When selecting an industrial coal-fired boiler, many buyers focus on capacity or pressure—but overlooking the impact of coal type and combustion behavior can lead to inefficient combustion, excessive emissions, and frequent maintenance issues. Different types of coal have vastly different properties that directly affect boiler design, combustion performance, fuel handling, and emission control systems. A properly matched fuel-boiler combination ensures maximum efficiency, equipment longevity, and regulatory compliance.
Fuel types and combustion characteristics affect your choice of industrial coal-fired boiler by determining furnace dimensions, combustion air supply, ash removal design, slagging tendency, and flue gas treatment systems. Coal varies in moisture, ash content, calorific value, sulfur levels, and volatile matter, all of which influence how the fuel burns and what kind of boiler technology is best suited. Choosing the wrong configuration for your coal type can lead to poor efficiency, corrosion, excessive slag formation, and failure to meet environmental standards.
Let’s explore how to make the right decision based on the specific fuel characteristics relevant to your facility.
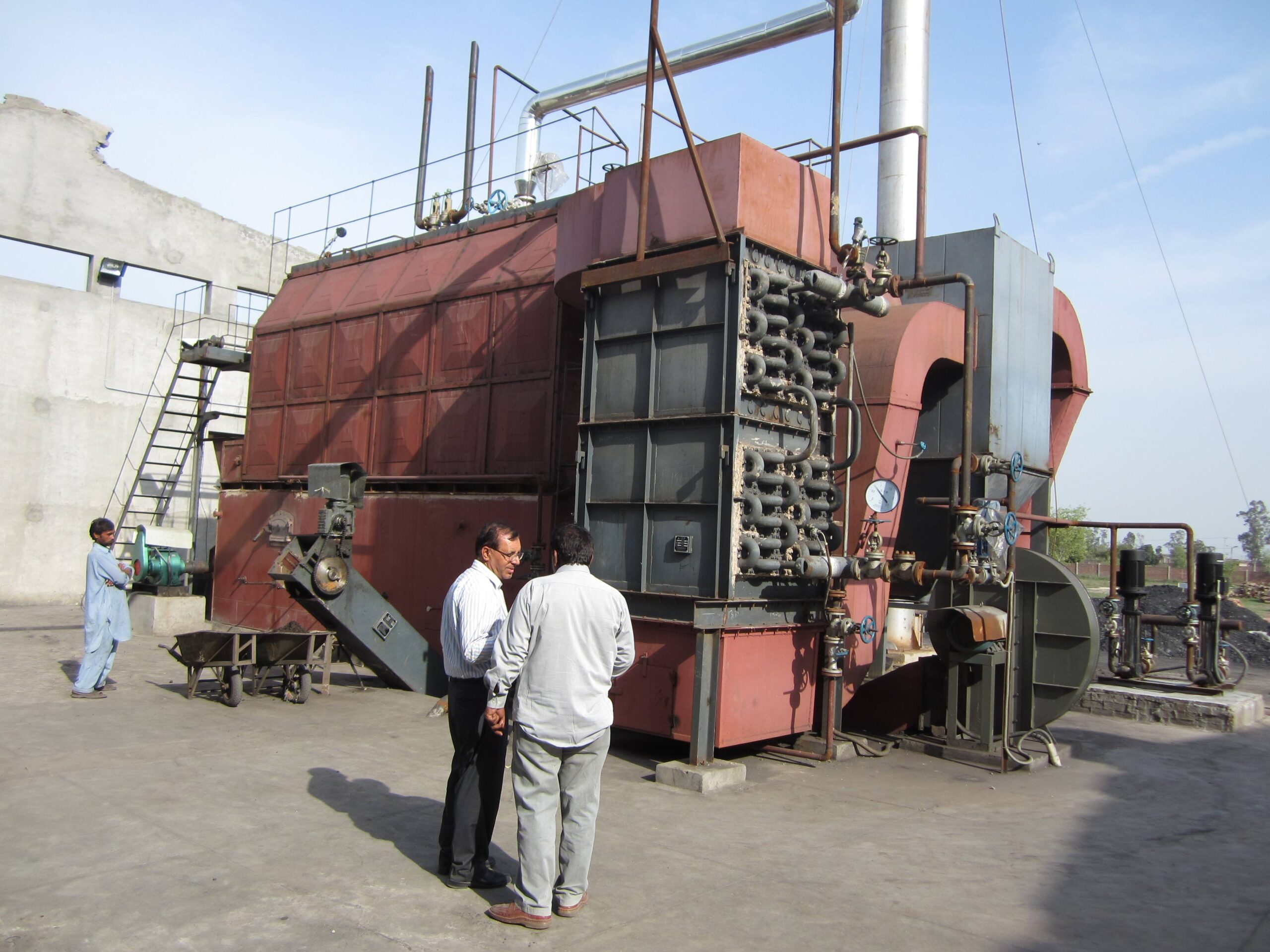
What Are the Main Types of Coal Used in Industrial Coal-Fired Boilers?
In industrial steam and power generation, coal-fired boilers remain vital for applications demanding high pressure and continuous energy output. However, not all coal types perform the same in combustion systems. Choosing the wrong coal type for a specific boiler design can result in low combustion efficiency, excessive slagging, high emissions, and unplanned shutdowns. Industrial boilers must be tailored to the chemical and physical characteristics of the coal used, including calorific value, moisture content, ash composition, and volatile matter. Knowing the differences between the main types of coal used in boilers is essential for achieving stable combustion, regulatory compliance, and long-term operational reliability.
The main types of coal used in industrial coal-fired boilers are anthracite, bituminous coal, sub-bituminous coal, and lignite. Each type differs in carbon content, calorific value, moisture, and volatile matter, which influence combustion efficiency, slagging behavior, and emissions. Bituminous coal is the most commonly used due to its balance of high energy content and good combustion characteristics. Lignite, with high moisture and low energy density, requires specially designed boilers, while anthracite burns cleanly but needs high ignition temperatures.
Selecting the right coal type is critical to optimizing fuel cost, system longevity, and combustion performance. Let’s explore each one in detail with comparative data and practical implications for boiler operation.
All coal types can be used interchangeably in the same industrial boiler system.False
Different coal types have varying combustion characteristics, and most industrial boilers are designed for specific coal grades. Using incompatible coal types can lead to inefficient combustion, equipment damage, and high emissions.
Classification of Coal Types by Combustion Characteristics
Coal types are typically classified based on rank, which reflects the degree of carbon concentration due to geological pressure and heat. Higher-rank coals have more carbon and energy, while lower-rank coals retain more moisture and volatile compounds.
