Circulating Fluidized Bed (CFB) boilers are renowned for their fuel flexibility, low emissions, and high combustion efficiency. But despite their adaptability, not all fuels behave the same within a CFB system. If fuel types and combustion properties are not properly evaluated, users may face slagging, incomplete combustion, excessive wear on components, or poor thermal performance. To optimize system design, cost-efficiency, and environmental compliance, it’s essential to understand how different fuels affect CFB boiler selection and operation.
Fuel types and combustion characteristics affect your choice of a Circulating Fluidized Bed boiler by influencing bed temperature, fluidization behavior, combustion stability, ash handling systems, and emission control strategies. CFB boilers are designed to accommodate a wide range of fuels—such as low-grade coal, biomass, petroleum coke, and industrial waste—but factors like calorific value, particle size, moisture content, sulfur levels, and ash properties determine the exact configuration of the combustion chamber, bed material, and air supply systems. A poor fuel-to-boiler match can reduce efficiency and increase operating costs.
Choosing a CFB boiler starts with understanding your fuel’s behavior under fluidized conditions.
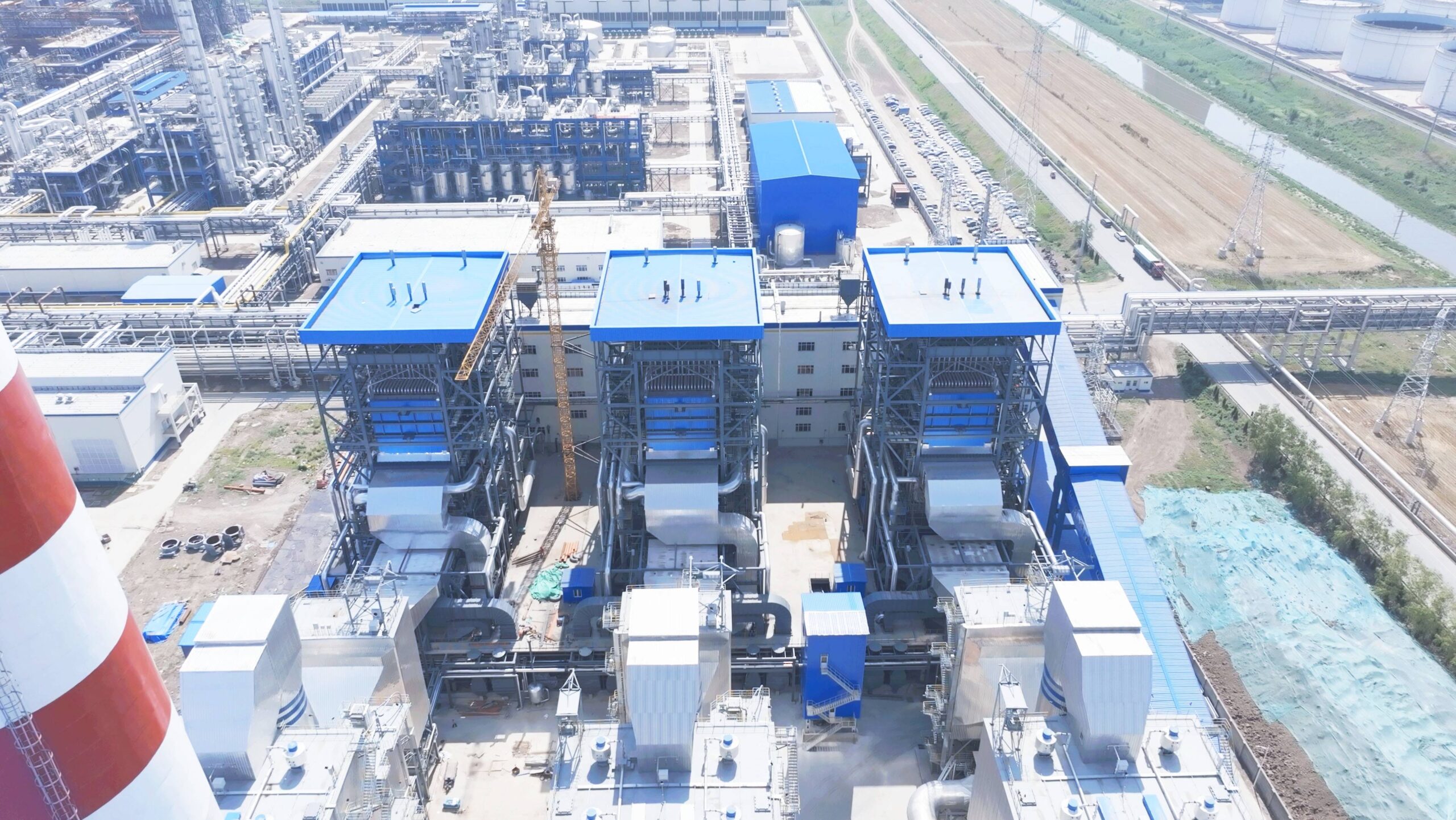
What Types of Fuels Can Be Burned in a Circulating Fluidized Bed Boiler?
Circulating Fluidized Bed (CFB) boilers are increasingly favored for their fuel flexibility, environmental performance, and combustion efficiency. Traditional boilers struggle with low-grade fuels or fuel blends, but CFB boilers can burn a wide variety—from high-ash coal and biomass to municipal solid waste—thanks to their unique combustion mechanics. These boilers suspend fuel in a turbulent, high-velocity bed of hot particles, ensuring complete burn-out even for challenging fuels. Understanding which fuels are compatible with CFB systems enables industrial users to maximize fuel cost savings, reduce emissions, and improve energy security.
CFB boilers can burn a wide range of solid fuels including bituminous and sub-bituminous coal, lignite, biomass (wood chips, rice husk, bagasse), petroleum coke (petcoke), municipal solid waste (RDF), sewage sludge, industrial waste residues, and fuel blends. Their ability to operate at lower combustion temperatures (800–900°C), combined with long residence times and in-bed desulfurization, allows efficient and low-emission combustion of fuels with high ash, moisture, sulfur, or volatile content.
CFB’s unmatched fuel flexibility makes it a powerful choice for cost control and sustainable energy strategies.
Circulating Fluidized Bed boilers are limited to burning high-grade coal only.False
CFB boilers are specifically designed to burn low-grade fuels like lignite, biomass, sludge, and waste blends with high efficiency and low emissions.
