FAQ
About Us FAQs
Frequently Asked Questions
Taishan Group is a leading designer, manufacturer, and exporter of industrial boilers and pressure vessels. Established in 1978, the company provides turnkey solutions for coal-fired and industrial boilers to customers worldwide.
Taishan Group has achieved ISO9001, ISO14001, OHSAS18001, ASME, and PCCC certifications. The company also holds Class A Manufacture License for boilers and Class A1, A2 & A3 Design and Manufacture Licenses for pressure vessels.
Taishan Group offers a wide range of products, including:
- Pulverized coal-fired boilers
- Waste heat recovery boilers
- Biomass industrial and power station boilers
- CFB power station boilers (35-670 t/h)
- Coal-fired chain grate steam boilers (1-75 t/h)
- Coal-fired hot water boilers (46-116 MW)
- Oil and gas-fired boilers (1-200 t/h)
- Organic heat carrier boilers
- Various pressure vessels (A1, A2, A3 grade)
- Spherical storage vessels
- Transformers (30-360000 kVA)
- Refrigeration equipment
- Related products such as seamless steel tubes, steel plates, electric traction lines, and generator sets
Taishan Group operates a 37800 square meter factory with assets worth 500 million USD. The company employs 5,000 staff across 15 subsidiaries.
Taishan Group’s products are used in over 36 countries, including Switzerland, Sweden, Australia, the USA, Canada, New Zealand, Japan, Pakistan, Spain, India, Malaysia, Singapore, the Philippines, South Africa, Argentina, Indonesia, Kenya, Algeria, Ghana, Guyana, Mongolia, Chile, Peru, Dubai, Poland, Mexico, Brazil, Lebanon, Thailand, Kazakhstan, Turkmenistan, Bangladesh, Colombia, and Bahrain.
Taishan Group focuses on innovation, high quality, and efficiency in product development. The company emphasizes integrated engineering design, structural design, finite element analysis, process planning, manufacturing deployment, site installation, and quality control.
Taishan Group has one national and two provincial technology development centers and collaborates with renowned universities like Shandong University and Shandong Institute of Technology. The company has acquired more than 76 patents and developed five series and 30 different types of industrial boilers and pressure vessels.
Tai’an Boao International Trade Co., Ltd., a wholly-owned subsidiary of Taishan Group, manages the group’s international business, including import and export, overseas sales, installation, after-sales service, technical cooperation, overseas investment, and joint ventures.
Taishan Group has strong competitive advantages in coal-fired and biomass-fired boilers due to its extensive R&D capabilities, advanced technology, high-quality products, and comprehensive after-sales service.
You can contact Taishan Group through their official website or reach out to Tai’an Boao International Trade Co., Ltd. for international business inquiries.
A garbage incinerator is a facility designed to burn solid waste as a method of waste management. By combusting waste, incinerators reduce its volume and mass, potentially generate energy, and minimize the amount of material sent to landfills.
Garbage incinerators have several advantages that make them a potential solution in waste management strategies. Here’s a breakdown of the key benefits:
Waste Volume Reduction: Incineration significantly reduces the volume of waste compared to landfills. This can be crucial for areas with limited landfill space. Burning waste at high temperatures can result in a 90% or more reduction in volume.
Energy Production (in some facilities): When equipped with heat recovery systems, incinerators can capture the heat generated during combustion to produce steam or hot water. This steam can then be used to generate electricity or used for industrial processes, offsetting reliance on fossil fuels for energy production.
Destruction of Pathogens: The high temperatures within the incinerator chamber effectively destroy harmful bacteria and pathogens present in the waste. This can help reduce the risk of disease transmission associated with landfills.
Reduced Reliance on Landfills: By diverting waste from landfills, incinerators can help to extend the lifespan of existing landfills and potentially reduce the need for creating new ones.
Here are some additional advantages to consider:
Potential for Waste-to-Energy independence: In some scenarios, the electricity generated from incinerators can contribute to a region’s energy independence, reducing reliance on imported fuels.
Treatment of Certain Wastes: Incineration can be a suitable option for specific types of waste that are difficult to recycle or compost, such as medical waste or hazardous materials (with proper controls).
It’s important to remember that these advantages come with some drawbacks that also need to be considered (see next answer for details on disadvantages).
While garbage incinerators offer some advantages in waste management, there are also significant drawbacks to consider:
Air Pollution: Despite emission control systems, incinerators still release pollutants like nitrogen oxides, sulfur oxides, and fine particulate matter into the atmosphere. These pollutants can contribute to respiratory problems, heart disease, and other health issues, especially for people living near incinerator facilities.
Ash Disposal: The burning process leaves behind ash residue, which can contain concentrated heavy metals and other contaminants. This ash requires careful handling and disposal in specially lined landfills, adding to overall waste management costs.
High Costs: Building and operating incinerator facilities is expensive. The initial investment for the incinerator itself, pollution control equipment, and ongoing maintenance can be significant.
Not a Recycling Solution: Incineration destroys materials that could potentially be recycled, such as paper, plastic, and metals. This goes against the principles of waste reduction and resource recovery preferred in a waste management hierarchy.
Limited Long-Term Benefits: While incinerators can reduce landfill dependence, they don’t eliminate waste. They also contribute to greenhouse gas emissions, albeit potentially less than landfills due to energy recovery capabilities in some facilities.
Here are some additional disadvantages to consider:
Public Opposition: Concerns about air quality and potential health risks can lead to public opposition to incinerator construction in communities.
Risk of Malfunction: Incinerator malfunctions can lead to even higher pollutant emissions, highlighting the importance of stringent regulations and proper operation.
Focus on Waste Disposal, Not Reduction: Incineration can encourage a “throw-away” mentality and distract from efforts to reduce waste generation at the source and prioritize recycling and composting.
Overall, the decision to utilize garbage incinerators requires careful consideration of both the potential benefits and drawbacks. Many countries are moving away from incineration and focusing on waste reduction, recycling, and composting strategies to create a more sustainable waste management approach.
A garbage incinerator tackles waste disposal in a series of key steps:
Waste Acceptance and Sorting (Optional): Garbage trucks deliver waste to the incinerator facility. In some cases, there might be preliminary sorting to remove recyclables or hazardous materials before incineration. This can help divert materials for recycling or require specialized treatment for hazardous waste.
Combustion Chamber: The sorted waste is then transferred into a large, enclosed combustion chamber. Here, the waste is burned at extremely high temperatures, typically exceeding 1,500°C (2,700°F). This intense heat breaks down the waste materials and significantly reduces their volume.
Air Pollution Control Systems: The exhaust gases from the combustion chamber contain pollutants like fly ash (fine particles), acid gases (sulfur dioxide, nitrogen oxides), and heavy metals. These can be harmful to human health and the environment if released untreated. The exhaust passes through a series of air pollution control systems designed to remove these contaminants before they are released into the atmosphere. Here are some common methods used:
- Scrubbers: These use a spray of water or a chemical solution to capture and remove pollutants from the exhaust gas.
- Baghouses: These are large fabric filters that trap fine particles like fly ash from the exhaust stream.
- Selective Non-catalytic Reduction (SNCR): This technology injects ammonia or urea into the exhaust gas stream to convert nitrogen oxides into less harmful substances like nitrogen and water vapor.
Ash Handling: The burning process significantly reduces the original waste volume, leaving behind ash residue. This ash may contain concentrated heavy metals or other contaminants and requires careful handling. It often undergoes further treatment to stabilize it before being disposed of in a designated landfill.
Energy Recovery (optional): In some incinerators, the heat generated during combustion isn’t simply released into the atmosphere. Heat exchangers capture this thermal energy to create steam or hot water. This steam can then be used for various purposes, including:
- Electricity Generation: The steam can be used to drive turbines that generate electricity.
- District Heating: The hot water can be piped to nearby buildings for space heating and hot water needs.
Here’s an analogy to visualize the process: Imagine a large, high-temperature oven (combustion chamber) that breaks down trash. The leftover smoke from the oven (flue gas) needs to be cleaned by filters and scrubbers (air pollution control) before it can be released outside. Some incinerators also capture the heat from the oven (energy recovery) to generate steam or hot water for other uses.
The environmental friendliness of garbage incinerators is a complex issue with strong arguments on both sides. Here’s a breakdown to help you form your own opinion:
Potential Benefits:
Waste Volume Reduction: Incineration significantly reduces waste volume compared to landfills, potentially extending their lifespan and reducing the need for new ones.
Energy Production (in some facilities): With proper technology, incinerators can capture heat from combustion to generate electricity or heat buildings, offsetting reliance on fossil fuels.
Destruction of Pathogens: High incineration temperatures effectively destroy harmful bacteria and pathogens present in the waste, potentially reducing health risks associated with landfills.
Environmental Drawbacks:
Air Pollution: Despite controls, incinerators emit pollutants like nitrogen oxides, sulfur oxides, and particulate matter, impacting air quality and potentially causing respiratory problems.
Ash Disposal: The burning process leaves behind ash containing concentrated heavy metals. This ash requires careful handling and disposal in landfills, adding to environmental burdens.
Greenhouse Gas Emissions: While potentially lower than landfills, incinerators still contribute to greenhouse gas emissions through incomplete combustion and energy use.
Additional Considerations:
Focus on Waste Disposal, Not Reduction: Incineration can encourage a “throw-away” mentality and distract from efforts to reduce waste generation at the source and prioritize recycling and composting.
Public Perception: Concerns about air quality and potential health risks can lead to public opposition to incinerator construction in communities.
The Future of Waste Management:
Many countries are moving away from incineration and focusing on a waste management hierarchy that prioritizes:
- Waste Reduction: Minimize waste generation through product design, reuse, and responsible consumption.
- Recycling and Composting: Recover valuable materials and organic matter for reuse in new products or soil amendment.
- Waste-to-Energy (with advanced technologies): Explore cleaner and more efficient technologies for energy recovery from waste, minimizing environmental impact.
Overall:
Garbage incinerators offer some advantages in waste management, but they come with environmental drawbacks. As we strive for sustainability, the focus is shifting towards waste reduction, recycling, and exploring cleaner waste-to-energy technologies.
Selecting the right garbage incinerator requires careful consideration of several factors specific to your needs and situation. Here’s a roadmap to guide you through the decision process:
Needs Assessment:
Waste Type and Volume: Identify the type of waste you plan to incinerate (municipal solid waste, medical waste, etc.) and the typical daily or annual volume you expect to handle.
Energy Recovery Needs: Do you require the incinerator to generate electricity or heat for your facility? If so, determine the desired energy output.
Environmental Regulations: Research and understand the local and national regulations regarding air emissions, ash disposal, and overall environmental impact.
Budgetary Constraints: Factor in the upfront cost of the incinerator itself, pollution control equipment, and ongoing maintenance expenses.
Choosing the Right Incinerator:
Type of Incinerator: Based on your waste type and needs, consider options like:
- Mass-burn incinerators: Suitable for various unsorted municipal solid waste.
- Waste-to-Energy (WtE) facilities: Prioritize capturing heat for electricity or district heating.
- Fluidized bed incinerators: May offer lower emissions for certain waste types.
- Plasma gasification (emerging technology): Breaks down waste into cleaner-burning syngas.
Capacity and Efficiency: Select an incinerator with sufficient capacity to handle your waste volume while ensuring optimal efficiency for cost-effectiveness.
Air Pollution Control Systems: Choose an incinerator with robust air pollution control systems that meet or exceed regulatory requirements.
Reputation and Experience: Research the reputation and experience of potential incinerator manufacturers and consider factors like after-sales service and maintenance support.
Additional Considerations:
Public Perception: Be mindful of potential public concerns about air quality and engage in transparent communication with the community.
Long-Term Sustainability: Evaluate the incinerator’s alignment with your long-term sustainability goals. Consider if it prioritizes waste reduction or primarily focuses on waste disposal.
Alternative Solutions:
Before committing to incineration, explore alternative waste management strategies like:
Waste Reduction Programs: Implement initiatives to reduce waste generation at the source.
Recycling and Composting: Prioritize recycling and composting programs to divert materials from incineration.
Advanced Waste-to-Energy Technologies: Consider emerging technologies like anaerobic digestion for organic waste conversion into biogas, or chemical recycling to break down plastics for reuse.
Remember, choosing a garbage incinerator is a significant decision. By carefully assessing your needs, researching options, and considering alternatives, you can determine if incineration is the most suitable solution for your specific waste management challenge.
The cost of a garbage incinerator can vary widely based on several factors including its capacity, technology, location, regulatory requirements, and additional features like energy recovery systems. Here’s an overview of the main cost components and factors influencing the price of garbage incinerators:
Initial Capital Costs
1. Size and Capacity: The capacity of the incinerator significantly impacts the price. Smaller units might cost a few million dollars, while large-scale municipal incinerators can cost upwards of $100 million or more, depending on the scale and capabilities.
2. Technology: Advanced technologies, especially those designed to handle different types of waste and include sophisticated emission control systems, are more expensive. Technologies such as rotary kilns or fluidized bed incinerators generally cost more than simple fixed grate designs.
3. Energy Recovery Systems: Incinerators equipped with systems to convert waste heat into electricity or heat (waste-to-energy) have higher upfront costs but can provide financial returns through energy production.
4. Emission Control Systems: Meeting stringent environmental standards requires installation of advanced air pollution control systems which add to the initial investment. Systems such as scrubbers, filters, and catalysts are essential for compliance but are costly.
Operating and Maintenance Costs
1. Fuel (if required): Some incinerators require additional fuel to maintain optimal combustion temperatures, adding to the operating costs.
2. Labor: Continuous operation involves staffing costs for monitoring, maintenance, and management.
3. Maintenance: Regular maintenance is crucial to ensure operational efficiency and compliance with environmental regulations, which involves periodic replacement of parts like filters and servicing of mechanical components.
4. Disposal of Residues: The costs associated with handling and safely disposing of ash and other residues can be significant, especially if the ash is classified as hazardous waste.
Other Costs
1. Permitting and Compliance: Costs associated with obtaining permits, conducting environmental impact assessments, and ensuring regulatory compliance can be considerable.
2. Infrastructure: Additional infrastructure needed for waste delivery, storage, and handling, as well as for residue disposal, must be factored into the total cost.
3. Financing: Interest on capital borrowed to build the incinerator can add substantially to the overall costs.
Estimation Examples
– Small-scale incinerators for specific applications (like medical waste) might start around $50,000 to $500,000.
– Medium-scale incinerators capable of processing several tons of municipal solid waste per day might range from $1 million to $15 million.
– Large municipal waste-to-energy plants can easily exceed $100 million, depending on their size and the complexity of technologies used.
The economic feasibility of a garbage incinerator also depends on potential revenue streams from energy production and the savings from reduced landfill use, which can offset some of the high initial and operational costs over time. When considering an investment in a garbage incinerator, it’s crucial to conduct a thorough cost-benefit analysis, including long-term operational costs and potential environmental and social impacts.
Yes, there are several alternatives to garbage incineration, each with its own set of advantages and challenges. These alternatives focus on waste management principles like reducing, reusing, recycling, and recovering waste in different forms. Here’s a brief overview of some key alternatives:
1. Recycling and Composting
– Recycling involves separating, collecting, and processing materials from waste to make new products. It can significantly reduce the need for extracting raw materials, save energy, and decrease pollution.
– Composting is the biological decomposition of organic waste, such as food scraps and yard waste, into nutrient-rich compost. It reduces the volume of waste sent to landfills and provides a natural fertilizer for agriculture and gardening.
2. Anaerobic Digestion
– This process breaks down organic material in the absence of oxygen, producing biogas (a mixture of methane and carbon dioxide) and digestate, a nutrient-rich substance. The biogas can be used as a renewable energy source, while the digestate can be used as a fertilizer.
3. Mechanical Biological Treatment (MBT)
– MBT combines mechanical separation of waste (to recover recyclable materials) with biological treatment (such as composting or anaerobic digestion) of the organic fraction. The process reduces the volume of waste and recovers materials and energy.
4. Landfill Gas Capture
– While landfills are often considered the last option for waste disposal, modern landfills can be designed to capture methane gas produced from the decomposition of organic waste. This gas can then be used to generate electricity or heat, reducing greenhouse gas emissions.
5. Pyrolysis and Gasification
– These are thermal processes that decompose organic material at high temperatures in the absence (pyrolysis) or limited presence (gasification) of oxygen. They produce syngas (a mixture of hydrogen, carbon monoxide, and other gases), which can be used to generate energy or as a feedstock for producing chemicals. These processes typically produce fewer pollutants than direct incineration.
6. Material Recovery Facilities (MRFs)
– MRFs focus on separating and preparing recyclable materials for end-user manufacturers. While not a disposal method, MRFs are integral to reducing the volume of waste needing disposal through incineration or landfilling.
7. Plasma Arc Recycling
– An advanced waste treatment technology that uses plasma torches to heat waste to extremely high temperatures, breaking down organic material into syngas and leaving behind a solid waste called slag, which can be used in construction. This process is expensive but can handle a wide range of wastes, including hazardous materials.
