Waste Heat Recovery Boiler
Waste heat boilers refer to boilers that utilize the waste heat generated during industrial production processes to produce steam or hot water. They are primarily used to cool high-temperature process gases and control the temperature of industrial process gases while simultaneously recovering the waste heat generated during the production process. They are widely applied in the waste heat recovery processes of industries such as petrochemical production, metallurgy, machinery, papermaking, building materials, etc.

Types
Unsure how to choose a Waste Heat Recovery Boiler?
Contact us for complimentary boiler selection guidance, cost estimations, and expert technical advice for your project.
Featured
Heat Recovery Design
The primary feature of WHRBs is their ability to recover waste heat from various processes. This is facilitated through specialized designs, such as water-tube or fire-tube configurations, which are tailored to maximize heat transfer from the waste heat source to the water or steam within the boiler.
Customization and Flexibility
Given the variety of industrial processes that produce waste heat, WHRBs are often custom-designed to fit specific operational needs and physical constraints. This includes adaptability to varying temperatures, flow rates, and chemical compositions of exhaust gases.
Robust Construction
Due to the harsh operating environments, especially when dealing with corrosive or varying temperatures of exhaust gases, WHRBs are built with robust materials that can withstand these conditions, ensuring longevity and reduced maintenance costs.
Integrated Control Systems
Advanced control systems are integrated into modern WHRBs to optimize their operation, ensure safety, and provide real-time monitoring and adjustments based on the process needs.
Multi-pressure Levels
In applications like combined cycles or in industries requiring varied pressure levels, WHRBs can be designed with multi-pressure levels to enhance the system’s thermodynamic efficiency.
Energy Efficiency
WHRBs are designed to be highly efficient, capitalizing on otherwise wasted heat to produce steam or hot water. This significantly enhances the overall energy efficiency of the facility by reducing the need for additional fuel consumption.
Cost-Effectiveness
Although the initial investment for a WHRB can be significant, the long-term savings on fuel costs and the potential for government incentives related to energy efficiency projects make these boilers a cost-effective solution.
High-Temperature Operation
WHRBs are capable of handling high inlet temperature gases, which is a common feature in many industrial processes. This is a critical design aspect that ensures the durability and effectiveness of the boiler.
Environmental Benefits
By reducing the need to burn additional fuel to generate heat, WHRBs help decrease the emission of pollutants and greenhouse gases. This supports compliance with environmental regulations and aids in achieving sustainability goals.
Reduced Water Usage
Many WHRBs are designed to minimize water usage, which is particularly beneficial in areas where water conservation is crucial or where water treatment costs are high.
Why Choose Taishan Group ?
Leading coal, biomass and waste to energy solution provider.
- Covering Entire Project Lifecycle A-Z Service.
- Ranked top in China's industrial boiler industry for 10 consecutive years.
- Access cutting-edge, eco-friendly energy solutions.
- Benefit from over 70 years of technical expertise.
- Align with global sustainability initiatives.
- China largest-capacity biomass power generation boiler.
- Experience reliable, efficient equipment for green development.
378000+
Workshop m²
5000+
Trained Staff
1978
History Since
Project Case
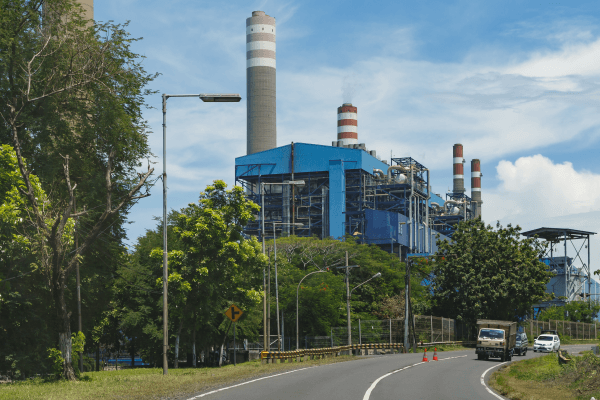
- Parnaíba Complex
- Brazil, Parnaíba
Provide 1 high-pressure drum and 1 low-pressure drum for a 70-ton waste heat boiler for Parnaíba Complex in Brazil. Parnaíba Complex is one of the largest thermal parks for natural gas energy production in Brazil.