Categories of Fuels Compatible with CFB Boilers
✅ 1. Coal Types
Coal Type | Typical Use in CFB |
---|---|
Bituminous Coal | Standard fuel, high energy, easy handling |
Sub-bituminous Coal | Slightly lower CV, more moisture, burns well |
Lignite | Low CV, high moisture and ash, ideal for CFB |
Anthracite (blended) | Low volatile content—requires co-firing |
Design Consideration:
Ash fusion temperature, reactivity
Requires cyclone separators and ash coolers
✅ 2. Biomass Fuels
Biomass Type | CFB Suitability |
---|---|
Wood chips/pellets | Excellent—burns clean, easy feed |
Rice husk | High silica ash—manageable in CFB |
Bagasse (sugarcane) | Moist but very reactive—high combustion rate |
Agricultural residues | Straw, shells, husks—needs pre-sorting |
Design Consideration:
Fuel feeding system (screw, drag chain)
High volatile matter = secondary air control
Low ash melting temp = bed material choice critical
✅ 3. Industrial and Municipal Waste
Waste Fuel | Description and Suitability |
---|---|
RDF (Refuse-Derived Fuel) | Blended plastics, paper, food waste |
TDF (Tire-Derived Fuel) | Rubber content—high energy, needs air staging |
Sludge (sewage, paper) | High moisture—co-firing or pre-drying needed |
Plastic waste | May be co-fired with biomass or coal |
Design Consideration:
Volatile gas control
Dioxin prevention via temperature management
In-bed sorbents to capture HCl or SO₂
✅ 4. Petroleum Coke (Petcoke)
High sulfur and CV (~30–40 MJ/kg)
CFB systems can neutralize SO₂ with limestone in-bed
Requires combustion air optimization to avoid high NOx
Design Tip: Co-fire with low-sulfur biomass to reduce desulfurization load
Fuel Flexibility Table
Fuel Category | Can CFB Burn It? | Key Boiler Adaptation |
---|---|---|
High-rank coal | ✅ Yes | Standard air and bed setup |
Low-grade coal (lignite) | ✅ Yes | Moisture control, larger furnace |
Biomass (wet or dry) | ✅ Yes | Secondary air, fuel feeder design |
RDF/sludge/waste | ✅ Yes | Emissions control, stable bed flow |
Petcoke/heavy residues | ✅ Yes | Limestone injection, air staging |
Gas or oil (backup) | ⚠️ Limited | Separate burners, often co-fired |
CFB Advantages for Mixed Fuels
Advantage | Why It Works in CFB |
---|---|
Low-temperature combustion (~850°C) | Reduces NOx formation, avoids slagging |
Long residence time (3–5 seconds) | Ensures complete burnout of volatile fuels |
Uniform bed mixing | Allows homogeneous combustion of fuel blends |
In-bed desulfurization | Captures SO₂ without external scrubbers |
Tolerant to fuel moisture and ash | High-turbulence fluidization maintains combustion |
Case Study: Cement Kiln CFB Co-Firing Biomass and RDF
Boiler size: 30 TPH steam output
Fuel: 50% biomass (rice husk, sawdust) + 30% RDF + 20% petcoke
Key Features:
Overfire air + secondary cyclone
Real-time CV monitoring
Bed material: high-ash fusion alumina-silicate
Results:
88% combustion efficiency
SO₂ controlled without wet scrubbers
NOx kept under 350 mg/Nm³
45% reduction in fuel cost vs. petcoke-only firing
Summary
Circulating Fluidized Bed (CFB) boilers offer unmatched fuel flexibility—capable of burning an exceptionally wide range of solid fuels including coal, biomass, sludge, petcoke, and RDF. Their low combustion temperatures, uniform mixing, and in-bed emission controls allow them to maintain high efficiency and low emissions even with challenging, variable, or low-grade fuels. For industries seeking to diversify their fuel sources, lower operational costs, and reduce environmental impact, CFB boilers are a strategic long-term investment in resilience and sustainability.
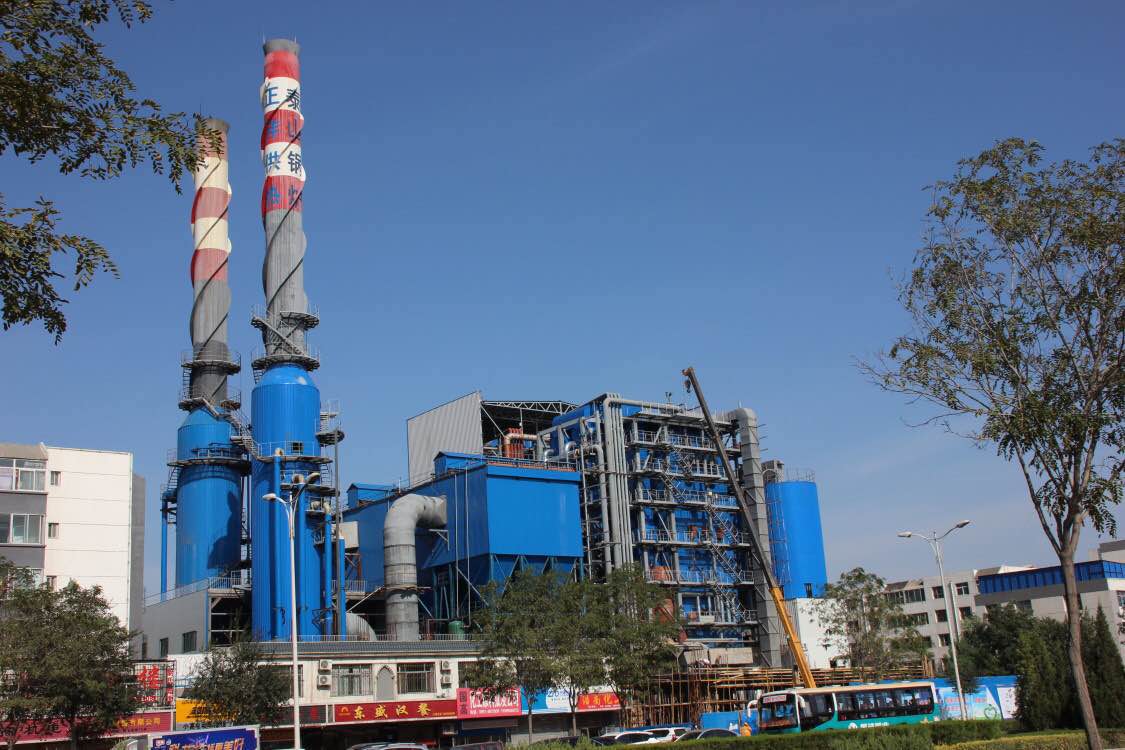
How Do Calorific Value and Volatile Content Affect Combustion in a CFB System?
Circulating Fluidized Bed (CFB) boilers are valued for their fuel flexibility, but their performance still depends heavily on the calorific value (CV) and volatile matter (VM) of the fuel. Many users assume that because CFBs can burn almost anything, fuel quality doesn’t matter—but that’s not true. If CV is too low, the furnace temperature drops below the optimal range, reducing efficiency and increasing unburned carbon. If volatile content is too high or too low, it causes flame instability or incomplete combustion. That’s why understanding how CV and VM affect combustion behavior is essential for CFB optimization and emissions control.
In a CFB system, calorific value affects the overall energy release and flame temperature, while volatile content determines ignition behavior and combustion rate. Low-CV fuels require higher feed rates and larger furnace volume to sustain temperature, while high-VM fuels ignite quickly but need precise air staging to avoid CO and unburned hydrocarbons. Proper management of both parameters ensures efficient burnout, thermal stability, and clean flue gas. The CFB’s staged air, long residence time, and bed circulation allow it to compensate for these challenges better than most combustion technologies.
Fuel flexibility doesn’t mean fuel neutrality—CV and VM still govern how combustion unfolds inside a CFB.
Fuels with low calorific value require increased feed rates and more furnace residence time in a CFB system.True
Low-CV fuels release less heat per kilogram and need to be burned in greater quantities to maintain combustion temperatures, which CFBs handle through extended residence time and bed volume.
1. Effect of Calorific Value on CFB Combustion
✅ What is Calorific Value (CV)?