8. Reduce, Reuse, Rethink
– Beyond technological solutions, reducing waste generation through lifestyle changes, reusing materials, and rethinking consumption patterns are fundamental to sustainable waste management. Policies and programs that encourage these behaviors can significantly decrease the amount of waste requiring disposal.
Each of these alternatives has its own environmental, economic, and social implications. The choice of waste management strategy depends on various factors, including the type and amount of waste generated, local regulations, available infrastructure, and societal values. Often, a combination of these methods, tailored to local conditions, is the most effective approach to managing waste sustainably.
There are several main types of garbage incinerators, each with their own advantages and disadvantages. Here’s a breakdown of some common ones:
Traditional Incineration:
- Mass-burn incinerators: These are the most common type, designed to burn unsorted municipal solid waste (MSW) at high temperatures. They offer a simple design but may have higher emission levels compared to some advanced technologies.
Advanced Incineration Technologies:
Fluidized bed incinerators: These utilize a bed of sand or inert material fluidized by air to suspend and burn the waste more efficiently at lower temperatures, potentially reducing some harmful emissions.
Rotary kiln incinerators: These employ a large, rotating cylindrical furnace to process waste. They can handle a wider variety of waste types and offer good efficiency, but can be more complex and expensive to build.
Emerging Technologies:
- Plasma gasification: This technology uses high-temperature plasma torches to break down waste into a syngas (synthetic gas) which can be used for fuel or further processed into cleaner burning fuels. It’s a developing technology with potential environmental benefits, but requires further research and development.
Here’s a table summarizing the key characteristics of these incinerator types:
Incinerator Type | Description | Advantages | Disadvantages |
---|---|---|---|
Mass-burn | Simplest design, burns unsorted MSW | Low upfront cost | Potentially higher emissions |
Fluidized Bed | Uses fluidized bed for efficient burning | Lower emissions compared to mass-burn | More complex design than mass-burn |
Rotary Kiln | Large rotating furnace, handles diverse waste | Good efficiency, processes various waste types | Higher cost and complexity compared to mass-burn |
Plasma Gasification | Uses plasma torches to break down waste into syngas | Potentially cleaner burning syngas | Emerging technology, high energy requirements |
Additional Considerations:
Waste-to-Energy (WtE) Facilities: These incinerators prioritize capturing the heat generated during combustion to produce electricity or district heating. They can be any of the above types but emphasize energy recovery.
Size and Capacity: Incinerators come in various sizes, with capacities to handle different volumes of waste.
When choosing an incinerator type, factors like waste composition, desired emission levels, energy recovery needs, and budget will influence the selection process.
Comparing garbage incinerators and landfills for environmental impact is complex, with both options having advantages and disadvantages. Here’s a breakdown to help you understand the trade-offs:
Waste Volume Reduction:
- Incinerators: Significantly reduce waste volume through burning, potentially extending landfill lifespan.
- Landfills: Waste accumulates and takes up space, requiring new landfills as existing ones reach capacity.
Air Pollution:
- Incinerators: Emit pollutants like nitrogen oxides, sulfur oxides, and particulate matter, even with controls. These can contribute to respiratory problems and other health issues.
- Landfills: Generate methane, a potent greenhouse gas, from decomposing organic waste. Landfills may also have issues with odor and air pollution from volatile organic compounds (VOCs).
Land and Water Contamination:
- Incinerators: Ash residue from incineration can contain heavy metals and require careful disposal in landfills, potentially impacting land and water quality if not properly managed.
- Landfills: Leachate, a liquid formed from decomposing waste, can seep into the ground and contaminate water sources if landfills are not properly lined and monitored.
Resource Recovery:
- Incinerators: Some incinerators (WtE facilities) can capture heat to generate electricity or heat buildings, offsetting reliance on fossil fuels.
- Landfills: Landfills offer limited opportunities for resource recovery, though some advancements are being made in capturing landfill gas for energy production.
Overall Impact:
- Incinerators: Reduce landfill dependence but introduce air pollution concerns and require careful ash management.
- Landfills: Offer lower upfront costs but contribute to greenhouse gas emissions and have potential for land and water contamination.
Here are some additional factors to consider:
Regulations: Both incinerators and landfills are subject to environmental regulations that aim to minimize their impact. However, the effectiveness of regulations can vary depending on location.
Long-Term Sustainability: Neither option is ideal for a sustainable waste management strategy. The focus is shifting towards waste reduction, recycling, and composting to minimize reliance on both landfills and incinerators.
Ultimately, the choice between incinerators and landfills depends on specific circumstances and priorities. Some communities may find a combination of waste reduction initiatives, recycling, and a smaller, well-controlled incinerator for residual waste to be the most suitable approach.
CFB Circulating Fluidized Bed boiler
A Circulating Fluidized Bed (CFB) boiler is a type of boiler that uses the circulating fluidized bed combustion (CFBC) process to generate heat or power. In this technology, the fuel and air are introduced into the combustion chamber, where they are rapidly mixed and brought to a fluidized state by the high-speed air flow from below. This fluidized mixture behaves much like a liquid, ensuring uniform temperature distribution and efficient combustion.
The core components of a CFB boiler include the combustion chamber, cyclone separators (to separate and recirculate the bed material), heat exchangers or boiler tubes (to absorb the heat generated by combustion), and control systems for managing air supply and fuel feed. The circulation of the bed material enhances heat transfer and ensures uniform temperature distribution within the combustion chamber, leading to efficient and clean combustion.
The Circulating Fluidized Bed Process
A circulating fluidized bed (CFB) is a reactor technology that utilizes a continuous loop of gas and solid particles to achieve efficient and environmentally friendly conversion processes. Here’s a breakdown of the key steps:
1. Feedstock Introduction: The process begins with feeding the desired fuel, which can be coal, biomass, or even waste materials, into the bottom of the reactor vessel. Air, preheated to a specific temperature, is also introduced at this stage.
2. Fluidization: The incoming air flows through a distributor plate at the bottom of the vessel, causing the solid particles (fuel and bed material) to become suspended and behave like a fluidized bed. This enhances gas-solid contact and promotes efficient mixing.
3. Combustion: The hot, fluidized environment provides ideal conditions for combustion. The fuel particles mix thoroughly with the air, leading to complete and efficient burning. The lower combustion temperature compared to traditional methods helps minimize the formation of nitrogen oxides (NOx) emissions.
4. Particle Separation: The high gas velocity in a CFB system creates a circulating loop. The flue gas (combustion products) is carried upwards, while a cyclone separator efficiently separates the entrained solid particles from the gas stream.
5. Solids Recirculation: The captured solids from the cyclone separator are then reintroduced back into the bottom of the reactor vessel. This continuous circulation ensures high fuel conversion efficiency and maximizes heat transfer within the bed.
6. Heat Recovery: The heat generated during combustion is transferred to the fluidized bed material and the gas stream. This thermal energy can be used for various purposes, such as generating steam for power production or process heating applications.
7. Flue Gas Treatment: The flue gas exiting the cyclone separator might undergo further treatment depending on the specific application. Scrubbers or other technologies can be employed to capture sulfur oxides (SOx) and other pollutants for cleaner emissions.
Circulating Fluidized Bed (CFB) technology, especially when it comes to boilers and combustion systems, offers several notable advantages compared to conventional combustion technologies. Here are some of the key benefits:
1. Fuel Flexibility: CFB technology can utilize a wide range of fuels, including low-grade coal, biomass, waste fuels, and peat. This flexibility allows for the use of local fuel sources and can help in reducing fuel costs and dependency on specific fuel types.
2. Low Emissions: CFB boilers are known for their ability to significantly reduce emissions of pollutants such as sulfur dioxide (SO2) and nitrogen oxides (NOx) through in-furnace capture methods. Limestone or other sorbents can be used within the bed to capture SO2 as it is released from the fuel, often eliminating the need for external flue gas desulfurization systems.
3. Efficient Combustion: The fluidized bed facilitates efficient heat transfer and uniform temperature distribution, leading to improved combustion efficiency. This efficiency is maintained even with varying fuel qualities, reducing the amount of unburned carbon in the ash and enhancing the overall efficiency of the system.
4. Reduced Corrosion and Fouling: The lower combustion temperatures in a CFB boiler (typically around 800°C to 900°C) reduce the risk of ash melting or clinker formation, which in turn minimizes the potential for corrosion and fouling of heating surfaces. This can lead to longer operational life and reduced maintenance costs.
5. Ability to Capture CO2: The technology offers potential advantages for carbon capture and storage (CCS) due to its compatibility with CO2 capture methods. The CFB process can be adapted to integrate with post-combustion CO2 capture technologies more efficiently than conventional systems.
6. Operational Flexibility: CFB boilers can easily adjust to changes in fuel quality and moisture content. They also offer good load-following capabilities, making them well-suited to meet fluctuating demand in power generation.
7. Lower Operating Temperature: The operating temperature of a CFB boiler is lower than that of a pulverized coal boiler, which can lead to a reduction in the formation of nitrogen oxides (NOx). This is an environmental benefit, as NOx is a precursor to smog and acid rain.
8. Use of Low-Quality Water: CFB technology can operate with lower quality water compared to conventional boilers, which can reduce the need for water treatment and decrease the overall environmental impact.
In summary, the Circulating Fluidized Bed technology offers environmental, operational, and economic benefits, making it an attractive choice for power generation and industrial applications where reducing emissions and fuel flexibility are critical concerns.
Circulating Fluidized Bed Combustion (CFBC) boilers can utilize a wide variety of fuels, showcasing one of the technology’s primary advantages: fuel flexibility. This feature allows for the use of less expensive, lower-grade fuels while still maintaining high efficiency and low emissions. Common fuels for CFBC boilers include:
1. **Coal:** Both low-grade and high-quality coals are suitable. CFBC technology is particularly advantageous for burning low-grade coal with high ash or sulfur content, as it can capture pollutants effectively.
2. **Biomass:** Various forms of biomass, such as wood chips, sawdust, agricultural waste, and energy crops, can be used. Biomass is a renewable energy source and can help reduce carbon emissions.
3. **Waste Fuels:** Refuse-derived fuels (RDF), which are produced from the combustion of municipal solid waste, and industrial wastes can be used in CFBC boilers. This not only helps in waste management but also in energy recovery.
4. **Petcoke:** Petroleum coke, a byproduct of oil refining, is another fuel that can be utilized in CFBC boilers. Despite its high sulfur content, the CFBC process can capture sulfur effectively, reducing SO2 emissions.
5. **Mixed Fuels:** CFBC boilers can co-fire a combination of different fuels, allowing for flexibility based on fuel availability and cost. This can include a mix of coal and biomass, coal and petcoke, or other combinations.
6. **Peat:** In some regions, peat is a significant energy source and can be burned in CFBC boilers.
The capability to burn a wide range of fuels, including those that are considered waste or have low commercial value, makes CFBC boilers a versatile and environmentally friendly option for generating heat and power in a variety of settings, from utility power plants to industrial applications.
While Circulating Fluidized Bed (CFB) boilers offer numerous advantages, like fuel flexibility, high efficiency, and low emissions, there are also several disadvantages and challenges associated with this technology:
1. High Initial Investment: The initial cost of setting up a CFB boiler can be higher than conventional pulverized coal-fired boilers due to its complex design and the need for additional equipment, such as cyclones for recirculating the bed material and advanced control systems.
2. Space Requirements: CFB boilers generally require more space due to their design and the need for auxiliary equipment, which can be a constraint in areas where space is limited.
3. Wear and Tear: The circulation of solid particles within the boiler can lead to higher levels of erosion and wear on boiler tubes and other components. This necessitates the use of more wear-resistant materials, which can increase maintenance costs.
4. Complexity in Operation and Maintenance: The operation and maintenance of a CFB boiler can be more complex compared to traditional boilers. Proper training and expertise are required to handle the sophisticated control systems and to manage the fluidized bed operation effectively.
5. Handling of Sorbents and Waste: The use of limestone or other sorbents to capture sulfur dioxide generates additional waste products, such as gypsum. This requires proper disposal or recycling mechanisms, which can add to the operational costs and complexities.
6. Fuel Quality Sensitivity: While CFB boilers are adaptable to various fuel types, changes in fuel quality (such as moisture content, size, and calorific value) can affect the combustion efficiency and require adjustments in operation to maintain performance.
7. Limited to Medium and Large Scale Applications: Due to their complexity and cost, CFB boilers are more suited to medium and large-scale applications and might not be economically viable for small-scale operations.
Despite these disadvantages, the environmental benefits and the ability to utilize a wide range of fuels often outweigh the drawbacks, making CFB technology a preferred choice for many industries and power generation applications seeking sustainable and flexible solutions.
Circulating Fluidized Bed (CFB) boilers are versatile and can be used across various industries for steam, power generation, and heating purposes. Their ability to efficiently combust a wide range of fuels, including low-grade fuels and waste, while achieving low emissions, makes them particularly attractive for many applications. Here’s where CFB boilers find use in industry:
1. Power Generation: Many power plants use CFB boilers for electricity production, taking advantage of their fuel flexibility to burn coal, biomass, or mixtures of fuels in a more environmentally friendly manner. This is especially valuable in regions with abundant biomass or low-grade coal resources.
2. Waste-to-Energy Plants: CFB technology is well-suited for burning municipal solid waste (MSW) or industrial waste to generate energy. These plants not only produce electricity but also significantly reduce waste volume, contributing to waste management efforts.
3. Pulp and Paper Industry: CFB boilers are used in the pulp and paper industry for generating steam required in various stages of the paper-making process. They can burn waste products from the process, such as bark and wood chips, making them a sustainable energy solution.
4. Chemical Industry: In the chemical manufacturing sector, CFB boilers provide steam and power needed for various chemical processes. They can also utilize by-product gases and waste as fuel, improving energy efficiency and reducing costs.
5. Cement Industry: The cement industry uses CFB boilers to generate the steam and power needed for cement production processes. Additionally, the CFB’s ability to use alternative fuels, such as petcoke and waste-derived fuels, is particularly beneficial for this energy-intensive industry.
6. Metal and Mining Industry: CFB boilers supply steam and power for metal processing and mining operations, including smelting and ore processing. Their fuel flexibility allows the use of locally available fuels, which can lower energy costs.
7. District Heating Systems: Some regions use CFB boilers in district heating systems to provide heat and hot water to residential and commercial buildings. This is particularly common in colder climates where efficient heating solutions are crucial.
8. Agricultural Industry: In regions with significant agricultural activity, CFB boilers can use crop residues and other biomass materials as fuel to generate steam and electricity, supporting sustainable agricultural practices.
The broad applicability of CFB boilers across these industries highlights their importance in supporting diverse energy needs while contributing to environmental sustainability and fuel flexibility.
Choosing the right Circulating Fluidized Bed (CFB) boiler for your application involves considering a range of factors to ensure optimal performance, efficiency, and cost-effectiveness. Here are key considerations when selecting a CFB boiler:
1. Fuel Type and Availability: Assess the types of fuel available for your application, including coal, biomass, industrial waste, or a mix. CFB boilers are known for their fuel flexibility, but the specific fuel characteristics (such as moisture content, ash content, and heating value) can impact the boiler design and efficiency.
2. Boiler Capacity and Efficiency: Determine the required boiler capacity, which is typically measured in tons of steam per hour or megawatts (MW) of power. The efficiency of the boiler in converting fuel into steam or electricity is also crucial, as higher efficiency leads to lower operating costs.
3. Emission Requirements: Identify the environmental regulations applicable to your location and industry. CFB boilers can significantly reduce sulfur dioxide (SO2) and nitrogen oxides (NOx) emissions, but the specific design may need to be tailored to meet stringent emission standards.
4. Operational Flexibility: Consider the need for operational flexibility, such as the ability to scale up or down based on demand, handle fuel quality variations, and quickly start up or shut down. CFB boilers offer good load-following capabilities, but specific requirements should be discussed with manufacturers.
5. Maintenance and Operating Costs: Evaluate the maintenance requirements and operating costs, including fuel, labor, and maintenance expenses. While CFB boilers may have higher initial costs, their ability to use cheaper, low-grade fuels can lead to lower overall operating costs.
6. Space Constraints: CFB boilers require more space than conventional boilers due to their design and the need for auxiliary equipment. Ensure you have adequate space for the boiler, including space for future maintenance and inspections.
7. Water Availability: Like all steam boilers, CFB boilers require a continuous supply of water for steam generation. Assess the availability and quality of water in your area, as it can affect the boiler’s operation and maintenance.
8. Long-term Sustainability: Consider the long-term sustainability of your fuel supply and the potential for future environmental regulations. Choosing a boiler that can adapt to different fuels or that can be easily upgraded for enhanced emissions control can be beneficial.
9. Manufacturer and Support: Select a manufacturer with a good track record in CFB technology, offering robust support and service. The availability of parts, technical support, and service can significantly impact the boiler’s operational efficiency and longevity.
