When selecting an industrial steam boiler, many buyers focus on output capacity, pressure ratings, and cost—but neglecting to consider fuel types and combustion characteristics can lead to serious operational inefficiencies. Choosing a boiler without matching it to the right fuel properties can cause incomplete combustion, excessive emissions, high maintenance costs, or non-compliance with environmental regulations. Understanding the interaction between fuel characteristics and boiler design is critical to achieving optimum performance, fuel efficiency, and long-term reliability.
Fuel types and combustion characteristics affect your choice of industrial steam boiler by influencing the burner configuration, furnace size, heat transfer efficiency, emission controls, ash handling systems, and overall boiler performance. Fuels such as coal, natural gas, oil, biomass, and waste materials vary significantly in calorific value, moisture content, combustion air requirements, ignition temperature, and ash content. These properties determine the most suitable boiler technology—whether it’s a fire-tube, water-tube, fluidized bed, or hybrid design—for your application.
Making the right match between fuel and boiler is essential for efficiency, safety, and regulatory compliance.
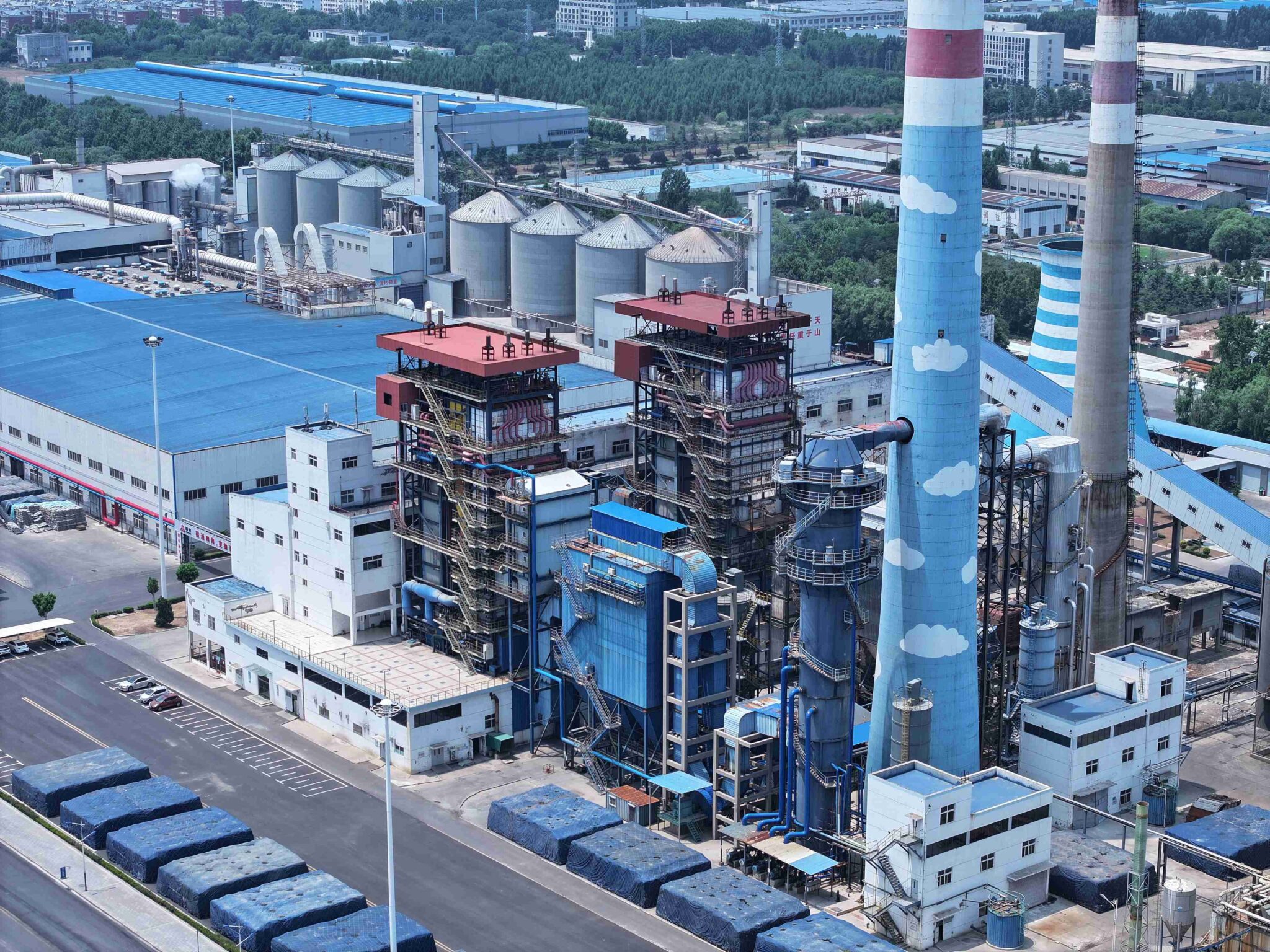
What Are the Common Fuel Types Used in Industrial Steam Boilers and How Do They Differ?
Industrial steam boilers power a wide range of applications—from food processing to textiles to power generation—by converting chemical energy in fuel into steam energy. However, not all fuels burn the same way, and the type of fuel used directly affects boiler size, efficiency, combustion system, emissions, and cost. Some fuels offer high energy content with clean combustion, while others require larger systems, robust ash handling, or advanced emission control. Choosing the right fuel is not just about what’s available—it’s about matching the fuel’s properties with the boiler’s technical requirements and operational goals.
The most common fuel types used in industrial steam boilers are coal, fuel oil, natural gas, biomass (wood chips, pellets, or agricultural residues), and industrial waste fuels. They differ in energy content (calorific value), combustion characteristics, ash and moisture content, emissions profile, storage and handling needs, and operational costs. These differences significantly influence boiler design, performance, and environmental impact.
Selecting the appropriate fuel type is a foundational decision that determines efficiency, compliance, and economic viability.
All fuel types can be used in the same industrial boiler design without modifications.False
Different fuels have unique combustion, ash, and moisture characteristics that require specific boiler designs to operate efficiently and safely.