Energy released per kg of fuel when fully combusted
Measured as Lower Heating Value (LHV) in MJ/kg
✅ Impact on CFB Operation:
Calorific Value | Combustion Impact |
---|---|
High CV (>30 MJ/kg) | Rapid heating, higher bed temp, faster burnout |
Medium CV (20–30 MJ/kg) | Balanced combustion, suitable for most coals |
Low CV (<18 MJ/kg) | Lower temp, requires higher mass flow, risk of instability |
🔧 Design Adaptations in CFB:
Low CV Fuel Strategy | Purpose |
---|---|
Larger furnace volume | Increases residence time for complete burn |
More feed points | Improves fuel dispersion |
Bed temperature control | Prevents drop in efficiency |
Fuel drying/pre-treatment | Reduces energy lost to moisture evaporation |
2. Effect of Volatile Matter on CFB Combustion
✅ What is Volatile Matter (VM)?
Gases released when fuel is heated (e.g., CO, CH₄, tars)
Influences ignition, flame speed, and primary air requirement
Fuel Type | Typical Volatile Matter (%) |
---|---|
Anthracite | 2–8 |
Bituminous Coal | 15–40 |
Biomass (Wood) | 70–85 |
Lignite | 30–55 |
RDF/Waste Fuels | 50–75 |
✅ Impact on Flame Behavior:
VM Level | Combustion Characteristic |
---|---|
Low (<10%) | Needs high temp for ignition, long burnout time |
Medium (15–35%) | Stable combustion, good ignition |
High (>50%) | Fast ignition, possible CO/HC emissions if air is poor |
High volatile fuels in CFB boilers need carefully staged combustion air to ensure full burnout and avoid high CO emissions.True
Volatile matter ignites quickly and burns above the bed; staged secondary air ensures mixing and complete combustion in upper furnace.
🔧 Design & Operational Adjustments for High-VM Fuels:
Feature | Function |
---|---|
Secondary air injection (OFAs) | Burns volatile gases above the bed |
Fuel particle sizing | Slows down combustion rate for uniform burn |
Refractory lining | Maintains high ignition temperature |
Dynamic air-fuel ratio control | Avoids excess CO or flameout |
Integrated Effects of CV and VM on Combustion Zones
Fuel Profile | Bed Temperature (°C) | Combustion Zone Focus | Operational Challenge |
---|---|---|---|
High CV, low VM (e.g. petcoke) | 850–900 | Bed and cyclone loop | NOx risk, slagging |
Low CV, high VM (e.g. biomass) | 800–850 | Upper furnace via secondary air | CO peaks, ash volatility |
Balanced (e.g. bituminous coal) | 850–870 | Uniform through bed and freeboard | Stable with minimal tuning |
Real-World Case: Mixed Fuel CFB Optimization
Fuel mix: 50% rice husk (VM ~70%, CV ~14 MJ/kg) + 50% sub-bituminous coal (VM ~25%, CV ~25 MJ/kg)
Problem: Fluctuating bed temperature, high CO during peak husk firing
Solutions:
Added second-level OFA injection to burn volatiles
Installed flue gas O₂/CO trim controls
Tuned fuel feed screw for stable blend delivery
Result:
CO reduced from 800 mg/Nm³ to <200 mg/Nm³
Combustion efficiency increased from 81% to 88%
Furnace temperature stabilized at ~860°C
Summary
In a CFB boiler, calorific value controls how much energy each kilogram of fuel contributes to the furnace, while volatile matter governs how quickly that energy is released. Low-CV fuels need larger combustion zones and higher feed rates to maintain thermal stability. High-VM fuels burn rapidly and require precise air staging to prevent emissions and incomplete combustion. CFB’s inherent advantages—like long residence time, staged air, and turbulent bed mixing—allow it to adapt to these fuel variations better than most technologies. Still, smart combustion management is essential to unlock high efficiency, low emissions, and flexible fuel usage.
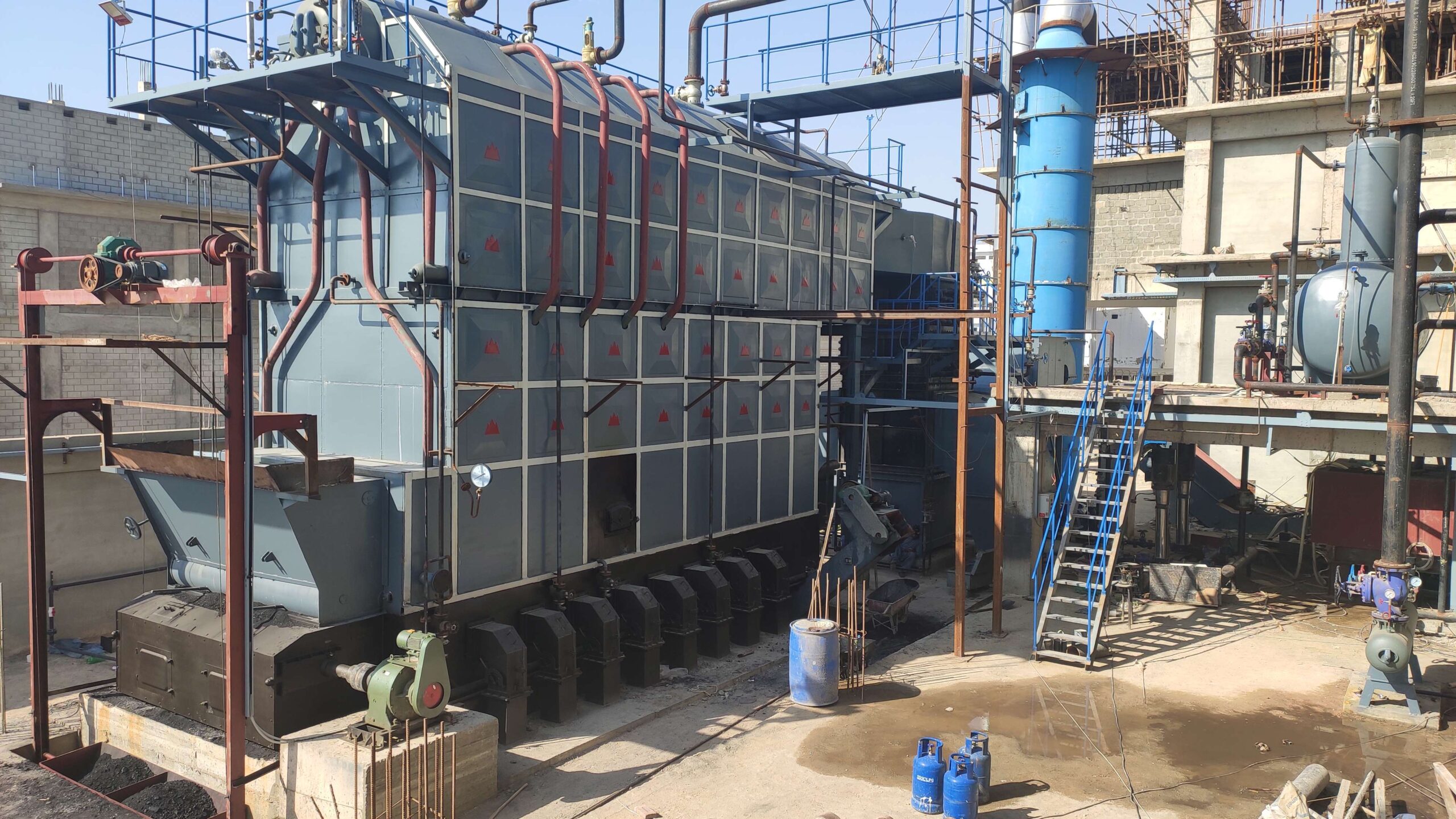
Why Do Moisture Content and Particle Size Matter in Fluidization and Heat Transfer?
