Choosing the right capacity and size of an industrial biomass boiler is critical to ensuring operational efficiency, fuel optimization, and long-term cost-effectiveness. Many industrial buyers either oversize their boilers—leading to wasted fuel, underutilization, and higher capital costs—or undersize them, resulting in inadequate heat supply, frequent cycling, and operational instability. To avoid these pitfalls, it’s essential to match boiler size precisely with your facility’s process heat or steam demands, fuel type, and load variability.
The capacity and size of an industrial biomass boiler depend on factors such as your thermal load (measured in kg/h, MW, or BTU/hr), type and calorific value of biomass fuel, system efficiency, pressure and temperature requirements, and whether the boiler operates under steady or fluctuating loads. Accurate sizing requires a detailed load assessment, including peak and base load demand, fuel moisture content, combustion efficiency, and potential for system expansion. A well-sized biomass boiler maximizes fuel utilization, ensures stable operation, and reduces lifecycle costs.
Let’s explore the key considerations to help you choose the right biomass boiler size for your industrial needs.
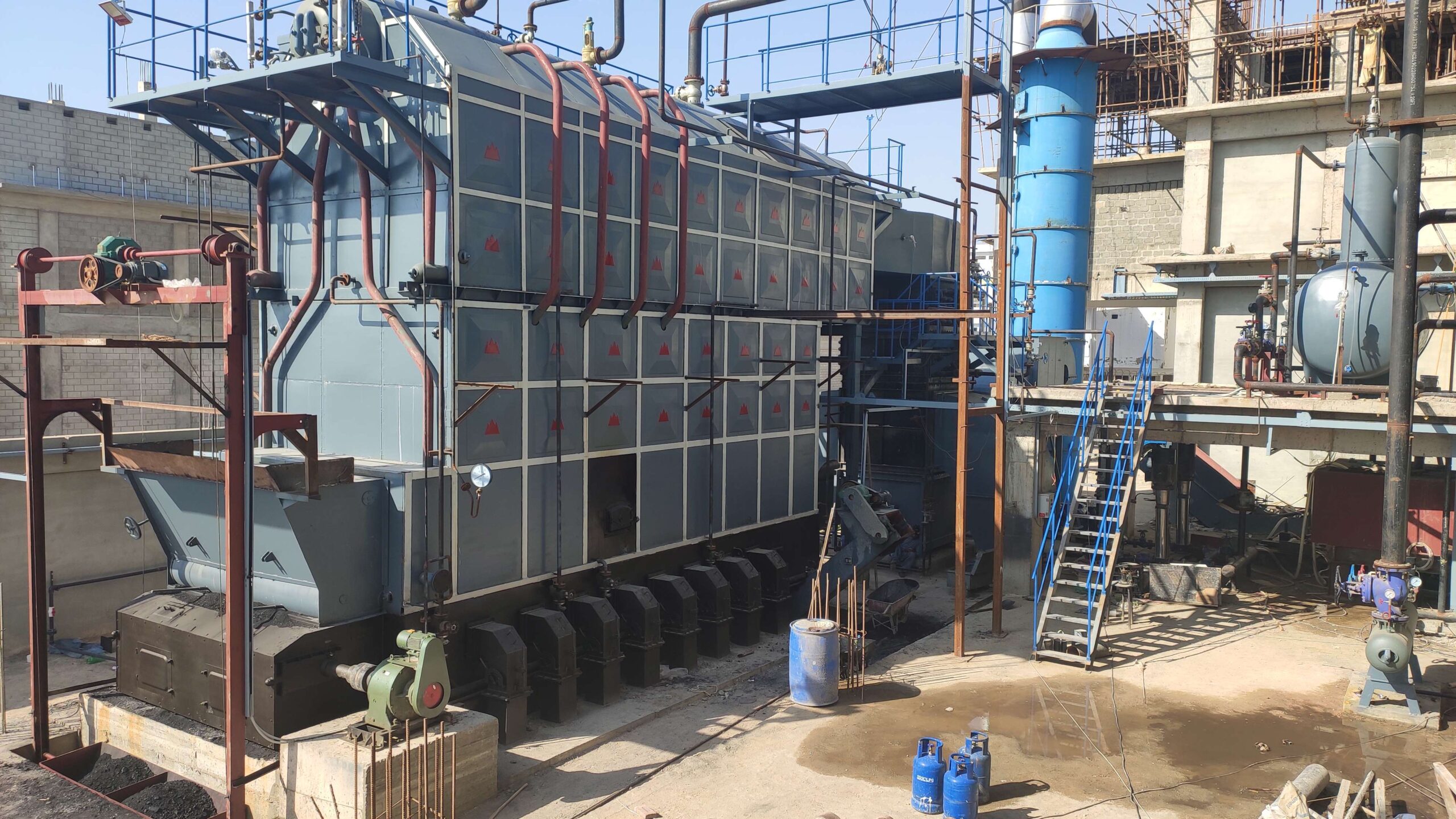
How Do You Calculate Steam or Heat Demand for Biomass Boiler Sizing?
Choosing the right size for a biomass boiler is crucial for system efficiency, reliability, and cost control. Yet, many users face difficulties during the sizing process due to uncertainties in calculating heat or steam demand, especially when multiple systems (heating, hot water, steam processes) are involved. If the demand is underestimated, the boiler cannot keep up, causing production delays. If oversized, it wastes fuel, cycles inefficiently, and increases costs. The good news? You don’t need to rely on overly complex equations to get this right. A structured, step-by-step approach with clear units and smart assumptions can give you an accurate boiler size for your biomass system.