Comparative Overview of Common Boiler Fuels
Fuel Type | Calorific Value (MJ/kg) | Moisture (%) | Ash (%) | Combustion Behavior | Emission Profile |
---|---|---|---|---|---|
Bituminous Coal | 24–32 | 5–15 | 10–20 | Stable flame, moderate slagging | High SO₂, NOx, particulates |
Lignite | 9–18 | 30–50 | 20–40 | Quick ignition, low flame temp | High ash, low sulfur |
Fuel Oil (Diesel) | 42–44 | <1 | <0.01 | High heat, clean burn | High CO₂, low particulates |
Natural Gas | 48–50 | 0 | 0 | Precise combustion, fast response | Low NOx (with controls) |
Biomass (Wood Chips) | 9–16 | 20–55 | 1–6 | Fast burn, variable CV | Carbon-neutral, high PM |
Biomass (Pellets) | 16–19 | 8–12 | <1 | Uniform combustion | Low ash, renewable |
Waste Fuels (RDF, sludge) | 10–22 | 20–60 | 10–30 | Unstable combustion, custom setup | High variability, needs FGT |
Fuel-by-Fuel Analysis
1. Coal (Bituminous & Lignite)
Pros: High energy density, widely available, long-term supply
Cons: High emissions (SO₂, NOx), heavy ash, needs large furnaces and pollution control
Best for: Large-scale steam generation, power plants
Design Requirements:
Grate, stoker, or pulverized coal systems
Ash hoppers and slagging controls
Electrostatic precipitators (ESPs), desulfurization
2. Fuel Oil (Heavy Oil, Diesel)
Pros: High energy, compact system, low ash
Cons: Volatile fuel costs, higher CO₂ output than gas
Best for: Standby systems, remote locations, backup fuel
Design Requirements:
Burners with atomization
Oil storage with heating coils
Fire-rated enclosures
3. Natural Gas
Pros: Cleanest fossil fuel, easy to control, high efficiency
Cons: Grid dependence, price volatility, safety risk
Best for: Urban/industrial areas with pipeline access
Design Requirements:
High-efficiency burners
Low-NOx combustion systems
Fast start/stop systems for load fluctuations
Natural gas-fired boilers produce fewer emissions than coal-fired systems.True
Natural gas combustion releases less SO₂, NOx, and particulate matter compared to coal, making it a cleaner energy option.
4. Biomass (Chips, Pellets, Ag Waste)
Pros: Renewable, CO₂-neutral, often locally sourced
Cons: Variable moisture/quality, high ash in some cases
Best for: Industries with waste biomass (sawmills, agri-plants)
Design Requirements:
Large furnaces (for low CV)
Grate, FBC, or moving bed systems
Moisture control and ash extraction
5. Industrial Waste Fuels (RDF, Sludge, Bagasse)
Pros: Waste-to-energy benefit, disposal cost offset
Cons: Unstable CV, high variability, strict emission rules
Best for: Cement plants, paper mills, municipal plants
Design Requirements:
Custom combustion zones
Aggressive flue gas cleaning
Waste handling and drying systems
Fuel Comparison Table – Operational Impact
Parameter | Coal | Oil | Gas | Biomass | Waste Fuels |
---|---|---|---|---|---|
Boiler size required | Large | Medium | Small | Very large | Variable |
Ash handling required | Yes | No | No | Yes | Yes |
Startup time | Moderate | Fast | Very fast | Slow | Slow |
Fuel storage footprint | Large (silo) | Medium (tank) | None (pipeline) | Large (shed/silo) | Large (bunker) |
Turndown flexibility | Medium | High | Very high | Medium | Low |
Emission control needed | High | Medium | Low | High (PM) | Very high |
Key Boiler Design Differences by Fuel
Fuel | Required Boiler Features |
---|---|
Coal | Large grate or pulverizer, ash extraction, FGD, ESP |
Oil | Burner with atomizer, oil heater, stack with draft control |
Gas | Compact design, modulating burner, low-NOx control |
Biomass | Large furnace volume, robust fuel feed, multi-stage air |
Waste | Variable fuel bed, high-temp zones, multiple emission stages |
Real-World Case: Textile Plant Fuel Switch
Original Fuel: Diesel (CV = 43 MJ/kg)
New Fuel: Biomass (wood chips, CV = 12 MJ/kg)
Boiler Adaptation:
Furnace volume doubled
Air staging system added
Fuel storage and conveyor installed
Outcome:
35% fuel cost savings
CO₂ emissions reduced by 70%
Minor drop in system efficiency, offset by operating cost
Summary
Each fuel type used in industrial steam boilers brings unique challenges and benefits. The calorific value, combustion profile, ash content, moisture level, and emissions define how the boiler must be designed, operated, and maintained. Gas and oil offer clean, compact solutions, while coal and biomass require large systems and robust handling, but may offer lower fuel costs or renewable benefits. Waste fuels need special care but can improve sustainability. In the end, choosing the right fuel isn’t just about what burns—it’s about what works best for your process, infrastructure, and long-term energy strategy.

How Do Calorific Value and Fuel Composition Affect Boiler Design and Efficiency?
When selecting or designing an industrial boiler, many users focus solely on capacity and cost—yet fuel calorific value (CV) and chemical composition are what truly dictate how efficiently that boiler will run and how it should be engineered. If a boiler is designed for high-calorific fuel but ends up burning low-grade or highly variable fuel, the result is poor combustion, incomplete fuel use, low steam output, or severe fouling. On the other hand, using high-CV fuels in a system built for low temperatures and slow burn rates may lead to overheating or unsafe conditions. Understanding these fuel-specific properties is essential for matching boiler configuration, combustion chamber size, and control systems to maximize long-term efficiency and reliability.
Calorific value and fuel composition directly affect boiler design and efficiency by determining how much heat energy is released during combustion, how fast the fuel burns, and what by-products (ash, sulfur, moisture) are produced. Low-CV fuels require larger furnaces, longer residence time, and higher feed rates, while fuels with high volatile matter need flame stabilization measures. Ash, moisture, sulfur, and mineral content affect corrosion, slagging, emissions, and overall thermal performance. For high efficiency, boilers must be customized to suit the chemical and physical behavior of the specific fuel being used.
Failing to align boiler design with the actual fuel profile results in lost energy, costly maintenance, and regulatory headaches.
A fuel’s calorific value and chemical makeup have minimal impact on boiler design and operation.False
Fuel characteristics such as calorific value, ash, moisture, and sulfur content significantly influence furnace dimensions, combustion conditions, heat exchange design, and emissions control systems.
What Is Calorific Value and Why Does It Matter?
Calorific Value (CV) is the amount of energy released when 1 kg of fuel is fully burned, typically measured in MJ/kg or kcal/kg. It indicates how much fuel is required to produce a certain amount of steam or heat.
