When selecting an industrial gas-fired boiler, many buyers focus primarily on size, pressure, and cost—yet fuel type and combustion properties are equally critical. Choosing the wrong configuration for your specific gas type can lead to inefficient combustion, higher emissions, equipment damage, and excessive operational costs. To ensure maximum performance, safety, and long-term value, it’s essential to understand how different gas fuels and their combustion behaviors influence boiler selection and design.
Fuel types and combustion characteristics affect your choice of industrial gas-fired boiler by influencing burner design, flame stability, combustion temperature, emissions profile, and heat transfer efficiency. Common fuel gases like natural gas, liquefied petroleum gas (LPG), biogas, and hydrogen blends differ in calorific value, pressure, ignition properties, and combustion air requirements. These differences impact boiler configuration, safety systems, emission controls, and automation settings. A properly matched boiler-fuel setup is essential for optimized performance, minimal downtime, and regulatory compliance.
Whether you’re using pipeline natural gas or considering alternative fuels like biogas or hydrogen, the right knowledge ensures a safer and more cost-effective investment.
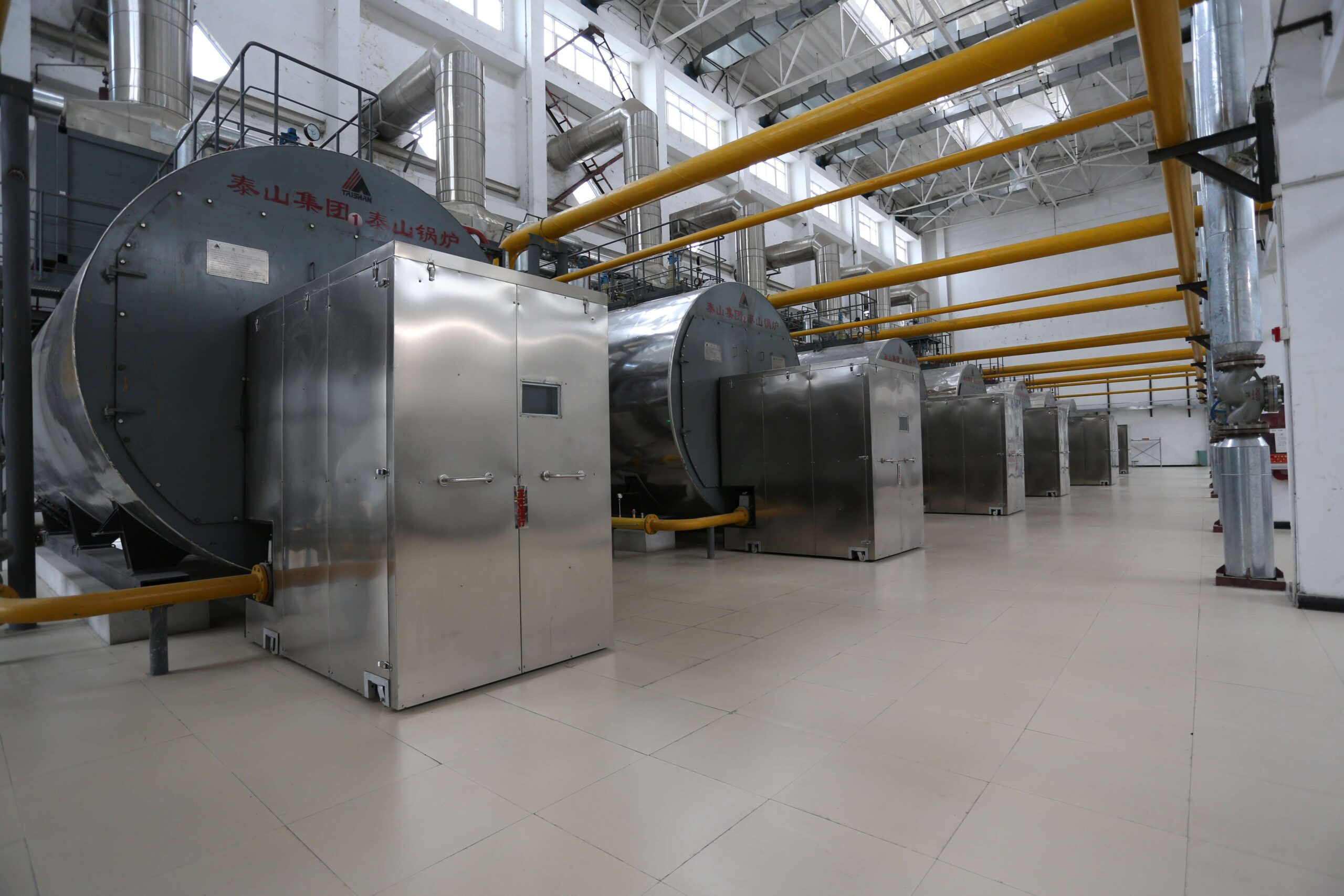
What Types of Fuel Gases Are Commonly Used in Industrial Gas-Fired Boilers?
In industrial production and heating systems, gas-fired boilers are the heartbeat of operations—but choosing the wrong fuel gas can lead to higher costs, increased emissions, and efficiency issues. Many users face the dilemma of understanding which type of fuel gas is most suitable for their specific application. A misstep here not only impacts performance but could also result in non-compliance with environmental standards. The solution lies in knowing the characteristics, advantages, and limitations of each commonly used industrial fuel gas. This article provides a comprehensive guide to help you make informed decisions when selecting a fuel gas for your industrial gas-fired boiler.
The most commonly used fuel gases in industrial gas-fired boilers include natural gas, liquefied petroleum gas (LPG), biogas, and syngas. Natural gas is the dominant choice due to its high calorific value, clean combustion, and wide availability. LPG, primarily composed of propane and butane, is favored for its portability and higher heating value per volume. Biogas and syngas are often used in waste-to-energy and biomass applications due to their renewable nature, although they require specific burner designs.
Understanding the pros and cons of each type of fuel gas is essential for industrial facility managers, procurement officers, and engineers. The remainder of this article explores their properties, performance, efficiency, environmental impacts, and typical applications in gas-fired boilers.
Natural gas is the most commonly used fuel in industrial gas-fired boilers.True
Natural gas is widely used because of its high energy content, clean combustion, and established distribution networks.
Key Characteristics of Common Industrial Boiler Fuel Gases
Industrial gas-fired boilers are engineered to work with specific fuel gas types based on combustion characteristics, availability, and cost. Below is a comprehensive overview of each major fuel gas category:
Natural Gas
Natural gas, composed mainly of methane (CH₄), is the most popular choice for industrial boilers due to its clean-burning properties and efficient heat generation. It has a high calorific value, typically around 38 MJ/m³, and a relatively low carbon footprint compared to other fossil fuels.