To calculate steam or heat demand for biomass boiler sizing, first identify all heating and steam applications in your facility, estimate their energy requirements in kilowatts (kW) or kilograms per hour (kg/h) of steam, and convert them into a total thermal load. Include average and peak loads, daily operation hours, and allow a buffer margin of 10–15%. Then, select a boiler that covers your base load and use auxiliary support for peak periods.
Accurate load calculation avoids costly errors and improves your return on investment. Here’s how you can do it simply and effectively.
Biomass boiler systems should always be oversized to ensure future scalability.False
Oversizing biomass boilers leads to frequent cycling, poor combustion efficiency, and higher emissions. They should be sized to base load and paired with buffers or auxiliary boilers for peak load.
Step-by-Step Guide: Estimating Thermal Load Without Complex Formulas
Step 1: List All Thermal Demands
Start by identifying everything in your facility that consumes heat or steam. Break it into three main categories:
Category | Examples | Units to Use |
---|---|---|
Space Heating | Radiators, floor heating, air handling units | kW |
Hot Water | Bathrooms, kitchens, CIP systems | Liters/day or kWh |
Process Steam | Food production, laundry, sterilization | kg/h of steam |
Pro tip: For existing systems, use your utility bills or metering data to estimate heating kWh/year or gas consumption.
Step 2: Convert Steam Demand to Heat Load (kW)
If your application involves steam, convert the steam flow (kg/h) to kilowatts using this simple rule:
For saturated steam at around 10 bar pressure:
Each 1 kg/h of steam ≈ 0.65 to 0.70 kW of heat demand
Example:
1,000 kg/h of steam × 0.67 kW ≈ 670 kW heat demand
You can now combine this with other heating needs.
Step 3: Add Up All Heat Loads
System | Estimated Load |
---|---|
Steam sterilizer | 500 kg/h ≈ 335 kW |
Space heating | 250 kW |
Hot water | 80 kW |
Total Base Load | 665 kW |
This is your continuous base demand. If you have peak loads, list those separately, like:
Winter peak heating: +100 kW
Weekend production surge: +200 kW
Plan for these with an auxiliary boiler or buffer tank.