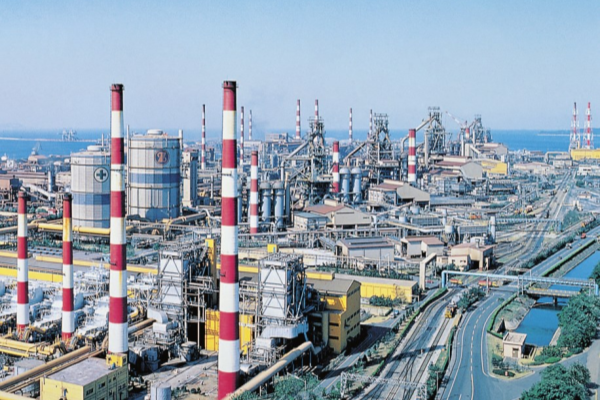
- Posco Steeleon
- Korea
Provide steam drum for their 18t/h waste heat boiler to Korea Posco Steeleon. Posco is a company manufacturing coated steel products.
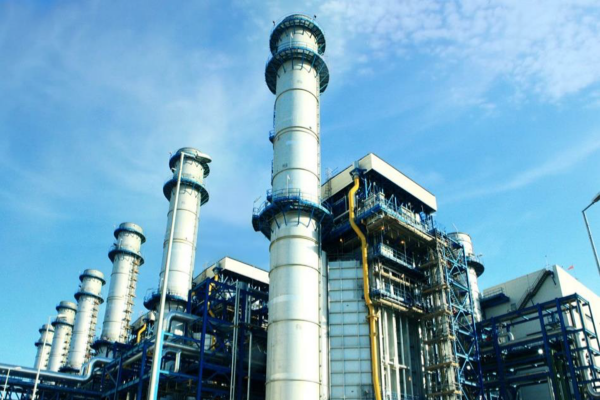
- Hyundai Steel
- Korea
Provide steam drum for their 26t/h waste heat boiler to Korea Hyundai Steel. Hyundai Steel is Korea's first steelmaker.
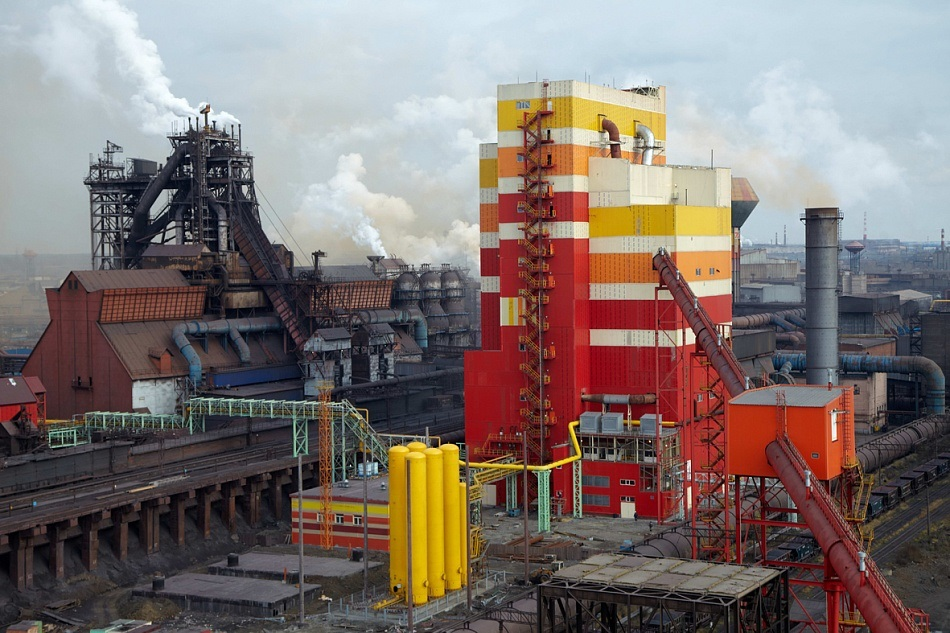
- EVRAZ plc
- Russian
Provides sets 12t/h waste heat recovery boilers to EVRAZ plc. EVRAZ plc is a UK-incorporated multinational steel manufacturing and mining company part-owned by Russian oligarchs.