10. Cost: While not the only factor, the cost of the boiler and the installation should be considered in the context of the expected operational savings and efficiency gains. A more expensive boiler that offers higher efficiency and lower emissions may justify its cost over its operational lifespan.
By carefully evaluating these factors and consulting with boiler manufacturers and experts, you can select a CFB boiler that meets your needs and offers reliable, efficient, and environmentally friendly operation.
The cost of a circulating fluidized bed (CFB) boiler can vary significantly depending on several factors. Here’s a breakdown of what influences the price:
- Boiler Capacity: The size and steam generation capacity of the boiler is a major cost driver. Larger boilers for industrial power generation will naturally cost more than smaller units for district heating applications.
- Fuel Type: Boilers designed for specific fuels like low-grade coal or biomass might have different material requirements and features compared to standard coal-fired CFBs, impacting the cost.
- Emission Control Requirements: Depending on your location’s air quality regulations, additional emission control equipment like scrubbers or selective non-catalytic reduction (SNCR) systems might be necessary, adding to the overall cost.
- Manufacturer and Features: The reputation and experience of the boiler manufacturer can influence the price. Additionally, boilers with advanced features like automated controls or specialized designs for specific fuels might have a higher cost.
While specific pricing information can be difficult to find publicly due to customization involved, here’s a general range to provide an idea:
- Small-scale CFB boilers (few megawatt capacity): $10,000 – $200,000 [1] (This range might be on the lower end and may not consider all the factors mentioned above).
- Industrial-scale CFB boilers (tens to hundreds of megawatt capacity): $ Costs can range from millions to tens of millions of dollars depending on the capacity and complexity.
Here are some recommendations to get a more accurate estimate for your project:
- Contact CFB Boiler Manufacturers: Reach out to reputable CFB boiler manufacturers and request quotes based on your specific requirements (capacity, fuel type, emission regulations).
- Consider Consulting Firms: Engineering consulting firms specializing in power generation or industrial processes can provide valuable insights into CFB boiler selection and cost estimation for your project.
Remember, the initial cost is just one aspect. When evaluating the economics of a CFB boiler, consider factors like:
- Fuel Efficiency: A highly efficient boiler can save on fuel costs over time.
- Maintenance Needs: Compare maintenance requirements and potential costs between different boiler options.
- Operational Lifetime: A CFB boiler with a long lifespan can provide a better return on investment.
By carefully considering all these aspects, you can choose a CFB boiler that offers the best value proposition for your specific needs and ensures a cost-effective and environmentally friendly solution for your industrial application.
For more information about pricing, please contact us. Our professional engineers will provide you with a more accurate quotation based on your project.
Choosing between an AFBC (atmospheric fluidized bed combustion) boiler and a CFBC (circulating fluidized bed combustion) boiler depends on your specific needs and priorities. Here’s a breakdown of their key differences to help you decide:
CFBC Advantages:
- Higher Efficiency: CFBC boilers generally achieve higher combustion efficiency due to the intense circulation and better heat transfer within the fluidized bed [3, 5]. This translates to lower fuel consumption and operating costs.
- Fuel Flexibility: CFBCs can handle a wider range of fuels, including low-grade coal, biomass, and even waste materials, with good efficiency [2, 5]. This offers operational flexibility and the potential to utilize renewable or waste fuels.
- Lower Emissions: The lower combustion temperature in CFBCs leads to significantly lower NOx emissions compared to AFBCs [4]. Additionally, they can be integrated with SOx capture systems for cleaner operation.
AFBC Advantages:
- Simpler Design: AFBC boilers have a simpler design compared to CFBCs, potentially leading to lower upfront costs [2].
- Lower Auxiliary Power Consumption: AFBCs require less electrical energy to operate the fluidized bed compared to CFBCs due to the lower gas velocity needed [1].
Here’s a table summarizing the key points:
Feature | CFBC Boiler | AFBC Boiler |
---|---|---|
Efficiency | Higher | Lower |
Fuel Flexibility | More Flexible | Less Flexible |
Emissions (NOx & SOx) | Lower | Higher |
Design Complexity | More Complex | Simpler |
Auxiliary Power Consumption | Higher | Lower |
Upfront Cost | Potentially Higher | Potentially Lower |
In general, CFBC boilers are considered the more advanced and efficient technology. They are a good choice for applications where:
- High efficiency and fuel cost savings are crucial.
- A wider range of fuels, including low-grade options or biomass, needs to be accommodated.
- Strict emission regulations require low NOx and SOx outputs.
AFBC boilers might be a suitable option if:
- Cost is a major concern and a simpler design is preferred.
- Lower auxiliary power consumption is a priority.
- Fuel options are limited to standard coals, and emission regulations are less stringent.
Here are some additional factors to consider:
- Project Size: For larger-scale applications (industrial power generation), CFBCs are often the preferred choice due to their efficiency and fuel flexibility.
- Fuel Availability and Characteristics: The type of fuel readily available and its properties (moisture content, ash content) can influence the choice between AFBC and CFBC.
- Environmental Regulations: If your location has strict emission regulations, a CFBC boiler with integrated emission control systems might be necessary.
Ultimately, the best choice depends on your specific project requirements and priorities. Consulting with our qualified engineers who can assess your needs and analyze the techno-economic feasibility of both options is highly recommended.
PC (pulverized coal) boilers and CFB (circulating fluidized bed) boilers are both used for industrial applications like power generation and process heating, but they differ significantly in their technology and operation. Here’s a breakdown of the key differences:
Fuel Preparation:
- PC Boiler: Coal is pulverized into a fine powder before being injected into the furnace for combustion. This requires dedicated grinding mills, adding complexity to the system.
- CFB Boiler: Coal (or other fuels) can be used in larger particle sizes. The bed itself acts as a heat source, eliminating the need for pre-pulverization.
Combustion Process:
- PC Boiler: Combustion occurs in suspension burning, where the powdered coal mixes with air in a large furnace chamber. This requires high temperatures (around 1600-1800°C) to achieve complete combustion.
- CFB Boiler: Combustion takes place in a fluidized bed of inert material (like sand) where the fuel particles are suspended and constantly circulated. Lower combustion temperatures (around 850-950°C) are used.
Emissions:
- PC Boiler: High combustion temperatures contribute to the formation of significant nitrogen oxides (NOx) emissions. Additionally, flue gas treatment systems are often required to capture sulfur oxides (SOx).
- CFB Boiler: Lower combustion temperatures lead to substantially lower NOx emissions. SOx capture can be integrated within the boiler itself using limestone injection, reducing the need for extensive downstream scrubbing systems.
Advantages of PC Boilers:
- Established Technology: PC boilers have been around for a longer time, making them a well-understood and mature technology.
- Potentially Lower Upfront Costs: The simpler design of PC boilers might translate to lower initial investment costs compared to CFBs.
Advantages of CFB Boilers:
- Fuel Flexibility: CFBs can efficiently burn a wider range of fuels, including low-grade coals, biomass, and even waste materials.
- Higher Efficiency: The fluidized bed process promotes efficient heat transfer and combustion, leading to lower fuel consumption.
- Lower Emissions: Significantly lower NOx and SOx emissions due to lower combustion temperatures and integrated capture mechanisms.
- Load Following: CFB boilers can adjust their power output more quickly in response to fluctuating energy demands.
Disadvantages of PC Boilers:
- High Emissions: Requires additional equipment to meet stricter emission regulations.
- Fine Coal Grinding: Requires dedicated mills for pulverizing coal, adding complexity and energy consumption.
- Slagging and Fouling: High temperatures can cause molten ash deposits within the boiler, requiring maintenance.
Disadvantages of CFB Boilers:
- Higher Auxiliary Power Consumption: More energy is needed to maintain the fluidized bed circulation compared to PC boilers.
- More Complex Design: The circulating fluidized bed technology requires a more intricate design compared to PC boilers.
- Potential for Erosion: Continuous particle circulation can lead to wear and tear on internal components, requiring maintenance.
Choosing Between PC and CFB Boilers:
The ideal choice depends on your specific needs. Here’s a general guideline:
- PC boilers might be suitable for: Established applications with readily available high-quality coal, where upfront cost is a major concern, and emissions regulations are less stringent.
- CFB boilers are a good choice for: Situations where fuel flexibility is important, stricter emission regulations need to be met, high efficiency is crucial, or utilizing renewable or waste fuels is desired.
Consulting with our engineers to assess your project requirements and analyze the techno-economic feasibility of both PC and CFB boilers is highly recommended for making an informed decision.
Biomass Boiler.
A biomass boiler is a heating system that uses biomass as fuel to provide hot water and heating for homes and businesses. Biomass refers to organic materials, such as wood logs, pellets, or chips, agricultural residues, and other plant-based materials, that can be used as fuel. These boilers are considered a sustainable and renewable source of energy because they utilize materials that are either waste products from other processes or sourced from sustainably managed forests.
The working process of a biomass boiler involves several key steps:
1. Fuel Feeding: Biomass fuel is fed into the boiler’s combustion chamber, either manually or automatically through a hopper system. Automatic feeding systems are common in modern biomass boilers, providing ease of use and consistent fuel supply.
2. Combustion: The biomass fuel is burned in the combustion chamber. This process releases heat energy. Biomass boilers are designed to achieve efficient combustion, often utilizing advanced technology to ensure complete burning of the fuel.
3. Heat Transfer: The heat generated from burning biomass is transferred to water. In a typical setup, water circulates through pipes or a heat exchanger in the boiler. As the water passes through, it absorbs the heat, becoming hot water or steam.
4. Distribution: The hot water or steam is then circulated throughout the building via a system of pipes to radiators or a heat exchanger in an air handling unit for space heating. In some systems, the hot water can also be used directly for domestic hot water needs.
5. Emission Control: Modern biomass boilers are equipped with advanced systems to reduce emissions. This includes filters and scrubbers that capture particulates and other pollutants, ensuring that the boiler operates within environmental standards.
6. Ash Removal: The combustion process produces ash as a byproduct. Many biomass boilers have automatic ash removal systems that collect and remove ash from the combustion chamber, making maintenance easier.
Biomass boilers offer several benefits, including the use of renewable and often local resources, reduced dependence on fossil fuels, and potential cost savings over time. However, their suitability and efficiency can depend on various factors, such as the type of biomass fuel used, the boiler’s technology, and the heating requirements of the building.
The core components of a CFB boiler include the combustion chamber, cyclone separators (to separate and recirculate the bed material), heat exchangers or boiler tubes (to absorb the heat generated by combustion), and control systems for managing air supply and fuel feed. The circulation of the bed material enhances heat transfer and ensures uniform temperature distribution within the combustion chamber, leading to efficient and clean combustion.
Whether biomass boilers are worth the investment depends on several factors related to your specific situation, the local availability and cost of biomass fuels, environmental considerations, and financial incentives. Here are key points to consider when evaluating the worthiness of a biomass boiler:
Advantages
1. Renewable Energy Source: Biomass boilers use materials that are considered renewable, which can help reduce reliance on fossil fuels and lower carbon emissions, assuming sustainable sourcing of biomass.
2. Cost-Effective Fuel: Depending on your location, biomass fuels like wood chips, pellets, or agricultural waste can be cheaper than fossil fuels, especially in areas with abundant biomass resources.
3. Financial Incentives: Some regions offer grants, tax incentives, or subsidies for installing renewable energy systems, which can offset the initial investment in a biomass boiler.
4. Energy Independence: Using locally sourced biomass can increase energy independence and resilience by reducing reliance on imported fuels.
5. Carbon Neutral: Biomass is often considered carbon neutral because the CO2 released during combustion is approximately equal to the CO2 absorbed by the plants during their growth, although this balance can vary based on fuel source and transport distances.
Disadvantages
1. High Initial Costs: The upfront cost of purchasing and installing a biomass boiler can be higher than traditional heating systems. This includes the cost of the boiler itself, storage for the biomass fuel, and potentially more complex installation requirements.
2. Space Requirements: Biomass boilers and the associated fuel storage can require more space than conventional boilers, making them less suitable for properties with limited space.
3. Fuel Storage and Handling: You’ll need to consider the logistics of storing and handling biomass fuel, including space for storage and the effort involved in loading the fuel into the boiler if not automated.
4. Maintenance: Biomass boilers can require more maintenance than gas or oil boilers. This includes managing ash production, cleaning to maintain efficiency, and ensuring the fuel supply is dry and of high quality.
5. Environmental Considerations: While biomass is considered renewable, there are environmental considerations such as the impact of cultivating, harvesting, processing, and transporting biomass fuels. The sustainability of biomass heating also depends on ensuring that biomass sources are managed and replenished.
Making the Decision
– Cost Analysis: Compare the total cost of ownership, including installation, fuel, maintenance, and potential savings or earnings from incentives.
– Environmental Goals: Consider whether reducing your carbon footprint aligns with your personal or business environmental goals.
– Fuel Availability: Research the availability and cost of biomass fuel in your area, as well as the reliability of supply.
– Local Regulations and Incentives: Check for any local regulations regarding biomass boilers and what incentives might be available to offset costs.
In summary, biomass boilers can be a worthwhile investment for those prioritizing renewable energy, have access to affordable and sustainable biomass fuel, and are prepared for the initial financial and logistical considerations.
The cost of a biomass boiler can vary widely depending on several factors, including the size and type of boiler, its capacity (measured in kilowatts (kW)), the complexity of the installation, and the type of biomass fuel it is designed to use. Here’s a general breakdown to give you an idea:
Small Residential Boilers
– For small homes or cabins: Prices might start from around $3,000 to $10,000 for smaller systems (up to 25 kW). These boilers are typically used in residential settings and can accommodate the heating needs of a modest-sized home.
Medium to Large Residential Boilers
– For larger homes or small commercial buildings: The cost can range from $10,000 to $25,000 or more for systems in the range of 25 kW to 100 kW. The price increases with the size and complexity of the system, including the need for larger fuel storage and more sophisticated emission control technologies.
Commercial and Industrial Boilers
– For commercial or industrial use: Prices can range significantly from $25,000 to over $100,000 for high-capacity systems (over 100 kW). Commercial systems are designed to heat larger spaces such as schools, office buildings, or industrial facilities and often require customized solutions to meet specific heating demands and efficiency requirements.
Additional Costs
– Installation: The cost of installing a biomass boiler can vary greatly based on the complexity of the system, any necessary modifications to the property, and local labor rates. Installation can add several thousand dollars to the total cost.
– Fuel Storage: You may need to construct or modify a space for fuel storage, which can add to the upfront costs.
– Maintenance and Operation: Ongoing costs include purchasing biomass fuel, routine maintenance, and potential repairs. These costs will vary based on the type of fuel used, the size of the boiler, and how often it’s used.
Financing and Incentives
– Incentives: Some governments offer financial incentives for installing renewable energy systems, including tax credits, rebates, and grants. These can significantly offset the initial investment.
– Return on Investment: While the upfront costs can be high, the potential savings on fuel costs compared to fossil fuels can make biomass boilers a cost-effective solution in the long term, especially in areas where biomass fuels are readily available and cheaper than conventional fuels.
It’s important to get multiple quotes from different suppliers and installers to understand the full range of options and costs for your specific needs. Also, consider the long-term savings and potential incentives when evaluating the overall cost-effectiveness of a biomass boiler system.
The running costs of biomass boilers can vary significantly based on several factors, including the type and cost of biomass fuel, the efficiency of the boiler, the size and heating requirements of the property, and how well the system is maintained. Here’s an overview to help you understand the potential expenses:
Fuel Costs
– Biomass Fuel: The most common types of biomass fuel are wood pellets, wood chips, and logs. The cost of these fuels can vary by region, availability, and quantity purchased. Generally, wood pellets are more expensive than wood chips and logs but are more energy-dense and burn more efficiently.
– Comparison with Fossil Fuels: Depending on the market, biomass fuels can be cheaper or comparable in price to fossil fuels like natural gas, oil, or electricity. However, prices can fluctuate based on demand, supply constraints, and changes in energy markets.
Efficiency and Consumption
– Boiler Efficiency: Modern biomass boilers are typically quite efficient, with ratings often between 80% to 90%. Higher efficiency means more of the fuel’s energy is converted into usable heat, potentially lowering running costs.
– Property Size and Insulation: The amount of fuel needed depends on the size of the property, its insulation quality, and the heating demand. Better-insulated homes require less energy to heat, which can significantly reduce running costs.
Maintenance and Operational Costs
– Maintenance: Regular maintenance is crucial for keeping a biomass boiler running efficiently and can include cleaning the heat exchanger, removing ash, and servicing moving parts. These costs vary depending on the complexity of the system and local service rates.
– Replacement Parts: Over time, certain components may need to be replaced, adding to the operational costs.
Environmental Considerations
– Carbon Tax and Environmental Regulations: In some regions, there may be taxes or levies on carbon emissions or incentives for reducing greenhouse gas emissions, which can affect the overall cost-effectiveness of biomass boilers compared to fossil fuel alternatives.
Long-term Savings and Incentives
– Government Incentives: Tax credits, subsidies, and other incentives for renewable energy installations can offset some of the operational costs.