Step 4: Determine the Boiler Size Based on Load Duration
Biomass boilers perform best at steady, high loads. Use the base load to size your boiler. Cover peak loads with:
An oil/gas auxiliary boiler
Or a thermal buffer tank to store excess energy
Daily Operation Hours | Boiler Sizing Strategy |
---|---|
24 hrs/day | Size close to total base demand (90–100%) |
8–16 hrs/day | Consider part-load performance and buffering |
Step 5: Choose the Biomass Boiler Capacity
Based on your total base load:
Heat Load Range | Recommended Boiler Size |
---|---|
100–250 kW | 150–200 kW |
250–500 kW | 300–400 kW |
500–1,000 kW | 600–800 kW |
Over 1,000 kW | Modular or custom system |
Add 10–15% safety margin, especially if steam quality or pressure varies.
Simplified Steam and Heat Load Conversion Table
Steam Demand (kg/h) | Estimated Heat Load (kW) | Recommended Boiler (kW) |
---|---|---|
300 | ~200 | 220–250 |
500 | ~335 | 350–400 |
1,000 | ~670 | 700–750 |
2,000 | ~1,340 | 1,400–1,500 |
Building Type | Heat Load (kW/m²) |
---|---|
Office (old, uninsulated) | 100–150 |
Office (modern, insulated) | 50–80 |
Factory (heated zones) | 30–60 |
Dairy/food plant (24/7) | 80–120 |
Important Factors to Include in Final Sizing
Fuel type & moisture: Wet wood chips need a larger boiler than dry pellets for same output.
Boiler efficiency: Typically 80–90%, so adjust for thermal losses.
Usage pattern: For intermittent loads, always use a buffer tank.
Maintenance access: Allow room for cleaning if ash is high.
Real-World Example: Food Processing Plant
Steam demand: 1,200 kg/h
Space heating: 300 kW
Domestic hot water: 100 kW
Total base load: ~1,200 kW
Peak load (winter): +200 kW
Selected biomass boiler: 1,250 kW chip-fired
Backup LPG boiler: 300 kW
Buffer tank: 10,000 liters
Payback: 3.2 years due to 50% fuel cost reduction
Summary
You don’t need complex math to size a biomass boiler accurately—just a logical breakdown of your heating and steam needs, smart use of conversion rules, and attention to load patterns. By combining steam demand, space heating, and domestic hot water loads into a unified thermal profile, and converting everything to kW, you can quickly determine the right boiler capacity. Match this to your operational needs and allow for buffers, peak loads, and fuel variability. This ensures your biomass boiler is efficient, responsive, and perfectly suited to your energy demand.
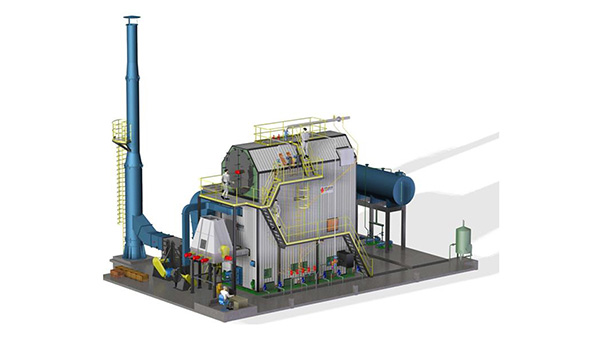
What Role Does Biomass Fuel Type and Calorific Value Play in Capacity Selection?
Choosing the correct capacity for a biomass boiler is not only about estimating your heating or steam demand—it’s also about understanding your biomass fuel’s type and energy content. A common mistake is assuming all biomass fuels are interchangeable or that boiler capacity is a fixed figure. In reality, the calorific value (CV) of your fuel directly affects how much biomass is needed to meet your heat load and thus influences everything from fuel storage to combustion system sizing. Using a low-CV fuel without accounting for its characteristics can result in oversized fuel feeding systems, underperforming boilers, and excessive ash generation. To size your biomass system correctly, the fuel type and energy content must be at the core of your calculations.