In Circulating Fluidized Bed (CFB) boilers, fuel particles are suspended in a high-velocity air stream, creating a fluid-like environment for combustion and heat exchange. For the system to work efficiently, this fluidization must be uniform and stable, ensuring that all particles are properly mixed, combusted, and in contact with heat transfer surfaces. However, moisture content and particle size of the fuel significantly affect these dynamics. Too much moisture can quench combustion and disrupt air flow, while particles that are too large or too small hinder uniform fluidization and reduce thermal efficiency. Proper fuel preparation and handling are therefore critical to CFB success.
Moisture content and particle size matter in fluidization and heat transfer because they directly influence how well fuel particles are suspended in the fluidized bed, how evenly they burn, and how effectively heat is transferred to the boiler tubes. High moisture reduces bed temperature and slows ignition, while excessively large or uneven particle sizes disrupt fluidization uniformity, causing hot spots, poor combustion, and fouling. Optimizing both parameters ensures efficient energy release, stable combustion, and maximum boiler efficiency.
The CFB system thrives on balance—and fuel moisture and size are key to maintaining that balance.
CFB boilers can fluidize fuel particles of any size and moisture content without affecting performance.False
Proper fluidization depends on particle density, size distribution, and moisture content. If these factors are not optimized, the bed becomes unstable, reducing combustion efficiency and heat transfer.
1. Moisture Content: The Invisible Heat Sink
Why It Matters:
Moisture in the fuel must be evaporated before combustion begins.
This process absorbs a large amount of heat, reducing bed temperature.
Wet fuels cause delayed ignition, unburned carbon, and CO formation.
Fuel Type | Typical Moisture (%) | Impact on Fluidization & Heat Transfer |
---|---|---|
Bituminous Coal | 5–15 | Minimal effect |
Lignite | 30–50 | Major quenching risk; needs air preheating |
Biomass (chips, husk) | 20–55 | Risk of sticking, bridging in feed system |
Sludge/municipal waste | 40–65 | Requires co-firing or drying |
Design and Operational Responses:
Adaptation | Purpose |
---|---|
Pre-drying (mechanical or thermal) | Reduces moisture before feeding |
Preheated combustion air | Maintains bed temperature |
Grate-assisted preheating zones | Allows moisture evaporation before ignition |
Fuel feed rate adjustment | Compensates for energy loss due to moisture |
Moisture in solid fuels consumes thermal energy and lowers combustion temperature in the fluidized bed.True
Before fuel can ignite, its moisture must be vaporized, consuming significant energy and reducing available heat for combustion and steam generation.
2. Particle Size: The Key to Stable Fluidization
Why It Matters:
CFB fluidization depends on uniform particle motion.
Particle size affects drag force vs. gravitational settling.
Too coarse → particles settle and defluidize
Too fine → particles blow out with the flue gas
Particle Size (mm) | Fluidization Behavior | Combustion Impact |
---|---|---|
< 0.1 mm | Easily entrained → losses, incomplete burn | |
0.1–5 mm | Optimal for CFB → stable, turbulent flow | |
> 6–8 mm | Settles in bed, poor mixing |
Particle Size vs. Fuel Type
Fuel Type | Recommended Particle Size Range |
---|---|
Coal (pulverized) | 0.1–1 mm |
Lignite | 1–5 mm |
Biomass (chipped) | <10 mm (after pre-chopping) |
RDF/Waste | 2–20 mm (coarsest fuel needs screening) |
Combined Effect on Heat Transfer Efficiency
Parameter | Effect on Heat Transfer |
---|---|
High Moisture | Lowers bed temperature → reduces convective & radiant transfer |
Large Particle Size | Settling delays burn → reduced contact with tubes |
Uneven Size Distribution | Disrupts fluidization uniformity → hotspots, dead zones |
Fine particles (dust) | Blow out → wasted energy and fouling downstream |
Resulting Problems:
Reduced steam generation
Tube surface fouling or erosion
Combustion instability
Increased emissions (CO, VOCs)
Solutions for Moisture and Particle Size Management
Engineering Solution | Function |
---|---|
Rotary or hammer mills | Standardize biomass and waste fuel size |
Vibrating or screen classifiers | Remove oversized or fines before feeding |
Fuel bunker blending | Mix dry and wet fuel for stable average properties |
Online moisture sensors | Adjust feed rate or air based on real-time fuel data |
Flue gas dryer system | Use waste heat to pre-dry incoming fuel stream |
Case Study: Paper Mill Using 45% Moisture Biomass
Fuel: Eucalyptus bark and sawmill waste
Problem:
Flameout during high-moisture days
Unstable bed fluidization
Low bed temperature (~780°C)
Upgrades:
Added biomass dryer using economizer heat
Installed chip sizer for <8 mm particle distribution
Implemented real-time air ratio control
Results:
Bed temperature restored to 850–870°C
Steam output increased by 14%
CO reduced by 50%; fluidization fully stabilized
Summary
In CFB boiler systems, moisture content and particle size are critical variables that determine how well fuel mixes with bed material, combusts, and transfers heat. High moisture absorbs combustion energy, reducing flame stability and steam production. Improper particle sizing leads to poor fluidization, dead zones, and fuel loss. These issues can be mitigated through fuel pre-processing, control systems, and tailored combustion engineering. Ultimately, optimized moisture and sizing enable cleaner, more stable, and more efficient combustion—unlocking the true power of fluidized bed technology.
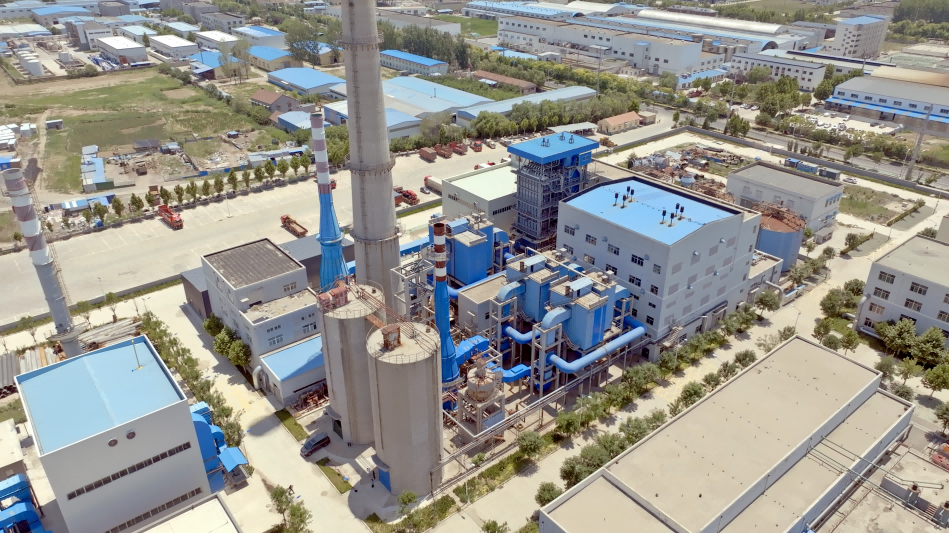
How Does Ash Content and Composition Influence Bed Material and Ash Removal Design?