Property | Natural Gas |
---|---|
Main Component | Methane (CH₄) |
Heating Value | 35–40 MJ/m³ |
Flame Temperature | ~1,950°C |
Availability | High (via pipelines) |
Environmental Impact | Low CO₂, very low SOx/NOx |
Technical Considerations:
Requires precise air-fuel ratio control
Low impurity levels reduce maintenance
Standard in most developed industrial networks
Liquefied Petroleum Gas (LPG)
LPG is a blend of propane (C₃H₈) and butane (C₄H₁₀), offering higher energy density than natural gas, making it ideal for remote sites lacking pipeline access.
Property | LPG (Propane/Butane) |
---|---|
Heating Value | ~93 MJ/m³ (propane) |
Storage | Pressurized tanks |
Flame Temperature | ~1,980°C |
Transportability | High |
Environmental Impact | Cleaner than diesel/oil |
Technical Considerations:
Requires pressurized tanks and regulators
Burner compatibility must be ensured
Higher carbon content than natural gas
Biogas
Biogas is produced via anaerobic digestion of organic waste, primarily containing methane and carbon dioxide. It is a renewable energy source and often used in conjunction with wastewater treatment or agricultural operations.
Property | Biogas |
---|---|
Methane Content | 50–70% |
Heating Value | 20–25 MJ/m³ |
CO₂ Content | 30–50% |
Source | Organic waste |
Environmental Impact | Renewable, carbon-neutral |
Technical Considerations:
Requires gas scrubbing/purification
Variable composition affects burner tuning
Needs corrosion-resistant components
Syngas (Synthetic Gas)
Syngas is produced via gasification of coal, biomass, or waste. It contains hydrogen, carbon monoxide, and traces of methane, making it highly versatile but challenging to manage.
Property | Syngas |
---|---|
Composition | H₂, CO, CH₄, CO₂ |
Heating Value | 10–20 MJ/m³ |
Source | Biomass, waste, coal |
Storage | On-demand production |
Environmental Impact | Low to moderate (depends on source) |
Technical Considerations:
Requires custom burner systems
Lower calorific value needs compensation in design
High combustion control precision is necessary
Comparison Table of Fuel Gas Suitability for Industrial Boiler Applications
Fuel Gas Type | Energy Density | Clean Combustion | Cost Effectiveness | Availability | Boiler Compatibility |
---|---|---|---|---|---|
Natural Gas | High | Excellent | High | Excellent | Broad |
LPG | Very High | Very Good | Moderate | Good | Requires adjustment |
Biogas | Medium | Good (if purified) | Low (if in-house) | Site-dependent | Custom design required |
Syngas | Low to Medium | Variable | Moderate | Moderate | Specialized equipment |
Advanced Considerations in Fuel Gas Selection
H3: Environmental Compliance
Industrial boilers must comply with regional emission limits for NOx, SOx, CO₂, and particulates. Natural gas and biogas offer the lowest emissions, while LPG emits slightly more CO₂ per unit of energy due to its higher carbon content.
H3: Burner and Control System Adaptability
Each fuel gas demands a distinct burner design and control strategy:
Natural gas burners feature premix or nozzle-mix designs.
LPG systems require adjustable orifices and flame retention heads.
Biogas and syngas require real-time combustion monitoring and oxygen trimming systems due to inconsistent calorific values.
Gas Type | Requires Gas Train Modifications? | Air-Fuel Ratio Tolerance | Control System Complexity |
---|---|---|---|
Natural Gas | No | Narrow | Standard |
LPG | Yes (pressure reduction) | Moderate | Moderate |
Biogas | Yes (scrubber, filters) | Wide | High |
Syngas | Yes (burner redesign) | Very Wide | Very High |
H3: Real-World Case Study – Switching from Diesel to Natural Gas
A textile manufacturer in Bangladesh transitioned its 10-ton steam boiler from diesel to natural gas. The switch resulted in:
30% fuel cost savings
60% lower carbon emissions
Improved combustion efficiency (from 78% to 92%)
However, the change required:
New burner retrofitting
Pipeline connection to local gas grid
Automated safety controls upgrade
Ending Summary
Selecting the right fuel gas for industrial gas-fired boilers is not just about energy cost—it’s about optimizing system efficiency, ensuring environmental compliance, and matching technical compatibility. From natural gas and LPG to renewable biogas and engineered syngas, each option offers unique advantages and requires careful evaluation. For many operations, natural gas remains the best combination of performance, availability, and emission control. Meanwhile, biogas and syngas are gaining ground in green industrial applications. A detailed analysis of fuel properties, combustion dynamics, and local infrastructure is essential for long-term success.

How Do Calorific Value and Combustion Air Ratio Affect Boiler Sizing and Efficiency?
In industrial heating and process environments, selecting the right boiler size and maximizing combustion efficiency is vital for energy savings and environmental compliance. However, many users overlook the critical impact of two fundamental combustion parameters: the calorific value of the fuel and the combustion air ratio. Misjudging these can lead to undersized or oversized boilers, wasted fuel, increased emissions, and even premature equipment failure. Understanding the interplay between fuel energy content and air-to-fuel mixture is key to optimizing boiler design and operation. This article will guide you through how calorific value and combustion air ratio directly influence boiler sizing and efficiency.
Calorific value determines the amount of energy a fuel can release during combustion, while the combustion air ratio governs how efficiently that energy is converted into usable heat. A higher calorific value allows smaller boilers to produce the same energy output, while an improper air ratio—especially excess air—reduces efficiency by absorbing heat into unused oxygen and nitrogen. Together, these two parameters critically affect boiler sizing, thermal performance, and fuel economy.
If you’re designing or upgrading a boiler system, getting these two parameters right is essential to avoid energy waste and oversized equipment. Let’s now dive deeper into the technical mechanics and practical implications of each.
Higher calorific value fuels require smaller boilers to achieve the same thermal output.True
Boilers are sized based on the heat input required to meet thermal demands, so a fuel with higher energy content reduces the volume of combustion gases and the heat exchanger surface area needed.
Understanding Calorific Value in Boiler Sizing
The calorific value (CV) of a fuel is the amount of energy released during complete combustion of a unit quantity of the fuel—usually expressed in MJ/m³ for gases or MJ/kg for solids/liquids. It directly determines how much fuel is needed to achieve a desired thermal output.
Fuel Type | Gross CV (MJ/m³) | Net CV (MJ/m³) | Typical Use in Boilers |
---|---|---|---|
Natural Gas | 38–42 | 35–39 | Standard industrial boiler fuel |
LPG (Propane) | ~93 | ~85 | Off-grid or mobile applications |
Biogas | 20–25 | 17–22 | Renewable energy & digestion sites |
Syngas | 10–20 | 8–17 | Biomass, waste-to-energy |
Diesel (liquid) | 45–46 MJ/kg | ~43 MJ/kg | Backup and mobile boilers |
Calorific Value and Boiler Sizing Formula
The required boiler thermal input is calculated using the desired output and system efficiency.
Then, the fuel flow rate needed depends on the CV:
Higher CV → Lower fuel flow rate → Smaller combustion chamber → Smaller boiler footprint.