Coal Type | Carbon (%) | Moisture (%) | Volatile Matter (%) | Calorific Value (MJ/kg) | Common Usage in Boilers |
---|---|---|---|---|---|
Anthracite | 86–97 | 3–8 | 2–8 | 28–33 | Rare, specialized high-temp boilers |
Bituminous | 65–85 | 2–15 | 12–40 | 24–35 | Widely used in steam power & industry |
Sub-bituminous | 45–65 | 15–30 | 15–30 | 17–25 | Suitable for circulating fluidized bed |
Lignite (Brown Coal) | 25–45 | 30–60 | 25–40 | 9–18 | Needs special low-temp boiler designs |
Key Types of Coal for Boiler Systems
H3: Bituminous Coal – The Industrial Workhorse
Bituminous coal is the most widely used in industrial coal-fired boilers due to its balance of:
High calorific value (24–35 MJ/kg)
Moderate moisture and volatile matter
Reliable ignition and stable combustion
Adaptability to grate, pulverized, and fluidized bed systems
Advantage | Implication for Boiler Design |
---|---|
High energy content | Smaller boiler size per kW output |
Moderate ash and sulfur content | Requires flue gas desulfurization (FGD) |
Suitable for a wide load range | Stable steam supply, good turndown ratio |
H3: Sub-Bituminous Coal – Lower Grade, But Reliable
Sub-bituminous coal has:
Moderate energy content (17–25 MJ/kg)
Higher moisture and volatile matter than bituminous
Lower sulfur content (environmental benefit)
Best used in:
Circulating Fluidized Bed (CFB) boilers
Plants focused on lower emissions or cheaper fuel availability
Pros | Cons |
---|---|
Lower SO₂ emissions | Larger combustion chamber required |
Good flame propagation | Higher flue gas volume, more particulate |
Cost-effective in some markets | More ash and moisture to manage |
H3: Lignite – Economical But Technically Demanding
Also called brown coal, lignite has:
Very low energy density (9–18 MJ/kg)
High moisture (often 30–50%)
High volatile matter → easy ignition, unstable flame
Used in:
Locally mined, low-cost power plants
Special boilers with pre-drying stages or large furnaces
Challenges | Mitigation Strategy |
---|---|
High moisture | Integrate fuel dryers or larger grate |
High ash formation | Use large ash hoppers and soot blowers |
Low energy per kg | Requires more fuel, larger feed system |
Lignite-fired boilers require larger combustion chambers and more sophisticated ash handling systems than bituminous coal-fired boilers.True
Lignite’s high moisture and ash content lead to increased fuel volume, requiring larger combustion zones and enhanced ash extraction equipment.
H3: Anthracite – High Performance, Limited Use
Anthracite is the highest rank of coal, with:
High carbon (86–97%)
Low volatile matter and sulfur
High ignition temperature
Used in:
Industrial applications with continuous high-temperature needs
Rarely in new boiler systems due to cost and handling difficulty
Strengths | Limitations |
---|---|
Very clean combustion | Hard to ignite, needs intense burner |
Very low emissions | Not suitable for low-load operation |
High energy per kg (up to 33 MJ/kg) | Expensive, limited availability |
Comparison Table: Coal Type Suitability by Boiler Technology
Boiler Type | Bituminous | Sub-bituminous | Lignite | Anthracite |
---|---|---|---|---|
Pulverized Coal (PC) | ✅ | ✅ (with pre-drying) | ❌ | ❌ (ignition issue) |
Chain Grate / Stoker | ✅ | ✅ | ⚠️ (custom needed) | ⚠️ (difficult ignition) |
Fluidized Bed (CFB/FBC) | ✅ | ✅ | ✅ | ❌ |
High-temp Process Boilers | ⚠️ | ❌ | ❌ | ✅ |
Other Considerations in Coal Selection
Factor | Impact on Boiler Sizing & Operation |
---|---|
Ash Fusion Temperature | Affects slagging and fouling risks |
Sulfur Content | Requires scrubbers or FGD systems if high |
Grindability (HGI) | Important for pulverized coal systems |
Local Availability | Impacts logistics and long-term fuel pricing |
Real-World Example: Textile Industry Steam Boiler
Boiler: 10 TPH stoker-fired unit
Initial coal: Bituminous (CV ~28 MJ/kg)
Switched to sub-bituminous (CV ~20 MJ/kg)
Modifications:
Increased grate area
Adjusted air distribution
Added fly ash cyclone
Result:
Maintained output
Fuel cost reduced by 18%
Slightly higher ash disposal frequency
Summary
Choosing the right type of coal is foundational to the successful design and operation of industrial coal-fired boilers. Bituminous coal remains the preferred choice for its balance of combustion properties, while sub-bituminous coal offers lower emissions and cost at the expense of higher fuel volume. Lignite requires careful boiler adaptation due to high moisture and ash, while anthracite is reserved for specialized, high-temperature applications. Understanding the fuel’s calorific value, moisture, ash, and burn behavior ensures proper boiler sizing, stable operation, and reduced operational risk. Selecting the right coal type isn’t just about combustion—it’s about system performance, sustainability, and economics.
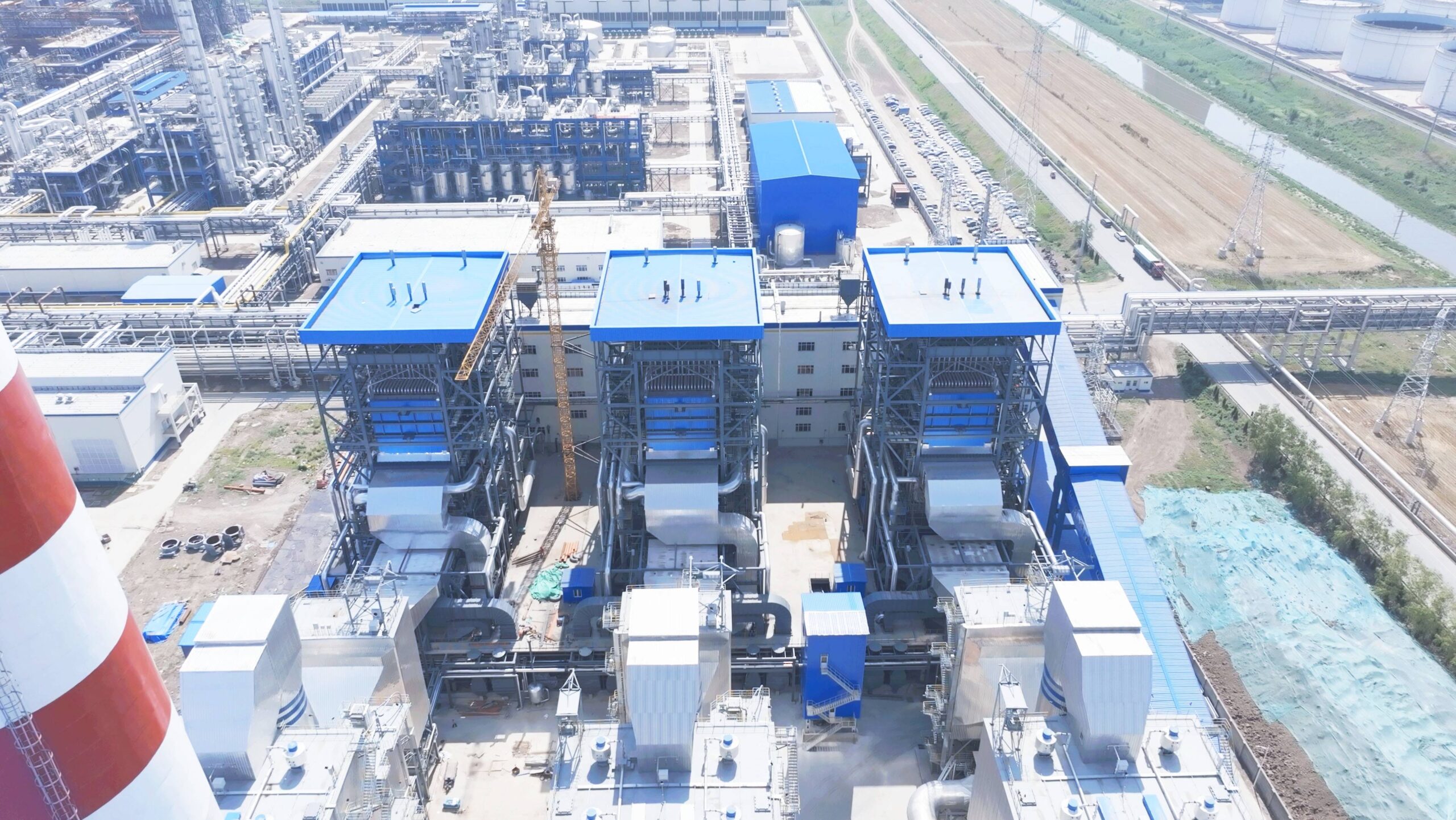
How Do Calorific Value and Ash Content Influence Boiler Size and Furnace Design?