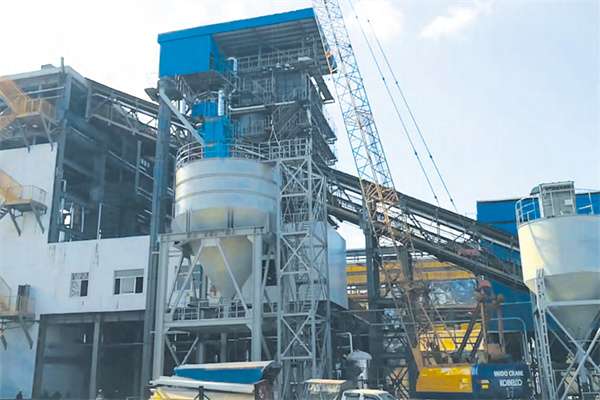
- Aksu Sunshine Thermal Company
- China
2 sets 116MW Coal CFB hot water boilers for Aksu Sunshine Thermal Company heating projects
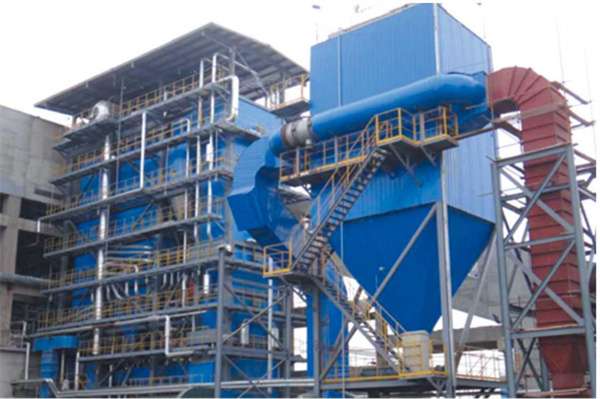
- Jinyu Tyre
- Vietnam
2*20 tons fluidized bed boiler in Jinyu Tyre Vietnam EPC project
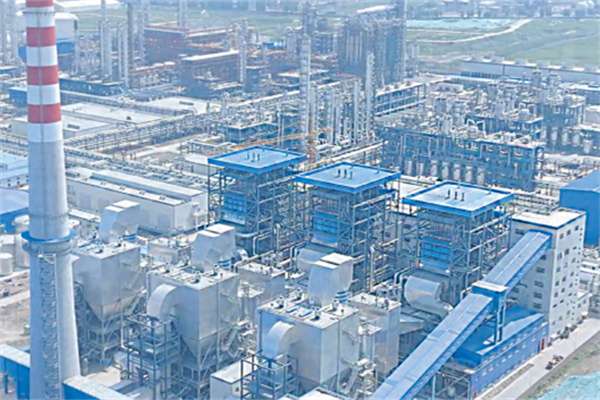
- PT QMB NEW ENERGY MATERIALSPt
- Indonesia
75t/h Coal CFB Boiler for Indonesia PT QMB NEW ENERGY MATERIALSPt Laterite Nickel Ore Smelting Project
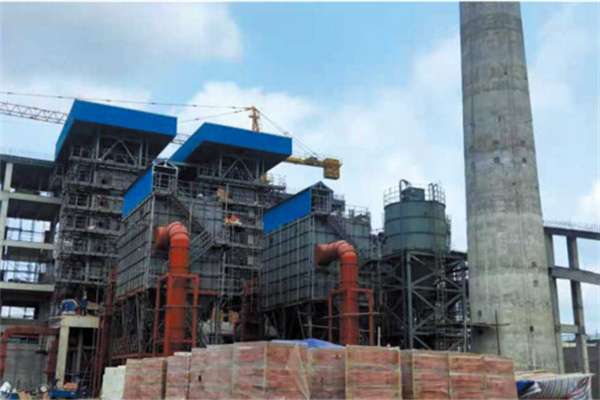
- Advance Tyre
- Vietnam
2*20 tons fluidized bed boiler in Vietnam Advance Tyre EPC project
FAQ
Frequently Asked Questions about Waste Heat Recovery Boiler.
A waste heat recovery boiler (WHRB) is a device that captures heat energy that would otherwise be wasted in industrial processes. This captured heat is then used to generate steam or hot water which can be used for a variety of purposes, such as heating buildings, generating electricity, or driving other industrial processes.