In Circulating Fluidized Bed (CFB) boilers, ash is not just a by-product—it’s a key design factor. Whether the ash comes from coal, biomass, sludge, or waste fuels, its quantity and chemical composition determine how the boiler’s bed material behaves, how much maintenance is needed, and what type of ash handling system is required. If the ash content is high, it can clog heat exchangers, degrade bed material, or overload conveyors. If the ash composition contains low-melting-point elements like alkali metals or silica, it can cause slagging, fouling, or even permanent damage. That’s why smart ash management is essential for high-efficiency, low-maintenance boiler operation.
Ash content and composition influence CFB boiler design by affecting the behavior of the bed material, the tendency to form slag or sinter, the efficiency of heat transfer surfaces, and the configuration of ash removal systems. High-ash fuels require robust ash discharge systems, greater separation efficiency, and erosion-resistant materials, while certain ash chemistries require higher-melting-point bed media to prevent sintering. The physical and chemical properties of ash must be matched with the right mechanical and thermal design strategies to maintain combustion efficiency and system longevity.
In CFB systems, ash isn’t just waste—it’s a fluidizing and reactive component that must be controlled by design.
Ash composition affects how the bed material performs and whether slagging or sintering will occur.True
Ash containing high levels of alkalis, iron, or silica with low fusion temperatures can react with bed material, causing sintering and agglomeration, which disrupt fluidization.
1. Ash Content: Volume Matters
Fuel Type | Typical Ash Content (%) | Impact on System Design |
---|---|---|
Bituminous Coal | 10–20 | Moderate ash handling load |
Lignite | 20–40 | Requires large ash discharge, risk of sintering |
Biomass (e.g. husk) | 4–25 | High silica, causes clinker, light fly ash |
Sludge/industrial waste | 30–60 | Highly variable, corrosive, heavy ash stream |
System Design Adaptations for High Ash Fuels:
Design Element | Purpose |
---|---|
Oversized bottom ash cooler | Prevents clogging and allows continuous discharge |
Fluidized ash extractors | Avoids bed pressure buildup |
Multiple hopper zones | Enables staged removal of coarse and fine ash |
Erosion-resistant duct linings | Protects from abrasive ash transport |
High ash content increases wear on boiler surfaces and ash handling components.True
Abrasive ash particles erode pipes, cyclones, and air nozzles, increasing the need for robust materials and regular maintenance.
2. Ash Composition: Chemistry Controls Behavior
Key Chemical Components in Ash:
Oxide | Effect on Boiler Operation |
---|---|
SiO₂ (Silica) | Forms low-melting eutectics, causes slagging |
Al₂O₃ (Alumina) | High-melting, stabilizes bed material |
Fe₂O₃ (Iron oxide) | Promotes ash melting, accelerates sintering |
Na₂O/K₂O (Alkalis) | Reacts with silica → sticky slag, deposits |
CaO/MgO (Lime) | Helps SO₂ capture, but can flux ash if unbalanced |
P₂O₅/Cl/S | Corrosive, causes acid attack on metal surfaces |
Example: Rice Husk
Ash content: 15–25%
High SiO₂ (>80%)
Fusion point: ~1000–1100°C
Effect: Tends to form glassy deposits in bed if temp >900°C
Design Need: Ash-agitation grate, sinter-resistant bed material
3. Bed Material Interaction and Agglomeration Risk
Issue | Cause | Solution |
---|---|---|
Bed agglomeration | Ash + sand sinter into glassy lumps | Use high-melting bed media (e.g., bauxite) |
Bed defluidization | Agglomerated particles prevent circulation | Periodic bed draining, alkali monitoring |
Sintered lumps in bed | Alkali-silica eutectics stick at ~850–950°C | Bed additives (dolomite, kaolin) to stabilize ash |
Recommended Bed Materials Based on Ash Chemistry:
Ash Type | Preferred Bed Material |
---|---|
High silica/alkali | Bauxite, calcined alumina |
High sulfur/lime | Dolomite, limestone blends |
Balanced (coal + biomass) | Quartz sand or recycled bed ash |
4. Ash Removal Systems: Bottom and Fly Ash
Bottom Ash System:
Wet-type ash coolers: use water to quench and move hot ash
Dry-type extractors: use conveyors or vibrators with air cooling
Discharge rate matched to fuel ash yield and flow stability
Fly Ash System:
Carried by flue gas → collected via:
Cyclones
Multiclones
Bag filters
ESP (Electrostatic Precipitators)
Fuel Type | Fly Ash Dominance | Removal Strategy |
---|---|---|
Pulverized coal | High | ESP + bag filter combo |
Biomass | Light, fluffy | High-pressure pulse jet bag filters |
Waste sludge | Sticky, corrosive | Dual-stage cyclones + activated carbon injection |
Real-World Case: CFB Boiler for Mixed Biomass and Lignite
Fuel: 60% lignite (ash 35%), 40% wood pellets (ash 1%, high alkali)
Issues:
Bed clumping every 2 weeks
Incomplete ash removal, fly ash buildup
Solutions:
Switched bed to alumina media
Added in-bed air spargers for ash agitation
Upgraded cyclone with wear-resistant ceramic liners
Results:
Ash-related shutdowns reduced by 90%
Fly ash emissions met EU standard <20 mg/Nm³
Bed stability maintained even with 30% RDF blending
Summary
Ash content and composition aren’t just operational side effects—they are design drivers in CFB boilers. High ash content requires durable, continuous ash removal infrastructure. Meanwhile, the ash’s chemical makeup determines whether your bed material will stay fluidized or clump into a solid mass. Using the wrong bed media or underestimating slagging tendencies can bring down even the best-designed boiler. Smart ash management—through the right materials, extractors, and monitoring systems—ensures that your CFB system performs reliably, even with the dirtiest or most diverse fuels on the market. In fluidized bed combustion, managing ash is just as important as burning fuel.