– Stable Fuel Prices: Biomass fuel prices can be more stable than fossil fuels, which are subject to geopolitical tensions and market volatility. This stability can make budgeting for heating costs easier over the long term.
Summary
While the initial investment in a biomass boiler can be higher than for conventional heating systems, the running costs need to be considered in the context of fuel prices, efficiency, maintenance, and potential financial incentives. For those with access to affordable biomass fuel, the running costs can be competitive with, or even lower than, fossil fuel systems. Additionally, the environmental benefits of using a renewable energy source can also be a significant factor in the decision to choose a biomass boiler.
1. Coal: Both low-grade and high-quality coals are suitable. CFBC technology is particularly advantageous for burning low-grade coal with high ash or sulfur content, as it can capture pollutants effectively.
2. Biomass: Various forms of biomass, such as wood chips, sawdust, agricultural waste, and energy crops, can be used. Biomass is a renewable energy source and can help reduce carbon emissions.
3. Waste Fuels: Refuse-derived fuels (RDF), which are produced from the combustion of municipal solid waste, and industrial wastes can be used in CFBC boilers. This not only helps in waste management but also in energy recovery.
4. Petcoke: Petroleum coke, a byproduct of oil refining, is another fuel that can be utilized in CFBC boilers. Despite its high sulfur content, the CFBC process can capture sulfur effectively, reducing SO2 emissions.
5. Mixed Fuels: CFBC boilers can co-fire a combination of different fuels, allowing for flexibility based on fuel availability and cost. This can include a mix of coal and biomass, coal and petcoke, or other combinations.
6. Peat: In some regions, peat is a significant energy source and can be burned in CFBC boilers.
The capability to burn a wide range of fuels, including those that are considered waste or have low commercial value, makes CFBC boilers a versatile and environmentally friendly option for generating heat and power in a variety of settings, from utility power plants to industrial applications.
The efficiency of industrial biomass boilers can vary depending on several factors, but here’s a general range:
- New boilers: These can achieve efficiencies in the range of 70% to 85% depending on the specific fuel type and boiler design.(Taishan® biomass boilers High heat efficiency reach 90-92%)
- Wood pellets: Highest efficiency, around 94%
- Wet wood chips: Lower efficiency, around 80%
- Older boilers: Efficiency can be considerably lower, possibly dropping to 60% or even below due to wear and tear and less advanced technology.
Here’s a breakdown of the key factors affecting efficiency:
- Fuel Type: Dry wood pellets generally burn cleaner and more efficiently than wet wood chips with higher moisture content.
- Boiler Design: Modern boilers with features like advanced combustion chambers, optimized heat exchangers, and automated controls can achieve higher efficiency.
- Operating Conditions: Maintaining optimal boiler operation with proper fuel-to-air ratios and cleaning schedules ensures efficient combustion and heat transfer.
Here are some additional points to consider:
- Full Load vs. Partial Load: Most industrial boilers operate at varying loads throughout the day. Efficiency tends to be highest at full load and can drop at lower loads. Newer, larger boilers often have better control systems to minimize efficiency losses during partial load operation.
- Heat Recovery Systems: Some industrial biomass boilers can incorporate heat recovery systems that capture waste heat from flue gasses and use it for other processes, further improving overall efficiency.
If you’re interested in the efficiency of a specific type of industrial biomass boiler, it’s best to consult with the manufacturer or a qualified engineer. They can provide detailed information on the expected efficiency based on the fuel type, boiler model, and operating conditions.
1. High Initial Investment: The initial cost of setting up a CFB boiler can be higher than conventional pulverized coal-fired boilers due to its complex design and the need for additional equipment, such as cyclones for recirculating the bed material and advanced control systems.
2. Space Requirements: CFB boilers generally require more space due to their design and the need for auxiliary equipment, which can be a constraint in areas where space is limited.
3. Wear and Tear: The circulation of solid particles within the boiler can lead to higher levels of erosion and wear on boiler tubes and other components. This necessitates the use of more wear-resistant materials, which can increase maintenance costs.
4. Complexity in Operation and Maintenance: The operation and maintenance of a CFB boiler can be more complex compared to traditional boilers. Proper training and expertise are required to handle the sophisticated control systems and to manage the fluidized bed operation effectively.
5. Handling of Sorbents and Waste: The use of limestone or other sorbents to capture sulfur dioxide generates additional waste products, such as gypsum. This requires proper disposal or recycling mechanisms, which can add to the operational costs and complexities.
6. Fuel Quality Sensitivity: While CFB boilers are adaptable to various fuel types, changes in fuel quality (such as moisture content, size, and calorific value) can affect the combustion efficiency and require adjustments in operation to maintain performance.
7. Limited to Medium and Large Scale Applications: Due to their complexity and cost, CFB boilers are more suited to medium and large-scale applications and might not be economically viable for small-scale operations.
Despite these disadvantages, the environmental benefits and the ability to utilize a wide range of fuels often outweigh the drawbacks, making CFB technology a preferred choice for many industries and power generation applications seeking sustainable and flexible solutions.
Biomass boilers offer a range of advantages, particularly in terms of environmental sustainability, energy independence, and the potential for cost savings, making them an attractive option for heating and power generation in various settings. Here are some of the key benefits:
1. Renewable Energy Source
– Biomass boilers use organic materials for fuel, such as wood chips, pellets, or agricultural waste, which are renewable resources. This contrasts with fossil fuels, which are finite and contribute significantly to environmental degradation.
2. Reduced Carbon Footprint
– The combustion of biomass releases carbon dioxide, but the CO2 emitted is generally considered part of the carbon cycle, with plants absorbing the same amount of CO2 during their growth. This makes biomass a low-carbon energy source, helping to reduce greenhouse gas emissions when substituting fossil fuels.
3. Utilization of Waste Materials
– Biomass boilers can convert waste from agricultural, forestry, and industrial processes into energy, reducing waste disposal issues and potentially minimizing the environmental impact of waste.
4. Energy Independence
– Using locally sourced biomass to fuel boilers can reduce dependence on imported energy, enhancing energy security and supporting local economies. It provides a use for materials that might otherwise go to waste, contributing to a more sustainable energy ecosystem.
5. Economic Advantages
– In regions with readily available biomass resources, the fuel can be cheaper than fossil fuels, leading to cost savings over time. Moreover, biomass heating systems can create jobs in local supply chains, from fuel production to boiler maintenance.
6. Compatibility with Existing Heating Systems
– Biomass boilers can often be integrated into existing heating systems, making them a feasible retrofit option for reducing the carbon footprint of existing buildings.
7. Financial Incentives
– Many governments and institutions offer subsidies, grants, or tax incentives for renewable energy projects, including biomass heating systems, to encourage their adoption and make them more financially viable.
8. Support for Rural and Agricultural Communities
– Biomass energy production can provide additional revenue streams for farmers and those in rural communities, such as through the sale of wood chips, pellets, or other biomass materials.
9. Reduced Energy Costs in the Long Term
– While the initial setup costs for a biomass boiler can be high, the long-term savings on energy costs, especially where biomass fuels are inexpensive and plentiful, can be significant.
10. Environmental Certifications and Green Building Credits
– Projects utilizing biomass for heating can qualify for environmental certifications and green building credits, enhancing the sustainability profile of businesses and communities.
Conclusion
Biomass boilers represent a sustainable heating solution that aligns with global efforts to reduce carbon emissions and combat climate change. Their benefits extend beyond environmental advantages to include economic and energy independence considerations, making them a compelling choice for many applications. However, the decision to adopt biomass technology should be weighed against potential disadvantages and tailored to specific circumstances, including local availability of biomass fuels and the financial feasibility of installation and operation.
Higher Upfront Costs: Installation costs for biomass boilers are typically higher than traditional gas or oil boilers. This includes the boiler unit itself, installation labor, and potentially modifications to your existing heating system.
More Maintenance: Biomass boilers require more regular maintenance compared to gas or oil boilers. This includes tasks like:
- Ash removal: Biomass fuel generates ash that needs to be removed and disposed of regularly.
- Cleaning: Regular cleaning of the combustion chamber and other components is essential for optimal performance.
- System checks: Periodic inspections by a qualified technician are recommended to ensure safe and efficient operation.
Space Requirements: Biomass boilers and fuel storage take up more space than conventional boiler systems. You’ll need a dedicated area for storing the biomass fuel (pellets, chips, logs) and ensure it stays dry to maintain efficiency.
Air Quality Concerns: While considered renewable, burning biomass can still release pollutants like particulate matter and nitrogen oxides. These emissions can contribute to air quality issues, especially if the boiler isn’t functioning correctly or using low-quality fuel.
Fuel Availability and Cost: The availability and cost of biomass fuel can vary depending on your location. Transportation costs can significantly affect the overall cost-effectiveness, especially in areas without a local and sustainable source of wood pellets or chips.
Potential for Deforestation: Large-scale reliance on biomass energy raises concerns about unsustainable forestry practices that could lead to deforestation. It’s important to ensure the biomass fuel is sourced responsibly from managed forests.
Overall:
Biomass boilers can be a good option for those who prioritize a renewable heating source and have the space and budget for installation and maintenance. However, carefully consider the upfront costs, fuel availability, ongoing maintenance needs, and potential environmental impacts before making a decision. It might be helpful to consult with a local HVAC professional to assess your situation and compare the costs and feasibility with other heating systems.
1. Power Generation: Many power plants use CFB boilers for electricity production, taking advantage of their fuel flexibility to burn coal, biomass, or mixtures of fuels in a more environmentally friendly manner. This is especially valuable in regions with abundant biomass or low-grade coal resources.
2. Waste-to-Energy Plants: CFB technology is well-suited for burning municipal solid waste (MSW) or industrial waste to generate energy. These plants not only produce electricity but also significantly reduce waste volume, contributing to waste management efforts.
3. Pulp and Paper Industry: CFB boilers are used in the pulp and paper industry for generating steam required in various stages of the paper-making process. They can burn waste products from the process, such as bark and wood chips, making them a sustainable energy solution.
4. Chemical Industry: In the chemical manufacturing sector, CFB boilers provide steam and power needed for various chemical processes. They can also utilize by-product gases and waste as fuel, improving energy efficiency and reducing costs.
5. Cement Industry: The cement industry uses CFB boilers to generate the steam and power needed for cement production processes. Additionally, the CFB’s ability to use alternative fuels, such as petcoke and waste-derived fuels, is particularly beneficial for this energy-intensive industry.
6. Metal and Mining Industry: CFB boilers supply steam and power for metal processing and mining operations, including smelting and ore processing. Their fuel flexibility allows the use of locally available fuels, which can lower energy costs.
7. District Heating Systems: Some regions use CFB boilers in district heating systems to provide heat and hot water to residential and commercial buildings. This is particularly common in colder climates where efficient heating solutions are crucial.
8. Agricultural Industry: In regions with significant agricultural activity, CFB boilers can use crop residues and other biomass materials as fuel to generate steam and electricity, supporting sustainable agricultural practices.
The broad applicability of CFB boilers across these industries highlights their importance in supporting diverse energy needs while contributing to environmental sustainability and fuel flexibility.
Biomass boilers offer a renewable heating option, but they come with some drawbacks compared to conventional systems. Here’s a closer look at the disadvantages:
Higher Upfront Costs: Installation costs for biomass boilers are typically higher than traditional gas or oil boilers. This includes the boiler unit itself, installation labor, and potentially modifications to your existing heating system.
More Maintenance: Biomass boilers require more regular maintenance compared to gas or oil boilers. This includes tasks like:
- Ash removal: Biomass fuel generates ash that needs to be removed and disposed of regularly.
- Cleaning: Regular cleaning of the combustion chamber and other components is essential for optimal performance.
- System checks: Periodic inspections by a qualified technician are recommended to ensure safe and efficient operation.
Space Requirements: Biomass boilers and fuel storage take up more space than conventional boiler systems. You’ll need a dedicated area for storing the biomass fuel (pellets, chips, logs) and ensure it stays dry to maintain efficiency.
Air Quality Concerns: While considered renewable, burning biomass can still release pollutants like particulate matter and nitrogen oxides. These emissions can contribute to air quality issues, especially if the boiler isn’t functioning correctly or using low-quality fuel.
Fuel Availability and Cost: The availability and cost of biomass fuel can vary depending on your location. Transportation costs can significantly affect the overall cost-effectiveness, especially in areas without a local and sustainable source of wood pellets or chips.
Potential for Deforestation: Large-scale reliance on biomass energy raises concerns about unsustainable forestry practices that could lead to deforestation. It’s important to ensure the biomass fuel is sourced responsibly from managed forests.
Overall:
Biomass boilers can be a good option for those who prioritize a renewable heating source and have the space and budget for installation and maintenance. However, carefully consider the upfront costs, fuel availability, ongoing maintenance needs, and potential environmental impacts before making a decision. It might be helpful to consult with a local HVAC professional to assess your situation and compare the costs and feasibility with other heating systems.
1. Power Generation: Many power plants use CFB boilers for electricity production, taking advantage of their fuel flexibility to burn coal, biomass, or mixtures of fuels in a more environmentally friendly manner. This is especially valuable in regions with abundant biomass or low-grade coal resources.
2. Waste-to-Energy Plants: CFB technology is well-suited for burning municipal solid waste (MSW) or industrial waste to generate energy. These plants not only produce electricity but also significantly reduce waste volume, contributing to waste management efforts.
3. Pulp and Paper Industry: CFB boilers are used in the pulp and paper industry for generating steam required in various stages of the paper-making process. They can burn waste products from the process, such as bark and wood chips, making them a sustainable energy solution.
4. Chemical Industry: In the chemical manufacturing sector, CFB boilers provide steam and power needed for various chemical processes. They can also utilize by-product gases and waste as fuel, improving energy efficiency and reducing costs.
5. Cement Industry: The cement industry uses CFB boilers to generate the steam and power needed for cement production processes. Additionally, the CFB’s ability to use alternative fuels, such as petcoke and waste-derived fuels, is particularly beneficial for this energy-intensive industry.
6. Metal and Mining Industry: CFB boilers supply steam and power for metal processing and mining operations, including smelting and ore processing. Their fuel flexibility allows the use of locally available fuels, which can lower energy costs.
7. District Heating Systems: Some regions use CFB boilers in district heating systems to provide heat and hot water to residential and commercial buildings. This is particularly common in colder climates where efficient heating solutions are crucial.
8. Agricultural Industry: In regions with significant agricultural activity, CFB boilers can use crop residues and other biomass materials as fuel to generate steam and electricity, supporting sustainable agricultural practices.
The broad applicability of CFB boilers across these industries highlights their importance in supporting diverse energy needs while contributing to environmental sustainability and fuel flexibility.
Biomass fuel encompasses a broad range of organic materials that can be used to generate energy in biomass boilers and other bioenergy conversion systems. Here are some of the common types of biomass that can be used as fuel:
1. Wood Chips
– Source: Often a byproduct of logging operations, tree trimming, and sawmills.
– Use: Wood chips are widely used in industrial biomass boilers due to their relatively low cost and ease of handling and storage.
2. Wood Pellets
– Source: Made from compressed sawdust and other wood waste products.
– Use: Their uniform size, shape, and density make wood pellets a popular choice for both residential and industrial biomass boilers, as they burn more consistently and efficiently than larger pieces of wood.
3. Crop Residues
– Source: Agricultural byproducts such as straw, husks, and corn stalks.
– Use: These materials can be used directly as fuel or processed into briquettes or pellets, providing a use for agricultural waste while generating energy.
4. Energy Crops
– Source: Plants grown specifically for energy production, such as switchgrass, miscanthus, and short-rotation coppice woods like willow and poplar.
– Use: Energy crops are harvested and can be burned directly as fuel or processed into pellets or other forms for more efficient combustion.
5. Animal Manure and Poultry Litter
– Source: Waste products from livestock and poultry farming.
– Use: While often used in anaerobic digestion systems to produce biogas, these can also be dried and combusted directly in biomass boilers, though less commonly due to challenges with emissions and ash content.
6. Food Waste
– Source: Organic waste from food production, processing, and consumption.
– Use: Pre-treated food waste can be used in biomass boilers or anaerobic digesters. It’s a way to reduce waste while producing energy, although its use as boiler fuel is less common than other biomass sources.
7. Industrial Waste
– Source: Organic waste products from industrial processes, including wood waste, fabric, and paper.
– Use: Can be burned directly if clean and uncontaminated, or processed into fuel forms suitable for biomass energy systems.
8. Sawdust and Wood Scraps
– Source: Byproducts of woodworking and lumber processing.
– Use: Similar to wood pellets, sawdust and small wood scraps can be used directly in boilers or processed into denser fuel forms.
Considerations for Biomass Fuel Use
– Moisture Content: Affects combustion efficiency and heat output. Generally, drier biomass fuels yield more energy.
– Energy Density: Varies among different biomass types, affecting storage requirements and transportation costs.
– Ash Content: Influences maintenance needs, as higher ash content can lead to more frequent cleaning and potential issues with slagging and fouling of boiler components.