Waste Heat Recovery Boilers (WHRBs) offer several significant advantages, particularly in terms of energy efficiency, cost savings, and environmental benefits. Here are some of the key advantages:
1. Energy Efficiency Improvement: WHRBs capture and reuse heat that would otherwise be wasted, thereby reducing the energy required to produce steam or hot water from scratch. This enhances the overall energy efficiency of the facility.
2. Cost Reduction: By generating steam or hot water that can be used in various industrial processes or for power generation, WHRBs reduce the need for additional fuel, leading to substantial cost savings on energy bills.
3. Reduced Environmental Impact: Reusing waste heat helps in lowering greenhouse gas emissions and other pollutants, since less fuel combustion is required. This contributes significantly to an organization’s efforts to meet environmental regulations and sustainability goals.
4. Increased System Efficiency: Integrating a WHRB can increase the efficiency of the primary equipment by cooling the exhaust gases. This can extend the life of equipment by reducing the thermal stress and maintenance requirements.
5. Flexibility and Versatility: WHRB systems can be designed to work with a variety of heat sources and can be customized to meet the specific needs of different industries, making them a versatile solution across multiple sectors.
6. Economic Payback: While the initial investment for a WHRB system can be significant, the economic payback through reduced energy costs can be quite favorable, often within a few years, depending on the specific application and operational efficiency.
7. Enhancement of Energy Security: By reducing dependence on external energy sources and maximizing on-site energy generation, WHRBs enhance energy security for industrial operations.
These benefits make WHRBs an appealing option for industries looking to improve their operational efficiencies and environmental impact while reducing operational costs.
While Waste Heat Recovery Boilers (WHRBs) offer numerous benefits, they also have some disadvantages and limitations that may affect their implementation and effectiveness in certain situations. Here are some of the key drawbacks:
1. High Initial Investment: The upfront cost of installing a WHRB can be significant, including the cost of the boiler itself, additional infrastructure, and integration into existing systems. This initial investment can be a barrier for some organizations, especially small to medium enterprises.
2. Maintenance Requirements: WHRBs require regular maintenance to operate efficiently and safely. This includes cleaning, inspection, and repair of heat exchanger surfaces and other components, which can add to operational costs.
3. Complexity of Design and Integration: Designing and integrating a WHRB into existing industrial processes can be complex. It requires careful planning to ensure compatibility with existing equipment and processes, and may sometimes require modifications to existing systems.
4. Dependence on Waste Heat Availability: The effectiveness of a WHRB is directly dependent on the availability and temperature of waste heat. In processes where waste heat is intermittent or at a low temperature, the effectiveness and efficiency of the WHRB can be significantly reduced.
5. Space Requirements: Installing a WHRB often requires additional space, which might be a constraint in facilities with limited physical area.
6. **Economic Viability Dependent on Fuel Costs**: The economic return of a WHRB project is often linked to fuel costs. In scenarios where fuel costs are low, the payback period for the initial investment might extend, reducing the economic attractiveness of such projects.
7. Potential for Increased Operating Costs: If not properly designed or maintained, WHRBs can introduce inefficiencies into the system, potentially increasing rather than decreasing operating costs.
8. Risk of Corrosion and Scaling: The boiler tubes and other components in a WHRB are susceptible to corrosion and scaling from the waste gases and fluids, which can impair heat transfer efficiency and lead to failures or leaks.
Despite these challenges, many industries find that the long-term benefits of WHRBs, such as reduced energy costs and environmental impact, outweigh the disadvantages, particularly in sectors with high energy consumption and suitable waste heat sources.
A waste heat recovery boiler (WHRB) works by capturing heat energy that would normally be lost in exhaust gases from industrial processes and using it to generate steam or hot water. Here’s a breakdown of the process:
Hot Exhaust Stream: The process starts with hot exhaust gases being emitted from an industrial source like a furnace, engine, or incinerator. These gases can reach temperatures in the hundreds or even thousands of degrees Celsius.
Heat Transfer via Tubes: The hot exhaust gases are then channeled into the WHRB system, where they flow through a series of tubes made of a heat-resistant material.