In coal-fired boiler design, two fuel characteristics—calorific value (CV) and ash content—have a profound impact on boiler size, furnace volume, and combustion system architecture. Using low-CV or high-ash fuel without adapting the boiler results in poor heat release, excessive slagging, overloading of ash handling systems, and ultimately decreased boiler efficiency and lifespan. Many operational failures and retrofit costs can be traced to improper fuel-characteristic-to-design matching. Successful boiler design starts with understanding how energy density and ash behavior influence combustion kinetics, heat transfer surface area, and furnace geometry.
Calorific value determines how much energy is available per unit of fuel, directly affecting the size of the combustion chamber and heat exchanger surface area. Lower CV fuels require larger furnaces to release the same energy. Meanwhile, ash content influences the design of ash handling systems, slag removal equipment, and furnace geometry. High ash fuels demand bigger combustion volumes, improved air distribution, and more robust cleaning systems to manage deposition and maintain efficiency.
These parameters not only define combustion performance but also determine the long-term reliability, cost-effectiveness, and scalability of coal-fired boiler installations.
Ash content has no significant impact on the size or configuration of a boiler's furnace.False
High ash content affects slagging, fouling, and ash accumulation, requiring larger furnaces, wider gas passes, and enhanced cleaning systems to maintain stable operation.
Understanding Calorific Value and Its Effect on Boiler Size
H3: Calorific Value Basics
Calorific value (CV), measured in MJ/kg or kcal/kg, represents the energy released during complete combustion of 1 kg of fuel. It determines the heat input required to produce a target output.
Coal Type | Typical CV (MJ/kg) | Heat Value (kcal/kg) |
---|---|---|
Anthracite | 28–33 | 6,700–7,900 |
Bituminous | 24–32 | 5,800–7,600 |
Sub-bituminous | 17–25 | 4,100–6,000 |
Lignite | 9–18 | 2,100–4,300 |
H3: Impact on Combustion Volume and Heat Exchange Area
Lower CV means:
More fuel mass must be burned to achieve the same heat output
Requires a larger furnace volume to ensure complete combustion
Increases flue gas volume, requiring more heat exchange surface
CV (MJ/kg) | Fuel Needed for 1,000 kW Output (kg/h) | Furnace Size Impact |
---|---|---|
30 (high CV) | ~120 | Compact |
20 (medium CV) | ~180 | Moderate |
10 (low CV) | ~360 | Large |
Example: A boiler using lignite will require nearly 3 times the fuel flow and furnace size of a similar system using anthracite.
Lower calorific value coal requires a larger combustion chamber to release the same amount of thermal energy as higher calorific value coal.True
Burning low-CV coal generates more flue gas and requires more residence time in the furnace, increasing combustion chamber size.
Understanding Ash Content and Its Effect on Furnace Design
H3: Ash Content Characteristics
Ash is the non-combustible residue left after coal burns, consisting of silica, alumina, iron oxide, lime, and trace metals. High ash coal creates:
Larger volumes of bottom and fly ash
More risk of slagging and fouling
Abrasive wear on surfaces
Coal Type | Typical Ash Content (%) |
---|---|
Anthracite | 8–12 |
Bituminous | 10–20 |
Sub-bituminous | 15–30 |
Lignite | 20–50+ |
H3: Boiler Design Adjustments for High Ash
High ash levels increase design complexity:
Wider furnace cross-section to avoid ash accumulation
Reduced heat flux near burners to avoid slagging
Enhanced ash hoppers, screw conveyors, and soot blowers
Cyclones or ESPs (Electrostatic Precipitators) for fly ash removal
Ash Content (%) | Required Design Features |
---|---|
<15% | Standard hopper and soot blower configuration |
15–30% | Larger grate area, more hopper volume, high-temp alloy walls |
>30% | Fluidized bed combustion, continuous ash removal, advanced cleaning |
Ash Fusion Temperature and Its Relevance
Ash fusion temperature (AFT) determines the softening point of ash. Lower AFT leads to slagging and clinker formation.
Ash Fusion Temperature (°C) | Operational Impact |
---|---|
>1,400 | Safe operation |
1,200–1,400 | Occasional slagging |
<1,200 | High risk, needs special furnace design |
Combined Effect: CV and Ash Interaction on Design
Both calorific value and ash content must be considered simultaneously.
Coal Type | CV (MJ/kg) | Ash Content (%) | Furnace Size | Ash System Complexity |
---|---|---|---|---|
Bituminous | 25–32 | 10–20 | Medium | Medium |
Sub-bituminous | 18–25 | 15–30 | Large | High |
Lignite | 10–18 | 30–50 | Very Large | Very High |
Anthracite | 28–33 | 8–12 | Small | Low |
Visual Sizing Impact Example
A 20 TPH boiler (steam output):
Coal Type | Furnace Volume (m³) | Ash Removal System |
---|---|---|
Bituminous | 50–70 | Manual/automatic hopper |
Sub-bituminous | 80–100 | Screw ash conveyor |
Lignite | 100–130 | Fluidized bed + bottom ash cooler |
Real-World Case: Cement Plant Conversion
Old coal: Bituminous (CV 26 MJ/kg, ash 12%)
New coal: Sub-bituminous (CV 18 MJ/kg, ash 28%)
Issues: Poor combustion, slag buildup
Retrofit:
Increased furnace width by 30%
Added continuous ash conveyor
Modified air staging and slag tapping
Results:
Restored steam output
Reduced maintenance downtime
Better fly ash capture with upgraded cyclone
Summary
Calorific value and ash content are fundamental to boiler and furnace design—not optional considerations. A fuel with low CV demands a larger combustion chamber, greater heat exchange area, and more fuel handling capacity. Meanwhile, high ash fuels require robust ash management systems, slag-resistant materials, and wider furnace geometries to prevent fouling and corrosion. When both factors are high (as in some low-grade coals), the system must be custom-engineered for fuel flexibility, long-term durability, and thermal efficiency. Correctly integrating CV and ash content into boiler design guarantees performance, compliance, and cost control.
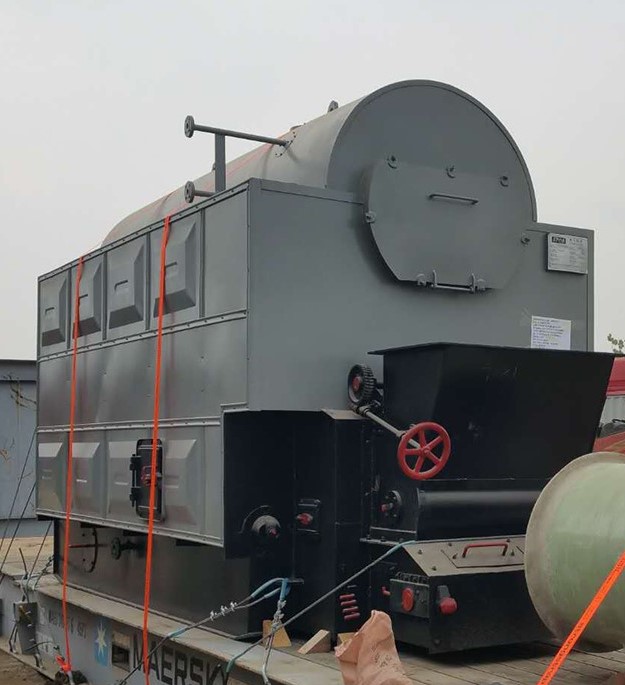
Why Do Volatile Matter and Moisture Content Matter in Combustion Performance?