Example: To generate 1,000 kW of steam at 90% efficiency:
Using natural gas (CV = 38 MJ/m³):
10000.9=1111 kW input⇒111138=29.2 m³/h gas\frac{1000}{0.9} = 1111 \text{ kW input} \Rightarrow \frac{1111}{38} = 29.2 \text{ m³/h gas}
Using biogas (CV = 22 MJ/m³):
111122=50.5 m³/h gas\frac{1111}{22} = 50.5 \text{ m³/h gas}
This affects burner size, combustion chamber design, and heat exchanger dimensions.
Combustion air ratio has little effect on boiler efficiency.False
Excess air beyond optimal levels reduces boiler efficiency by carrying away heat in flue gases and lowering flame temperature.
Combustion Air Ratio and Its Efficiency Impact
The combustion air ratio is the ratio of actual air supplied to the stoichiometric air required for perfect combustion. This ratio profoundly impacts flame stability, combustion completeness, and heat loss in flue gases.
Air Ratio (λ) | Description | Typical Efficiency Impact |
---|---|---|
λ = 1.0 | Stoichiometric (ideal) | Theoretical max, but unsafe |
λ = 1.1–1.3 | Controlled excess air | Peak practical efficiency |
λ > 1.5 | High excess air | Efficiency drop >5–10% |
λ < 1.0 | Air-deficient (rich flame) | CO formation, safety hazard |
How Excess Air Affects Efficiency
When excess air increases:
More cold air enters combustion chamber → Heat absorbed by nitrogen and unused oxygen
Flue gas temperature rises without increasing useful heat → Lost energy
Flame temperature drops → Incomplete combustion, higher CO emissions
Air Ratio | Typical Stack Temp (°C) | Boiler Efficiency (%) |
---|---|---|
1.1 | 180 | 91 |
1.3 | 220 | 89 |
1.5 | 270 | 85 |
2.0 | 320 | 80 |
Maintaining optimal air ratio is critical to reducing fuel usage and meeting emissions standards.
Interaction Between Calorific Value and Air Ratio
When evaluating both parameters for sizing and performance:
Low-CV fuels (e.g., biogas, syngas) require larger combustion chambers and higher air flow → increased flue gas volume and pressure loss
High-CV fuels enable compact burner design but demand precise air ratio control due to hotter flame temperatures
For fuels with variable CV (biogas, landfill gas), adaptive combustion controls and oxygen trim systems are essential
Fuel | CV | Ideal λ | Key Control Strategy |
---|---|---|---|
Natural Gas | High | 1.1–1.2 | PID + O₂ trim |
LPG | Very High | 1.1 | Tight excess air margin |
Biogas | Low | 1.3–1.5 | Real-time calorific adjustment |
Syngas | Low | 1.4–1.7 | Variable burner + flame monitoring |
Practical Boiler Design Implications
Combustion Chamber Sizing
Boiler designers must ensure the combustion chamber volume matches the flame length and heat release rate, both of which are affected by:
Fuel CV: Lower CV → larger volume needed
Air ratio: Excess air → longer flame, higher flue volume
Burner Design and Control System
Efficient combustion systems rely on:
Modulating burners matched to fuel CV
Accurate air-fuel ratio control using:
Mass flow meters
O₂ sensors
Variable frequency drives (VFDs) for fans
Case Example: Biogas Conversion Challenges
A wastewater treatment plant retrofitted a 4-ton/hr boiler to run on biogas. Due to biogas’s low and variable CV:
Burner was redesigned with wider flame stability range
Air-fuel controller installed with CV feedback loop
Combustion chamber lengthened to ensure complete burn
The result:
15% efficiency drop compared to natural gas baseline
However, net operating cost was 40% lower due to on-site fuel use
Final Thoughts
Both calorific value and combustion air ratio play decisive roles in boiler sizing and thermal efficiency. Calorific value determines how much heat can be extracted per unit of fuel and affects everything from burner sizing to heat exchanger area. Meanwhile, the combustion air ratio governs how efficiently this energy is used, with excessive air leading to significant heat losses. Mastering these parameters is essential not only for technical optimization but also for sustainable energy use and compliance with environmental standards.

Why Is Burner Compatibility Critical for Different Gas Fuels?
When industries switch between gas fuels or design systems for multi-fuel flexibility, burner compatibility is often underestimated—leading to serious safety risks, poor combustion, low thermal efficiency, and even equipment failure. Each gas fuel has unique physical and chemical characteristics that influence how it burns, such as flame speed, calorific value, and air requirements. Using a burner not designed for the specific gas type can result in unstable flames, carbon monoxide formation, or overloading of combustion components. The solution lies in choosing or modifying burners to precisely match the fuel characteristics. This article unpacks why burner compatibility is so critical when dealing with different gas fuels.
Burner compatibility is critical because each gas fuel has distinct combustion properties—including flame speed, calorific value, ignition temperature, and air-to-fuel ratio—that must match the burner’s design. Mismatched burners can lead to unstable combustion, incomplete fuel burn, dangerous emissions like CO, and system inefficiencies. Therefore, burner selection or modification must align precisely with the physical and chemical profile of the intended fuel gas.
Understanding burner compatibility allows engineers and facility operators to safely switch fuels, optimize combustion, and reduce operational costs. Let’s explore the technical reasons and practical consequences of matching burners to specific gas fuels.
A burner designed for natural gas can be used safely with LPG without modification.False
LPG has a significantly higher calorific value and different combustion properties than natural gas, requiring nozzle and pressure adjustments or burner redesign for safe and efficient operation.
How Gas Fuel Properties Affect Burner Design
Each type of gas fuel interacts uniquely with combustion components. Key parameters that influence burner compatibility include:
Property | Natural Gas | LPG | Biogas | Syngas |
---|---|---|---|---|
Calorific Value (MJ/m³) | 38–42 | 93–100 | 20–25 | 10–20 |
Flame Speed (m/s) | Moderate | Fast | Slow | Variable (low–med) |
Stoichiometric Air Ratio | ~10:1 | ~24:1 | ~6:1 | ~1–2:1 |
Ignition Temp (°C) | ~600 | ~470 | ~650 | 500–700 |
Moisture/CO₂ Content | Low | Low | High | Medium |
These differences demand specific burner characteristics:
Orifice size
Air mixing method (premix vs. nozzle mix)
Turbulence control
Flame stabilization technique
Control system tuning
If not adjusted, the burner may fail to ignite, experience flame lift-off, or produce excess emissions.
Burner-Fuel Compatibility Matrix
Fuel Gas | Standard NG Burner | Modified NG Burner | Dedicated Burner Required | Why? |
---|---|---|---|---|
Natural Gas | ✅ | — | — | Designed match |
LPG | ❌ | ✅ | Optional | Requires orifice & pressure mods |
Biogas | ❌ | ❌ | ✅ | High CO₂, low CV needs custom burner |
Syngas | ❌ | ❌ | ✅ | Highly variable composition |
Hydrogen | ❌ | ❌ | ✅ | Ultra-fast flame speed |
Important Note: Even if fuels seem similar, such as natural gas and LPG, they differ significantly in CV and density, requiring dedicated adjustments in burner pressure settings and mixing orifice geometry.