Heat Absorption by Working Fluid: Surrounding these tubes is a working fluid, typically water. The water circulates around the tubes, absorbing heat from the hot exhaust gases by conduction through the metal tubes.
Steam Generation or Hot Water Use: The heated water from step 3 can be used in two ways:
- Steam Generation: If steam is required, the hot water is further heated in a chamber within the WHRB until it boils and turns into steam. This steam can then be used for various purposes like power generation, heating buildings, or industrial processes.
- Direct Hot Water Use: Alternatively, if hot water is sufficient for the application, the heated water from step 3 can be used directly without converting it to steam. This hot water can be used for tasks like space heating, cleaning, or specific industrial processes requiring hot water.
Cooled Exhaust: After transferring heat to the working fluid, the exhaust gases are significantly cooler. These cooled exhaust gases are then released from the WHRB system through a stack and vented out to the atmosphere.
By capturing this waste heat, WHRBs significantly improve the overall efficiency of industrial operations. Imagine all that thermal energy just going up the smokestack – a WHRB captures it and puts it to good use!
Common types of waste heat recovery boilers mainly include the following:
1. Based on Installation Type: These are classified into horizontal and vertical waste heat boilers. Horizontal boilers are characterized by their simple structure and ease of maintenance, but they have a small evaporation capacity, low steam pressure, and slow water circulation, typically used for small and medium-sized waste heat boilers. Vertical boilers have fast water circulation speeds and high heat transfer rates, featuring large steam spaces and high evaporation capacities, mainly used for large-scale waste heat boilers that recover substantial amounts of heat and operate at high steam pressures.
2. Based on the Characteristics of the Steam-Water Circulation System: There are natural circulation waste heat boilers and forced circulation waste heat boilers. Natural circulation waste heat boilers do not require a circulation pump, relying on the driving force generated by the density difference between the downcomers and risers to achieve steam-water circulation, which is relatively reliable. Forced circulation waste heat boilers use an external circulation pump to drive the steam-water circulation, consuming energy when the boiler operates.
3. Based on Structural Features: There are shell and tube waste heat boilers and flue-type waste heat boilers. Shell and tube waste heat boilers use wall heat exchange between high-temperature process gases and the water inside the boiler to produce steam, similar to shell and tube heat exchangers, and are widely used. Flue-type waste heat boilers use high-temperature industrial gases passing through flues made of non-metallic materials, heat exchange tube bundles set in the flues, and water walls to produce steam, recovering heat from high-temperature process gases, similar to the flue structures of conventional boilers.
4. Based on Boiler Pressure: There are low-pressure, medium-pressure, and high-pressure waste heat boilers.
– Low-pressure waste heat boilers: 0.1MPa ≤ p < 1.6MPa
– Medium-pressure waste heat boilers: 1.6MPa ≤ p < 10.0MPa
– High-pressure waste heat boilers: 10.0MPa ≤ p < 100MPa
5. Based on Industry Use: These include cement kiln waste heat boilers, sintering machine waste heat boilers, catalytic cracking waste heat boilers, chemical waste waste heat boilers, waste incineration waste heat boilers, ferrosilicon industry waste heat boilers, titanium dioxide industry waste heat boilers, sulfuric acid waste heat boilers, turbine waste heat boilers, coke dry quenching waste heat boilers, and others.
Waste heat recovery boilers (WHRBs) are a versatile technology used across various industries due to their ability to capture wasted thermal energy and convert it into usable steam or hot water. Here are some of the most common industrial applications of WHRBs:
Power Generation: In co-generation plants, WHRBs capture waste heat from engines or turbines to generate steam. This steam then drives turbines for electricity production, promoting efficient combined heat and power (CHP) systems.
Steel Mills: The steel production process generates a significant amount of high-temperature exhaust gas. WHRBs in steel mills recover this heat to create steam for various purposes within the plant, such as powering processes, heating buildings, or even generating electricity on-site.
Cement Plants: Similar to steel mills, cement production involves high-temperature processes that release substantial waste heat. WHRBs in cement plants capture this heat to generate steam for powering kilns or drying processes.
Chemical Plants: Chemical reactions often generate considerable heat. WHRBs in chemical plants capture this waste heat to produce steam or hot water for distillation, concentration, or other processes requiring thermal energy.