When designing or operating a coal-fired boiler, combustion performance is the cornerstone of efficiency, stability, and emissions control. Two of the most influential but often misunderstood fuel properties are volatile matter (VM) and moisture content. These two parameters dictate how coal ignites, how flames propagate, and how much energy is actually available for useful heating. Improper handling of high-moisture or high-volatile fuels can result in flame instability, poor thermal conversion, high CO emissions, and boiler damage. Therefore, understanding how VM and moisture affect combustion is essential for choosing the right fuel, burner settings, and furnace design.
Volatile matter and moisture content significantly affect combustion performance by influencing ignition behavior, flame propagation, heat release rate, and efficiency. High volatile matter fuels ignite more easily and support stable flames, while low volatile coals need higher ignition temperatures and longer combustion times. High moisture content absorbs heat during vaporization, reducing flame temperature and thermal efficiency, and increasing fuel consumption. Together, these properties determine the energy release profile and combustion system requirements.
Failing to account for these characteristics can severely impair combustion quality and boiler reliability.
Moisture in coal helps combustion by increasing steam generation.False
Moisture in coal absorbs heat during vaporization, lowering flame temperature and reducing overall combustion efficiency. It does not contribute to steam generation.
What Is Volatile Matter and Why It Matters
Volatile matter refers to the gaseous hydrocarbons and tars released when coal is heated before combustion. These materials ignite quickly and form the initial flame front that supports further burning of the fixed carbon.
Coal Type | Volatile Matter (%) | Combustion Behavior |
---|---|---|
Anthracite | 2–8 | Slow ignition, needs high temperature |
Bituminous | 12–40 | Good ignition, strong flame propagation |
Sub-bituminous | 15–30 | Quick ignition, moderate flame |
Lignite | 25–40 | Very fast ignition, but lower flame stability |
H3: Influence of Volatile Matter on Combustion
Volatile Matter Level | Combustion Effect |
---|---|
Low (<10%) | Delayed ignition, needs high furnace temp |
Medium (10–20%) | Balanced ignition and burn rate |
High (>25%) | Fast ignition, easier flame stabilization |
Boiler Design Response:
High-VM coal: Suitable for chain grate or fluidized bed combustion
Low-VM coal: Needs pulverized coal system with high-temperature burner zone
Coals with high volatile matter content ignite more easily and support better flame stability.True
Volatile matter provides the gaseous fuel phase that ignites at lower temperatures and propagates the combustion flame.
Moisture Content and Its Combustion Impact
Moisture content refers to free and bound water in the coal. It must be evaporated during combustion—consuming energy without contributing to heat output.
Moisture Level (%) | Typical in Coal Type | Energy Penalty |
---|---|---|
5–10 | Bituminous, Anthracite | Minor efficiency drop |
15–30 | Sub-bituminous | Moderate energy loss |
30–50+ | Lignite, low-rank coal | Major energy loss, flame instability |
H3: How Moisture Reduces Combustion Performance
Consumes latent heat: ~2,260 kJ/kg required to evaporate water
Lowers flame temperature: Less energy remains for steam generation
Increases flue gas volume: More moisture in gas = more stack loss
Slows ignition and drying: Poor combustion near grates or burners
Fuel | CV (MJ/kg) | Moisture (%) | Thermal Efficiency Impact |
---|---|---|---|
Dry Bituminous | 25–30 | 5–10 | 85–90% |
Wet Sub-bituminous | 18–22 | 20–30 | 75–80% |
Lignite | 10–15 | 35–50 | 60–70% |
Combined Effect: Volatile Matter + Moisture
These two properties interact in determining:
Flame length and intensity
Air-fuel ratio requirements
Combustion air preheat needs
Soot, CO, and NOx emissions
Fuel Type | VM (%) | Moisture (%) | Combustion Challenge |
---|---|---|---|
Anthracite | 4–7 | 3–5 | Slow ignition, hard to maintain stable flame |
Bituminous | 12–40 | 5–15 | Balanced, preferred for boiler use |
Sub-bituminous | 20–30 | 15–30 | High flue loss, moderate combustion tuning |
Lignite | 25–40 | 30–50 | Flame instability, very low thermal efficiency |
Boiler Design Adjustments
For High Volatile Matter:
Use longer combustion zones to complete volatile burn
Optimize air staging to reduce NOx
Use multi-zone burners to stabilize flame
For High Moisture:
Include fuel drying system or air preheaters
Enlarge grate or combustion bed
Increase flue gas flow capacity
Design Element | High VM Fuel | High Moisture Fuel |
---|---|---|
Furnace volume | Moderate | Large |
Air ratio | Lean primary, rich secondary | High total air volume |
Combustion controls | Zonal burners, modulating air | Fuel moisture sensors, adaptive air flow |
Ash handling | Normal (unless dirty coal) | Increased due to unburned particles |
Real-World Example: Sugar Mill Boiler Conversion
Original fuel: Bituminous (VM 25%, moisture 8%)
New fuel: Lignite (VM 35%, moisture 40%)
Problems:
Low flame temperature
High CO and unburned carbon
Poor steam output
Retrofit actions:
Added primary fuel dryer
Modified air system with extra preheating
Increased furnace residence time
Results:
Steam output restored to target
CO reduced by 55%
Efficiency improved from 67% to 75%
Summary
Volatile matter and moisture content play critical roles in shaping the combustion characteristics of coal and biomass fuels. High VM makes ignition easier and improves flame stability, while low VM fuels require higher ignition energy and advanced burners. Moisture, on the other hand, is always a combustion penalty—absorbing heat, lowering flame temperature, and reducing thermal efficiency. Correctly evaluating and compensating for these parameters ensures optimal combustion performance, fuel efficiency, and boiler longevity. For any solid fuel combustion system, knowing your fuel’s VM and moisture is as important as knowing its calorific value.