Impact of CV on Boiler Design
Fuel Type | Calorific Value (MJ/kg) | Fuel Required per 1,000 kW Output (kg/h) |
---|---|---|
Natural Gas | 48–50 | ~720 |
Fuel Oil | 42–44 | ~850 |
Bituminous Coal | 24–32 | ~1,200–1,400 |
Biomass (Pellets) | 16–19 | ~2,400 |
Lignite | 9–18 | ~3,600 |
Lower CV = more fuel needed = larger furnace, greater flue gas volume, increased ash
Design Adjustments for Low-CV Fuels
Increase combustion chamber size for longer residence time
Install larger heat exchange surfaces
Use enhanced fuel feed systems to manage higher flow rates
Key Fuel Composition Parameters That Affect Boiler Design
Fuel Component | Design Implication |
---|---|
Volatile Matter (VM) | Affects ignition temperature and flame propagation |
Moisture Content | Reduces flame temperature and thermal efficiency |
Ash Content | Requires larger ash handling and slagging management |
Sulfur Content | Needs flue gas desulfurization (FGD) and corrosion protection |
Chlorine / Alkali Metals | Increases risk of tube corrosion and fouling |
High moisture content in fuel lowers boiler efficiency by absorbing heat during vaporization.True
Water in fuel must be evaporated before combustion can proceed, which consumes energy that could otherwise be used to generate steam.
How Fuel Composition Affects Efficiency and Emissions
1. Volatile Matter (VM)
High VM fuels (e.g., biomass, lignite) burn fast but may require flame stabilization
Low VM fuels (e.g., anthracite) need higher furnace temperatures to ignite
Design Response:
Add secondary air staging
Use burner cones or refractory liners for flame stability
2. Moisture Content
Fuel | Moisture (%) | Efficiency Loss (Typical) |
---|---|---|
Dry Bituminous | 5–10 | <5% |
Biomass Chips | 30–50 | 10–15% |
Lignite | 35–60 | 15–20% |
Design Response:
Include fuel drying systems
Oversize furnace to allow more complete combustion
3. Ash Content
Leads to fouling, slagging, and corrosion if not managed
Alters heat transfer efficiency and increases O&M
Design Response:
Install soot blowers
Use fluidized beds for even combustion
Apply anti-slag coatings on furnace tubes
4. Sulfur and Chlorine
Sulfur → SO₂/acidic condensate → causes corrosion
Chlorine → Combines with alkalis → sticky ash, corrosion
Design Response:
Use corrosion-resistant steel (like T22 or Inconel)
Integrate flue gas desulfurization systems
Adjust air/fuel ratio for optimal combustion chemistry
Boiler Efficiency vs. Fuel Quality
Fuel Profile | Combustion Efficiency (%) | Real Boiler Efficiency (%) |
---|---|---|
Dry Natural Gas | 99.5 | 90–92 |
Light Oil (Diesel) | 98.5 | 88–90 |
Bituminous Coal | 96–98 | 82–88 |
Biomass Pellets | 95–97 | 78–84 |
Wet Biomass or Lignite | 90–94 | 65–75 |
Real-world boiler efficiency includes radiation losses, heat lost in blowdown, and stack losses.
Real-World Boiler Redesign: Biomass Fuel Switch
Original fuel: Fuel oil (CV = 42 MJ/kg, moisture <1%)
New fuel: Rice husk (CV = 13 MJ/kg, moisture 20%, ash 18%)
Problems:
Flame instability
Excessive ash buildup
High CO emissions
Adaptations:
Enlarged furnace volume
Installed grate agitators
Added preheated combustion air
Implemented fly ash cyclone separator
Outcome:
24% reduction in fuel cost
Stable flame with 83% efficiency
Low NOx and CO levels post-retrofit
Summary
Calorific value and fuel composition are fundamental to boiler design, combustion performance, and long-term efficiency. Low-calorific fuels need more combustion volume and longer residence time, while moisture and ash demand larger heat recovery and cleaning systems. Volatile matter influences flame stability, and sulfur content drives corrosion and environmental control strategies. A properly designed boiler considers every aspect of the fuel to optimize energy use, reduce emissions, and ensure safe, reliable operation. The key is not just burning fuel—but understanding how that fuel burns.
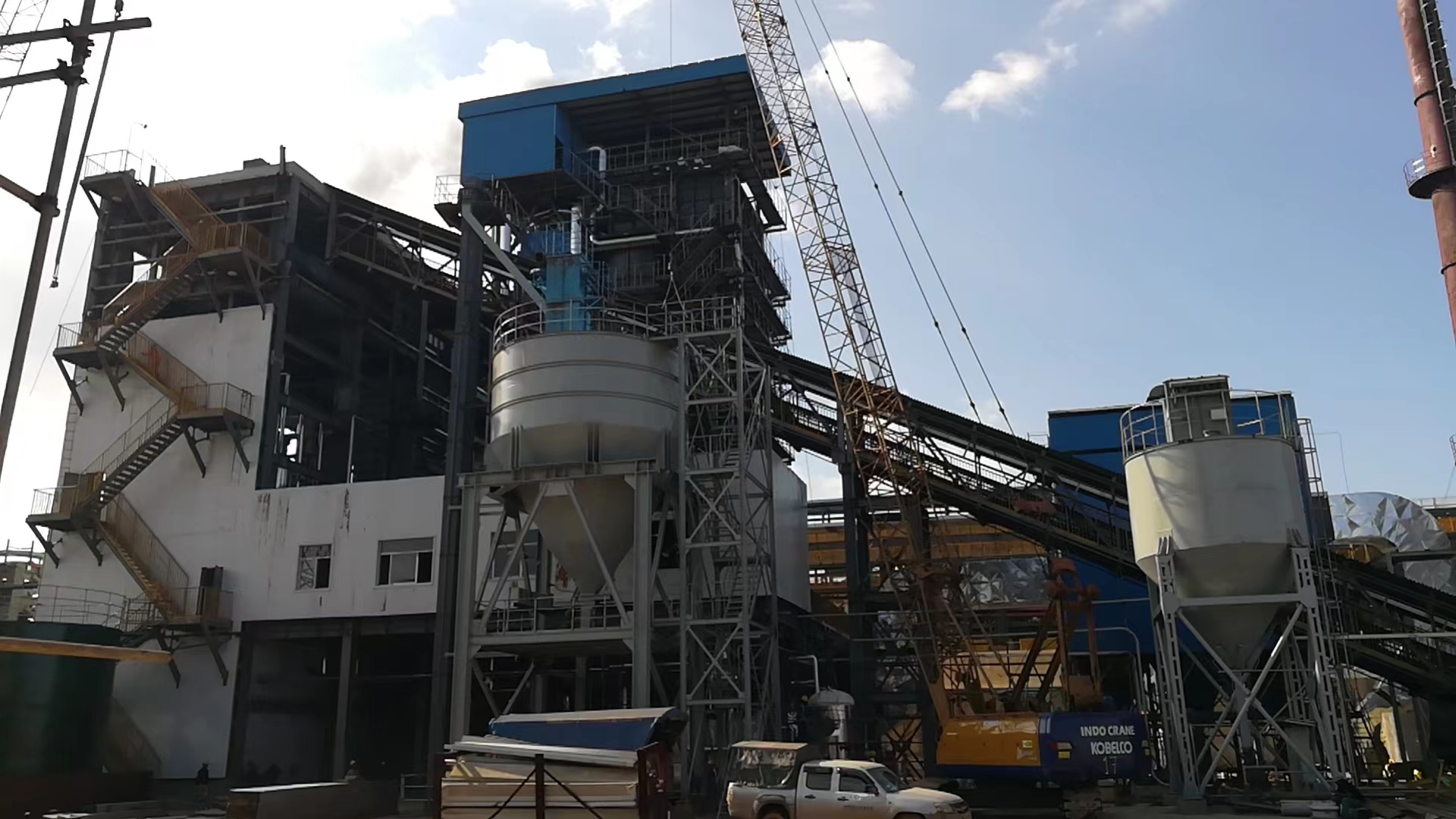
Why Does Moisture, Volatile Content, and Ash Level Matter in Combustion Performance?