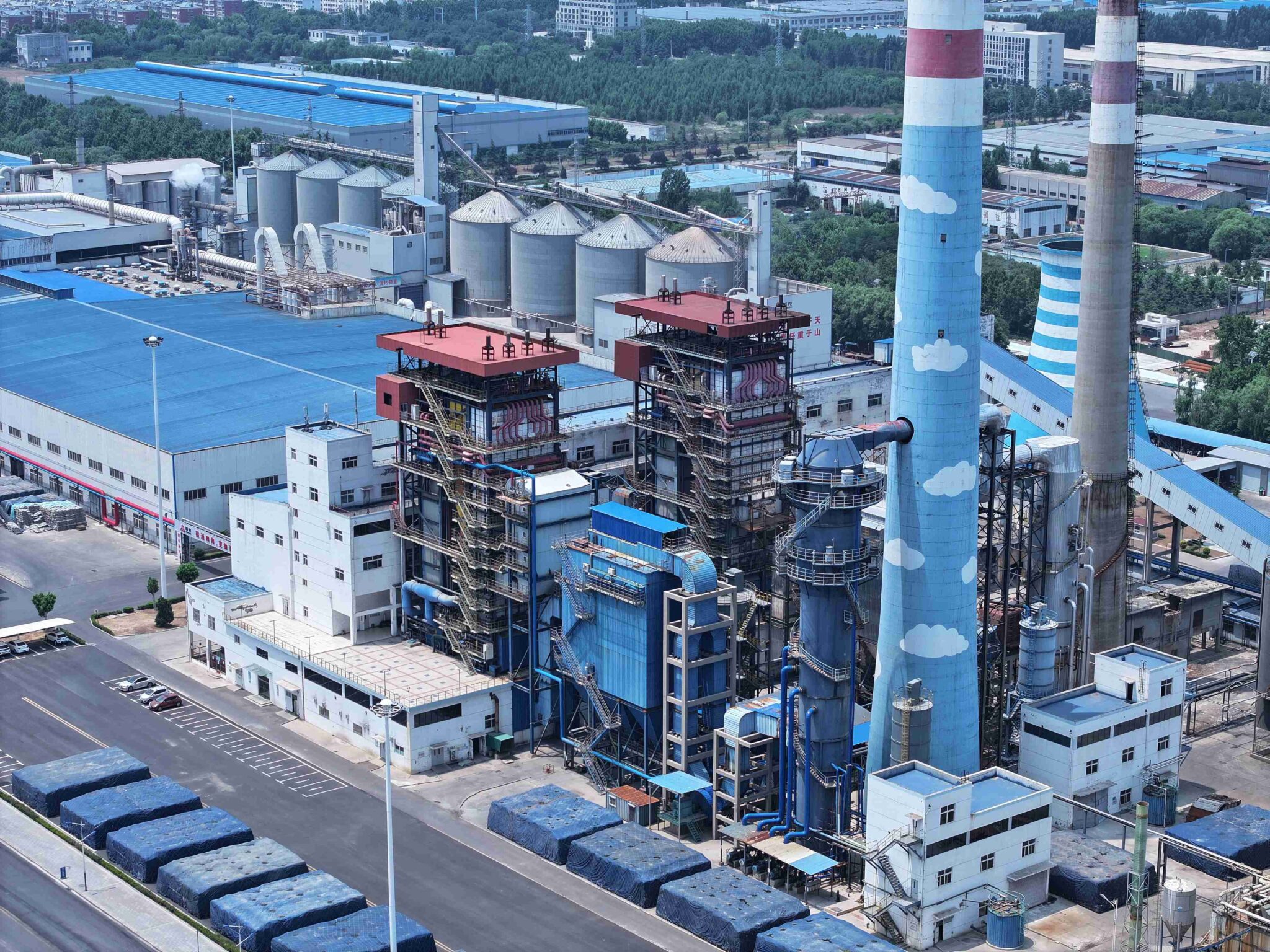
What Impact Do Sulfur and Nitrogen Levels Have on Emissions and Control Systems?
Sulfur and nitrogen levels in fuel don’t just influence boiler operation—they directly determine your emissions profile, environmental compliance obligations, and the type of emissions control technologies your system must use. High-sulfur fuels release sulfur dioxide (SO₂), which contributes to acid rain and corrodes equipment. High-nitrogen fuels or high-temperature combustion release nitrogen oxides (NOₓ), which cause smog and respiratory issues. Both pollutants are heavily regulated worldwide. Without the correct flue gas treatment systems, high SO₂ or NOₓ levels can lead to violations, fines, and shutdowns. That’s why understanding sulfur and nitrogen content is essential to designing compliant and cost-effective combustion systems.
Sulfur and nitrogen levels in fuel significantly affect SO₂ and NOₓ emissions in industrial boilers. High sulfur leads to higher SO₂, requiring flue gas desulfurization (FGD), while fuel-bound nitrogen and high combustion temperatures generate NOₓ, necessitating controls like Low-NOₓ burners, SNCR, or SCR systems. Fuel selection, combustion temperature, air staging, and post-combustion treatment must all be tailored to these fuel properties to meet emission limits and maintain environmental compliance.
Whether you’re burning coal, biomass, oil, or waste, your sulfur and nitrogen content dictates your emissions strategy.
High nitrogen content in fuel directly increases NOₓ emissions during combustion.True
Fuel-bound nitrogen is oxidized at high temperatures, especially in fluidized bed and flame-based systems, contributing to NOₓ formation unless controls are in place.
1. Sulfur Content → Sulfur Dioxide (SO₂) Emissions
Source:
Sulfur is present in most fossil fuels (coal, oil, petcoke) and some waste streams.
During combustion, sulfur converts to SO₂ and SO₃.
Fuel Type | Typical Sulfur Content (% by wt) | SO₂ Emission Potential (mg/Nm³) |
---|---|---|
Bituminous Coal | 1.0–3.5 | 2,000–4,000 |
Lignite | 0.4–1.2 | 800–2,400 |
Fuel Oil (HFO) | 1.5–4.0 | 2,500–5,000 |
Biomass (clean) | <0.05 | <50 |
Waste Fuels (RDF) | 0.2–1.0 | 200–2,000 |
Design Considerations:
Control Method | Function |
---|---|
Limestone injection (in-bed) | Reacts with SO₂ to form CaSO₄ (CFB systems) |
Dry sorbent injection (DSI) | Injected into ductwork for moderate SO₂ control |
Wet scrubbers (FGD) | Absorb SO₂ in limestone slurry |
Spray dry scrubbers (semi-dry) | Combines heat and slurry to neutralize SO₂ |
Fuel oil with high sulfur content requires post-combustion flue gas desulfurization systems to meet emission standards.True
High-sulfur fuel oil emits significant SO₂, which must be reduced using scrubbers or sorbent injection to comply with environmental limits.
2. Nitrogen Content and Flame Temperature → Nitrogen Oxides (NOₓ)
Types of NOₓ:
NOₓ Type | Formation Mechanism |
---|---|
Thermal NOₓ | From nitrogen in combustion air at high flame temperatures |
Fuel NOₓ | From nitrogen compounds in fuel oxidized during burning |
Prompt NOₓ | Minor role, formed in hydrocarbon-rich flames |
Fuel | Typical Nitrogen (%) | NOₓ Potential (mg/Nm³) |
---|---|---|
Bituminous Coal | 1.2–1.8 | 400–800 |
Fuel Oil | 0.5–1.5 | 250–600 |
Biomass (varies) | 0.2–0.8 | 150–400 |
RDF/Waste | 0.8–2.0 | 500–1,200 |
Design Strategies for NOₓ Reduction:
Method | How It Works |
---|---|
Low-NOₓ Burners | Create staged air zones to limit peak flame temp |
Flue Gas Recirculation (FGR) | Cools flame, reduces O₂ concentration |
Overfire Air (OFA) | Completes combustion with lower NOₓ in upper furnace |
Selective Non-Catalytic Reduction (SNCR) | Urea or ammonia injected into hot gas (~900°C) |
Selective Catalytic Reduction (SCR) | NH₃ over catalyst at 300–400°C to convert NOₓ to N₂ |
SO₂ and NOₓ Emissions Control Matrix
Fuel Type | SO₂ Control Needed | NOₓ Control Needed | Typical Technologies Used |
---|---|---|---|
Coal (high sulfur) | ✅ Required | ✅ Required | FGD + SNCR or SCR + Low-NOₓ Burner |
Biomass | ❌ Often not needed | ⚠️ Required (depends on flame temp) | Staged air + SNCR |
Fuel Oil | ✅ Required (for HFO) | ✅ Required | Wet scrubber + Low-NOₓ Burner |
Natural Gas | ❌ Minimal | ✅ Required | Low-NOₓ Burner + FGR |
Waste/RDF | ✅ Required | ✅ Required | Dry scrubbing + SNCR + activated carbon (for dioxins) |
Real-World Example: CFB Boiler Emission Control Retrofit
Fuel: 70% high-sulfur coal + 30% RDF
Issues: SO₂ > 3,000 mg/Nm³, NOₓ > 650 mg/Nm³
Solutions:
In-bed limestone injection
Added SNCR with urea injection
Upgraded air staging and O₂ trim system
Outcome:
SO₂ reduced to <200 mg/Nm³
NOₓ reduced to <350 mg/Nm³
Compliance achieved with EU Industrial Emissions Directive (IED)
Emissions vs. Sulfur/Nitrogen Chart
Parameter | Low S/N Fuel (e.g., Biomass) | Medium S/N Fuel (e.g., Lignite) | High S/N Fuel (e.g., Coal, RDF) |
---|---|---|---|
SO₂ Emissions | <100 mg/Nm³ | 200–600 mg/Nm³ | 1,000–4,000 mg/Nm³ |
NOₓ Emissions | 100–300 mg/Nm³ | 300–500 mg/Nm³ | 500–1,000+ mg/Nm³ |
Controls Needed | Air staging only | SNCR + sorbent | Full FGD + SCR + staged combustion |
Summary
Sulfur and nitrogen content in fuel are key combustion variables that determine whether your boiler will run clean or become an environmental liability. High sulfur fuels like coal and fuel oil demand desulfurization systems to control SO₂. Fuels with high nitrogen or high flame temperatures require NOₓ controls, such as Low-NOₓ burners, SNCR, or SCR. Even biomass and RDF may emit dangerous levels of NOₓ or SO₂ if poorly managed. Therefore, every combustion system must match fuel chemistry to emissions control technology—ensuring clean, compliant, and responsible steam generation.