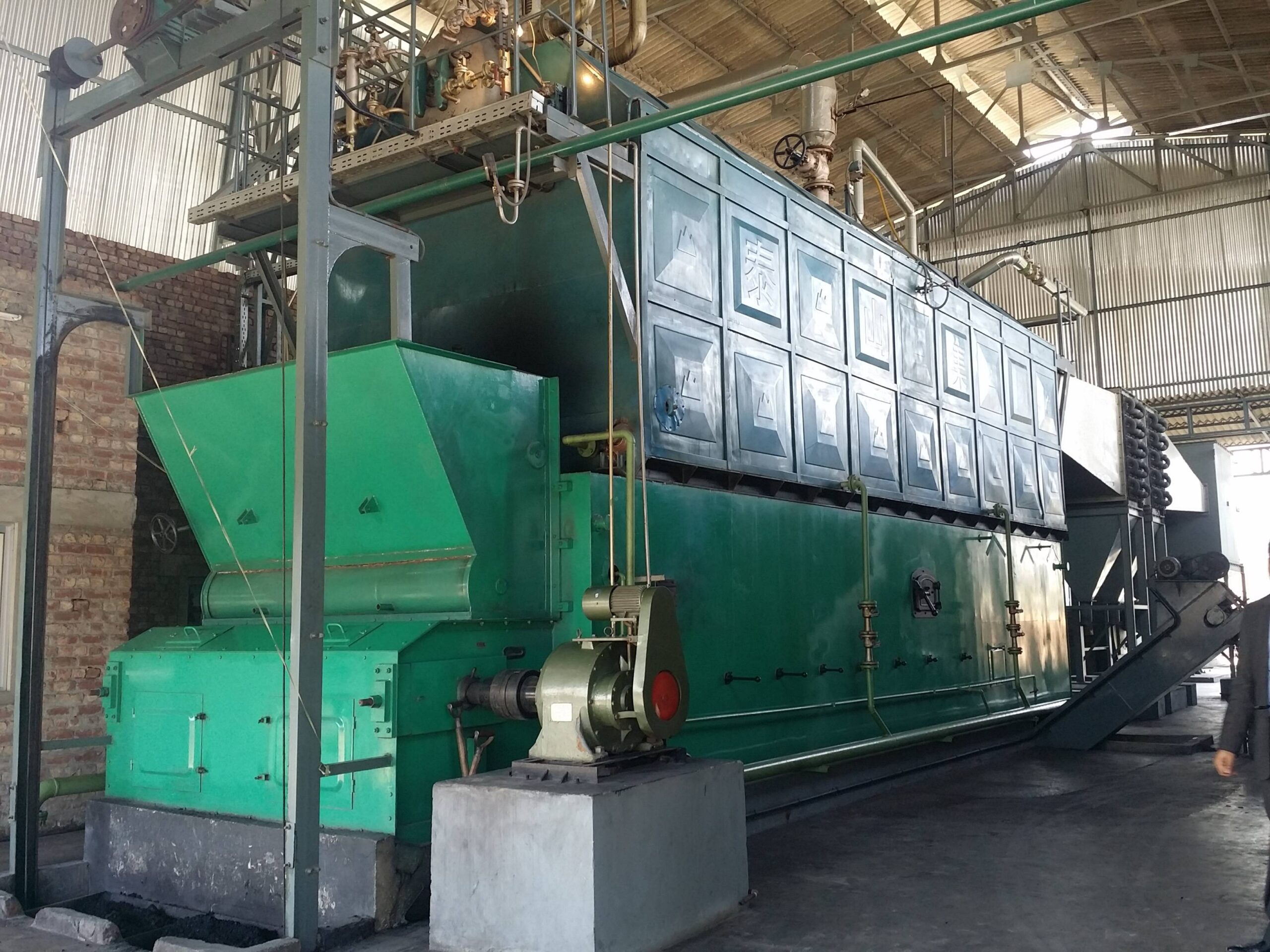
How Does Sulfur Content Affect Emissions and the Need for Desulfurization Systems?
In coal-fired boiler systems, sulfur content in fuel is a critical determinant of air pollutant emissions, system corrosion risk, and environmental compliance. During combustion, sulfur is released primarily as sulfur dioxide (SO₂) and, to a lesser extent, sulfur trioxide (SO₃). These gases contribute to acid rain, PM2.5 formation, and health hazards, and are heavily regulated worldwide. Ignoring sulfur levels can lead to emissions violations, boiler corrosion, and rapid equipment degradation. This is why coal selection, boiler design, and desulfurization system integration must all be coordinated based on the sulfur content of the fuel.
Sulfur content in coal directly influences the level of sulfur dioxide (SO₂) emissions during combustion, requiring appropriate flue gas desulfurization (FGD) systems to prevent environmental harm and comply with regulations. Higher sulfur levels demand more robust scrubbers or sorbent injection systems, while low-sulfur coals may reduce or eliminate the need for desulfurization. The choice of control technology, reagent type, and cost is driven by the amount and form of sulfur present in the fuel.
Managing sulfur effectively ensures cleaner combustion, regulatory compliance, and protection of downstream equipment.
Low-sulfur coals can be burned without the need for flue gas desulfurization systems in many jurisdictions.True
Coal with low sulfur content often produces SO₂ levels within permissible emission limits, reducing or eliminating the need for complex desulfurization systems, especially in small- to medium-scale plants.
Types and Levels of Sulfur in Coal
Sulfur in coal appears in three main forms:
Form of Sulfur | Description | Combustion Behavior |
---|---|---|
Pyritic Sulfur (FeS₂) | Inorganic sulfur bound to iron | Converts easily to SO₂ |
Organic Sulfur | Chemically bonded to coal matrix | Converts slowly to SO₂ |
Sulfate Sulfur | Minor; oxidized form (e.g., CaSO₄) | Stable, little conversion to SO₂ |
Coal Type | Typical Sulfur Content (%) | SO₂ Emissions Impact |
---|---|---|
Anthracite | 0.5–1.0 | Low |
Bituminous | 1.0–3.5 | Medium to High |
Sub-bituminous | 0.2–1.0 | Low to Moderate |
Lignite | 0.5–2.0 | Variable |
SO₂ Emissions and Environmental Impact
Sulfur converts to SO₂ at high temperatures:
S (in fuel) + O₂ → SO₂
Each 1% sulfur in coal can produce up to 20–25 kg of SO₂ per ton of coal burned.
Sulfur Content (%) | SO₂ Emission (g/Nm³) | Need for FGD |
---|---|---|
<0.5% | <300 | May not be required |
0.5–1.5% | 300–1,200 | Likely needed |
>1.5% | >1,200 | FGD mandatory |
SO₂ emissions increase linearly with sulfur content in coal during combustion.True
The amount of SO₂ generated is directly proportional to the sulfur content in the coal, assuming complete combustion.
Desulfurization System Types and Their Suitability
Technology | Process Type | SO₂ Removal Efficiency (%) | Best Suited For |
---|---|---|---|
Wet Limestone Scrubber | Absorptive (wet) | 90–98% | Large utility or industrial boilers |
Dry Sorbent Injection (DSI) | Adsorptive (dry) | 50–80% | Medium plants, retrofit-friendly |
Spray Dry Scrubber (SDA) | Semi-dry | 80–95% | Medium to large plants with space |
Circulating Fluidized Bed | In-furnace reaction | 70–90% | Low-grade coal, high ash and sulfur |
Regenerative FGD | Sorbent recovery | 90–99% | High-end systems with sulfur recovery |
Desulfurization Equipment Integration with Boiler
H3: Equipment Layout Considerations
System Location | Purpose |
---|---|
After economizer | Cools flue gas for scrubbing |
Pre-stack | SO₂ removal zone |
Recirculation fan zone | Keeps scrubber pressure balanced |
Boiler control systems must be tightly linked to the FGD system to manage:
Flue gas temperature
Flow rate changes
Reagent feed rates (lime, limestone, etc.)
Sulfur Content and Fuel Selection Strategy
Sulfur Content | Coal Strategy | System Impact |
---|---|---|
Low (<0.5%) | No or minimal scrubber | Reduced CAPEX/OPEX |
Medium (0.5–1.5%) | Moderate FGD system or in-furnace control | Moderate operational complexity |
High (>1.5%) | Advanced wet FGD system + sorbent management | High cost, higher water and reagent use |
Real-World Case Study: Textile Boiler Retrofit
Old coal: Sub-bituminous, S = 0.6%
New coal: High-sulfur bituminous, S = 2.4%
Initial result: SO₂ emissions exceeded 1,800 mg/Nm³ (limit = 600 mg/Nm³)
Retrofit: Installed spray dry absorber + lime injection system
Post-retrofit emissions: ~280 mg/Nm³
Efficiency: 88% SO₂ reduction
Added OPEX: $4.50/ton of coal burned
Summary
Sulfur content is a decisive factor in both emissions performance and system design for coal-fired boilers. High sulfur coal increases SO₂ emissions significantly, which triggers the need for flue gas desulfurization (FGD) systems such as scrubbers or sorbent injectors. Depending on the sulfur form and concentration, the design and cost of these systems can vary dramatically. Choosing the appropriate fuel or control technology based on sulfur content helps ensure environmental compliance, reduce acid corrosion risk, and protect human health. In essence, effective sulfur management is essential for cleaner combustion and sustainable boiler operation.