Biomass fuel type and calorific value determine how much energy each kilogram or cubic meter of fuel can provide, directly impacting the boiler size, feeding rate, combustion chamber dimensions, and overall efficiency. Fuels with lower calorific value require larger volumes to deliver the same energy output, leading to larger boilers and fuel storage, while high-CV fuels allow smaller, more compact systems. Therefore, capacity selection must be aligned with the specific energy content and characteristics of the chosen biomass fuel.
This relationship is essential for achieving efficiency, reliability, and environmental compliance in biomass boiler systems. Let’s explore how fuel variations influence boiler design, capacity decisions, and operational outcomes.
All biomass fuels provide the same amount of energy per kilogram.False
Different biomass fuels vary significantly in calorific value based on their composition, density, and moisture content. For example, wood pellets offer more energy per kilogram than wet wood chips or straw.
Understanding Calorific Value Differences Between Biomass Fuels
Calorific value (CV), also known as heating value, is the amount of energy released during the combustion of a specific quantity of fuel. For biomass, this is usually measured in megajoules per kilogram (MJ/kg) or kilowatt-hours per kilogram (kWh/kg).
Fuel Type | Moisture Content (%) | Net CV (MJ/kg) | Net CV (kWh/kg) | Remarks |
---|---|---|---|---|
Wood Pellets | 8–10 | 16.5–18 | 4.6–5.0 | High density, low ash |
Dry Wood Chips (≤25%) | 18–25 | 13–15 | 3.6–4.2 | Good efficiency, requires drying |
Wet Wood Chips (40–50%) | 40–50 | 8–10 | 2.2–2.8 | Lower efficiency, more fuel volume |
Straw Bales | 15–20 | 13–15 | 3.6–4.2 | Light, bulky, needs robust feeding |
Miscanthus (Pellets) | 12–15 | 14–15 | 3.9–4.2 | Low ash, suitable for pellet boilers |
Agricultural Waste | 20–50 | 6–14 | 1.7–3.9 | Variable CV, may need pre-treatment |
Fuel Type’s Influence on Boiler Capacity Selection
H3: How CV Impacts Required Fuel Quantity
Boiler capacity must meet the site’s heat or steam demand, but the actual amount of biomass fuel required depends on its calorific value.
Example:
To generate 1,000 kW of heat continuously, how much fuel is required?
Using wood pellets (CV = 5 kWh/kg):
Fuel needed = 1,000 ÷ 5 = 200 kg/hUsing wet wood chips (CV = 2.5 kWh/kg):
Fuel needed = 1,000 ÷ 2.5 = 400 kg/h
So, the same heat output requires twice as much low-CV fuel by weight—affecting:
Fuel storage size
Feeding system speed
Ash handling capacity
Combustion chamber volume
Boilers using low-calorific biomass fuels require higher fuel feeding rates to meet the same energy output.True
Lower energy density fuels must be burned in greater quantities, so the feeding and combustion systems must be scaled accordingly.
Comparison Table: Fuel Impact on System Design
Parameter | High-CV Fuel (e.g., pellets) | Low-CV Fuel (e.g., wet chips, agri-waste) |
---|---|---|
Fuel Feed Rate | Lower | Higher |
Storage Volume Needed | Compact | Large |
Ash Generation | Low | High |
Boiler Sizing | More compact | Larger combustion volume |
Emission Control | Easier to manage | May require extra filtration or scrubbers |
Fuel Handling System | Simpler screw conveyors | Robust augers, agitators, possibly drying |
Biomass Boiler Sizing Chart by Fuel Type and Energy Demand
Thermal Load (kW) | Fuel Type | Boiler Capacity (kW) | Fuel Use (kg/h) |
---|---|---|---|
200 | Wood pellets | 200 | ~40–45 |
200 | Dry wood chips | 200 | ~50–60 |
200 | Wet wood chips | 200 | ~75–90 |
200 | Straw bales | 200 | ~50–70 |
200 | Agri waste (low CV) | 200 | ~80–100 |
Always allow a 10–15% margin for real-world inefficiencies and variations in fuel quality.