Combustion performance in industrial steam boilers depends heavily on the chemical and physical characteristics of the fuel. Among the most critical of these characteristics are moisture content, volatile matter (VM), and ash level. These factors directly influence how well the fuel burns, how efficiently energy is released, and what kind of emissions and residues are produced. If they are not accounted for in boiler design or operation, the result is poor ignition, unstable flame, slag formation, high particulate emissions, or even boiler tube failures. Whether you’re using coal, biomass, or alternative fuels, understanding how these parameters behave during combustion is key to maximizing thermal efficiency, fuel economy, and environmental compliance.
Moisture, volatile content, and ash level matter in combustion performance because they determine how easily the fuel ignites, how consistently it burns, and how much energy is lost during combustion. High moisture reduces flame temperature and efficiency by consuming heat for evaporation. Volatile matter controls the ignition characteristics and flame stability—too low causes delayed combustion, too high can lead to incomplete burn. Ash content affects slagging, fouling, and heat transfer, and requires robust ash handling systems. Together, these factors define the combustion kinetics and boiler configuration needed for reliable performance.
No fuel burns in isolation—its moisture, volatiles, and residue determine the whole combustion process.
Moisture in solid fuel improves combustion by creating steam inside the furnace.False
Moisture in fuel absorbs heat during evaporation, which lowers the flame temperature and reduces combustion efficiency. It does not enhance combustion or generate usable steam.
1. Moisture Content: The Hidden Efficiency Killer
Why It Matters:
Moisture must be evaporated before combustion, consuming energy that could otherwise produce steam.
Every 1 kg of water requires ~2,260 kJ to evaporate.
Reduces flame temperature, slows ignition, and increases stack losses.
Fuel Type | Moisture Content (%) | Effect on Efficiency |
---|---|---|
Bituminous Coal | 5–12 | Moderate effect |
Biomass (Wood Chips) | 30–55 | Major efficiency loss |
Lignite | 40–60 | Very high energy penalty |
Combustion Impact:
Increases unburned carbon losses
Causes flame quenching
Requires larger furnace volume and hotter air
Design Response:
Pre-drying systems (mechanical or flue gas)
Preheated combustion air
Oversized combustion zones
2. Volatile Matter: The Flame Starter
What Is It?
Volatile matter (VM) includes gases (CO, H₂, CH₄) and tars released during initial heating of fuel.
Determines how easily fuel ignites and how the flame propagates.
Fuel Type | Volatile Matter (%) | Combustion Behavior |
---|---|---|
Anthracite | 2–8 | Hard to ignite, needs high temps |
Bituminous Coal | 12–40 | Balanced ignition and flame length |
Lignite / Biomass | 25–45 | Easy ignition, risk of unstable flame |
Combustion Impact:
Low VM = slow ignition, poor flame development
High VM = easy ignition, but risk of CO and unburned hydrocarbons if not properly mixed
Design Response:
Use burners with flame stabilization cones
Add secondary air staging
Use refractory-lined furnaces to retain heat
Fuels with high volatile matter require additional air staging to achieve complete combustion.True
High-VM fuels release a large amount of combustible gases early, requiring staged air injection to ensure full burnout and minimize CO emissions.
3. Ash Content: The Combustion Residue Challenge
Why It Matters:
Ash is the non-combustible residue left after burning fuel.
High ash causes:
Slagging (molten ash on furnace walls)
Fouling (ash deposits on heat exchangers)
Reduced heat transfer efficiency
Fuel Type | Ash Content (%) | Boiler Implications |
---|---|---|
Bituminous Coal | 10–20 | Manageable with standard ash systems |
Lignite | 20–40 | Needs continuous ash removal |
Biomass (Husk, Bark) | 4–25 | High silica → clinker formation |
Combustion Impact:
Narrows gas paths → increases pressure drop
Insulates heat surfaces → lowers efficiency
Deposits can block nozzles or damage tubes
Design Response:
Install soot blowers and ash conveyors
Use slag-tapping or fluidized bed systems
Select high ash fusion temperature refractory linings
Combined Effects on Boiler Performance
Parameter | Effect on Flame Stability | Effect on Efficiency | Effect on Maintenance |
---|---|---|---|
High Moisture | ↓ (quenching effect) | ↓ (latent heat loss) | ↑ (corrosion, wet ash) |
High Volatile Matter | ↑ (easy ignition) | ↑ (if air ratio optimized) | ↑ (if air staging is poor) |
High Ash | Neutral to ↓ (depends on type) | ↓ (heat transfer loss) | ↑↑ (slagging, fouling) |
Real-World Example: Cement Plant Biomass Retrofit
Fuel: Shifted from diesel to biomass (CV 13 MJ/kg, moisture 35%, ash 18%)
Issues:
Delayed ignition
Heavy ash accumulation
Frequent burner clogging
Upgrades:
Pre-drying conveyor
Multi-stage air distribution
High-temperature ash removal screw
Results:
Flame stabilization improved
Efficiency increased from 68% to 81%
Ash collection reduced unplanned shutdowns by 80%
Summary
Moisture content, volatile matter, and ash level are core fuel properties that dramatically affect the performance of any combustion system. High moisture steals energy from steam generation, volatile matter controls ignition and combustion speed, and ash complicates heat transfer and cleaning. Boiler systems must be carefully designed—or retrofitted—to account for these fuel-specific characteristics through furnace geometry, air staging, drying, and ash handling systems. Optimizing for these properties is the key to unlocking high-efficiency, low-emission combustion.