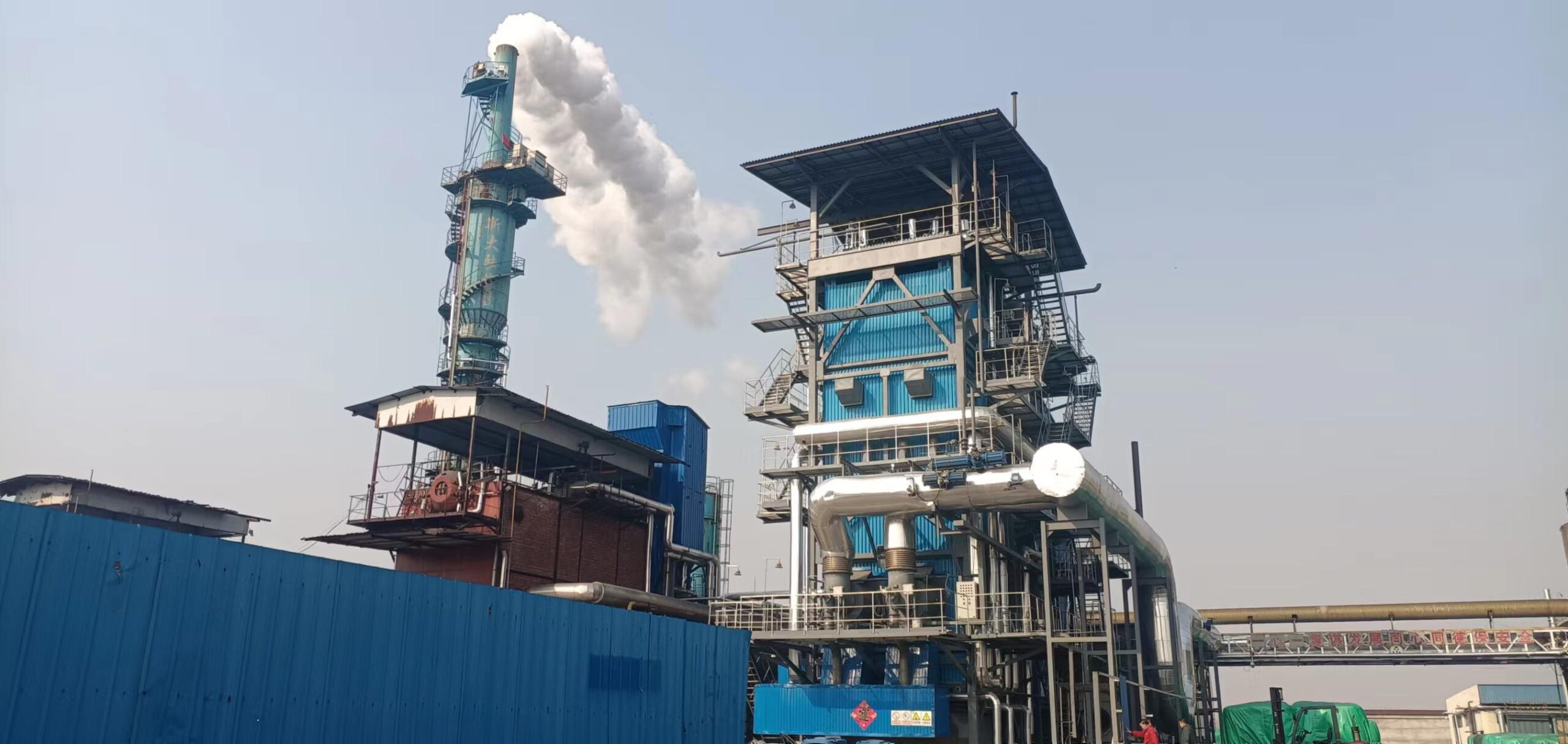
What Role Does Coal Grindability and Slagging Tendency Play in Boiler Selection?
In coal-fired boiler engineering, coal grindability and slagging tendency are two of the most decisive—but often underappreciated—fuel properties affecting boiler type selection, combustion efficiency, and long-term maintenance requirements. If the coal is difficult to grind, fuel preparation becomes energy-intensive and slows combustion response. If the coal has high slagging potential, it can rapidly form deposits in the furnace, reducing heat transfer and causing unplanned shutdowns. These characteristics directly impact the choice between pulverized coal (PC), fluidized bed (FBC), stoker, or chain grate systems, as well as material specifications and ash management strategies. Properly evaluating grindability and slagging behavior avoids costly mismatches between fuel and boiler technology.
Coal grindability and slagging tendency determine the suitability of a boiler system for a given fuel by affecting how easily the coal can be pulverized and how much ash deposition occurs during combustion. Low grindability coals require more energy for size reduction and favor systems like fluidized beds, while high-slagging coals demand boilers with larger furnace volume, slag-resistant materials, and advanced ash removal systems. Matching boiler design to these properties ensures stable combustion, high efficiency, and reduced fouling and maintenance.
Boiler performance is not just about how much coal you burn—it’s about how that coal behaves before and during combustion.
Coal grindability does not significantly impact boiler type or design.False
Coal grindability determines how much energy is needed to pulverize the fuel. Boilers relying on fine coal particles, like pulverized coal systems, require coals with high grindability for stable and cost-effective operation.
Understanding Coal Grindability (HGI) and Its Design Implications
H3: What Is HGI?
Hardgrove Grindability Index (HGI) measures how easily coal can be ground into fine powder for combustion. It’s a unitless number between 30 and 100:
HGI Value | Grinding Behavior |
---|---|
<45 | Very hard to grind |
45–60 | Medium grindability |
60–80 | Good grindability |
>80 | Easily pulverized |
Coal Type | Typical HGI |
---|---|
Anthracite | 35–50 |
Bituminous (low ash) | 60–85 |
Sub-bituminous | 45–65 |
Lignite | 70–100 |
H3: How Grindability Affects Boiler Selection
Boiler Type | HGI Suitability | Why It Matters |
---|---|---|
Pulverized Coal (PC) | HGI > 60 | Requires finely ground coal for stable suspension firing |
Fluidized Bed (CFB/FBC) | HGI > 45 (flexible) | Tolerates coarser coal, ideal for low-HGI fuels |
Chain Grate/Stoker | Any (coarse feed possible) | Coal fed in lumps or granules—no fine grinding needed |
Low-HGI coals increase:
Energy consumption in pulverizers
Mill wear and downtime
Particle size variability, affecting flame stability
Pulverized coal boilers require high-grindability coals to ensure effective fuel atomization and combustion.True
Fine, consistent coal particle size is essential for stable flame propagation in PC boilers, making high HGI values desirable.
Slagging Tendency and Its Influence on Furnace Design
H3: What Is Slagging?
Slagging is the formation of molten or semi-molten ash deposits on furnace surfaces, caused by:
Low ash fusion temperatures
High furnace temperatures
Ash composition (Na₂O, Fe₂O₃, SiO₂ ratios)
It reduces heat transfer, narrows flue paths, and can damage tubes.