– Sustainability: The environmental impact of using biomass for energy depends on how the biomass is sourced and managed. Sustainable practices ensure that biomass use does not contribute to deforestation or compete with food production.
The choice of biomass fuel depends on local availability, cost, specific boiler technology, and environmental considerations.
Choosing the right biomass boiler for your industrial facility requires careful consideration of several factors. Here’s a breakdown of the key steps to guide you through the process:
1. Assess Your Heating Needs:
- Heat Output: Determine the required heating capacity for your facility in kilowatts (kW) or British Thermal Units (BTU) per hour. This will influence the size and power rating of the boiler you need.
- Hot Water Needs: Consider if you also need hot water generation for domestic or industrial processes alongside space heating.
2. Evaluate Fuel Availability and Costs:
- Research local suppliers: Identify potential suppliers of different biomass fuel types (pellets, chips, etc.) in your area.
- Compare fuel prices: Factor in transportation costs to get a clear picture of the overall fuel cost per unit of energy.
- Fuel quality: Ensure consistent access to high-quality fuel with appropriate moisture content for optimal boiler performance.
3. Consider Boiler Specifications:
- Fuel Type Compatibility: Choose a boiler designed for the type of biomass fuel you plan to use. Some boilers can handle multiple fuel options.
- Boiler Size and Efficiency: Select a boiler with the appropriate capacity to meet your heating needs and prioritize high-efficiency models to maximize fuel use.
- Automation Level: Decide on the desired level of automation for fuel feeding, ash removal, and system operation. Fully automatic systems offer convenience but come at a higher cost.
4. Regulations and Environmental Impact:
- Emissions Compliance: Ensure the boiler meets all local and regional air quality regulations regarding emissions.
- Sustainability Practices: Choose a boiler supplier that prioritizes sustainable sourcing of biomass fuels to minimize environmental impact.
5. Additional Considerations:
- Space Requirements: Biomass boilers and fuel storage require dedicated space. Factor this into your planning for boiler installation and fuel handling.
- Maintenance Needs: Regular maintenance is crucial for efficient operation. Understand the maintenance requirements and associated costs.
- Government Incentives: Research any available financial incentives or tax credits in your region for installing a biomass boiler system.
Here are some helpful tips for choosing a biomass boiler:
- Consult with experienced biomass boiler suppliers and engineers: They can assess your needs and recommend suitable boiler options based on your specific situation.
- Get quotes from multiple suppliers: Compare pricing, boiler specifications, and maintenance plans from different vendors.
- Consider long-term costs: Factor in not just the upfront boiler cost but also fuel costs, maintenance needs, and potential replacement parts over the boiler’s lifespan.
- Look for reliable and experienced boiler service providers: Having a reliable service team is crucial for ongoing maintenance and troubleshooting.
By carefully considering these factors and conducting thorough research, you can make an informed decision and choose the most suitable biomass boiler system for your industrial heating needs.
1. Fuel Type and Availability: Assess the types of fuel available for your application, including coal, biomass, industrial waste, or a mix. CFB boilers are known for their fuel flexibility, but the specific fuel characteristics (such as moisture content, ash content, and heating value) can impact the boiler design and efficiency.
2. Boiler Capacity and Efficiency: Determine the required boiler capacity, which is typically measured in tons of steam per hour or megawatts (MW) of power. The efficiency of the boiler in converting fuel into steam or electricity is also crucial, as higher efficiency leads to lower operating costs.
3. Emission Requirements: Identify the environmental regulations applicable to your location and industry. CFB boilers can significantly reduce sulfur dioxide (SO2) and nitrogen oxides (NOx) emissions, but the specific design may need to be tailored to meet stringent emission standards.
4. Operational Flexibility: Consider the need for operational flexibility, such as the ability to scale up or down based on demand, handle fuel quality variations, and quickly start up or shut down. CFB boilers offer good load-following capabilities, but specific requirements should be discussed with manufacturers.
5. Maintenance and Operating Costs: Evaluate the maintenance requirements and operating costs, including fuel, labor, and maintenance expenses. While CFB boilers may have higher initial costs, their ability to use cheaper, low-grade fuels can lead to lower overall operating costs.
6. Space Constraints: CFB boilers require more space than conventional boilers due to their design and the need for auxiliary equipment. Ensure you have adequate space for the boiler, including space for future maintenance and inspections.
7. Water Availability: Like all steam boilers, CFB boilers require a continuous supply of water for steam generation. Assess the availability and quality of water in your area, as it can affect the boiler’s operation and maintenance.
8. Long-term Sustainability: Consider the long-term sustainability of your fuel supply and the potential for future environmental regulations. Choosing a boiler that can adapt to different fuels or that can be easily upgraded for enhanced emissions control can be beneficial.
9. Manufacturer and Support: Select a manufacturer with a good track record in CFB technology, offering robust support and service. The availability of parts, technical support, and service can significantly impact the boiler’s operational efficiency and longevity.
10. Cost: While not the only factor, the cost of the boiler and the installation should be considered in the context of the expected operational savings and efficiency gains. A more expensive boiler that offers higher efficiency and lower emissions may justify its cost over its operational lifespan.
By carefully evaluating these factors and consulting with boiler manufacturers and experts, you can select a CFB boiler that meets your needs and offers reliable, efficient, and environmentally friendly operation.
- Fuel Type: Dry wood pellets generally burn cleaner and more efficiently than materials with higher moisture content.
- Boiler Design: Advanced features like optimized combustion chambers and heat exchangers contribute to higher efficiency.
- Operating Conditions: Maintaining proper fuel-to-air ratios and cleaning schedules ensures efficient fuel use.
- Full vs. Partial Load: Efficiency is highest at full boiler capacity and can drop slightly during partial load operation. Newer boilers may have features to minimize these losses.
Oil & Gas fired Boiler
An Oil & Gas fired boiler is a type of boiler that uses oil or gas as its fuel source. The basic operation of these boilers is similar to that of any other boiler type, where the fuel is combusted to heat water and produce steam or hot water for heating and industrial processes.
Oil & Gas fired boilers are crucial in residential heating, industrial processes, and power generation, offering a reliable and efficient source of heat when operated and maintained properly.
The operating costs of oil and gas-fired boilers can vary significantly based on several factors, making them more or less expensive to run in different contexts. Here are the key considerations:
1. Fuel Prices
– The cost of oil and gas fluctuates based on global market conditions, regional availability, and geopolitical factors. Generally, when fuel prices are high, the operating costs of these boilers increase correspondingly.
2. Efficiency
– The efficiency of a boiler determines how much fuel is converted into usable heat. Modern high-efficiency boilers can achieve efficiencies of 90% or more, meaning less fuel is wasted. Older or poorly maintained units may have significantly lower efficiencies, leading to higher fuel consumption and operating costs.
3. Boiler Size and Load
– Oversized or undersized boilers for the specific needs of a building or process can lead to inefficiencies. Additionally, boilers that frequently operate at partial load (not at full capacity) can be less efficient than those running at full load.
4. Maintenance
– Regular maintenance is essential for keeping a boiler running efficiently. Neglected boilers can face issues like scaling, soot buildup, and inefficient combustion, all of which can increase fuel consumption and operating costs.
5. Type of Fuel
– The choice between oil and gas can also affect operating costs, as these fuels typically have different prices. In many regions, natural gas is cheaper than oil, though this is not universally the case.
6. Environmental Regulations
– In some regions, there may be taxes or levies on certain fuels or emissions, which can affect the overall cost of running an oil or gas-fired boiler.
Comparison with Other Heating Options:
– When compared to electric heat pumps, oil and gas boilers may have higher operational costs due to the cost of fuel. However, they are often preferred in areas where the electricity supply is unreliable or where electricity prices are high.
– Compared to renewable energy sources like solar or wind power, which have lower operational costs once installed, oil and gas boilers have ongoing fuel expenses. However, boilers can provide consistent heating without reliance on weather conditions.
In conclusion, while oil and gas-fired boilers can be more expensive to run than some alternatives, especially during periods of high fuel prices, their actual operating costs depend on a variety of factors. Efficiency improvements, proper sizing, and regular maintenance can help mitigate these costs. For many applications, especially where high-temperature heat or steam is required, they remain a practical and reliable choice.
Oil and gas-fired boilers offer several advantages that make them popular choices for residential, commercial, and industrial heating requirements. Here are some of the key benefits:
1. High Energy Efficiency
– Modern oil and gas boilers are designed to achieve high levels of energy efficiency, often exceeding 90%. This means that a greater portion of the fuel used is converted into usable heat, reducing fuel consumption and lowering operating costs.
2. Reliability and Availability
– These boilers are known for their reliability and consistent performance. Oil and gas are widely available fuels in many regions, ensuring that these heating systems can be operated without interruption due to fuel scarcity.
3. Versatility
– Oil and gas-fired boilers can be used in a variety of applications, from small residential heating systems to large industrial processes that require steam or hot water. They can be designed to meet the specific needs of almost any application, including adjustable heat outputs and pressures.
4. Rapid Heating
– These boilers can produce heat very quickly from the time of ignition, making them ideal for situations where heat is needed on demand. This rapid response is particularly beneficial in industrial processes and residential heating during cold weather.
5. Cost-Effectiveness
– In regions where oil and gas prices are competitive, these boilers can be a cost-effective solution for heating. Initial installation costs can be higher than some alternatives, but the high efficiency and reliability of modern boilers can lead to lower overall operating costs.
6. Ease of Installation and Maintenance
– Oil and gas-fired boilers have been in use for many years, which has led to well-established standards for their installation and maintenance. A wide network of experienced service providers is available, making maintenance and repair services readily accessible.
7. Compatibility with Existing Systems
– Many existing heating systems are designed to be compatible with oil and gas-fired boilers, making them a straightforward choice for upgrades or replacements without the need for extensive modifications to heating distribution systems.
8. Environmental Options
– Newer models of oil and gas boilers are designed to be more environmentally friendly, with options for condensing technology that captures and reuses heat from exhaust gases, further improving efficiency and reducing emissions.
9. Scalability
– These boilers can be scaled up to meet the needs of large industrial facilities or scaled down for residential use, providing a flexible solution that can be tailored to the specific requirements of the user.
While oil and gas-fired boilers present these advantages, it’s important to also consider environmental impacts and the potential for fluctuating fuel prices. However, for many applications, the benefits of reliability, efficiency, and versatility make them a preferred choice.
While oil and gas-fired boilers offer several advantages, they also come with a set of disadvantages that are important to consider. Here are some of the key drawbacks:
1. Environmental Impact
– The combustion of oil and gas releases carbon dioxide (CO2), a greenhouse gas that contributes to climate change. Other emissions can include nitrogen oxides (NOx), sulfur dioxide (SO2), and particulate matter, which have various environmental and health impacts.
2. Fluctuating Fuel Prices
– The cost of oil and gas can vary significantly over time due to geopolitical events, changes in demand, and other factors. This can make the operating costs of oil and gas boilers unpredictable and potentially high.
3. Fuel Storage
– Oil-fired boilers require on-site storage of oil, which can pose a risk of spills or leaks. This requires careful management and can add to the overall footprint of the heating system.
4. Infrastructure and Supply Concerns
– Natural gas-fired boilers depend on the availability of a gas supply network, which may not be available in all areas. For oil, regular deliveries must be scheduled, and storage capacity needs to be managed.
5. Maintenance and Cleaning
– Oil and gas boilers require regular maintenance to operate efficiently and safely. This includes cleaning to remove soot and other residues that can accumulate and reduce efficiency. Maintenance and repair can add to the overall cost of operation.
6. Installation Costs
– The initial installation cost of an oil or gas boiler can be high, especially for systems that require extensive ductwork or piping. This can be a significant investment for homeowners or businesses.
7. Regulatory and Environmental Compliance
– In some regions, there are strict regulations regarding the installation and operation of oil and gas boilers due to their emissions. Compliance with these regulations can add to the cost and complexity of using these systems.
8. Long-Term Sustainability
– As the world moves towards cleaner energy sources, the long-term sustainability of relying on fossil fuels for heating is questionable. Investments in oil and gas boilers may face obsolescence as renewable energy technologies become more prevalent and affordable.
9. Space Requirements
– Boilers and their associated fuel storage can take up considerable space, which may be a limitation in densely populated areas or for facilities with limited available space.
Despite these disadvantages, oil and gas boilers remain a common choice for heating due to their reliability, efficiency, and the existing infrastructure in many places. However, the growing emphasis on reducing greenhouse gas emissions and improving air quality is leading to increased interest in alternative, more sustainable heating solutions.
The lifespan of an oil or gas-fired boiler can vary based on several factors, including the quality of the boiler, maintenance practices, and the intensity of its use. On average, you can expect a well-maintained oil or gas boiler to last between 15 to 30 years.
Key Factors Influencing Boiler Lifespan:
1. Quality of the Boiler:
– Higher quality boilers are typically built with better materials and engineering designs, which can extend their useful life.
2. Regular Maintenance:
– Regular servicing is crucial for maximizing the lifespan of a boiler. This includes tasks such as cleaning, checking for leaks, ensuring that the combustion process is efficient, and replacing worn parts. Proper maintenance can prevent small issues from turning into bigger problems that might shorten the boiler’s lifespan.
3. Operating Conditions:
– Boilers that operate under constant high demand or in harsh conditions may experience more wear and tear, potentially reducing their lifespan. Conversely, boilers operating under moderate conditions with periodic breaks tend to last longer.
4. Water Quality:
– The quality of water used in the boiler can have a significant impact on its lifespan. Hard water, which is high in minerals, can lead to scale buildup inside the boiler’s heat exchanger, reducing efficiency and potentially causing overheating and failure.
5. Installation:
– Proper installation by a professional is crucial for the longevity of a boiler. Incorrect installation can lead to operational issues and increased wear over time.
Signs It’s Time to Replace Your Boiler:
– Frequent Breakdowns: Regularly occurring issues might indicate that the boiler is nearing the end of its useful life.
– Increasing Energy Bills: If your energy costs are rising despite regular maintenance, it could be a sign that your boiler is losing efficiency.
– Difficulty Finding Replacement Parts: As boilers age, it can become harder to find parts, which can be a sign that it’s time for an upgrade.
– Visible Wear or Damage: Signs of rusting, leaks, or damage to the boiler itself or to the surrounding infrastructure can indicate that replacement is necessary.
While the average lifespan provides a general guideline, the actual longevity of a boiler will depend on the specific circumstances of its use and care. Investing in a high-quality boiler and adhering to a regular maintenance schedule are the best ways to ensure that you get the most years out of your investment.
Oil and gas-fired boilers are versatile and widely used across various sectors of industry due to their efficiency and capacity to provide high-pressure steam and hot water. Here are some of the key industries where these boilers play a crucial role:
1. Power Generation
– Used in power plants for generating steam that drives turbines to produce electricity. While coal-fired power plants are more common, oil and gas boilers are used in areas where those fuels are more readily available or as backup systems.
2. Manufacturing
– Essential in industries that require large amounts of steam or hot water for their processes, such as chemical manufacturing, food processing, textile, and paper manufacturing. They are used for heating, drying, sterilization, and in chemical reactions that require steam.
3. Petrochemical and Refineries
– Refineries use these boilers to generate steam and heat for distillation, cracking, and other processes critical in transforming crude oil into usable products like gasoline, diesel, and other chemicals.
4. Pharmaceuticals
– In the pharmaceutical industry, precise control of temperature and clean steam is crucial for the manufacturing of medications, sterilization of equipment, and other processes where contamination must be avoided.
5. Healthcare
– Hospitals and healthcare facilities use steam generated from boilers for sterilization of instruments, laundry, food service, and for creating a controlled environment in terms of humidity and temperature.
6. Hospitality and Commercial
– Large hotels, resorts, and commercial buildings utilize boilers for space heating, hot water supply, cooking, and laundry services.
7. Maritime
– Ships and offshore platforms use oil and gas-fired boilers for heating, propulsion, and power generation, especially in areas where other fuel types are not viable.
8. Agriculture
– Used for heating in greenhouses, processing of farm products, and in some cases, for irrigation through steam-powered equipment.
Advantages in Industrial Use:
– **Flexibility and Scalability:** These boilers can be scaled up to produce large amounts of steam or hot water as per industrial requirements.
– Efficiency: Modern designs and technologies have made oil and gas boilers more efficient, reducing fuel consumption and operational costs.
– Reliability: They offer a reliable heat source, critical for continuous industrial operations.
Challenges:
– Environmental Regulations: Stricter environmental regulations are pushing industries to adopt cleaner energy sources or to invest in emissions-reducing technologies for their boilers.
– Fuel Volatility: Fluctuations in oil and gas prices can significantly affect operational costs.
Despite these challenges, the efficiency, availability, and technological advancements in oil and gas-fired boilers continue to make them a preferred choice in many industrial applications.