Key Burner Design Parameters Influenced by Fuel
Flame Stabilization
Burners must create a stable flame envelope to prevent flame lift-off or flashback. Fuels like LPG and hydrogen with high flame speeds require flame arrestors and high-velocity ports to control flame travel.
Mixing and Combustion Air Control
Different fuels need different air-fuel premix strategies:
Biogas and syngas require low excess air and recirculation support to maintain flame temperature.
LPG and natural gas demand precise venturi or nozzle mixing to avoid incomplete combustion.
Fuel | Air-Fuel Mixing Strategy | Air Control Complexity |
---|---|---|
Natural Gas | Venturi premix or nozzle mix | Medium |
LPG | Venturi with adjusted jets | High (due to volatility) |
Biogas | Nozzle mix, staged air | Very High |
Syngas | Nozzle mix with dynamic control | Extreme (real-time adaptation) |
Burner Material and Construction
Some gas fuels (e.g., biogas, syngas) contain corrosive compounds like H₂S, CO₂, or NH₃, which corrode metal parts:
Stainless steel burners may be required
Ceramic coatings or gas pre-treatment is advised
Consequences of Incompatible Burner Use
Problem | Resulting Impact |
---|---|
Flame instability | Blow-off, flashback, burner damage |
Incomplete combustion | High CO, soot, low thermal efficiency |
Overheating of burner surface | Burner deformation, premature failure |
Incorrect air-fuel ratio | Low flame temp, excessive flue loss |
Poor ignition reliability | Shutdowns, safety risks |
Case Study Example: LPG in Natural Gas Burner
A facility in Turkey attempted to run LPG on an unmodified NG burner. The result:
Burner tip overheated due to higher flame temp
Flame lifted from the burner mouth
Excess CO detected in exhaust
System required emergency retrofit with smaller jets and regulator change
The cost of repair exceeded $25,000 including downtime.
Key Burner Design Types and Fuel Suitability
Burner Type | Best Fuel Matches | Notes |
---|---|---|
Premix Burner | NG, LPG (with mods) | Excellent flame control, sensitive to pressure |
Nozzle Mix Burner | Biogas, syngas, mixed gas | Good for variable CV and staged combustion |
Dual-Fuel Burner | NG/LPG or NG/Oil | Requires auto-switching systems |
Flare/Low CV Burners | Biogas, landfill, syngas | High tolerance for impurities, low flame speed |
Hydrogen Burner | Hydrogen, NG blends | Must prevent flashback and need special materials |
Modern Solutions for Multi-Fuel Compatibility
To safely operate with different gas fuels, burners must feature:
Adaptive air-fuel ratio control
Flame ionization sensors
Oxygen trim systems
Modular orifice kits
Dual manifold systems
Manufacturers now offer smart burners with:
Integrated calorific value sensors
Real-time fuel composition adjustment
Cloud-based burner performance monitoring
These ensure safe switching and consistent performance across multiple fuels.
Summary
Burner compatibility is essential for reliable, efficient, and safe combustion in gas-fired boilers. Because each fuel type exhibits distinct energy content, density, ignition behavior, and air requirements, burner designs must be carefully matched or modified to accommodate these properties. Failing to do so not only compromises performance but also introduces serious safety and maintenance issues. Whether you’re switching fuels or designing for multi-fuel flexibility, understanding burner-gas interaction is non-negotiable for long-term operational success.

How Do Fuel Impurities and Moisture Content Impact Combustion Performance?
In industrial combustion systems, even a seemingly small level of fuel impurity or moisture can wreak havoc on performance, emissions, and equipment lifespan. Fuel impurities such as sulfur, chlorine, and siloxanes, along with high moisture content, often lead to incomplete combustion, corrosion, scaling, and increased fuel consumption. Many operators fail to consider these factors during fuel procurement or boiler design, leading to unplanned maintenance, emissions violations, and lower thermal efficiency. To avoid these pitfalls, it is essential to understand how fuel quality, particularly impurity levels and moisture content, directly influences combustion dynamics and system reliability.
Fuel impurities and moisture content significantly reduce combustion performance by lowering flame temperature, increasing unburned hydrocarbons and CO emissions, and accelerating corrosion and fouling in heat exchangers. Moisture absorbs latent heat during vaporization, reducing overall energy output, while impurities like sulfur and chlorine form corrosive compounds that damage boiler internals. Clean, dry fuel is crucial for efficient and stable combustion.
These issues are especially relevant in boilers using non-traditional or renewable fuels like biogas, syngas, or waste-derived gases. Let’s dive deep into the physics and chemistry behind how fuel quality affects combustion performance.
High moisture content in fuel improves combustion efficiency by reducing flame temperature.False
Moisture in fuel absorbs significant heat during vaporization, lowering flame temperature and reducing combustion efficiency.
Chemical and Physical Impacts of Fuel Moisture
H3: How Moisture Affects Combustion Energy Balance
Moisture in fuel does not contribute to combustion but instead absorbs heat during vaporization (enthalpy of vaporization ~2,260 kJ/kg for water). This process pulls energy from the flame zone, reducing overall thermal efficiency.
Parameter | Dry Fuel | Fuel with 20% Moisture |
---|---|---|
Calorific Value (CV) | 38 MJ/m³ | ~30 MJ/m³ |
Flame Temperature (°C) | 1,950 | ~1,780 |
Combustion Efficiency (%) | 90–92 | 75–85 |
This means the boiler must burn more fuel to achieve the same heat output, increasing operational costs.
H3: Real Case – Moist Biogas Effect
A paper mill using biogas with ~10% water vapor noted:
12% drop in flame temperature
8% increase in fuel flow rate
Fluctuating flame stability
Solution: A gas dehydration skid using condensation and membrane separation improved flame stability and reduced gas usage by 10%.
Impact of Fuel Impurities on Combustion and Equipment
Fuel impurities vary depending on fuel type. Here’s a summary of common impurities and their combustion impacts:
Impurity | Common Source | Combustion Impact | Resulting Problem |
---|---|---|---|
H₂S | Biogas, landfill gas | Converts to SO₂, reacts with water to form sulfuric acid | Corrosion, acid dewpoint issues |
Siloxanes | Waste gas, landfill | Form silicon dioxide on hot surfaces | Abrasive deposits on burners/turbines |
Chlorine | Waste gas, PVC-derived | Converts to HCl, corrosive to stainless steel | Rapid corrosion, toxic emissions |
Dust/Particulates | Biomass syngas | Do not burn, collect on boiler surfaces | Fouling, poor heat transfer |
Tar | Low-temp gasification | Incomplete combustion, clogs nozzles | Burner fouling, instability |
Siloxane impurities in biogas can damage burner nozzles and heat exchangers.True
Siloxanes form hard silicon dioxide deposits when combusted, causing abrasive damage to metal surfaces and impairing heat transfer.