Slagging Index | Description |
---|---|
<0.6 | Low slagging potential |
0.6–2.0 | Medium risk |
>2.0 | High slagging tendency |
H3: How Slagging Impacts Boiler Design
High Slagging Coal | Required Boiler Design Features |
---|---|
Lignite, high-Na coal | Wider furnace cross-section |
Bituminous with high Fe₂O₃ | Slag-tapping furnace or larger refractory areas |
Low ash fusion temp fuel | Tube shields and slag hoppers |
H3: Slagging Control Measures
Method | Purpose |
---|---|
Lower excess air | Reduces peak flame temperature |
Fuel blending | Dilutes slag-forming compounds |
Refractory lining | Protects hot spots from slag adhesion |
On-load cleaning | Keeps surfaces clear with sonic or steam blowers |
Combined Effect: Grindability + Slagging on Boiler System Choice
Coal Profile | Best Boiler Type | Design Response |
---|---|---|
High HGI, Low Slagging | Pulverized Coal Boiler | Compact furnace, minimal cleaning systems |
Low HGI, High Slagging | Fluidized Bed Boiler | Coarse feed, wide bed, high ash handling |
Medium HGI, Medium Slagging | Chain Grate or CFB | Large grate, mechanical ash removal |
Low HGI, Low Slagging | FBC or Stoker | Simple air staging and coarse feed burner |
Boiler Component Impact Chart
Component | Effect of Low HGI | Effect of High Slagging |
---|---|---|
Pulverizer | Higher wear, energy use | Not applicable |
Furnace | None directly | Larger volume, slag-resistant linings |
Superheater | Poor flame due to coarse particles | Slag insulation = reduced heat transfer |
Air System | Requires tighter fuel-air control | May require staged air for temp control |
Ash Handling | Standard | Robust grates, hoppers, conveyors |
Real-World Example: Power Plant Coal Changeover
Original coal: Bituminous (HGI = 70, slag index = 0.8)
New coal: Sub-bituminous (HGI = 45, slag index = 2.4)
Issues:
Pulverizer overload and wear
Furnace slagging in superheater zone
Solution:
Switched to CFB boiler design
Installed larger ash coolers
Added real-time fuel blending system
Result:
25% reduction in maintenance downtime
Improved combustion uniformity
Ash melting managed through air staging
Summary
Coal grindability and slagging tendency are core design parameters for selecting and engineering an industrial boiler system. High-grindability coals enable efficient pulverization and are well-suited to PC boilers, while low-HGI fuels favor robust systems like fluidized beds. Slagging-prone coals require careful furnace geometry, air control, and ash removal design. By aligning the boiler system to match these two critical coal properties, operators ensure long-term stability, cleaner combustion, and lower maintenance costs. Selecting the right boiler isn’t just about output—it’s about understanding the behavior of your fuel.
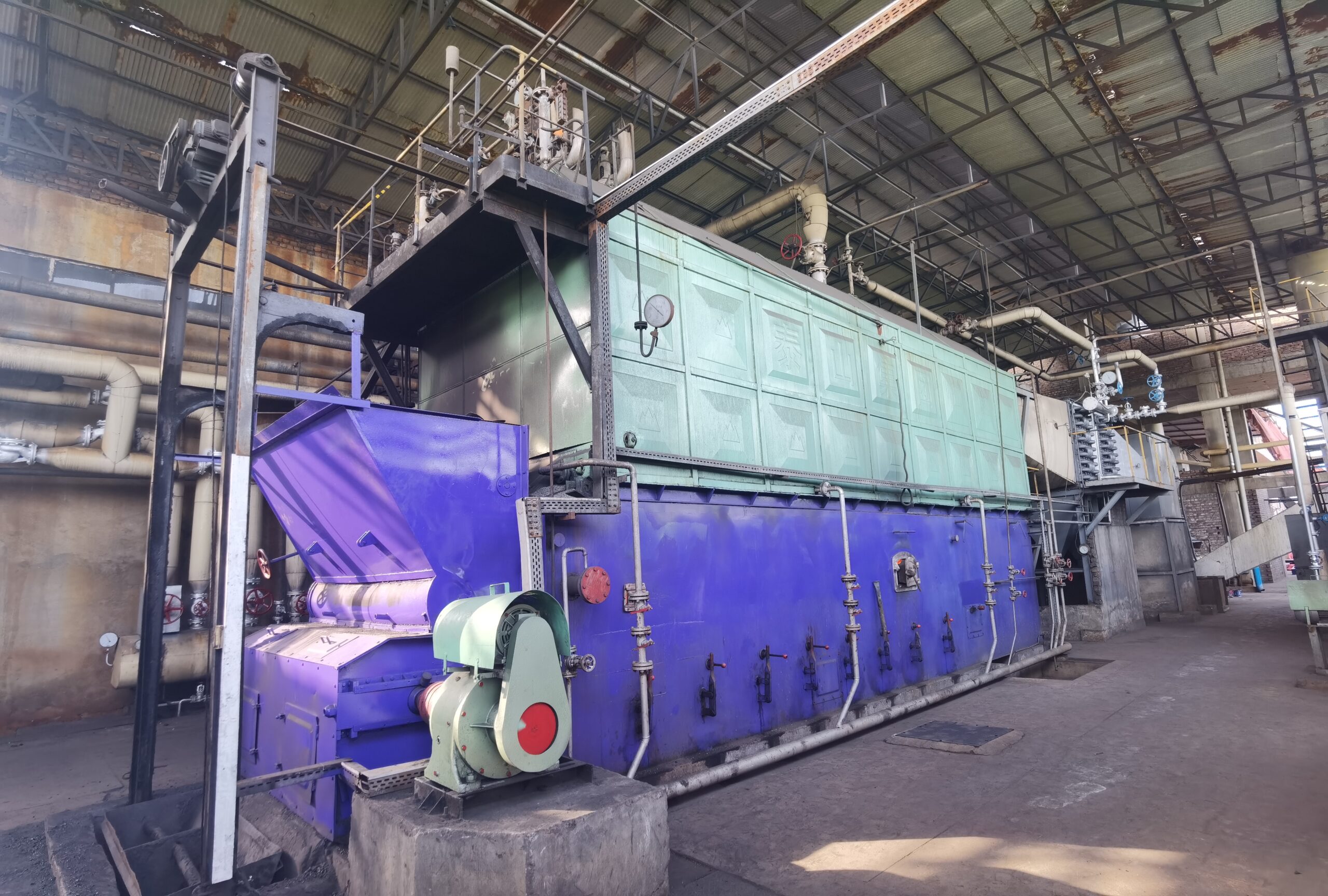
How Can Boiler Systems Be Adapted for Mixed or Low-Grade Coal Fuels?
In many parts of the world, industrial users have limited access to premium, high-rank coal. Instead, they must rely on low-grade or mixed coal fuels—characterized by low calorific value, high moisture, high ash, and variable volatile matter. However, standard boiler designs optimized for consistent, high-grade coal struggle to handle these inferior fuels. The result? Incomplete combustion, excessive slagging, high particulate emissions, and frequent shutdowns. Fortunately, with the right engineering adaptations—ranging from fuel preparation to combustion control and ash handling—boiler systems can be effectively modified or designed to reliably and efficiently burn even the most challenging coal blends.
Boiler systems can be adapted for mixed or low-grade coal fuels by incorporating fuel-flexible furnace designs, enhanced air staging, larger combustion chambers, fluidized bed or chain grate technologies, ash-resistant materials, and intelligent combustion control systems. These modifications compensate for variability in fuel properties such as calorific value, ash content, and moisture, ensuring stable combustion, reduced emissions, and improved thermal efficiency. Effective adaptation also includes fuel homogenization, feed system optimization, and real-time fuel quality monitoring.
Adaptation is not just about burning difficult fuels—it’s about optimizing performance with resilience, safety, and sustainability in mind.
Standard pulverized coal boilers can handle low-grade, high-moisture coal without any modifications.False
Standard PC boilers are designed for consistent, high-energy fuel. Low-grade, high-moisture coals require additional furnace volume, drying capacity, and ash management systems to perform efficiently.