Selecting the right oil or gas-fired boiler for your industrial application requires careful consideration of several factors. Here’s a breakdown of the key steps to guide you:
1. Assess Your Heating Needs:
- Heat Output: Determine the amount of heat required for your specific industrial processes. This will help size the boiler appropriately to avoid inefficiencies from an underpowered or oversized unit. A qualified HVAC professional can help you with this assessment.
- Fuel Availability and Cost: Consider the availability and pricing of natural gas compared to oil in your region. While gas is generally cheaper, oil might be the only option in some areas.
2. Boiler Efficiency:
- AFUE Rating: Look for boilers with a high Annual Fuel Utilization Efficiency (AFUE) rating. This indicates the percentage of fuel converted into usable heat, with higher ratings signifying better efficiency and lower operating costs. Condensing boilers, both gas and oil-fired, can achieve AFUE ratings exceeding 90%.
3. Boiler Type:
- Cast Iron Boilers: These traditional boilers are known for durability and can last over 30 years with proper care. However, they tend to be less efficient than newer models.
- Condensing Boilers: These high-efficiency boilers capture additional heat from exhaust fumes, leading to significant energy savings. They are a good choice for facilities with continuous heating demands.
- Hot Water vs. Steam Boilers: Hot water boilers are more common for most industrial applications due to their efficient heat transfer and safety features. Steam boilers might be suitable for specific high-temperature processes.
4. Additional Considerations:
- Maintenance Needs: Oil-fired boilers generally require more frequent maintenance compared to gas-fired models due to potential issues with the oil itself. Factor in maintenance costs when comparing options.
- Fuel Storage: If opting for an oil-fired boiler, consider the cost and space requirements for installing a dedicated oil storage tank.
- Environmental Regulations: Ensure the chosen boiler meets local regulations regarding emissions and environmental impact.
5. Consult a Professional:
- Our experienced professional can help you evaluate your heating needs, recommend suitable boiler options based on your requirements, and provide insights on factors like installation and maintenance considerations.
By following these steps and consulting with our professional, you can make an informed decision when choosing an oil or gas-fired boiler that meets your industrial heating needs efficiently and cost-effectively.
The cost of oil and gas-fired industrial boilers can significantly vary depending on a wide range of factors, including the boiler’s capacity, efficiency, design, and the specific requirements of the industrial process it will serve. Unlike residential boilers, industrial boilers are designed to handle much larger volumes of water and produce higher pressures and temperatures of steam, which can significantly influence their cost.
Initial Purchase Cost
– Small to Medium Capacity Boilers: For smaller industrial applications, costs can range from $10,000 to $50,000. These boilers typically have lower capacities and are suited for light manufacturing processes, small facilities, or as backup units.
– Large Capacity Boilers: For larger industrial operations, prices can start from $50,000 and can go up to several hundred thousand dollars for high-capacity, high-efficiency units that are essential for heavy manufacturing processes, large facilities, or power generation.
Factors Influencing Cost
– Capacity and Output: Industrial boilers are often customized to meet specific steam or hot water requirements, with higher capacities leading to higher costs.
– Efficiency: High-efficiency boilers, especially those designed to recover heat or to operate under condensing conditions, are more expensive but can lead to significant fuel savings over time.
– Design and Type: The design (fire tube vs. water tube), type (steam vs. hot water), and fuel flexibility can affect the price. Specialized designs for specific industrial processes can also increase costs.
– Installation and Setup: Installation costs for industrial boilers can be significant, including the setup of the boiler, integration into existing systems, construction of any necessary infrastructure like flue gas stacks, and compliance with environmental regulations.
– Operational Environment: Boilers designed to operate in harsh conditions or to handle corrosive or unusual fuels can be more expensive due to the need for specialized materials and designs.
– Regulatory Compliance: Compliance with emissions and safety regulations can add to the cost, requiring additional control systems and safety features.
Additional Costs
– Maintenance and Operation: Industrial boilers require regular maintenance to operate efficiently and safely. The complexity of the boiler and the quality of water used can influence maintenance costs.
– Fuel Storage and Handling: For oil-fired boilers, or gas-fired boilers in areas without a direct gas line, the cost for fuel storage and handling infrastructure needs to be considered.
– Energy Costs: The choice of fuel and the efficiency of the boiler will directly impact ongoing energy costs, which can be a significant part of the total cost of ownership.
Conclusion
Given the broad range of industrial applications and boiler specifications, obtaining a precise cost without specific details is challenging. For a detailed and accurate estimate, consultation with manufacturers or suppliers who can tailor a solution to the specific needs of the industrial process is essential. These professionals can provide comprehensive quotes that include the boiler, installation, and any additional components or services required.
Choosing between oil & gas-fired boilers and coal-fired boilers depends on several factors including environmental impact, cost, efficiency, and application requirements. Each type has its advantages and disadvantages based on these criteria. Here’s a comparison to help determine which might be better for specific needs:
Environmental Impact
– Oil & Gas Boilers: Produce fewer emissions compared to coal. Natural gas, in particular, burns cleaner than oil and coal, with significantly lower levels of sulfur dioxide (SO2), nitrogen oxides (NOx), and particulate matter.
– Coal Boilers: Generally have a higher environmental impact due to the higher carbon dioxide (CO2) emissions and other pollutants like SO2 and mercury. However, modern coal-fired boilers equipped with advanced emission control technologies can mitigate some of these effects.
Cost
– Oil & Gas Boilers: Operational costs can fluctuate based on the volatile prices of oil and gas. However, these boilers tend to have lower upfront costs compared to coal boilers equipped with advanced emission controls.
– Coal Boilers: Coal typically offers lower fuel costs, especially in regions with easy access to coal supplies. However, the initial investment might be higher due to the need for emission control systems and more complex fuel handling equipment.
Efficiency
– Oil & Gas Boilers: Tend to be more efficient than coal boilers. Modern gas-fired boilers can achieve efficiencies above 90%.
– Coal Boilers: Historically less efficient, but advancements in technology have improved the efficiency of new coal-fired boilers. However, achieving high efficiency often requires additional systems like superheaters, which can increase costs.
Application Requirements
– Oil & Gas Boilers:Are more versatile and can be used in a wide range of applications, from residential heating to large industrial processes. They are easier to operate and require less space.
– Coal Boilers: Are often used in industrial applications and power generation where high heat output is needed. They require more space for the boiler itself and for coal storage and handling.
Maintenance and Operation
– Oil & Gas Boilers: Generally require less maintenance than coal boilers, as they do not produce ash and have fewer soot and slag problems.
– Coal Boilers: Require more intensive maintenance due to ash production and the need for regular cleaning to maintain efficiency and operation.
Availability
– The availability of fuel can also be a determining factor. Regions with easy access to natural gas or oil may find that oil & gas boilers are more practical, while areas with abundant coal supplies might prefer coal boilers.
Conclusion
The choice between oil & gas-fired boilers and coal-fired boilers depends on the specific needs of the application, environmental regulations, fuel availability, and cost considerations. For residential and light commercial applications, oil & gas boilers are often preferred due to their efficiency, lower environmental impact, and ease of use. For industrial applications or in regions with low-cost coal, coal-fired boilers might be more economical, especially if equipped with modern pollution control technologies. Ultimately, the decision should be based on a comprehensive analysis of total operating costs, environmental impact, and regulatory compliance.
The working principle of oil and gas-fired boilers is relatively straightforward, yet it involves several key processes to efficiently convert fuel into heat. Here’s a breakdown of how these boilers operate:
1. Fuel Delivery
– For a gas-fired boiler, natural gas is supplied via a pipeline directly to the boiler. In the case of an oil-fired boiler, oil is pumped from a storage tank to the boiler.
2. Combustion
– The oil or gas fuel is mixed with air inside the burner. This mixture is then ignited by an electric igniter or pilot flame in the combustion chamber. The combustion process generates hot gases.
3. Heat Transfer
– The hot gases produced by the combustion process pass through a series of tubes or a heat exchanger. Water or another fluid circulates around these tubes or through the heat exchanger. The heat from the gases is transferred to the water, heating it up. This process effectively turns the water into hot water or steam, depending on the boiler’s purpose.
4. Circulation of Steam or Hot Water
– In the case of a steam boiler, the steam generated is circulated through pipes to radiators or to a process where heat is needed. The steam transfers its heat to the environment or process and condenses back into water. This water returns to the boiler to be reheated.
– In a hot water boiler, the heated water is circulated through a closed system where it releases its heat and is then returned to the boiler to be reheated.
5. Exhaust
– The combustion gases, after transferring their heat, are considered waste and need to be expelled. They are vented out of the boiler through a flue or chimney, thereby completing the combustion process.
Key Components Involved
– Burner: Mixes fuel with air and ignites it.
– Combustion Chamber: Where the fuel is burned to produce hot gases.
– Heat Exchanger: Transfers heat from the combustion gases to the water or steam.
– Pipes or Radiators: In a steam system, pipes carry steam to where heat is needed. In a hot water system, water circulates through radiators or a heating circuit.
– Controls: Including thermostats, pressure controls, and safety devices to regulate the boiler’s operation and ensure safety.
– Flue or Chimney: Expels combustion gases outside.
Efficiency and Environmental Considerations
Modern oil and gas-fired boilers are designed to achieve high levels of efficiency, often above 90%, meaning most of the energy in the fuel is converted into usable heat. They are also equipped with emission reduction technologies to minimize the environmental impact of the combustion process.
Coal Fired Boiler.
A coal-fired boiler is a type of boiler that burns coal as its fuel source to generate heat or steam for various industrial processes or heating applications. Coal-fired boilers are commonly used in power plants for electricity generation and in industrial settings such as factories, chemical plants, and refineries.
The basic principle of operation involves combustion of pulverized coal in a furnace, where the heat produced is used to convert water into steam. This steam then drives turbines connected to generators, producing electricity. In other applications, the steam generated by the coal-fired boiler may be used for heating purposes or to power various industrial processes.
Coal-fired boilers come in various configurations and designs, including:
1. Pulverized coal-fired boilers: Coal is ground to a fine powder and blown into the combustion chamber, where it burns efficiently.
2. Cyclone-fired boilers: Coal and air are mixed in a cyclone burner, where combustion occurs at high temperatures.
3. Fluidized bed boilers: Coal is burned in a bed of inert particles (such as sand or limestone) suspended by a stream of air or gas, allowing for efficient combustion and reduced emissions.
The core components of a CFB boiler include the combustion chamber, cyclone separators (to separate and recirculate the bed material), heat exchangers or boiler tubes (to absorb the heat generated by combustion), and control systems for managing air supply and fuel feed. The circulation of the bed material enhances heat transfer and ensures uniform temperature distribution within the combustion chamber, leading to efficient and clean combustion.
A coal-fired boiler works by burning pulverized coal to generate heat, which is then used to produce steam. Here’s a simplified explanation of how it operates:
1. Fuel Supply: Pulverized coal, typically in the form of fine powder, is fed into the boiler furnace through coal feeders. The coal may be stored in bunkers near the boiler for easy access.
2. Combustion: Inside the furnace or combustion chamber, the pulverized coal is mixed with combustion air (primary air) and ignited. The combustion process releases heat energy, raising the temperature of the furnace.
3. Heat Exchange: The heat generated from burning coal heats up water-filled tubes or pipes that run through the boiler. These tubes are surrounded by the hot gases produced by combustion. As the water absorbs heat, it begins to boil and turn into steam.
4. Steam Generation: The steam produced by the boiler is collected in a steam drum at the top of the boiler. The steam is then routed out of the boiler through piping to be used for various applications, such as powering turbines in a power plant, heating processes in industrial facilities, or providing steam for heating purposes.
5. Expansion and Energy Conversion: In power plants, the steam is directed through turbines, where it expands and causes the turbine blades to rotate. The rotating turbines are connected to generators, which convert the mechanical energy of the turbines into electrical energy. This electricity is then transmitted to the grid for distribution to consumers.
6. Cooling and Condensation: After passing through the turbines, the steam is condensed back into water in a condenser using cooling water. The condensed water is then returned to the boiler to be reheated and reused in the steam generation process, completing the cycle.
Throughout this process, various controls and safety mechanisms are in place to regulate the combustion process, maintain boiler pressure and temperature, and ensure safe and efficient operation.
It’s important to note that coal-fired boilers come in different configurations, such as pulverized coal-fired boilers, fluidized bed boilers, and cyclone-fired boilers, each with its own variations in design and operation. However, the basic principles of combustion, heat exchange, steam generation, and energy conversion remain consistent across these different types of boilers.
Coal-fired boilers do have some advantages, though their environmental drawbacks are significant and driving a shift towards cleaner energy sources. Here’s a breakdown of the pros:
Fuel Efficiency: Compared to other solid fuels like wood, coal packs more energy per unit volume. This translates to less frequent refueling for a coal boiler.
Reliable Heat Source: Coal is a dependable fuel source not impacted by weather fluctuations like solar or wind power. Coal-fired boilers can provide consistent heat around the clock.
Lower Fuel Cost (in some regions): In certain areas, coal can be a relatively inexpensive fuel source compared to other options. This can be a factor for industrial facilities.
Simpler Technology: Coal-fired boiler technology is well-established and understood. This can mean lower upfront costs and easier maintenance for experienced technicians.
Bulk Storage Potential: Coal can be stored relatively easily in large volumes without taking up excessive space and is resistant to pests or rot unlike firewood.
It’s important to note that the advantages of coal-fired boilers need to be weighed against their environmental consequences. Because of air and greenhouse gas emissions, regulations and a shift towards cleaner energy sources are making coal a less attractive option in many areas.
Coal-fired boilers also have several disadvantages, primarily related to their environmental impact and operational challenges:
1. Greenhouse Gas Emissions: Burning coal releases large amounts of carbon dioxide (CO2) and other greenhouse gases into the atmosphere, contributing to climate change and global warming. Coal-fired boilers are significant contributors to CO2 emissions, which are a major driver of climate change.
2. Air Pollution: Coal combustion emits various pollutants into the air, including sulfur dioxide (SO2), nitrogen oxides (NOx), particulate matter (PM), and hazardous air pollutants (HAPs) such as mercury and arsenic. These pollutants can have adverse effects on human health, ecosystems, and air quality, leading to respiratory problems, cardiovascular diseases, acid rain, and smog formation.
3. Ash Disposal and Waste Management: Coal combustion produces ash and other solid residues, which must be disposed of properly to prevent environmental contamination. Ash disposal can pose challenges due to the large volumes generated and the potential for leaching of toxic substances into soil and water bodies if not managed carefully.
4. Water Consumption and Pollution: Coal-fired power plants require large quantities of water for cooling purposes, which can strain local water resources and ecosystems, particularly in water-stressed regions. Additionally, wastewater discharges from coal-fired boilers may contain pollutants such as heavy metals and organic compounds, posing risks to aquatic life and water quality.
5. Coal Mining Impacts: The extraction and transportation of coal for use in boilers can have significant environmental and social impacts, including habitat destruction, land degradation, water pollution, and displacement of communities. Coal mining operations also contribute to deforestation, biodiversity loss, and greenhouse gas emissions from land-use changes.
6. Operational Challenges: Coal-fired boilers require regular maintenance and cleaning to ensure efficient and safe operation. Issues such as ash buildup, fouling of heat exchanger surfaces, and corrosion can affect boiler performance and reliability, leading to downtime and increased operating costs.
7. Limited Fuel Flexibility: While coal is abundant and relatively inexpensive, coal-fired boilers have limited flexibility in fuel selection compared to some other types of boilers. They are designed to burn coal efficiently and may require significant modifications to accommodate alternative fuels or renewable energy sources.
8. Regulatory Compliance and Costs: Coal-fired boilers are subject to stringent environmental regulations aimed at reducing emissions of pollutants and mitigating their environmental impact. Compliance with these regulations often requires the installation of costly pollution control technologies, which can increase the overall cost of coal-fired power generation.
Overall, the environmental and social impacts of coal-fired boilers underscore the need for transitioning to cleaner and more sustainable energy sources to mitigate climate change, improve air quality, and protect ecosystems and public health.
The life expectancy of a coal boiler can vary depending on various factors, including the quality of construction, maintenance practices, operating conditions, and technological advancements. Generally, well-maintained coal boilers can have a lifespan of 20 to 40 years or more. However, several factors can influence the longevity of a coal boiler:
1. Quality of Construction: The durability and longevity of a coal boiler depend on the quality of materials used in its construction and the adherence to engineering standards and specifications during manufacturing. High-quality components and robust construction can contribute to a longer lifespan.
2. Maintenance Practices: Regular maintenance and servicing are essential for prolonging the lifespan of a coal boiler. Proper maintenance includes cleaning, inspection, lubrication, and replacement of worn-out parts to prevent corrosion, fouling, and mechanical failures.
3. Operating Conditions: The operating conditions of a coal boiler, such as temperature, pressure, and load fluctuations, can affect its lifespan. Extreme operating conditions or frequent cycling between startup and shutdown can accelerate wear and tear on boiler components, reducing longevity.
4. Water Treatment: Proper water treatment is crucial for preventing corrosion, scale buildup, and fouling in coal boilers. Effective water treatment programs can extend the lifespan of boiler tubes, piping, and other components by minimizing the risk of damage from water-related issues.