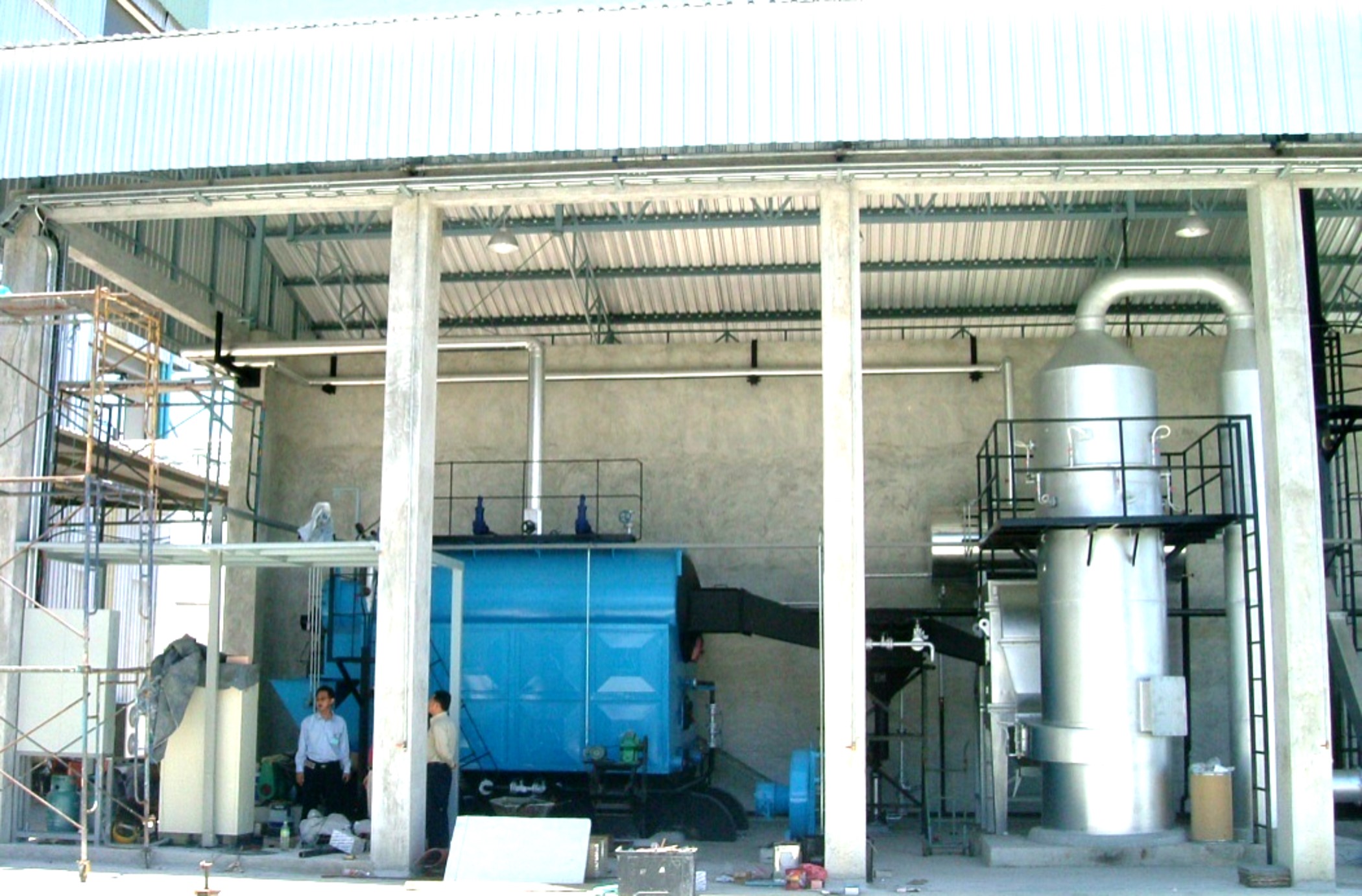
How Should CFB Boilers Be Designed for Multi-Fuel or Alternative Fuel Flexibility?
In today’s energy landscape, industries face increasing pressure to reduce fuel costs, improve energy security, and lower carbon emissions. This shift has accelerated the demand for boilers that can handle multiple fuel types, including low-grade and alternative fuels. Circulating Fluidized Bed (CFB) boilers are uniquely positioned to meet this challenge due to their inherent fuel flexibility. However, achieving stable, efficient, and clean combustion with multiple fuels requires purpose-driven boiler design. From fuel feeding to ash handling, every component must be engineered to accommodate different combustion behaviors, particle properties, moisture levels, and emission profiles.
To design a CFB boiler for multi-fuel or alternative fuel flexibility, engineers must incorporate modular fuel feeding systems, oversized combustion chambers, in-bed and overfire air staging, real-time combustion controls, high-performance cyclone separators, and robust ash extraction infrastructure. The design must account for varying fuel properties such as calorific value, moisture, ash composition, volatile content, and particle size. Flexibility also requires durable bed materials, automated fuel blending, and scalable emissions control systems to maintain performance and regulatory compliance across a wide fuel mix.
CFB flexibility doesn’t happen by chance—it’s the result of a deliberate and intelligent engineering strategy.
CFB boilers must be specially designed to maintain combustion efficiency when firing multiple or alternative fuels.True
Each fuel has unique characteristics, so achieving high efficiency and low emissions across a range of fuels requires a boiler designed with features like air staging, flexible feed systems, and robust combustion control.
Key Design Challenges of Multi-Fuel CFB Systems
Design Factor | Challenge with Multi-Fuel Use |
---|---|
Fuel Feed System | Different fuels vary in flowability, density, and moisture |
Combustion Behavior | Fuels burn at different rates and temperatures |
Bed Stability | Ash fusion, agglomeration risks from reactive or variable fuels |
Emissions Control | NOₓ, SO₂, and PM vary by fuel chemistry |
Heat Release Pattern | Uneven energy distribution may cause hotspots or cold zones |
Ash and Slag Formation | High-ash fuels require reinforced ash systems |
1. Modular and Redundant Fuel Feeding Systems
To accommodate different fuels, the boiler must include multiple independent feed systems, each tuned for its specific fuel type.