Impact on Burner and Combustion Control
Burners must maintain a stable flame and correct stoichiometric ratio, but impurities can:
Alter flame ionization → Misleading flame detection
Increase NOx and CO → Fail emissions compliance
Cause deposit buildup → Distorted flame patterns and backpressure
Burner Effect | Cause | Mitigation Strategy |
---|---|---|
Flame Lift/Blow-off | Low CV from moisture | Pre-drying, preheating fuel |
Burner Tip Clogging | Tar, particulates | Cyclone separators, filters |
Flame Instability | Variable CV, siloxanes | Real-time CV monitoring, adaptive controls |
High CO Formation | H₂S, insufficient air mix | Secondary air injection, precise control loops |
Heat Exchanger and Boiler Tube Impacts
Impurities also damage downstream equipment:
Component | Impurity Effect | Failure Mode |
---|---|---|
Superheater Tubes | HCl, SO₂, alkali salts | Pitting, thinning, creep |
Economizers | Dust, sulfur compounds | Plugging, acid corrosion |
Air Preheaters | Condensable moisture and chlorides | Corrosion under deposit |
Condensers | HCl and H₂SO₄ condensation | Acid dew point corrosion |
Example: In a syngas-fired CHP plant, failure of superheater tubes was traced to vanadium-sodium chloride deposits forming a low-melting eutectic, causing localized overheating.
Moisture & Impurity Tolerance by Fuel Type
Fuel Type | Moisture Tolerance | Impurity Sensitivity | Required Pre-treatment |
---|---|---|---|
Natural Gas | Very Low | Very Low | Minimal (dry pipeline-grade) |
LPG | Low | Low | None |
Biogas | High | High (H₂S, siloxanes) | Scrubbing, drying, filtration |
Syngas | Medium | Very High (tars, Cl) | Cooling, tar cracking, acid gas removal |
Landfill Gas | High | Very High (siloxanes, H₂S) | Activated carbon, dehydration |
Key Equipment for Fuel Treatment
To mitigate the effects of impurities and moisture, modern boiler systems integrate:
Gas scrubbers: Remove H₂S, NH₃
Chillers and condensers: Reduce moisture
Siloxane adsorbers: Protect turbines and burners
Particulate filters: Prevent clogging and fouling
Tar reformers: Gasify heavy hydrocarbons in syngas
These systems not only improve combustion performance but also extend equipment life and reduce downtime.
Summary
Moisture and fuel impurities significantly degrade combustion performance, reduce efficiency, and increase maintenance costs in industrial gas-fired boilers. Moisture absorbs energy without contributing to combustion, while impurities form corrosive, toxic, or abrasive by-products that damage equipment and increase emissions. Advanced fuel treatment systems and burner adaptation are essential for stable, clean, and cost-effective operation—especially when using biogas, syngas, or other low-grade fuels. Understanding and managing these contaminants ensures long-term reliability and high combustion efficiency.
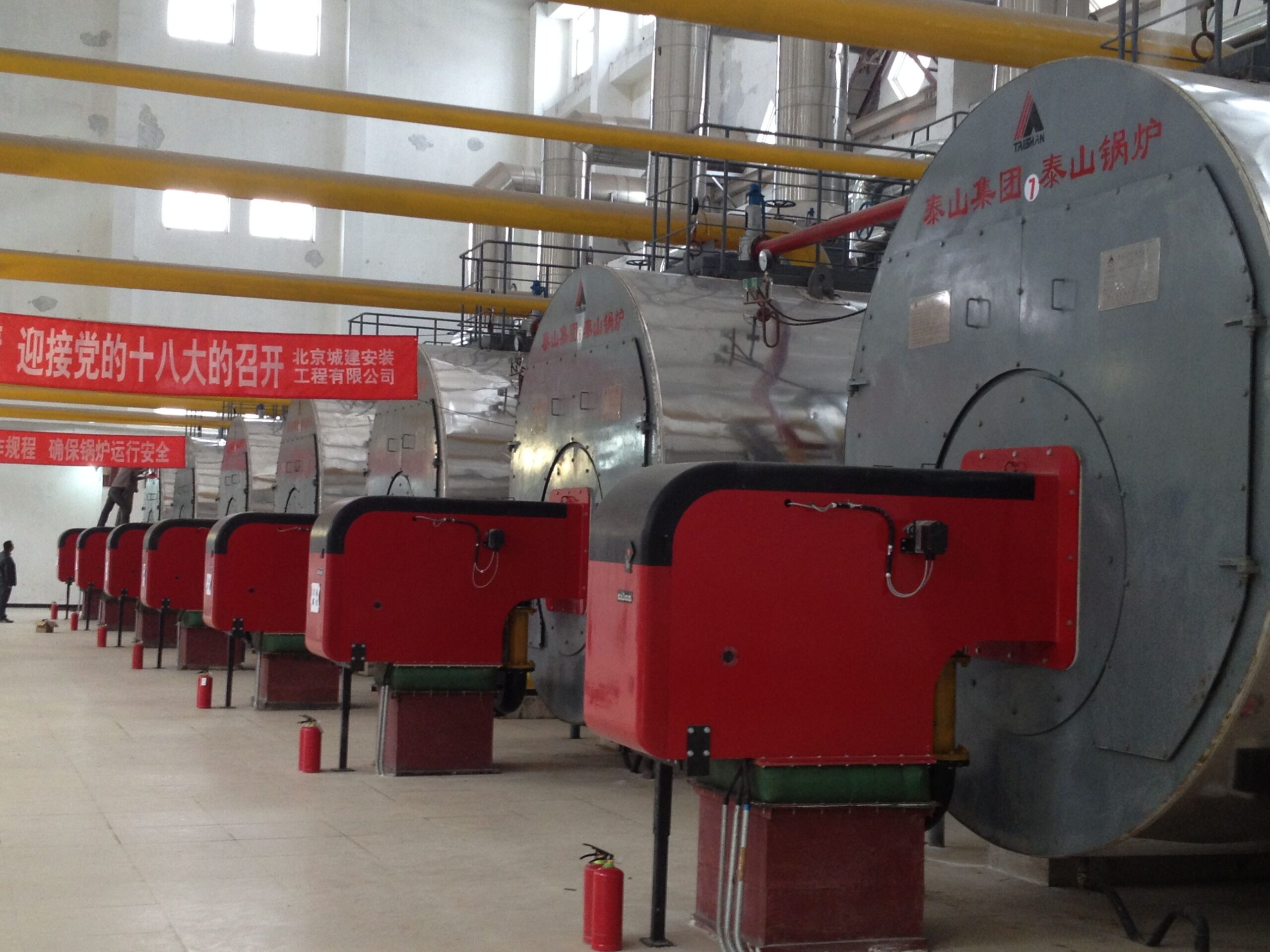
What Emissions Control Systems Are Needed for Various Gas Types?
Industrial gas-fired boilers must comply with strict air emission regulations that vary by region and fuel type. Yet many facilities underestimate the importance of customizing emissions control systems based on the specific gas used. Emissions such as nitrogen oxides (NOx), carbon monoxide (CO), sulfur oxides (SOx), particulate matter (PM), and volatile organic compounds (VOCs) are highly dependent on fuel composition, combustion temperature, and burner design. Without appropriate control systems, emissions can easily exceed legal limits, exposing businesses to fines, shutdowns, and environmental harm. Understanding which emission control technologies to use for each fuel gas type is essential for regulatory compliance and sustainable operation.