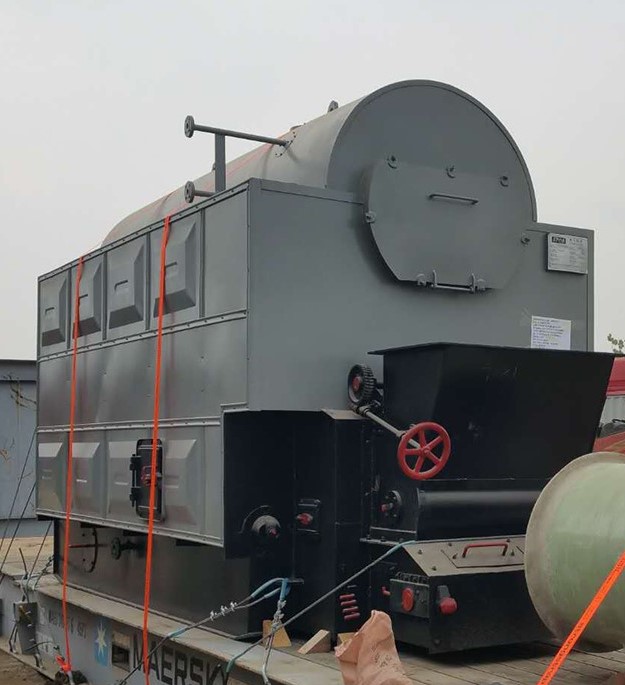
How Do Different Fuel Types Impact Burner Technology and Flame Stability?
In an industrial steam boiler, the burner is the heart of the combustion system—where fuel is introduced, mixed with air, ignited, and burned to release heat. However, not all fuels behave the same way. Natural gas ignites instantly and burns cleanly, while coal or biomass needs staged air, longer residence time, and robust flame stabilization. Using the wrong burner for a given fuel leads to flame instability, incomplete combustion, soot buildup, and even explosive conditions. Each fuel type has unique physical and chemical traits that require tailored burner technology to ensure stable, efficient, and safe flame performance.
Different fuel types impact burner technology and flame stability by influencing the fuel-air mixing process, ignition temperature, flame propagation speed, and combustion zone requirements. Gaseous fuels need precise mixing and flame control; liquid fuels require atomization; and solid fuels need staged combustion and residence time. Burner design—including nozzle type, swirl generation, air staging, and flame stabilization devices—must be customized to handle each fuel’s volatility, moisture, and combustion characteristics to maintain a steady and efficient flame.
Burners are not universal—they must be engineered around the fuel’s unique behavior for reliable performance.
A single burner design can efficiently and safely combust all fuel types without modification.False
Different fuels require different burner technologies due to their combustion rates, ignition temperatures, and physical forms. Using one burner for all fuels compromises flame stability, safety, and efficiency.
How Fuel Properties Influence Burner Requirements
Fuel Property | Burner Requirement |
---|---|
Phase (gas, liquid, solid) | Dictates mixing method (premix, atomization, mechanical feed) |
Volatile Matter | Affects flame speed and ignition zone |
Moisture Content | Determines preheat and flame temperature |
Ash Content | Impacts nozzle clogging and flame shape |
Calorific Value | Controls flame length and burner load |
Fuel-Specific Burner Technologies and Flame Behavior
1. Natural Gas Burners
Characteristics:
High CV (~50 MJ/kg)
No ash or moisture
Low ignition temperature (~650°C)
Burner Type:
Premix or diffusion-type burners
Modulating turndown (10:1 or better)
Low-NOx staging and swirlers
Advantages | Challenges |
---|---|
Very stable flame | Requires precise air-fuel control |
Fast startup/shutdown | Prone to flashback in poor mixing |
Flame Behavior: Short, intense blue flame with little radiant zone
2. Fuel Oil Burners (Diesel, HFO)
Characteristics:
High CV (42–44 MJ/kg)
Needs atomization into fine droplets
Burner Type:
Pressure atomizing or steam-assisted burners
Preheating system for heavy oils
Advantages | Challenges |
---|---|
High heat output | Sludge formation, coking risk |
Good for backup systems | Requires clean atomization nozzles |
Flame Behavior: Yellow-orange flame with long luminous region, moderate radiation
3. Coal Burners (Pulverized or Stoker)
Characteristics:
Medium to high CV (24–32 MJ/kg)
Requires air staging and longer burn time
Burner Type:
Pulverized coal burners with primary + secondary air
Rotating or swirl stabilizers
High-inertia flame design
Advantages | Challenges |
---|---|
Suitable for large loads | High slagging/fouling risk |
Long, radiant flame | Requires mill and feeder synchronization |
Flame Behavior: Long, radiant flame with progressive combustion of volatiles and char
4. Biomass Burners (Chips, Pellets, Husk)
Characteristics:
Low CV (8–18 MJ/kg)
High moisture (20–50%) and variable ash
Burner Type:
Moving grate, fluidized bed, or cyclonic chamber
Multi-stage air injection
Large combustion volume
Advantages | Challenges |
---|---|
Renewable, CO₂ neutral | Needs drying or air preheating |
Supports waste reduction | High particulate and clinker formation |
Flame Behavior: Broad flame with delayed ignition; needs longer residence time
5. Multi-Fuel Burners (Gas + Oil + Biomass)
Burner Features:
Dual-fuel nozzles or hybrid injectors
Separate control loops for each fuel
Automatic changeover between fuels
Use Case | Challenge |
---|---|
Plants with fuel flexibility | Complex controls and flame monitoring |
Flame Behavior: Depends on selected fuel; burner must adapt flame geometry accordingly
Dual-fuel burners allow rapid fuel switching while maintaining flame stability and performance.True
Properly designed dual-fuel burners use dedicated nozzles and control systems for each fuel, allowing stable combustion and seamless transitions.
Flame Stability Factors by Fuel Type
Fuel | Stabilization Method | Risk of Instability |
---|---|---|
Natural Gas | Swirlers, flame retention rings | Low (with good controls) |
Oil | Proper droplet sizing, stable atomization | Moderate (poor atomization = flash) |
Coal | Residence time, swirl flame cone | High (char burnout delay) |
Biomass | Hot refractory walls, staged air | High (due to moisture, VM) |
Waste Fuels | Custom burner throat, fluidized design | Very high (variable CV) |
Real-World Case: Burner Retrofit for Fuel Change
Old Burner: Heavy oil burner (pressure atomizing)
New Fuel: Biogas (CV = 22 MJ/kg)
Issues:
Flame instability
Incomplete combustion
Burner tripping
Solution:
Installed gas-specific burner with swirl control
Tuned air/fuel ratio via oxygen trim
Added flame scanner with high-speed response
Result:
Stable flame within 20 seconds
NOx reduced by 35%
95% combustion efficiency with biogas
Summary
Fuel type is the single most influential factor in determining burner design and flame behavior. Gaseous fuels need precise premix or diffusion burners; oils require atomization; solid fuels like coal and biomass demand robust residence time and air staging. Using the wrong burner leads to flame instability, excess emissions, and safety risks. The key to safe, efficient combustion lies in selecting burner technology that matches the specific combustion kinetics and thermal behavior of the fuel in use. For industrial boiler operators, this means thinking of the burner and fuel as a matched system, not standalone components.