Core Challenges with Low-Grade or Mixed Coal
Property | Issue Caused |
---|---|
Low Calorific Value (CV) | Requires higher fuel flow, larger combustion zones |
High Moisture | Reduces flame temperature, lowers combustion efficiency |
High Ash Content | Causes slagging, fouling, increases ash handling load |
Variable Volatile Matter | Affects ignition, flame stability |
Unstable Composition | Requires constant adjustment to air/fuel ratio |
Key Boiler Adaptations for Low-Grade and Mixed Coals
H3: 1. Use of Fluidized Bed Combustion (FBC or CFB)
Feature | Benefit for Low-Grade Fuel |
---|---|
Combustion at lower temp (850–900°C) | Minimizes slagging and NOx |
High turbulence in bed | Promotes complete combustion of coarse or wet coal |
Ability to burn wide range of fuel CV (10–25 MJ/kg) | Ideal for blends and low-rank fuels |
Fluidized bed boilers are the preferred choice for mixed or low-CV coals due to their inherent flexibility and high ash tolerance.
H3: 2. Larger and Deeper Furnace Design
Design Modification | Purpose |
---|---|
Increased residence time | Ensures full combustion of volatile and char phases |
Wider cross-section | Prevents ash agglomeration and fouling |
Reduced heat flux zones | Avoids clinker formation from fusible ash |
H3: 3. Advanced Air Staging and Distribution
Staging Zone | Function in Mixed Coal Combustion |
---|---|
Primary air (beneath grate or bed) | Ensures fuel drying and initial ignition |
Secondary air (above bed or flame zone) | Burns volatile matter, controls NOx |
Tertiary air (for reburn or cleanup) | Stabilizes flame and ensures full burnout |
Air staging must be adjustable and automated to adapt to fuel variability in real time.
H3: 4. Fuel Preprocessing: Drying, Blending, and Sizing
Adaptation | Why It Matters |
---|---|
Coal blending silos | Homogenizes CV and ash profile |
Pre-drying system | Reduces moisture to improve combustion stability |
Screen/sizer at feed | Maintains consistent particle size distribution |
Pre-drying of high-moisture coals significantly improves combustion efficiency and flame temperature.True
Drying removes excess moisture that otherwise consumes combustion energy, improves flame stability, and increases net calorific input.
Combustion Control and Monitoring System Upgrades
Smart Control Features for Mixed Coal Operation
System Function | Adaptation Purpose |
---|---|
Real-time fuel CV monitoring | Adjust air-fuel ratio on the fly |
Flue gas analyzer (O₂, CO, SO₂) | Optimize combustion and emissions control |
Dynamic burner control | Modulate primary/secondary air depending on VM |
Thermal camera or flame scanner | Detect hot spots or cold zones in furnace |
AI-based adaptive controls are increasingly used for continuous optimization in coal-mixed fuel environments.
Ash Handling and Slag Management Adaptations
For High Ash and Slagging Potential
System Element | Adaptation for High Ash Fuels |
---|---|
Bottom ash hopper | Enlarged and water-cooled for slag collection |
Soot blowers | High-frequency pulse or steam type |
Tube shields | Installed in superheater and water wall zones |
Fuel additives (e.g. kaolin, dolomite) | Used to increase ash fusion point |
In high-slag environments, slag-tapping furnaces or ash fusion sensors are also employed.
Real-World Comparison Table: Conventional vs. Adapted Boiler for Low-Grade Coal
Feature | Standard PC Boiler | Adapted FBC/Hybrid Boiler |
---|---|---|
Min CV Handling | >22 MJ/kg | 9–25 MJ/kg |
Max Moisture | <15% | Up to 50% |
Ash Content Tolerance | <20% | Up to 50% |
Feed Flexibility | Uniform only | Multiple coals and biomass blends |
Emissions (NOx, SO₂) | Moderate–High (requires SCR/FGD) | Lower (in-bed desulfurization) |
Furnace Cleaning Frequency | Weekly | Monthly or quarterly |
Case Study: Cement Kiln Auxiliary Boiler – Lignite + Petcoke Mix
Fuel Mix: 60% lignite (CV = 12 MJ/kg, ash = 38%) + 40% petcoke (CV = 28 MJ/kg, sulfur = 5.2%)
Boiler Type: Retrofitted CFB boiler, 15 TPH steam
Adaptations:
Lime injection in bed for SO₂ capture
Furnace widened by 30%
Dual fuel metering system
Upgraded ESP for high ash content
Result:
92% combustion efficiency
SO₂ emissions < 350 mg/Nm³
Stable operation across fuel CV shifts of ±15%
Summary
Successfully burning mixed or low-grade coals in industrial boilers requires a holistic approach to combustion design, fuel handling, and emission control. Adaptations like fluidized bed combustion, enlarged furnace geometry, advanced air staging, pre-drying, and intelligent controls make it possible to harness even the most difficult fuels safely and efficiently. As fuel markets shift and energy security becomes critical, flexibility in fuel type is no longer optional—it’s a strategic advantage. Properly adapted boiler systems turn variable, low-quality coal into a reliable, cost-effective energy source for the future.
🔍 Conclusion
Coal is not a one-size-fits-all fuel. Its chemical and physical properties directly impact boiler configuration, combustion strategy, and emissions control systems. A well-matched industrial coal-fired boiler ensures complete combustion, high thermal efficiency, and compliance with local environmental regulations. Failing to consider coal’s characteristics can lead to underperformance, frequent breakdowns, and non-compliance penalties. Always design your boiler system around the coal you plan to use.
📞 Contact Us
💡 Need help matching your boiler to your coal type? Our team of engineers provides coal analysis, system design, and technical support to ensure optimal performance and emissions compliance.
🔹 Contact us today for a fuel-to-boiler compatibility consultation built for your industrial needs! 🏭🔥🪨
FAQ
How do different coal types impact coal-fired boiler selection?
Coal varies by rank—such as lignite, sub-bituminous, bituminous, and anthracite—each with unique calorific values, moisture content, ash levels, and volatile matter. These properties affect combustion efficiency, heat output, and boiler design requirements.
What are key combustion characteristics of coal?
Important characteristics include ash content, fixed carbon, volatile matter, sulfur content, and grindability. High ash or sulfur requires enhanced emission controls, while low volatility coal may need preheating or specialized burners for stable combustion.
Why is fuel preparation important in coal-fired systems?
Coal must be properly sized and sometimes pulverized for uniform combustion. The grindability of the coal determines the type of coal mill needed, which affects operational efficiency and maintenance frequency.
How does coal quality affect boiler efficiency and emissions?
Low-quality coal with high moisture or ash reduces thermal efficiency and increases slagging, fouling, and pollutant emissions. Boilers must be optimized for specific coal grades to maintain performance and regulatory compliance.
Can coal-fired boilers be adapted for various coal types?
Yes. Industrial coal-fired boilers can be designed or modified to burn multiple coal types by adjusting combustion settings, adding fuel preparation systems, or integrating flexible air/fuel controls. This enhances versatility and fuel sourcing flexibility.
References
Coal Properties and Boiler Performance – https://www.energy.gov
Combustion Characteristics of Coal – https://www.sciencedirect.com
Coal-Fired Boiler Design Principles – https://www.researchgate.net
Coal Handling and Preparation – https://www.epa.gov
Coal Rank and Fuel Efficiency – https://www.bioenergyconsult.com
Industrial Emissions and Coal Quality – https://www.mdpi.com
Ash & Sulfur Management in Boilers – https://www.energysavingtrust.org.uk
Fuel Flexibility in Coal-Fired Boilers – https://www.iea.org
Boiler Adaptability and Retrofits – https://www.automation.com
Optimizing Combustion for Coal Types – https://www.sciencedirect.com
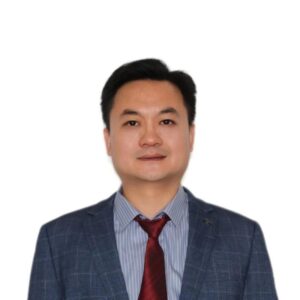