Different gas fuels produce distinct emissions profiles requiring specific control systems. Natural gas requires low-NOx burners and selective catalytic reduction (SCR) for NOx; LPG needs similar NOx controls but typically doesn’t require sulfur or particulate controls. Biogas and syngas, on the other hand, often require desulfurization systems, particulate filters, and activated carbon for VOCs and siloxanes. Matching control technologies to the combustion byproducts of each gas is critical for clean, compliant, and efficient operation.
Let’s examine in detail how emissions vary with fuel type and the required emissions control strategies for each, backed by technical insights and system design data.
Natural gas combustion typically requires desulfurization equipment to reduce SO₂ emissions.False
Natural gas contains negligible sulfur, so SO₂ emissions are minimal, and desulfurization is generally not needed.
Fuel-Specific Emissions Profile and Required Controls
Each fuel type has unique chemical properties that influence its emission output. The table below summarizes typical pollutants and the required control technologies for each gas:
Gas Type | Main Pollutants | Control Systems Required |
---|---|---|
Natural Gas | NOx, CO | Low-NOx burner, Flue gas recirculation (FGR), SCR |
LPG | NOx, CO | Low-NOx burner, combustion tuning |
Biogas | NOx, CO, H₂S, siloxanes | SCR/SNCR, Desulfurization, Activated carbon, Filters |
Syngas | NOx, CO, tars, PM, HCl | Wet scrubbers, Baghouse filters, SCR, Acid gas removal |
Landfill Gas | H₂S, siloxanes, VOCs | Activated carbon, Biological scrubbers, Pre-filtering |
Hydrogen | NOx (from high flame temp) | Ultralow-NOx burners, FGR, staged combustion |
Emissions Control Systems – Technical Overview
H3: NOx Control Systems
NOx (nitrogen oxides) are produced due to high flame temperatures. Control technologies include:
Technology | Description | Best For |
---|---|---|
Low-NOx Burners | Burners that limit flame temperature or stage air/fuel | NG, LPG, Biogas |
Flue Gas Recirculation (FGR) | Recirculates cooled flue gas to reduce flame temp | NG, hydrogen |
Selective Catalytic Reduction (SCR) | Uses ammonia/urea and catalyst to convert NOx to N₂ and H₂O | All high-NOx fuels |
Selective Non-Catalytic Reduction (SNCR) | Direct urea/ammonia injection at 850–1100°C | Smaller-scale biogas, syngas |
Case Study: A brewery using biogas saw a 40% NOx reduction after installing an SCR system combined with low-NOx burners, maintaining emissions at 15 ppm.
H3: SOx and H₂S Control Systems
SOx emissions originate from sulfur compounds like H₂S, common in biogas and landfill gas.
Technology | Function | Fuel Application |
---|---|---|
Gas Scrubbers (chemical) | Absorb H₂S in caustic soda or iron sponge | Biogas, landfill gas |
Biological Desulfurization | Uses bacteria to oxidize H₂S | Biogas, cost-effective |
Claus Process | Industrial-scale sulfur recovery | Large-scale syngas plants |
Biogas with high H₂S content requires desulfurization before combustion.True
Combusting biogas with high H₂S without treatment produces corrosive SO₂ and damages heat exchangers and flues.
H3: CO and VOC Control Systems
Incomplete combustion produces CO and VOCs, which require proper air-fuel ratio management and sometimes post-combustion treatments.
Control Method | Description | Best For |
---|---|---|
Combustion Tuning | Precise control of air-to-fuel ratio | All fuels |
Catalytic Oxidizers | Oxidize CO and VOCs at lower temps using catalyst | Biogas, landfill |
Thermal Oxidizers | Burn VOCs at high temps with excess air | High-VOC syngas streams |
H3: Particulate and Tar Control Systems
Tar and PM originate mainly from low-grade syngas and biomass gas.
System | Function | Fuel Application |
---|---|---|
Cyclone Separators | Remove large particles | Syngas, biomass |
Baghouse Filters | Trap fine particulates using filter media | High-dust syngas |
Wet Scrubbers | Capture PM and dissolve soluble gases | Syngas, acid gases |
Electrostatic Precipitators | Electrically charge and collect PM | Large-scale syngas |
Example: A gasification plant installed both a cyclone and a baghouse filter to reduce PM to <10 mg/Nm³, achieving EU air quality compliance.
H3: Siloxane Control Systems
Siloxanes are unique to landfill and sewage gas. When burned, they form abrasive SiO₂ deposits on turbines and heat exchangers.
Control System | Function | Fuel Source |
---|---|---|
Activated Carbon | Adsorbs siloxanes and VOCs | Biogas, landfill gas |
Chilled Condensation Units | Cool gas to condense and remove moisture/siloxanes | Biogas |
Silica Gel Beds | Targeted siloxane capture | High-siloxane environments |
Comparison Chart: Emissions vs Control Needs by Gas Type
Gas Type | NOx Control | SOx/H₂S Control | CO/VOC Control | PM/Tar Control | Siloxane Control |
---|---|---|---|---|---|
Natural Gas | Low-NOx burner, SCR | Not needed | Air-fuel tuning | Not needed | Not needed |
LPG | Low-NOx burner | Not needed | Tuning | Not needed | Not needed |
Biogas | SCR, SNCR | Chemical scrubber | Catalytic oxidizer | Minimal | Activated carbon |
Syngas | SCR, FGR | Wet scrubber | Thermal oxidizer | Baghouse/wet scrubber | Not needed |
Landfill Gas | SNCR | Biological scrubber | Catalytic oxidizer | Minimal | Carbon + chillers |
Hydrogen | FGR, staged burner | Not needed | Tuning | Not needed | Not needed |
Control Integration and System Design Considerations
Industrial boiler designers must incorporate emissions controls into both upstream fuel processing and downstream flue gas treatment, considering:
Fuel variability (e.g., biogas CV or impurity changes)
System scalability
Cost vs. compliance trade-off
Integration with burner and control systems
Real-time monitoring (O₂ sensors, stack analyzers)
Modern control systems include:
PLC/SCADA for emissions tracking
Auto-tuning burners
Continuous Emissions Monitoring Systems (CEMS) for reporting compliance
Summary
Selecting appropriate emissions control systems for various gas fuels is essential for environmental compliance, equipment protection, and sustainable operations. While natural gas needs only minimal controls for NOx and CO, fuels like biogas, syngas, and landfill gas demand comprehensive solutions including desulfurization, particulate removal, VOC oxidation, and siloxane capture. A one-size-fits-all approach doesn’t work. Instead, emissions control must be customized to the unique combustion profile of each gas type, integrated into the combustion system, and continually monitored for optimal performance.