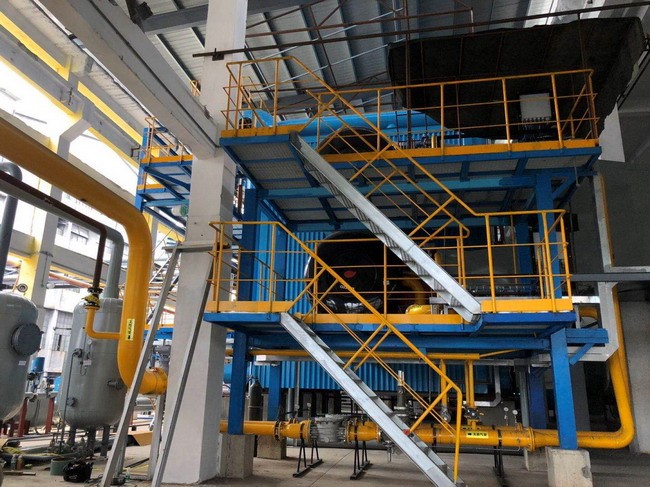
What Emissions Considerations Are Associated with Each Fuel Type?
In industrial steam boiler systems, fuel combustion releases various air pollutants—including carbon dioxide (CO₂), sulfur oxides (SOx), nitrogen oxides (NOx), particulate matter (PM), and carbon monoxide (CO). The type and concentration of these emissions are directly influenced by the chemical composition of the fuel used. Some fuels like natural gas burn cleanly, while others like coal and biomass produce high particulate or sulfur emissions. Regulatory compliance, environmental impact, and operational cost are all tied to the fuel’s emission profile, making it critical to select the right fuel-emission-control combination in boiler system design.
Each fuel type used in industrial boilers produces a unique emissions profile based on its carbon, sulfur, nitrogen, and ash content. Natural gas emits low SOx and PM but produces CO₂ and some NOx. Coal has high SOx, NOx, CO₂, and PM emissions. Biomass is renewable and carbon-neutral but emits particulates and sometimes CO and NOx. Fuel oil produces moderate SOx and NOx and low PM if cleanly burned. Each fuel requires specific flue gas treatment technologies—such as scrubbers, filters, and low-NOx burners—to meet emission standards.
Choosing the right fuel isn’t just about cost and heat output—it’s about regulatory readiness and environmental responsibility.
Natural gas combustion produces no significant air pollutants.False
While natural gas burns cleaner than most fuels, it still produces CO₂, NOx, and small amounts of CO, and may require controls to meet air quality standards.
Emissions Summary by Fuel Type
Fuel Type | CO₂ | SOx | NOx | PM | CO | Other |
---|---|---|---|---|---|---|
Natural Gas | Medium | Low | Medium | Very Low | Low | CH₄ leaks (fugitive) |
Fuel Oil (Diesel, HFO) | High | Medium–High | Medium–High | Low | Low | Black carbon |
Bituminous Coal | Very High | High | High | High | Medium | Heavy metals, Hg |
Lignite | High | High | Medium | Very High | High | Clinker-forming ash |
Biomass (Wood Chips) | Neutral (net zero) | Very Low | Medium | High | Medium | Alkali vapors |
Biomass (Pellets) | Neutral | Very Low | Low–Medium | Medium | Low–Medium | NH₃ slip (if denoxed) |
Industrial Waste Fuels | Variable | High | High | Very High | High | Dioxins, heavy metals |
“Neutral” CO₂ means biogenic emissions that are offset by fuel regrowth or recycling under carbon accounting rules.
Key Pollutants Explained
✅ Carbon Dioxide (CO₂)
Proportional to carbon content in fuel
Highest in coal and oil
Biogenic (from biomass) not counted under many carbon credit systems
✅ Sulfur Oxides (SOx)
Comes from sulfur in fuel (especially coal and heavy oils)
Causes acid rain, corrosion, and health impacts
Control:
Wet or dry FGD (Flue Gas Desulfurization)
Limestone injection
SOx emissions are highest in fuels with high sulfur content, like coal and heavy oils.True
Sulfur content in these fuels converts to SO₂ during combustion, which must be removed via flue gas scrubbing to prevent air pollution.
✅ Nitrogen Oxides (NOx)
Formed from fuel-bound nitrogen and high flame temperatures
Contributes to smog and respiratory illness
Control:
Low-NOx burners
Flue Gas Recirculation (FGR)
Selective Non-Catalytic Reduction (SNCR)
Selective Catalytic Reduction (SCR)
✅ Particulate Matter (PM10/PM2.5)
From ash, soot, and incomplete combustion
Severe in solid fuels like coal and biomass
Control:
Bag filters (fabric filters)
Cyclones
Electrostatic Precipitators (ESPs)
✅ Carbon Monoxide (CO)
Indicates incomplete combustion
Often occurs with poor mixing or high moisture
Control:
Proper air-fuel ratio
Flame stabilization
Refractory or staged combustion
Emission Control Requirements by Fuel Type
Fuel | Emission Control Technologies Needed |
---|---|
Natural Gas | Low-NOx burners, FGR, O₂ trim |
Fuel Oil | Scrubber (for SOx), low-NOx burner, occasional ESP |
Bituminous Coal | ESP + FGD + SNCR/SCR + bottom ash removal |
Biomass | Cyclone + bag filter + staged combustion |
Lignite | ESP + ash extractor + overfire air + limestone injection |
Waste Fuels | ESP + activated carbon + SCR + rotary kiln temp control |
Real-World Comparison: Boiler Emissions with Different Fuels
Boiler Output: 20 TPH | Natural Gas | Coal | Biomass |
---|---|---|---|
CO₂ (kg/h) | ~3,600 | ~6,800 | ~Neutral |
SO₂ (mg/Nm³) | <100 | >2,500 | <100 |
NOx (mg/Nm³) | 200–350 | 400–800 | 300–600 |
PM (mg/Nm³) | <10 | 150–300 | 200–400 |
CO (mg/Nm³) | <50 | 100–300 | 200–500 |
Compliance and Regulation Considerations
Jurisdiction | Key Limits (Large Boiler) |
---|---|
EU (IED Directive) | NOx < 150 mg/Nm³, SOx < 200, PM < 20 |
US (EPA MACT standards) | Varies by fuel; coal NOx < 130–210 mg/Nm³ |
India (CPCB) | NOx < 300, SOx < 600 (with scrubbers) |
China (GB13223-2011) | NOx < 100, SOx < 200, PM < 30 |
Design Tip: Always assess fuel-switching impact on emissions permits, especially when changing from gas to biomass or coal.