5. Emissions Control: The implementation of emissions control technologies, such as flue gas desulfurization systems and particulate control devices, can impact the lifespan of a coal boiler. These technologies help reduce corrosion and fouling caused by acidic gases and particulate matter, thereby preserving boiler integrity.
6. Technological Advancements: Advances in boiler design, materials, and technology can enhance the efficiency, reliability, and lifespan of coal boilers. Upgrading older boilers with modern control systems and pollution control equipment can improve performance and extend their operational life.
7. Regulatory Compliance: Compliance with environmental regulations and emission standards may require retrofitting or upgrading coal boilers with pollution control equipment, which can affect their lifespan and operational costs.
It’s important for operators and owners of coal boilers to implement proactive maintenance strategies, monitor performance closely, and invest in necessary upgrades or replacements to ensure safe, efficient, and sustainable operation over the lifespan of the equipment. Additionally, as the energy industry transitions towards cleaner and more sustainable alternatives, the lifespan of coal boilers may be influenced by factors such as regulatory changes, market dynamics, and technological innovations in renewable energy and energy storage.
The efficiency of a coal-fired steam boiler can vary depending on factors such as the design of the boiler, the type of coal used, operating conditions, and the implementation of efficiency-enhancing technologies. Generally, coal-fired steam boilers can achieve thermal efficiencies ranging from 70% to over 90%, with modern, well-designed boilers typically performing at the higher end of this range.
Several factors contribute to the efficiency of a coal-fired steam boiler:
1. Boiler Design: The design of the boiler, including the arrangement of combustion chambers, heat exchange surfaces, and flow paths, plays a significant role in determining its efficiency. Modern boiler designs incorporate features such as high-efficiency heat exchangers, optimized combustion systems, and advanced control technologies to maximize thermal efficiency.
2. Combustion Efficiency: Efficient combustion of coal is critical for maximizing boiler efficiency. Factors such as proper fuel-air mixing, optimal combustion chamber design, and effective control of combustion parameters (such as excess air and fuel-to-air ratio) can improve combustion efficiency and reduce heat loss.
3. Heat Recovery: Coal-fired steam boilers often incorporate heat recovery systems, such as economizers and air preheaters, to capture waste heat from flue gases and preheat boiler feedwater. Heat recovery systems help increase overall efficiency by utilizing waste heat that would otherwise be lost to the environment.
4. Steam Generation Process: The efficiency of steam generation in a coal-fired boiler depends on factors such as steam pressure, temperature, and quality. Efficient steam generation systems optimize steam conditions to minimize energy losses during steam production and distribution.
5. Boiler Maintenance: Proper maintenance practices, including regular cleaning, inspection, and tuning, are essential for maintaining high boiler efficiency. Preventive maintenance helps ensure optimal boiler performance and reduces the risk of efficiency losses due to fouling, corrosion, or mechanical problems.
6. Pollution Control Equipment: Some pollution control technologies, such as selective catalytic reduction (SCR) and electrostatic precipitators (ESP), can also contribute to boiler efficiency by reducing flue gas emissions and minimizing energy losses associated with pollution control processes.
Overall, the efficiency of a coal-fired steam boiler can be influenced by various factors, and continuous efforts to optimize design, operation, and maintenance practices are essential for achieving and maintaining high levels of efficiency. Additionally, as the energy industry focuses on reducing greenhouse gas emissions and transitioning to cleaner energy sources, the development and adoption of advanced coal combustion technologies and carbon capture and storage (CCS) solutions may further improve the efficiency and environmental performance of coal-fired boilers.
Choosing the right coal-fired boiler requires careful consideration of several factors to ensure optimal performance, efficiency, reliability, and compliance with regulatory requirements. Here are some key steps to help guide the selection process:
1. Determine Requirements and Specifications: Define the specific requirements and specifications for the coal-fired boiler, including capacity, steam pressure and temperature, fuel type and quality, emissions limits, operational flexibility, and budget constraints. Consider factors such as the intended application (e.g., power generation, industrial heating), operating conditions, and regulatory compliance requirements.
2. Evaluate Boiler Types and Technologies: Assess different types of coal-fired boilers, such as pulverized coal-fired boilers, fluidized bed boilers, and cyclone-fired boilers, to determine which best meets your needs and preferences. Consider factors such as efficiency, emissions performance, fuel flexibility, reliability, and ease of maintenance.
3. Consider Fuel Characteristics: Evaluate the characteristics of the coal fuel available for use, including moisture content, ash content, heating value, particle size distribution, and sulfur content. Choose a boiler design and combustion system that can accommodate the specific fuel properties and optimize combustion efficiency while minimizing emissions.
4. Assess Efficiency and Performance: Compare the thermal efficiency, energy efficiency, and overall performance of different coal-fired boiler models and configurations. Consider factors such as heat transfer efficiency, combustion efficiency, steam generation capacity, turndown ratio, and operational flexibility to ensure optimal performance under varying operating conditions.
5. Review Emissions Control Technologies: Assess the availability and effectiveness of emissions control technologies for reducing air pollutants and greenhouse gas emissions from coal-fired boilers. Evaluate options such as flue gas desulfurization systems, particulate control devices, selective catalytic reduction (SCR), and electrostatic precipitators (ESP) to ensure compliance with regulatory requirements and minimize environmental impact.
6. Evaluate Operational and Maintenance Requirements: Consider the operational and maintenance requirements of different coal-fired boiler designs, including accessibility for inspection and servicing, ease of cleaning, availability of spare parts, and requirements for water treatment and ash disposal. Choose a boiler design that is reliable, easy to operate, and cost-effective to maintain over its lifespan.
7. Consult with Experts and Suppliers: Seek advice and guidance from boiler manufacturers, engineering firms, and industry experts to help evaluate options, analyze technical specifications, and make informed decisions. Consider factors such as supplier reputation, experience, technical support, and after-sales service when selecting a boiler supplier.
8. Consider Long-Term Sustainability: Take into account long-term sustainability considerations, such as future regulatory trends, environmental impact, energy security, and potential for future upgrades or retrofits. Choose a coal-fired boiler that aligns with your organization’s sustainability goals and can adapt to evolving market conditions and technology advancements.
By carefully considering these factors and conducting a comprehensive evaluation of available options, you can choose the most suitable coal-fired boiler for your specific requirements, ensuring efficient, reliable, and environmentally responsible operation over the long term.
Coal-fired boilers and gas-fired boilers differ primarily in the type of fuel they use and the combustion process involved. Here are some key differences between the two types of boilers:
1. Fuel Type:
– Coal-fired boiler: Burns pulverized coal as its primary fuel source. Coal is a fossil fuel that is abundant and widely available but produces higher emissions of greenhouse gases and air pollutants compared to natural gas.
– Gas-fired boiler: Burns natural gas or liquefied petroleum gas (LPG) as its primary fuel source. Natural gas is a cleaner-burning fossil fuel compared to coal, resulting in lower emissions of carbon dioxide (CO2), sulfur dioxide (SO2), nitrogen oxides (NOx), and particulate matter.
2. Combustion Process:
– Coal-fired boiler: Combustion of coal involves burning pulverized coal in a furnace or combustion chamber to generate heat. Coal combustion typically occurs at lower temperatures compared to gas combustion, requiring specialized combustion systems and emissions control technologies to optimize efficiency and reduce emissions.
– Gas-fired boiler: Combustion of natural gas or LPG involves mixing the gas with air and igniting it in a burner to produce a flame. Gas combustion occurs at higher temperatures compared to coal combustion, resulting in cleaner and more efficient combustion with lower emissions of pollutants.
3. Efficiency:
– Coal-fired boiler: Thermal efficiency of coal-fired boilers can vary but generally ranges from 70% to over 90%, depending on factors such as boiler design, operating conditions, and emissions control technologies.
– Gas-fired boiler: Gas-fired boilers typically have higher thermal efficiency compared to coal-fired boilers, with efficiencies ranging from 80% to over 95%, depending on the boiler design and operating parameters.
4. Emissions:
– Coal-fired boiler: Produces higher emissions of greenhouse gases (CO2) and air pollutants (SO2, NOx, PM) compared to gas-fired boilers. Requires emissions control technologies such as flue gas desulfurization (FGD), selective catalytic reduction (SCR), and particulate control devices to meet environmental regulations.
– Gas-fired boiler: Produces lower emissions of CO2, SO2, NOx, and PM compared to coal-fired boilers. Natural gas combustion emits fewer pollutants and requires less extensive emissions control compared to coal combustion.
5. Environmental Impact:
– Coal-fired boiler: Has a greater environmental impact due to higher emissions of greenhouse gases and air pollutants, as well as environmental impacts associated with coal mining, transportation, and disposal of ash and other solid residues.
– Gas-fired boiler: Has a lower environmental impact compared to coal-fired boilers, with cleaner combustion and lower emissions of pollutants. Natural gas is considered a cleaner-burning fossil fuel with fewer environmental drawbacks compared to coal.
Overall, the choice between coal-fired and gas-fired boilers depends on factors such as fuel availability, cost, emissions regulations, environmental considerations, and operational requirements. While coal-fired boilers offer certain advantages such as fuel availability and lower initial costs, gas-fired boilers are often preferred for their cleaner combustion, higher efficiency, and lower emissions profile.
The cost of a circulating fluidized bed (CFB) boiler can vary significantly depending on several factors. Here’s a breakdown of what influences the price:
- Boiler Capacity: The size and steam generation capacity of the boiler is a major cost driver. Larger boilers for industrial power generation will naturally cost more than smaller units for district heating applications.
- Fuel Type: Boilers designed for specific fuels like low-grade coal or biomass might have different material requirements and features compared to standard coal-fired CFBs, impacting the cost.
- Emission Control Requirements: Depending on your location’s air quality regulations, additional emission control equipment like scrubbers or selective non-catalytic reduction (SNCR) systems might be necessary, adding to the overall cost.
- Manufacturer and Features: The reputation and experience of the boiler manufacturer can influence the price. Additionally, boilers with advanced features like automated controls or specialized designs for specific fuels might have a higher cost.
While specific pricing information can be difficult to find publicly due to customization involved, here’s a general range to provide an idea:
- Small-scale CFB boilers (few megawatt capacity): $10,000 – $200,000 [1] (This range might be on the lower end and may not consider all the factors mentioned above).
- Industrial-scale CFB boilers (tens to hundreds of megawatt capacity): $ Costs can range from millions to tens of millions of dollars depending on the capacity and complexity.
Here are some recommendations to get a more accurate estimate for your project:
- Contact CFB Boiler Manufacturers: Reach out to reputable CFB boiler manufacturers and request quotes based on your specific requirements (capacity, fuel type, emission regulations).
- Consider Consulting Firms: Engineering consulting firms specializing in power generation or industrial processes can provide valuable insights into CFB boiler selection and cost estimation for your project.
Remember, the initial cost is just one aspect. When evaluating the economics of a CFB boiler, consider factors like:
- Fuel Efficiency: A highly efficient boiler can save on fuel costs over time.
- Maintenance Needs: Compare maintenance requirements and potential costs between different boiler options.
- Operational Lifetime: A CFB boiler with a long lifespan can provide a better return on investment.
By carefully considering all these aspects, you can choose a CFB boiler that offers the best value proposition for your specific needs and ensures a cost-effective and environmentally friendly solution for your industrial application.
For more information about pricing, please contact us. Our professional engineers will provide you with a more accurate quotation based on your project.
There are three major types of coal-fired boilers, each with their own design and operational characteristics:
Stoker-fired boilers:
- In stoker-fired boilers, the coal is fed into the furnace by a mechanical grate system.
- The grate system continuously moves the coal through the furnace, ensuring efficient burning.
- Stoker-fired boilers are available in a variety of sizes and can be used for industrial, commercial, and institutional applications.
- They are relatively simple in design and have lower upfront costs compared to other boiler types.
- However, stoker-fired boilers tend to have lower efficiency and higher emissions compared to other coal-fired boiler types.
Pulverized coal-fired boilers:
- Pulverized coal-fired boilers are the most common type of large coal-fired boiler used in power plants.
- In these boilers, the coal is pulverized into a fine powder before being injected into the furnace.
- The fine particles of coal burn more efficiently than larger chunks, resulting in higher boiler efficiency and lower emissions compared to stoker-fired boilers.
- Pulverized coal-fired boilers are also capable of achieving higher operating temperatures and pressures, which can further improve efficiency and power generation.
- However, pulverized coal-fired boilers are more complex and expensive than stoker-fired boilers due to the need for coal grinding equipment.
Fluidized bed combustion (FBC) boilers:
- Fluidized bed combustion (FBC) boilers are a relatively new type of coal-fired boiler that offers several advantages over traditional stoker-fired and pulverized coal-fired boilers.
- In FBC boilers, the coal is burned in a bed of sand or limestone particles that are fluidized by air flowing upwards through the bed.
- The fluidized bed allows for more uniform combustion and efficient heat transfer.
- FBC boilers also have lower emissions compared to other coal-fired boiler types because the limestone in the bed can capture sulfur oxides from the burning coal.
- However, FBC boilers are typically more expensive than stoker-fired boilers and may have slightly lower efficiency compared to pulverized coal-fired boilers.
Waste Heat Recovery Boiler
A waste heat recovery boiler (WHRB) is a device that captures heat energy that would otherwise be wasted in industrial processes. This captured heat is then used to generate steam or hot water which can be used for a variety of purposes, such as heating buildings, generating electricity, or driving other industrial processes.
Waste Heat Recovery Boilers (WHRBs) offer several significant advantages, particularly in terms of energy efficiency, cost savings, and environmental benefits. Here are some of the key advantages:
1. Energy Efficiency Improvement: WHRBs capture and reuse heat that would otherwise be wasted, thereby reducing the energy required to produce steam or hot water from scratch. This enhances the overall energy efficiency of the facility.
2. Cost Reduction: By generating steam or hot water that can be used in various industrial processes or for power generation, WHRBs reduce the need for additional fuel, leading to substantial cost savings on energy bills.
3. Reduced Environmental Impact: Reusing waste heat helps in lowering greenhouse gas emissions and other pollutants, since less fuel combustion is required. This contributes significantly to an organization’s efforts to meet environmental regulations and sustainability goals.
4. Increased System Efficiency: Integrating a WHRB can increase the efficiency of the primary equipment by cooling the exhaust gases. This can extend the life of equipment by reducing the thermal stress and maintenance requirements.
5. Flexibility and Versatility: WHRB systems can be designed to work with a variety of heat sources and can be customized to meet the specific needs of different industries, making them a versatile solution across multiple sectors.
6. Economic Payback: While the initial investment for a WHRB system can be significant, the economic payback through reduced energy costs can be quite favorable, often within a few years, depending on the specific application and operational efficiency.
7. Enhancement of Energy Security: By reducing dependence on external energy sources and maximizing on-site energy generation, WHRBs enhance energy security for industrial operations.
These benefits make WHRBs an appealing option for industries looking to improve their operational efficiencies and environmental impact while reducing operational costs.
While Waste Heat Recovery Boilers (WHRBs) offer numerous benefits, they also have some disadvantages and limitations that may affect their implementation and effectiveness in certain situations. Here are some of the key drawbacks:
1. High Initial Investment: The upfront cost of installing a WHRB can be significant, including the cost of the boiler itself, additional infrastructure, and integration into existing systems. This initial investment can be a barrier for some organizations, especially small to medium enterprises.
2. Maintenance Requirements: WHRBs require regular maintenance to operate efficiently and safely. This includes cleaning, inspection, and repair of heat exchanger surfaces and other components, which can add to operational costs.
3. Complexity of Design and Integration: Designing and integrating a WHRB into existing industrial processes can be complex. It requires careful planning to ensure compatibility with existing equipment and processes, and may sometimes require modifications to existing systems.
4. Dependence on Waste Heat Availability: The effectiveness of a WHRB is directly dependent on the availability and temperature of waste heat. In processes where waste heat is intermittent or at a low temperature, the effectiveness and efficiency of the WHRB can be significantly reduced.
5. Space Requirements: Installing a WHRB often requires additional space, which might be a constraint in facilities with limited physical area.
6. **Economic Viability Dependent on Fuel Costs**: The economic return of a WHRB project is often linked to fuel costs. In scenarios where fuel costs are low, the payback period for the initial investment might extend, reducing the economic attractiveness of such projects.
7. Potential for Increased Operating Costs: If not properly designed or maintained, WHRBs can introduce inefficiencies into the system, potentially increasing rather than decreasing operating costs.
8. Risk of Corrosion and Scaling: The boiler tubes and other components in a WHRB are susceptible to corrosion and scaling from the waste gases and fluids, which can impair heat transfer efficiency and lead to failures or leaks.
Despite these challenges, many industries find that the long-term benefits of WHRBs, such as reduced energy costs and environmental impact, outweigh the disadvantages, particularly in sectors with high energy consumption and suitable waste heat sources.