Practical Design Adjustments Based on Fuel Type
H3: Boiler and Combustion Chamber
Low-CV fuels need larger combustion chambers for longer residence time and higher air volumes
Pellets allow for compact, highly automated boilers
Combustion control must be adaptive to handle varying CV in waste or mixed fuels
H3: Fuel Storage and Feed Systems
High-volume fuels require larger silos, walking floor systems, or agitated hoppers
Conveyors must be sized based on bulk density and flow rate
Fuel Type | Bulk Density (kg/m³) |
---|---|
Wood Pellets | 650–750 |
Dry Wood Chips | 300–400 |
Wet Wood Chips | 200–300 |
Straw | 100–150 |
Miscanthus | 250–350 |
H3: Ash and Emissions Handling
Fuels with bark, straw, or soil contamination produce more ash
Boilers must include:
Automatic ash removal systems
Cyclones or bag filters for particulates
Scrubbers for agricultural fuel gases
Real-World Example: Municipal District Heating System
Heat demand: 3,000 kW
Original fuel: Dry wood chips (CV ~3.8 kWh/kg)
Switched to straw (CV ~3.5 kWh/kg), but increased ash caused clogs
Upgraded boiler to handle:
Straw bale feed system
Augmented ash handling
Buffer tank added for load smoothing
Result:
20% lower fuel cost
Slight derating of boiler (to 2,800 kW output)
15% increase in ash handling frequency
Summary
Biomass fuel type and calorific value are not just background details—they are central to selecting the correct boiler capacity. High-CV fuels like pellets support compact, efficient systems with lower feeding rates, while low-CV fuels like wet wood or agri-waste require larger combustion volumes, higher feed rates, and more robust emissions and ash management. To avoid inefficiency, high emissions, or costly redesigns, the fuel characteristics must be integrated into every aspect of boiler selection and system design. Understanding the fuel-to-energy relationship helps ensure your biomass boiler performs at its peak while supporting sustainability and cost-effectiveness.
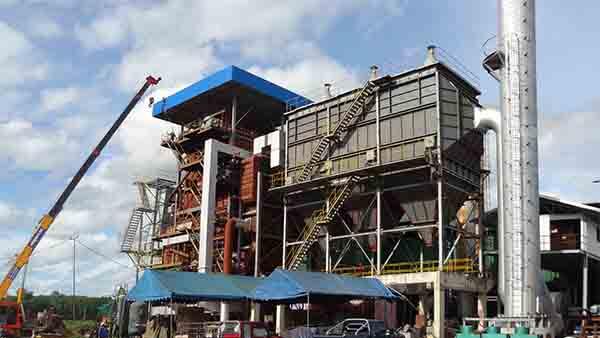
Why Is Combustion Efficiency Critical When Sizing a Biomass Boiler?
When it comes to sizing a biomass boiler, many engineers and facility managers focus on calculating heat or steam demand—but overlook one of the most important design variables: combustion efficiency. If combustion efficiency is overestimated, the boiler will underperform, unable to meet thermal demands. If underestimated, it could lead to over-sizing, fuel waste, and higher upfront costs. Inaccurate assumptions about how efficiently the boiler converts biomass fuel into usable heat can result in performance gaps, excess emissions, and short cycling. Simply put, combustion efficiency is the critical bridge between theoretical fuel energy and actual delivered heat output—and must be factored precisely during boiler sizing.