Case Study: Switching from Fuel Oil to Biomass
Old System: 15 TPH oil-fired boiler (SO₂ = 1,800 mg/Nm³)
New Fuel: Rice husk biomass
Retrofit Actions:
Installed cyclone and bag filter
Replaced burners with air-staged combustion
Monitored ash composition (high silica)
Results:
SO₂ reduced to <100 mg/Nm³
PM within limits after filtering
CO emissions fluctuated, corrected via real-time O₂ trim
Summary
Each industrial fuel type comes with its own emissions fingerprint, which must be managed through proper burner design, combustion control, and flue gas treatment systems. Natural gas offers low-emission, high-efficiency combustion, while coal and waste fuels require extensive filtration and scrubbing. Biomass is renewable but can pose challenges with particulate matter and volatile emissions. Understanding the emission risks of your fuel is essential not only for boiler performance, but also for environmental compliance, safety, and long-term sustainability.
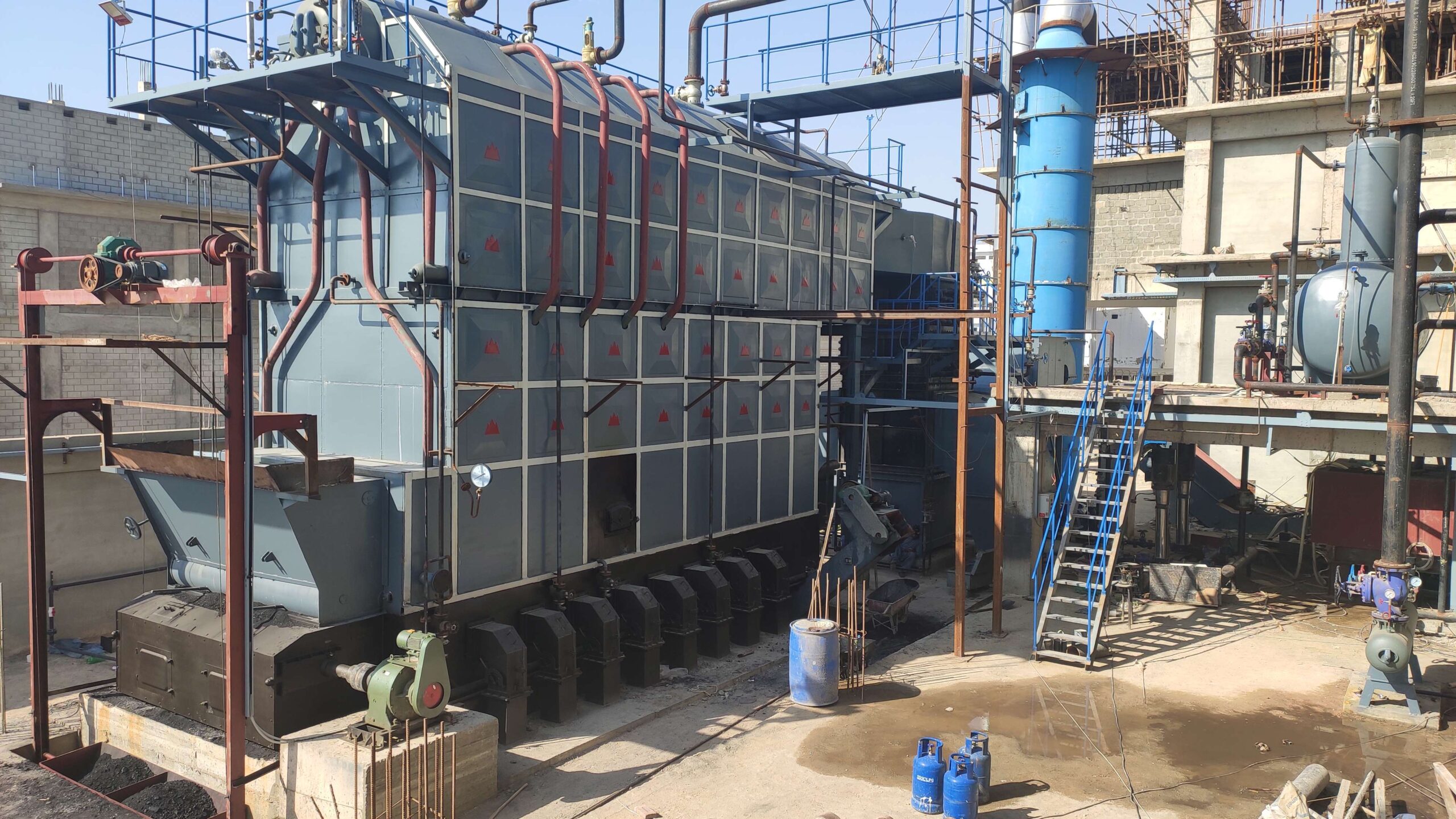
How Do Boiler Systems Adapt to Multi-Fuel or Low-Grade Fuel Operations?
Industrial operators are increasingly turning to multi-fuel and low-grade fuel strategies to reduce energy costs, improve supply security, and transition to renewable or circular energy sources. However, these fuels—ranging from wet biomass and sub-bituminous coal to waste residues—pose serious challenges: inconsistent calorific value, high moisture, unpredictable ash, and variable combustion behavior. If the boiler system isn’t designed or adapted to handle these inconsistencies, problems like poor flame stability, slagging, and high emissions will result. That’s why advanced boiler systems today must be flexible, fuel-tolerant, and smartly engineered to manage the complexity of multi-fuel and low-grade fuel operation.
Boiler systems adapt to multi-fuel or low-grade fuel operations through design enhancements such as enlarged furnaces, fluidized bed combustion (FBC) technology, staged air injection, adaptive feed systems, real-time control algorithms, and robust ash and moisture handling. These adaptations allow the boiler to efficiently burn fuels with widely different combustion characteristics, calorific values, and impurities. Success depends on precise fuel-air control, flexible burners or grates, and integrated fuel blending, drying, and monitoring systems.
The goal is not just to burn more types of fuel—but to do it efficiently, safely, and cleanly.
Standard industrial boilers can operate on any low-grade or mixed fuel without modifications.False
Low-grade and mixed fuels require specific design features—such as larger combustion chambers, air staging, and adaptive controls—to maintain combustion efficiency and avoid damage.