A waste heat recovery boiler (WHRB) works by capturing heat energy that would normally be lost in exhaust gases from industrial processes and using it to generate steam or hot water. Here’s a breakdown of the process:
Hot Exhaust Stream: The process starts with hot exhaust gases being emitted from an industrial source like a furnace, engine, or incinerator. These gases can reach temperatures in the hundreds or even thousands of degrees Celsius.
Heat Transfer via Tubes: The hot exhaust gases are then channeled into the WHRB system, where they flow through a series of tubes made of a heat-resistant material.
Heat Absorption by Working Fluid: Surrounding these tubes is a working fluid, typically water. The water circulates around the tubes, absorbing heat from the hot exhaust gases by conduction through the metal tubes.
Steam Generation or Hot Water Use: The heated water from step 3 can be used in two ways:
- Steam Generation: If steam is required, the hot water is further heated in a chamber within the WHRB until it boils and turns into steam. This steam can then be used for various purposes like power generation, heating buildings, or industrial processes.
- Direct Hot Water Use: Alternatively, if hot water is sufficient for the application, the heated water from step 3 can be used directly without converting it to steam. This hot water can be used for tasks like space heating, cleaning, or specific industrial processes requiring hot water.
Cooled Exhaust: After transferring heat to the working fluid, the exhaust gases are significantly cooler. These cooled exhaust gases are then released from the WHRB system through a stack and vented out to the atmosphere.
By capturing this waste heat, WHRBs significantly improve the overall efficiency of industrial operations. Imagine all that thermal energy just going up the smokestack – a WHRB captures it and puts it to good use!
Common types of waste heat recovery boilers mainly include the following:
1. Based on Installation Type: These are classified into horizontal and vertical waste heat boilers. Horizontal boilers are characterized by their simple structure and ease of maintenance, but they have a small evaporation capacity, low steam pressure, and slow water circulation, typically used for small and medium-sized waste heat boilers. Vertical boilers have fast water circulation speeds and high heat transfer rates, featuring large steam spaces and high evaporation capacities, mainly used for large-scale waste heat boilers that recover substantial amounts of heat and operate at high steam pressures.
2. Based on the Characteristics of the Steam-Water Circulation System: There are natural circulation waste heat boilers and forced circulation waste heat boilers. Natural circulation waste heat boilers do not require a circulation pump, relying on the driving force generated by the density difference between the downcomers and risers to achieve steam-water circulation, which is relatively reliable. Forced circulation waste heat boilers use an external circulation pump to drive the steam-water circulation, consuming energy when the boiler operates.
3. Based on Structural Features: There are shell and tube waste heat boilers and flue-type waste heat boilers. Shell and tube waste heat boilers use wall heat exchange between high-temperature process gases and the water inside the boiler to produce steam, similar to shell and tube heat exchangers, and are widely used. Flue-type waste heat boilers use high-temperature industrial gases passing through flues made of non-metallic materials, heat exchange tube bundles set in the flues, and water walls to produce steam, recovering heat from high-temperature process gases, similar to the flue structures of conventional boilers.
4. Based on Boiler Pressure: There are low-pressure, medium-pressure, and high-pressure waste heat boilers.
– Low-pressure waste heat boilers: 0.1MPa ≤ p < 1.6MPa
– Medium-pressure waste heat boilers: 1.6MPa ≤ p < 10.0MPa
– High-pressure waste heat boilers: 10.0MPa ≤ p < 100MPa
5. Based on Industry Use: These include cement kiln waste heat boilers, sintering machine waste heat boilers, catalytic cracking waste heat boilers, chemical waste waste heat boilers, waste incineration waste heat boilers, ferrosilicon industry waste heat boilers, titanium dioxide industry waste heat boilers, sulfuric acid waste heat boilers, turbine waste heat boilers, coke dry quenching waste heat boilers, and others.
Waste heat recovery boilers (WHRBs) are a versatile technology used across various industries due to their ability to capture wasted thermal energy and convert it into usable steam or hot water. Here are some of the most common industrial applications of WHRBs:
Power Generation: In co-generation plants, WHRBs capture waste heat from engines or turbines to generate steam. This steam then drives turbines for electricity production, promoting efficient combined heat and power (CHP) systems.
Steel Mills: The steel production process generates a significant amount of high-temperature exhaust gas. WHRBs in steel mills recover this heat to create steam for various purposes within the plant, such as powering processes, heating buildings, or even generating electricity on-site.
Cement Plants: Similar to steel mills, cement production involves high-temperature processes that release substantial waste heat. WHRBs in cement plants capture this heat to generate steam for powering kilns or drying processes.
Chemical Plants: Chemical reactions often generate considerable heat. WHRBs in chemical plants capture this waste heat to produce steam or hot water for distillation, concentration, or other processes requiring thermal energy.
Refineries: Oil refineries involve numerous high-temperature processes. WHRBs can recover waste heat from these processes to generate steam for powering distillation units, crackers, or other refinery operations.
Glass Manufacturing: Glass production utilizes high-temperature furnaces. WHRBs capture waste heat from these furnaces to generate steam or hot water for preheating raw materials or other glass manufacturing processes.
Food Processing: Some food processing applications, like drying or sterilization, require hot water or steam. WHRBs can capture waste heat from boilers or ovens used in food processing to generate hot water or steam, reducing reliance on primary fuel sources.
Paper and Pulp Mills: Paper and pulp production involves processes like drying and pulping that require thermal energy. WHRBs can capture waste heat from various stages of the process to generate steam or hot water for these applications.
Textile Industry: Textile manufacturing often utilizes heat for drying fabrics or setting dyes. WHRBs can capture waste heat from boilers or other processes to generate hot water for these applications.
Overall, WHRBs offer a cost-effective and environmentally friendly solution for various industries by harnessing what would otherwise be wasted thermal energy. Their widespread use across these sectors highlights their potential for improving industrial efficiency and sustainability.
Selecting the right waste heat recovery boiler (WHRB) requires careful consideration of several factors to ensure it aligns with your specific needs and offers optimal performance. Here’s a breakdown of the key steps involved in choosing a WHRB:
Evaluate Heat Source:
- Temperature: Analyze the temperature of your exhaust gas stream. This is crucial as WHRB effectiveness is highly dependent on the available waste heat temperature. Higher temperatures generally translate to more recoverable heat and potentially higher boiler efficiency.
- Flow Rate: Assess the volume or flow rate of the exhaust gases. A WHRB needs to be sized appropriately to handle the expected exhaust gas volume for optimal heat transfer.
- Composition: Identify any contaminants or corrosive elements present in the exhaust stream. The WHRB material selection and design may need to consider corrosion resistance to ensure durability.
Determine Steam or Hot Water Needs:
- Application: Clearly define whether you require steam or hot water from the WHRB. This will influence the selection of boiler type (steam generating or hot water) and the required output temperature and pressure.
- Consumption: Estimate the amount of steam or hot water your facility needs. Sizing the WHRB to meet your consumption demands is essential for efficient operation and avoiding unnecessary capacity.
Economic Analysis:
- Investment Cost: Consider the initial investment cost of the WHRB system, including equipment, design, and installation.
- Operational Costs: Factor in ongoing operational costs like maintenance, fuel savings due to waste heat utilization, and potential water treatment needs.
- Payback Period: Estimate the time it takes for the cost savings from the WHRB to offset the initial investment. A shorter payback period indicates a more financially attractive proposition.
Space Constraints:
- Boiler Footprint: Evaluate the available space at your facility to accommodate the WHRB system. Recuperative boilers tend to be more compact, while regenerative boilers may require more space due to their valve systems and chambers.
Expertise and Maintenance:
- Technical Support: Consider the availability of qualified personnel to operate and maintain the WHRB system. Some manufacturers may offer training or service packages.
- Maintenance Requirements: Understand the ongoing maintenance needs of the chosen WHRB technology to ensure optimal performance and prevent issues.
Regulations and Permits:
- Environmental Compliance: Research any local regulations or permits required for installing and operating a WHRB system. Ensure the chosen boiler meets environmental compliance standards.
Consulting with experienced WHRB manufacturers and engineers is highly recommended during the selection process. They can provide valuable insights based on your specific requirements and help you choose the most suitable WHRB technology for your application.
By carefully considering these factors, you can make an informed decision when selecting a waste heat recovery boiler that optimizes efficiency, meets your operational needs, and delivers a good return on investment.
The cost of a waste heat recovery boiler (WHRB) can vary significantly depending on several factors, making it difficult to provide a fixed price range. Here’s a breakdown of the key elements that influence WHRB cost:
Boiler Type: Recuperative boilers are generally less expensive than regenerative boilers due to their simpler design. Regenerative boilers, while offering higher efficiency, involve more complex components like rotating valves and heat storage chambers, leading to a higher price tag.
Size and Capacity: Larger WHRBs designed to handle higher exhaust gas volumes and generate more steam or hot water will naturally cost more than smaller units.
Material Selection: The materials used in the boiler construction can impact the cost. Higher-grade materials chosen for durability in corrosive environments will add to the overall cost.
Manufacturer and Features: Different manufacturers may offer WHRBs at varying price points depending on their brand reputation, included features, and warranties.
Customization Needs: Any custom design requirements or modifications to suit a specific application will add to the overall cost.
While specific prices can’t be quoted here, some general indications can be gleaned from online resources. Here’s a ballpark range to consider, keeping in mind these are estimates and actual costs can differ:
- Low-Range: Simpler WHRBs for smaller applications might start around $6,300 (USD) depending on the source.
- Mid-Range: Industrial WHRBs for typical applications may range from $50,000 to $200,000 (USD) or more.
It’s important to remember that the initial cost of a WHRB is just one part of the equation. The long-term operational savings from reduced fuel consumption and improved efficiency can be significant. A feasibility study considering your specific situation is crucial to determine the payback period and assess the overall cost-effectiveness of a WHRB for your facility.
For a more accurate estimate on a WHRB system, it’s advisable to consult directly with WHRB manufacturers and obtain quotes based on your specific requirements like exhaust gas characteristics, desired steam/hot water output, and any customization needs.
A Waste Heat Recovery Boiler (WHRB) consists of several key components, each playing a crucial role in the efficient recovery of waste heat and conversion into usable energy. Here’s a breakdown of the main components:
1. Heat Exchanger: The core component where the transfer of heat from the waste gases to the water or steam occurs. It can be designed as a bundle of tubes through which hot gases flow while water circulates around them, or vice versa, depending on whether it’s a fire-tube or water-tube boiler.
2. Burner (if applicable): In some WHRBs, especially those used in conjunction with lower temperature waste gases, a supplementary burner may be included to boost the temperature of the gases before they enter the heat exchanger.
3. Economizer: Often used to preheat the feedwater entering the boiler using residual heat from the flue gases. This component enhances the overall efficiency of the system by reducing the energy needed to bring the water up to boiling point.
4. Superheater: This component increases the temperature of the steam produced by the boiler above its saturation point, without increasing the pressure. This dry steam is particularly useful for power generation and industrial processes requiring high-quality steam.
5. Air Preheater: Utilizes the waste heat to preheat the air entering the combustion chamber, improving the efficiency of the burner and reducing fuel requirements.
6. Evaporator: This is where the phase change from liquid to vapor (water to steam) occurs. It is a crucial component that handles the primary thermal load of converting water into steam using the recovered heat.
7. Condenser: Not present in all WHRB systems, but when used, it condenses the exhaust steam from a turbine back into water that can be reheated and turned back into steam, enhancing the system’s efficiency through recirculation.
8. Boiler Drums and Headers: These are pressure vessels that serve as reservoirs for steam and water. They help to separate steam from water and distribute feedwater and steam to different parts of the boiler.
9. Control Systems: Automated systems that monitor and regulate the operation of the boiler, including temperature, pressure, and flow rates to ensure efficient and safe operation.
10. Safety Valves and Gauges: Essential for preventing overpressure conditions which could lead to explosions. Safety valves release steam if the pressure becomes too high, while gauges allow operators to monitor the boiler’s operational parameters.
11. Blowdown Tank: Used to periodically remove water from the boiler to control the concentrations of dissolved minerals and impurities, helping to prevent scaling and corrosion.
12. Stack: A chimney that allows exhaust gases to exit the system once they have passed through the boiler. It plays a critical role in ensuring proper draft to remove gases efficiently.
These components work together to ensure that the WHRB operates efficiently, safely, and effectively, converting waste heat into useful thermal energy or steam.
The efficiency of a waste heat recovery boiler (WHRB) refers to how effectively it captures usable heat from the exhaust gases and converts it into steam or hot water. Here’s the approach commonly used to calculate WHRB efficiency:
Efficiency Formula:
The most common formula used to calculate WHRB efficiency is:
η = 100 - (q2 + q3 + q4 + q5 + q6)
where:
- η (eta) represents the WHRB efficiency as a percentage.
- q2, q3, q4, q5, and q6 represent the heat losses from the boiler system expressed in kW or another unit of power.
Heat Loss Breakdown (q terms):
These terms account for various heat losses that occur within the WHRB, reducing the overall efficiency:
- q2 (Flue Gas Losses): This represents the heat carried away by the cooled exhaust gases exiting the WHRB stack.
- q3 (Incomplete Combustion Losses): This accounts for any unburned fuel present in the exhaust gases due to incomplete combustion in the primary process.
- q4 (Solid Incomplete Combustion Losses): This applies to specific cases where solid fuels are used, and some unburned solid particles are carried over with the exhaust gases.
- q5 (Heat Radiation Losses): This represents heat lost to the surrounding environment through radiation from the boiler surfaces.
- q6 (Slag and Ash Physical Losses): This term is relevant for WHRBs handling exhaust gases with slag or ash particles. It accounts for the heat carried away by these physical materials exiting the boiler.
Data Requirements:
To calculate WHRB efficiency using this formula, you’ll need data for:
- Mass flow rate of the working fluid (water) through the boiler (m_dot_w).
- Specific heat capacity of the working fluid (water) (cp_w).
- Inlet and outlet temperatures of the working fluid (T_w1 and T_w2).
- Mass flow rate of the fuel used in the primary process (m_dot_f) (assumed for simplicity). This might not be directly applicable depending on the WHRB setup.
- Enthalpy of vaporization of the fuel (h_fg) (assumed for simplicity). This might not be directly applicable depending on the WHRB setup.
Alternative Efficiency Calculation (for specific cases):
If the focus is on the heat output specifically delivered to the working fluid, an alternative approach can be used:
η_whrb = (Q_out / Q_in) * 100
where:
- η_whrb represents the WHRB efficiency as a percentage in this specific context.
- Q_out represents the heat gained by the working fluid (water), calculated using its mass flow rate, specific heat capacity, and temperature change.
- Q_in represents the heat input, which can be estimated based on the fuel mass flow rate and its enthalpy of vaporization (assuming all heat goes to the exhaust gases).
Importance of Efficiency:
A higher WHRB efficiency signifies that the boiler is capturing a larger portion of the available waste heat and converting it into usable thermal energy. This translates to greater operational benefits like:
- Reduced fuel consumption for steam or hot water generation.
- Lower energy costs for your facility.
- Minimized environmental impact by utilizing waste heat and reducing reliance on fossil fuels.
Who Performs the Calculations?
WHRB efficiency calculations are typically performed by engineers specializing in thermodynamics or thermal systems. They can assess the specific WHRB design, measure or obtain relevant data points, and apply the appropriate formula to determine the efficiency.
In conclusion, calculating WHRB efficiency requires understanding the heat loss components and having access to specific data about the boiler operation and working fluid. While the formulas may seem complex, consulting with WHRB specialists or manufacturers can help you determine the efficiency of your system and identify areas for improvement.
sales@www.coalbiomassboiler.com
Phone
Office. 0086-538-6619637
Office. 0086-538-6619632
Mob. +86-18661318800
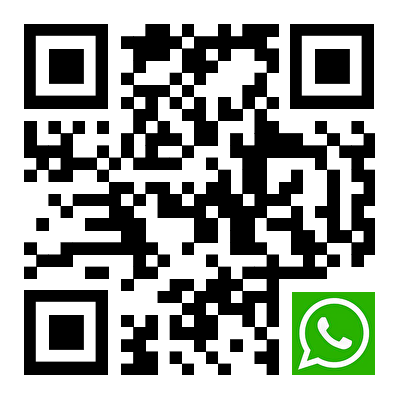
+86-18661318800
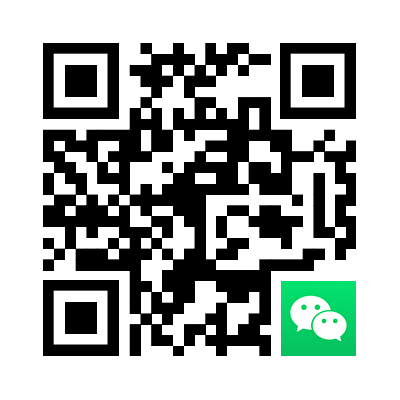
+86 18661318800
Address
No. 1169 Beitianmen Street, High-tech Zone, Taian, Shandong, China