Fuel Type | Feeding Method |
---|---|
Pulverized coal | Pneumatic or screw conveyor with gravimetric dosing |
Biomass (chips, pellets) | Drag chain, screw feeder, belt conveyor |
Sludge or RDF | Ram feeder, pusher-type bunker, weigh feeders |
Features:
Variable speed drives (VFDs) for dynamic flow adjustment
Separate chutes to avoid cross-contamination
Fuel homogenization bunker for pre-mixed or blended fuels
Auto-blend control based on calorific value or combustion feedback
2. Combustion Chamber and Air Staging Design
Furnace Volume:
Fuel Class | Suggested Design Feature |
---|---|
High moisture/low CV | Oversized combustion chamber for long residence time |
High volatile matter | Staged air (primary + secondary + tertiary) for flame control |
High ash/sludge fuels | Lower bed temp zones to reduce agglomeration |
Air Distribution:
Primary air → Fluidizes bed and initiates ignition
Secondary/Overfire air → Burns volatile gases, reduces CO
Air staging helps NOₓ reduction and combustion control
Multi-stage air injection helps achieve full combustion and reduce NOₓ emissions in multi-fuel CFB boilers.True
Staged combustion air ensures that volatile gases from high-volatile fuels fully oxidize, while limiting local peak temperatures that produce NOₓ.
3. Bed Material Selection and Management
Multi-fuel combustion increases the risk of bed agglomeration and chemical reaction with ash.
Fuel Property | Recommended Bed Strategy |
---|---|
High alkali/silica ash | Use high-melting-point bed materials like bauxite or alumina |
Variable ash load | Install bed drain and recirculation systems |
Frequent slagging | Add bed additives (kaolin, dolomite) |
Monitoring:
Bed pressure sensors detect defluidization risk
Online temperature control maintains ideal combustion range (800–900°C)
4. Cyclone and Heat Exchanger Adaptations
Multi-fuel systems cause wide variations in flue gas load and particulate carryover.
Cyclones and Heat Recovery:
Design Upgrade | Purpose |
---|---|
High-efficiency cyclone | Separates fine ash and particles from gas stream |
Anti-abrasion linings | Withstand high-silica or corrosive ash |
Superheater/evaporator protection | Minimize fouling and erosion from volatile fuels |
Control:
Install back-pressure dampers, bed seal valves, and bed ash coolers for enhanced flow regulation
5. Emissions Control Flexibility
System Integration:
Pollutant | Fuel Risk Level | Control Solution |
---|---|---|
SO₂ | High (coal, petcoke, sludge) | In-bed limestone injection, DSI, FGD |
NOₓ | High (waste, oil) | Staged air + SNCR/SCR |
PM | High (biomass, RDF) | Cyclone + bag filter or ESP |
Dioxins/VOCs | RDF, plastic-rich fuels | Activated carbon + post-combustion oxidation |
Smart control systems (PLC/SCADA) dynamically adjust fuel-air ratio, O₂ trim, and reagent dosing based on sensor feedback.
Real-World Case: 100 MWth Multi-Fuel CFB Boiler
Fuels Fired: 40% lignite, 30% wood chips, 15% RDF, 15% sewage sludge
Design Features:
Triple feed systems with independent bunkers
Air staging: 3-level overfire air
High-temperature-resistant bed media (alumina blend)
Cyclone lined with silicon-carbide bricks
SNCR + in-bed limestone injection
Results:
Achieved 89% combustion efficiency across all fuels
NOₓ reduced to <180 mg/Nm³, SO₂ <150 mg/Nm³
Fuel flexibility led to 28% cost savings over mono-fuel operation
Summary
Designing a multi-fuel or alternative-fuel-ready CFB boiler means planning for diversity—not uniformity. Each fuel brings its own moisture, ash, energy content, and emissions profile. To manage this variability, engineers must use modular fuel feeds, adaptive air systems, specialized bed materials, and intelligent control systems. When done right, a multi-fuel CFB boiler becomes a strategic energy platform—resilient, economical, and future-ready for fuels ranging from coal to biomass to waste. With the right design, your boiler isn’t just a combustion device—it’s a flexible fuel engine for industrial sustainability.
🔍 Conclusion
Fuel selection is a critical design input for any Circulating Fluidized Bed boiler. While CFBs offer excellent fuel versatility, performance depends heavily on matching the combustion characteristics of the fuel with the boiler’s fluidization, heat exchange, and emissions systems. A well-matched fuel and boiler design ensures optimal combustion efficiency, lower emissions, and cost-effective operation—making your investment in CFB technology both sustainable and future-ready.
📞 Contact Us
💡 Need help analyzing your fuel for a CFB boiler system? Our engineering team offers fuel testing, system design, and performance optimization services tailored to your application.
🔹 Let us help you design a CFB boiler system that’s optimized for your fuel and performance goals! 🔄🔥♻️
FAQ
How do different fuel types affect the selection of a CFB boiler?
CFB boilers are known for their fuel flexibility. They can burn a wide variety of fuels, including low-grade coal, biomass, petroleum coke, and industrial waste. The selection depends on fuel availability, energy content, ash content, and environmental regulations.
What combustion characteristics are important in CFB boiler operation?
Key combustion traits include fuel particle size, moisture content, volatile matter, ash fusion temperature, and sulfur content. CFB technology excels at handling fuels with high ash or moisture due to its low combustion temperature and long residence time.
Why are CFB boilers ideal for low-grade and variable fuels?
Unlike conventional boilers, CFB boilers maintain stable combustion and heat transfer even with inconsistent fuel quality. Their circulating bed and in-furnace desulfurization capability allow for efficient burning of inexpensive or waste-derived fuels.
How does fuel type impact emissions in a CFB boiler?
High-sulfur fuels can lead to SO₂ emissions, but CFB boilers mitigate this using limestone for in-bed desulfurization. Additionally, their low-temperature combustion reduces NOx formation, making them suitable for emission-sensitive applications.
Can a CFB boiler be designed for multi-fuel or co-firing applications?
Yes, CFB boilers are highly adaptable and often designed for co-firing multiple fuels simultaneously. This flexibility improves fuel sourcing, reduces costs, and supports renewable integration with biomass or RDF alongside coal or petcoke.
References
CFB Boiler Fuel Flexibility Overview – https://www.energy.gov
Combustion Principles in CFB Technology – https://www.sciencedirect.com
Multi-Fuel Capability of CFB Boilers – https://www.researchgate.net
In-Bed Desulfurization in CFB Boilers – https://www.epa.gov
CFB Boiler Emissions and Control – https://www.bioenergyconsult.com
Boiler Design for Ash-Rich Fuels – https://www.mdpi.com
Fuel Adaptability in Industrial Boilers – https://www.energysavingtrust.org.uk
Efficiency Optimization in CFB Boilers – https://www.iea.org
Fluidized Bed Combustion Explained – https://www.automation.com
Advanced CFB Boiler Engineering – https://www.sciencedirect.com
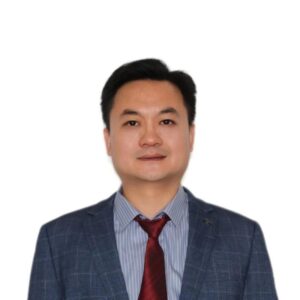