Refineries: Oil refineries involve numerous high-temperature processes. WHRBs can recover waste heat from these processes to generate steam for powering distillation units, crackers, or other refinery operations.
Glass Manufacturing: Glass production utilizes high-temperature furnaces. WHRBs capture waste heat from these furnaces to generate steam or hot water for preheating raw materials or other glass manufacturing processes.
Food Processing: Some food processing applications, like drying or sterilization, require hot water or steam. WHRBs can capture waste heat from boilers or ovens used in food processing to generate hot water or steam, reducing reliance on primary fuel sources.
Paper and Pulp Mills: Paper and pulp production involves processes like drying and pulping that require thermal energy. WHRBs can capture waste heat from various stages of the process to generate steam or hot water for these applications.
Textile Industry: Textile manufacturing often utilizes heat for drying fabrics or setting dyes. WHRBs can capture waste heat from boilers or other processes to generate hot water for these applications.
Overall, WHRBs offer a cost-effective and environmentally friendly solution for various industries by harnessing what would otherwise be wasted thermal energy. Their widespread use across these sectors highlights their potential for improving industrial efficiency and sustainability.
Selecting the right waste heat recovery boiler (WHRB) requires careful consideration of several factors to ensure it aligns with your specific needs and offers optimal performance. Here’s a breakdown of the key steps involved in choosing a WHRB:
Evaluate Heat Source:
- Temperature: Analyze the temperature of your exhaust gas stream. This is crucial as WHRB effectiveness is highly dependent on the available waste heat temperature. Higher temperatures generally translate to more recoverable heat and potentially higher boiler efficiency.
- Flow Rate: Assess the volume or flow rate of the exhaust gases. A WHRB needs to be sized appropriately to handle the expected exhaust gas volume for optimal heat transfer.
- Composition: Identify any contaminants or corrosive elements present in the exhaust stream. The WHRB material selection and design may need to consider corrosion resistance to ensure durability.
Determine Steam or Hot Water Needs:
- Application: Clearly define whether you require steam or hot water from the WHRB. This will influence the selection of boiler type (steam generating or hot water) and the required output temperature and pressure.
- Consumption: Estimate the amount of steam or hot water your facility needs. Sizing the WHRB to meet your consumption demands is essential for efficient operation and avoiding unnecessary capacity.
Economic Analysis:
- Investment Cost: Consider the initial investment cost of the WHRB system, including equipment, design, and installation.
- Operational Costs: Factor in ongoing operational costs like maintenance, fuel savings due to waste heat utilization, and potential water treatment needs.
- Payback Period: Estimate the time it takes for the cost savings from the WHRB to offset the initial investment. A shorter payback period indicates a more financially attractive proposition.
Space Constraints:
- Boiler Footprint: Evaluate the available space at your facility to accommodate the WHRB system. Recuperative boilers tend to be more compact, while regenerative boilers may require more space due to their valve systems and chambers.
Expertise and Maintenance:
- Technical Support: Consider the availability of qualified personnel to operate and maintain the WHRB system. Some manufacturers may offer training or service packages.
- Maintenance Requirements: Understand the ongoing maintenance needs of the chosen WHRB technology to ensure optimal performance and prevent issues.
Regulations and Permits:
- Environmental Compliance: Research any local regulations or permits required for installing and operating a WHRB system. Ensure the chosen boiler meets environmental compliance standards.
Consulting with experienced WHRB manufacturers and engineers is highly recommended during the selection process. They can provide valuable insights based on your specific requirements and help you choose the most suitable WHRB technology for your application.
By carefully considering these factors, you can make an informed decision when selecting a waste heat recovery boiler that optimizes efficiency, meets your operational needs, and delivers a good return on investment.
The cost of a waste heat recovery boiler (WHRB) can vary significantly depending on several factors, making it difficult to provide a fixed price range. Here’s a breakdown of the key elements that influence WHRB cost:
Boiler Type: Recuperative boilers are generally less expensive than regenerative boilers due to their simpler design. Regenerative boilers, while offering higher efficiency, involve more complex components like rotating valves and heat storage chambers, leading to a higher price tag.
Size and Capacity: Larger WHRBs designed to handle higher exhaust gas volumes and generate more steam or hot water will naturally cost more than smaller units.