Typical Challenges of Multi-Fuel and Low-Grade Fuels
Fuel Characteristic | Common Examples | Impact on Combustion |
---|---|---|
Low Calorific Value (CV) | Lignite, wet biomass | Requires higher fuel input, larger furnace |
High Moisture Content | Wood chips, sludge | Reduces flame temp, increases flue gas volume |
High Ash Content | Rice husk, low-rank coal | Causes slagging, fouling, increases maintenance |
Variable Composition | Waste fuels, RDF | Unstable combustion, uneven heat release |
High Volatile Matter | Biomass, peat | Risk of flashback, requires flame stabilization |
Core Boiler Adaptations for Multi-Fuel Operation
🔥 1. Fluidized Bed Combustion (FBC/CFB)
Feature | Why It Works |
---|---|
Combustion bed suspended by air | Supports a wide range of fuel sizes and properties |
Low temperature (800–900°C) | Reduces slagging and NOx |
In-bed limestone injection | Captures SO₂ from high-sulfur fuels |
Ideal for: Biomass + coal blends, waste fuels, RDF, wet agro residues
🔥 2. Flexible Grate or Feed System
Moving grates handle coarse and variable fuels
Screw feeders control fuel rate and prevent choking
Dual/triple fuel hoppers allow automatic switching or blending
Fluidized bed combustion is well-suited for burning fuels with low calorific value and high ash content.True
FBC systems provide even combustion and robust ash handling, making them ideal for inconsistent and ash-heavy fuels.
Air and Combustion Control Adaptations
System Component | Adaptation for Multi-Fuel Use |
---|---|
Primary Air | Adjustable flow for coarse or wet fuel ignition |
Secondary/Tertiary Air | Injected above bed for volatile matter burn-out |
O₂/CO Sensors | Real-time monitoring of combustion stability |
Variable Frequency Drives | Control air and fuel delivery based on real-time load |
PLC/SCADA Systems | Automated fuel changeover and alarm triggers |
Ash, Slag, and Moisture Management
Ash Handling:
Solution | Why It Matters |
---|---|
Wet/dry ash conveyors | Handle large ash volumes from husk, coal, etc. |
Slag crushers | Break hard fused ash chunks |
Ash fusion temperature control | Prevents slag buildup through additives (dolomite, kaolin) |
Moisture Adaptation:
Install pre-drying units (waste heat-based)
Preheat combustion air to maintain flame stability
Use thermal buffering to handle CV fluctuations
Real-World Configuration Example
Plant Type | Boiler Rating | Fuel Mix | Adaptations |
---|---|---|---|
Paper Mill | 25 TPH | 60% coal + 30% biomass + 10% sludge | CFB boiler, fuel blending unit, bag filter |
Agro-Waste CHP Plant | 15 TPH | 80% rice husk + 20% wood chips | Step grate, cyclone, preheated air, O₂ sensor |
Textile Factory | 10 TPH | Dual-fuel: biomass and fuel oil backup | Dual burners, fuel switching panel, PLC BMS |
Monitoring and Control Systems
System | Functionality for Multi-Fuel |
---|---|
Combustion Optimization | Adjusts air/fuel ratio based on O₂, CO, CV |
Fuel CV Estimation System | Infrared or density-based CV tracking |
Alarm & Interlock System | Prevents ignition during poor fuel-air mix |
Auto Fuel Changeover | Seamless transition between fuels without flameout |
Performance and Efficiency Tips
Keep fuel blend homogeneous—segregate wet and dry streams
Pre-test ash melting point for fuel mixes—avoid slagging surprises
Consider modular boiler design for staged loading and fuel flexibility
Maintain constant excess air tuning to adapt to CV shifts
Use flue gas recirculation to manage flame temperature and emissions
Summary
Adapting boiler systems for multi-fuel or low-grade fuel use demands a complete approach—from combustion chamber geometry to air delivery, ash handling, and control logic. Technologies like fluidized bed combustion, staged air injection, and automated feed systems make it possible to burn a broad spectrum of fuels without sacrificing performance or compliance. Whether you’re blending biomass with coal, using sludge from your own process, or incorporating RDF, modern boiler engineering allows your system to remain fuel-flexible, cost-effective, and sustainable.
🔍 Conclusion
The type of fuel you intend to use isn’t just a supply choice—it’s a fundamental design driver for your industrial steam boiler. Fuel characteristics directly impact combustion efficiency, emissions, maintenance requirements, and cost-effectiveness. By carefully evaluating your fuel properties and matching them with the right boiler configuration, you’ll achieve optimal performance, minimize emissions, and ensure long-term system reliability.
📞 Contact Us
💡 Not sure which boiler fits your fuel type best? Our engineers provide custom fuel analysis, boiler selection, and combustion system design tailored to your specific industrial needs.
🔹 Let us help you build a fuel-smart steam boiler system designed for performance and compliance! 🔥♻️✅
FAQ
How do different fuel types affect industrial steam boiler selection?
The fuel type—coal, oil, gas, biomass, or electricity—determines the boiler’s combustion system, burner configuration, fuel handling equipment, and emission controls. Each fuel has unique energy content, combustion temperature, and pollution potential, which impact boiler design and efficiency.
What are key combustion characteristics that influence boiler performance?
Important combustion traits include ignition temperature, flame speed, calorific value, moisture content, ash production, and emissions profile. Fuels with higher volatility or energy content typically offer more efficient combustion, while those with high ash or moisture require special handling.
Why is matching burner type to fuel important?
Each burner is engineered to handle a specific fuel’s pressure, flow rate, and combustion behavior. Using the wrong burner can result in incomplete combustion, soot buildup, reduced efficiency, and safety hazards.
How do combustion characteristics affect emission control?
Fuels high in sulfur, nitrogen, or ash produce more SOx, NOx, and particulate emissions. Boilers using such fuels need advanced emission control systems like scrubbers, electrostatic precipitators, or low-NOx burners to meet environmental regulations.
Can industrial steam boilers be designed for multiple fuel types?
Yes, many modern boilers support dual-fuel or multi-fuel capabilities, allowing operators to switch between fuels like gas and oil or biomass and coal, optimizing cost, supply reliability, and emissions compliance.
References
Boiler Fuel Type Comparison – https://www.energy.gov
Combustion Principles in Steam Boilers – https://www.sciencedirect.com
Emission Characteristics by Fuel Type – https://www.epa.gov
Industrial Steam Boiler Burner Selection – https://www.researchgate.net
Fuel Flexibility in Boiler Design – https://www.bioenergyconsult.com
Optimizing Combustion Efficiency – https://www.mdpi.com
Boiler Selection Based on Fuel Type – https://www.energysavingtrust.org.uk
Industrial Boiler Technologies – https://www.iea.org
Dual-Fuel and Hybrid Boiler Systems – https://www.automation.com
Fuel Handling and Preparation in Boilers – https://www.sciencedirect.com
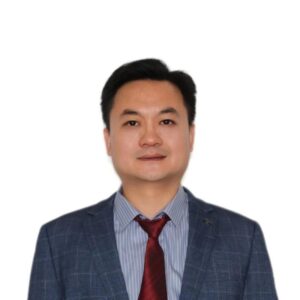