuel or multi-fuel configurations, allowing switching between fuel oil and alternatives like gas or bio-oil. This enhances fuel flexibility, cost optimization, and energy security.
References
Fuel Properties and Boiler Design – https://www.energy.gov
Combustion Characteristics of Fuel Oils – https://www.sciencedirect.com
Burner Design and Fuel Compatibility – https://www.researchgate.net
Fuel Quality Impact on Boilers – https://www.epa.gov
Heavy Oil Combustion and Boiler Efficiency – https://www.bioenergyconsult.com
Industrial Fuel Oil Specifications – https://www.mdpi.com
Boiler Maintenance and Fuel Contaminants – https://www.energysavingtrust.org.uk
Multi-Fuel Boiler Systems Overview – https://www.iea.org
Dual-Fuel Burner Technology – https://www.automation.com
Fuel Viscosity and Boiler Operation – https://www.sciencedirect.com
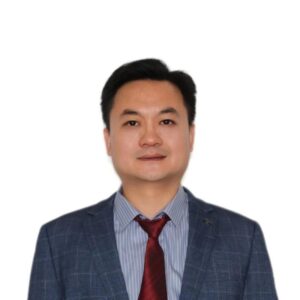