Material Selection: The materials used in the boiler construction can impact the cost. Higher-grade materials chosen for durability in corrosive environments will add to the overall cost.
Manufacturer and Features: Different manufacturers may offer WHRBs at varying price points depending on their brand reputation, included features, and warranties.
Customization Needs: Any custom design requirements or modifications to suit a specific application will add to the overall cost.
While specific prices can’t be quoted here, some general indications can be gleaned from online resources. Here’s a ballpark range to consider, keeping in mind these are estimates and actual costs can differ:
- Low-Range: Simpler WHRBs for smaller applications might start around $6,300 (USD) depending on the source.
- Mid-Range: Industrial WHRBs for typical applications may range from $50,000 to $200,000 (USD) or more.
It’s important to remember that the initial cost of a WHRB is just one part of the equation. The long-term operational savings from reduced fuel consumption and improved efficiency can be significant. A feasibility study considering your specific situation is crucial to determine the payback period and assess the overall cost-effectiveness of a WHRB for your facility.
For a more accurate estimate on a WHRB system, it’s advisable to consult directly with WHRB manufacturers and obtain quotes based on your specific requirements like exhaust gas characteristics, desired steam/hot water output, and any customization needs.
A Waste Heat Recovery Boiler (WHRB) consists of several key components, each playing a crucial role in the efficient recovery of waste heat and conversion into usable energy. Here’s a breakdown of the main components:
1. Heat Exchanger: The core component where the transfer of heat from the waste gases to the water or steam occurs. It can be designed as a bundle of tubes through which hot gases flow while water circulates around them, or vice versa, depending on whether it’s a fire-tube or water-tube boiler.
2. Burner (if applicable): In some WHRBs, especially those used in conjunction with lower temperature waste gases, a supplementary burner may be included to boost the temperature of the gases before they enter the heat exchanger.
3. Economizer: Often used to preheat the feedwater entering the boiler using residual heat from the flue gases. This component enhances the overall efficiency of the system by reducing the energy needed to bring the water up to boiling point.
4. Superheater: This component increases the temperature of the steam produced by the boiler above its saturation point, without increasing the pressure. This dry steam is particularly useful for power generation and industrial processes requiring high-quality steam.
5. Air Preheater: Utilizes the waste heat to preheat the air entering the combustion chamber, improving the efficiency of the burner and reducing fuel requirements.
6. Evaporator: This is where the phase change from liquid to vapor (water to steam) occurs. It is a crucial component that handles the primary thermal load of converting water into steam using the recovered heat.
7. Condenser: Not present in all WHRB systems, but when used, it condenses the exhaust steam from a turbine back into water that can be reheated and turned back into steam, enhancing the system’s efficiency through recirculation.
8. Boiler Drums and Headers: These are pressure vessels that serve as reservoirs for steam and water. They help to separate steam from water and distribute feedwater and steam to different parts of the boiler.
9. Control Systems: Automated systems that monitor and regulate the operation of the boiler, including temperature, pressure, and flow rates to ensure efficient and safe operation.
10. Safety Valves and Gauges: Essential for preventing overpressure conditions which could lead to explosions. Safety valves release steam if the pressure becomes too high, while gauges allow operators to monitor the boiler’s operational parameters.
11. Blowdown Tank: Used to periodically remove water from the boiler to control the concentrations of dissolved minerals and impurities, helping to prevent scaling and corrosion.
12. Stack: A chimney that allows exhaust gases to exit the system once they have passed through the boiler. It plays a critical role in ensuring proper draft to remove gases efficiently.
These components work together to ensure that the WHRB operates efficiently, safely, and effectively, converting waste heat into useful thermal energy or steam.
The efficiency of a waste heat recovery boiler (WHRB) refers to how effectively it captures usable heat from the exhaust gases and converts it into steam or hot water. Here’s the approach commonly used to calculate WHRB efficiency:
Efficiency Formula:
The most common formula used to calculate WHRB efficiency is:
η = 100 - (q2 + q3 + q4 + q5 + q6)
where:
- η (eta) represents the WHRB efficiency as a percentage.
- q2, q3, q4, q5, and q6 represent the heat losses from the boiler system expressed in kW or another unit of power.