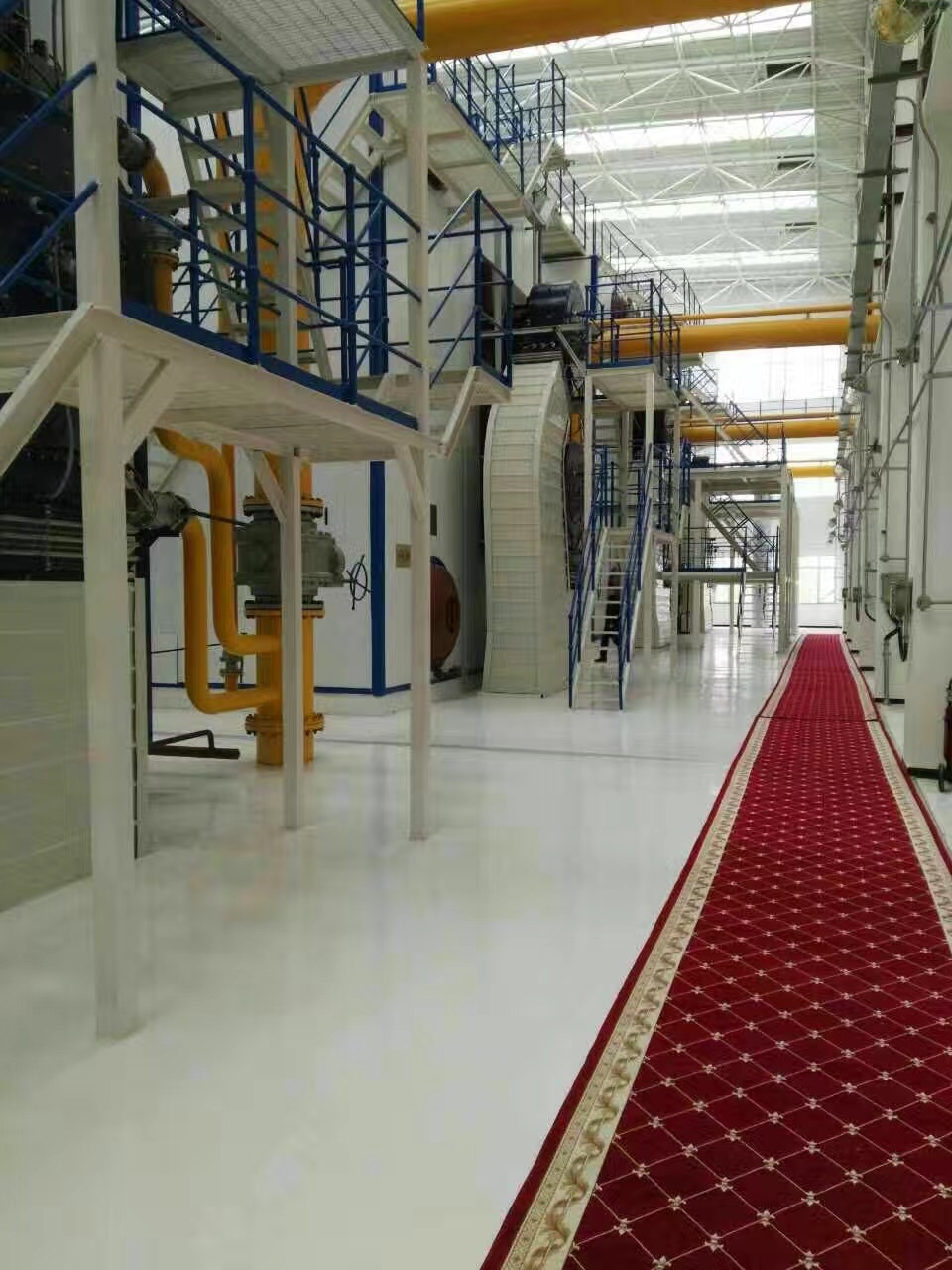
How Can Hydrogen or Biogas Integration Impact Future Boiler Design and Retrofits?
As industries shift toward carbon neutrality and energy decentralization, integrating hydrogen and biogas into boiler systems is becoming a necessity rather than a choice. However, these renewable fuels present unique combustion characteristics and engineering challenges that make conventional boiler systems unsuitable without redesign or retrofit. Failure to adapt boilers to the specific demands of hydrogen’s high flame speed or biogas’s moisture and impurity levels can lead to inefficiencies, safety risks, and non-compliance with emissions regulations. The solution lies in proactively reengineering both new and existing boilers to accommodate these low-carbon fuels—creating a future-ready, adaptable heating infrastructure.
Integrating hydrogen or biogas into boiler systems impacts design and retrofit requirements by necessitating burner modifications, combustion control upgrades, fuel conditioning systems, and material changes to withstand new thermal and chemical environments. Hydrogen’s fast flame speed demands flashback prevention and precise air-fuel control, while biogas integration requires impurity removal and moisture management. Designing or retrofitting for these fuels enhances sustainability but involves significant reengineering of core combustion and safety systems.
Industrial users, OEMs, and energy strategists must understand these engineering implications to transition boilers toward clean fuels without compromising safety, performance, or operational reliability. Read on for in-depth design principles, retrofit strategies, and real-world deployment examples.
Hydrogen and biogas can be used in conventional natural gas boilers without any modification.False
Both hydrogen and biogas have combustion properties that differ significantly from natural gas, requiring specific burner designs, control systems, and sometimes material upgrades for safe and efficient use.