Heat Loss Breakdown (q terms):
These terms account for various heat losses that occur within the WHRB, reducing the overall efficiency:
- q2 (Flue Gas Losses): This represents the heat carried away by the cooled exhaust gases exiting the WHRB stack.
- q3 (Incomplete Combustion Losses): This accounts for any unburned fuel present in the exhaust gases due to incomplete combustion in the primary process.
- q4 (Solid Incomplete Combustion Losses): This applies to specific cases where solid fuels are used, and some unburned solid particles are carried over with the exhaust gases.
- q5 (Heat Radiation Losses): This represents heat lost to the surrounding environment through radiation from the boiler surfaces.
- q6 (Slag and Ash Physical Losses): This term is relevant for WHRBs handling exhaust gases with slag or ash particles. It accounts for the heat carried away by these physical materials exiting the boiler.
Data Requirements:
To calculate WHRB efficiency using this formula, you’ll need data for:
- Mass flow rate of the working fluid (water) through the boiler (m_dot_w).
- Specific heat capacity of the working fluid (water) (cp_w).
- Inlet and outlet temperatures of the working fluid (T_w1 and T_w2).
- Mass flow rate of the fuel used in the primary process (m_dot_f) (assumed for simplicity). This might not be directly applicable depending on the WHRB setup.
- Enthalpy of vaporization of the fuel (h_fg) (assumed for simplicity). This might not be directly applicable depending on the WHRB setup.
Alternative Efficiency Calculation (for specific cases):
If the focus is on the heat output specifically delivered to the working fluid, an alternative approach can be used:
η_whrb = (Q_out / Q_in) * 100
where:
- η_whrb represents the WHRB efficiency as a percentage in this specific context.
- Q_out represents the heat gained by the working fluid (water), calculated using its mass flow rate, specific heat capacity, and temperature change.
- Q_in represents the heat input, which can be estimated based on the fuel mass flow rate and its enthalpy of vaporization (assuming all heat goes to the exhaust gases).
Importance of Efficiency:
A higher WHRB efficiency signifies that the boiler is capturing a larger portion of the available waste heat and converting it into usable thermal energy. This translates to greater operational benefits like:
- Reduced fuel consumption for steam or hot water generation.
- Lower energy costs for your facility.
- Minimized environmental impact by utilizing waste heat and reducing reliance on fossil fuels.
Who Performs the Calculations?
WHRB efficiency calculations are typically performed by engineers specializing in thermodynamics or thermal systems. They can assess the specific WHRB design, measure or obtain relevant data points, and apply the appropriate formula to determine the efficiency.
In conclusion, calculating WHRB efficiency requires understanding the heat loss components and having access to specific data about the boiler operation and working fluid. While the formulas may seem complex, consulting with WHRB specialists or manufacturers can help you determine the efficiency of your system and identify areas for improvement.
Waste Heat Recovery Boiler
Ultimate Guide
2024
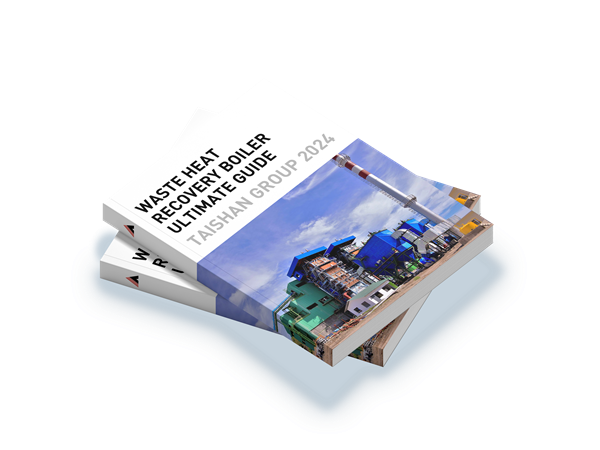
This guidebook serves as an extensive resource for professionals, engineers, and researchers interested in Waste Heat Recovery Boiler. It covers the fundamental principles, technology advancements, design considerations, operational challenges, and environmental impacts of Waste Heat Recovery Boiler. Through detailed explanations, case studies, and practical insights, readers will gain a deep understanding of Waste Heat Recovery Boiler technology and its applications in modern power and heat generation.