Engineering Challenges in Hydrogen and Biogas Combustion
H3: Hydrogen’s Combustion Behavior and Design Needs
Hydrogen is a high-energy, carbon-free fuel with unique combustion traits:
Property | Hydrogen | Impact on Boiler Design |
---|---|---|
Flame Speed | ~2.9 m/s (very fast) | Requires anti-flashback burner design |
Ignition Energy | 0.02 mJ (very low) | Needs robust flame detection and isolation |
Flame Temperature | ~2,000–2,100°C | High-temperature-resistant materials needed |
Density | ~0.089 kg/m³ (low) | Higher flow rates and new valve sizing |
NOx Formation Tendency | Very high | Demands staged combustion or FGR |
Design Response:
Use special flame arrestor mesh in burners
Implement multi-stage combustion
Apply flue gas recirculation (FGR) for NOx control
Upgrade safety systems: double block valves, hydrogen leak detection
H3: Biogas Combustion Characteristics and Design Needs
Biogas is a variable, low-CV fuel with high moisture and impurities:
Property | Biogas | Design Impact |
---|---|---|
Calorific Value (CV) | ~20–25 MJ/m³ | Larger burner size, longer combustion chamber |
CO₂ Content | 30–50% | Reduces flame stability, needs air-fuel tuning |
Moisture | High | Corrosion risk, affects flame temperature |
H₂S and Siloxanes | Often present | Requires pre-treatment and material resistance |
Design Response:
Install gas scrubbers and chillers
Use oxidation-resistant alloys for wetted parts
Integrate advanced air-fuel ratio control
Opt for dual-fuel or biogas-specialized burners
Boiler Retrofit Strategies for Hydrogen & Biogas
Key Components That Must Be Retrofitted or Replaced
Boiler Component | Hydrogen Retrofit | Biogas Retrofit |
---|---|---|
Burner | Anti-flashback, staged design | Large flame stabilizer, impurity-resistant |
Fuel Valves & Manifold | Hydrogen-rated, leak-proof | Corrosion-resistant, moisture handling |
Control System | Real-time lambda and flame sensors | CV sensor and adaptive combustion tuning |
Flame Detection | Ionization probe, UV/IR sensor | Moisture-tolerant, responsive detection |
Piping | Seamless steel or stainless (hydrogen-ready) | Rust-resistant or plastic-lined steel |
Heat Exchanger | High-temp alloys for hydrogen’s hotter flame | Anti-scaling design for siloxane removal |
Retrofit Timeframe:
Light retrofits (e.g., biogas pre-cleaned): ~2–3 weeks
Full dual-fuel conversion: ~6–8 weeks
Hydrogen-ready conversion: ~3–4 months due to safety testing and compliance
Cost Comparison: Retrofit vs. New Design
Integration Strategy | Estimated Cost (USD) | Best Fit For |
---|---|---|
Biogas retrofit (light) | $20,000–$60,000 | Farms, WWTPs, food industries |
Hydrogen-ready boiler retrofit | $100,000–$250,000 | District heat, refineries, chemicals |
New dual-fuel boiler system | $200,000–$500,000+ | Long-term industrial or institutional |
Advanced Control Systems for Mixed Fuel Combustion
Hydrogen and biogas demand adaptive combustion controls for safety and efficiency:
System Feature | Function |
---|---|
Fuel CV Sensor | Detects biogas quality in real time |
Oxygen Trim Controller | Optimizes excess air |
Mass Flow Meters | Maintain correct fuel-air ratio |
Modulating Burner Control | Adjusts flame shape and intensity |
Safety PLC + Flame Relay | Reacts quickly to flashback or flame loss |
Hydrogen-specific addition: Double containment sensors, high-speed shutdown solenoids, and leak-proof interlocks.
Real-World Use Cases: Biogas and Hydrogen Boiler Integration
Case Study 1: Biogas Retrofit in a Brewery
Location: Germany
System: 6-ton/hr steam boiler
Action: Retrofit to use anaerobic digester biogas
Upgrades: Activated carbon filter, burner change, CV sensor
Result:
40% reduction in natural gas use
Payback in 18 months
Emissions reduced by 35%
Case Study 2: Hydrogen Co-Firing at Chemical Plant
Location: Netherlands
System: 10 MW steam boiler retrofitted for 30% hydrogen blend
Actions: Installed hydrogen-compatible burner, added UV flame scanner
Challenges: NOx increased initially, corrected with FGR
Result:
Smooth fuel transition
18% reduction in CO₂ emissions
Fully scalable to 100% hydrogen
Future-Proof Boiler Design Principles
H3: Key Principles for Hydrogen/Biogas-Ready Boilers
Fuel Flexibility: Dual-fuel burners with swappable jets and variable control systems
Emission Compliance: Built-in FGR, SCR, and desulfurization readiness
Safety First: Integrated gas detectors, double-walled piping, and smart shut-off logic
Modular Design: Replaceable burner heads, pluggable sensor arrays, and expandable control units
Digitalization: Remote diagnostics, AI-predictive tuning, and cloud emissions reporting
Summary
The integration of hydrogen and biogas into industrial boiler systems is reshaping how we approach combustion engineering. Hydrogen demands precision, speed, and thermal resilience, while biogas introduces variability, moisture, and chemical complexity. Retrofitting existing boilers or designing new ones to accommodate these fuels requires significant adjustments to burners, control systems, fuel handling, and safety infrastructure. However, these efforts are critical investments toward carbon neutrality, regulatory compliance, and long-term energy flexibility. Embracing these innovations now positions industries for a cleaner, more resilient future.
🔍 Conclusion
Fuel type is not just a supply issue—it’s a fundamental factor in how your industrial gas-fired boiler performs, operates, and complies with environmental regulations. By understanding the specific combustion characteristics of your fuel, you can select or customize a boiler that ensures optimum energy efficiency, flame stability, and minimal emissions. The right fuel-boiler match reduces costs, enhances safety, and prepares your system for future energy shifts.
📞 Contact Us
💡 Need help evaluating fuel compatibility for your gas-fired boiler system? Our team of experts offers custom engineering consultations and fuel-flexible boiler solutions tailored to your industrial needs.
🔹 Talk to us today to ensure your boiler system is engineered for performance and fuel adaptability! 🔥🔧✅
FAQ
How do fuel gas types impact the selection of a gas-fired boiler?
The choice between natural gas, liquefied petroleum gas (LPG), or biogas affects burner design, combustion control, pressure regulation, and piping. Each fuel has unique energy content, flame speed, and combustion behavior that must be matched with boiler specifications.
What are the key combustion characteristics of gaseous fuels?
Gaseous fuels vary in calorific value, ignition temperature, flame stability, and emissions profile. Natural gas burns cleanly with high efficiency, while LPG provides higher energy per unit but requires precise air-fuel control to avoid soot or NOx formation.
Why is burner compatibility critical in gas-fired boiler systems?
Burners must be calibrated to the specific gas type’s pressure and flow rate. Using an incompatible burner can lead to flame instability, incomplete combustion, or hazardous conditions. Dual-fuel or modulating burners may offer more flexibility.
How do impurities or variations in gas composition affect boiler performance?
Impurities such as hydrogen sulfide, moisture, or siloxanes (common in biogas) can corrode components, reduce thermal efficiency, or clog burner nozzles. Monitoring gas quality is vital for maintaining system integrity and reducing maintenance costs.
Can gas-fired boilers handle multiple gas types or switching?
Yes, some industrial gas-fired boilers are designed to operate on multiple gas types (e.g., natural gas and LPG) with the help of dual-fuel burners and adaptive control systems. This offers fuel flexibility, cost management, and supply security.
References
Types of Gaseous Fuels for Boilers – https://www.energy.gov
Combustion Characteristics of Natural Gas and LPG – https://www.sciencedirect.com
Gas Burner Design and Efficiency – https://www.researchgate.net
Effect of Gas Quality on Boiler Operation – https://www.epa.gov
Natural Gas vs LPG in Industrial Boilers – https://www.bioenergyconsult.com
Fuel Flexibility in Gas-Fired Systems – https://www.mdpi.com
Boiler System Optimization with Fuel Switching – https://www.energysavingtrust.org.uk
Biogas Use in Industrial Boilers – https://www.iea.org
Automation and Control in Gas Boilers – https://www.automation.com
Impact of Fuel Variability on Combustion – https://www.sciencedirect.com
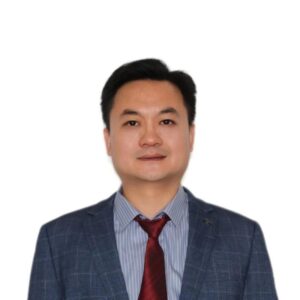