Combustion efficiency directly impacts biomass boiler sizing because it determines how much of the fuel’s energy is actually converted into usable heat. A boiler with lower combustion efficiency requires more fuel and a higher capacity to meet the same thermal demand, while a highly efficient system allows for smaller, more cost-effective boiler sizing. Therefore, ignoring combustion losses during sizing results in under- or over-dimensioned systems, operational inefficiencies, and increased lifecycle costs.
To ensure accurate boiler capacity selection and optimal system performance, combustion efficiency must be measured, understood, and incorporated into all sizing calculations.
Combustion efficiency has little effect on biomass boiler sizing since fuel energy content is fixed.False
Even if fuel calorific value is fixed, only a portion of it is converted into usable heat. Combustion efficiency determines how much of that energy contributes to actual heating, directly influencing required boiler capacity.
What Is Combustion Efficiency in Biomass Systems?
Combustion efficiency refers to the percentage of energy released by the fuel during combustion that is effectively transferred into usable heat in the boiler.
It is affected by:
Excess air supply
Flue gas temperature
Incomplete combustion (CO, unburned carbon)
Fuel moisture
Ash behavior and turbulence in combustion zone
Parameter | Effect on Efficiency |
---|---|
High moisture content | Lowers flame temperature |
Excess combustion air | Increases stack heat losses |
Incomplete combustion (CO, soot) | Lost unburned energy |
Poor mixing or fuel feed | Causes unstable flame |
Typical combustion efficiencies for biomass boilers range from:
65–75% for basic fixed grate systems using wet wood
80–85% for modern chip-fired or straw boilers with good controls
85–92% for advanced pellet boilers with lambda control and FGR
Efficiency’s Direct Impact on Boiler Sizing
H3: How Efficiency Affects Required Boiler Capacity
If your building or process requires 1,000 kW of thermal energy, and your boiler operates at 85% efficiency, the required input is:
Required boiler input = Heat demand ÷ Efficiency
= 1,000 ÷ 0.85 = 1,176 kW
If the efficiency were only 70%, then:
1,000 ÷ 0.70 = 1,429 kW
That’s a 25% increase in boiler size needed due to efficiency loss.
Efficiency (%) | Required Boiler Size (for 1,000 kW Output) |
---|---|
92% | 1,087 kW |
85% | 1,176 kW |
80% | 1,250 kW |
70% | 1,429 kW |
Higher efficiency = smaller, cheaper, more fuel-efficient boiler.
Boiler Efficiency and Fuel Usage Table
Efficiency (%) | Fuel Required (kg/h) (for 1,000 kW output, CV = 4 kWh/kg) |
---|---|
92% | 272 kg/h |
85% | 294 kg/h |
80% | 313 kg/h |
70% | 357 kg/h |
More efficiency = less fuel = lower OPEX and smaller feeding system.
Boiler systems with higher combustion efficiency require less fuel and smaller combustion chambers for the same output.True
Higher efficiency means more of the fuel’s energy is used for heating, reducing the need for excess fuel volume and large combustion zones.
Common Causes of Low Efficiency in Biomass Combustion
Problem Area | Resulting Impact |
---|---|
Excess air > 100% | Heat lost in flue gas, lower flame temp |
Incomplete burn | High CO, unburned char or fly ash |
Poor fuel quality | High moisture = latent heat loss |
Slagging and clinker buildup | Poor air flow, blocked combustion zones |
Poor feed rate control | Load mismatch, cold-end corrosion |
Efficient systems control these with:
Lambda sensors
Modulating air fans
Optimized fuel feed augers
Real-time O₂ trim and CV monitoring
Combustion Efficiency vs. Boiler Type
Boiler Type | Typical Efficiency Range | Notes |
---|---|---|
Fixed Grate (manual) | 60–75% | Inexpensive, but inconsistent combustion |
Moving Grate (automatic) | 75–85% | Handles chips, requires tuning |
Step Grate + Controls | 80–88% | Good for high-moisture fuels |
Fluidized Bed | 80–90% | High thermal uniformity |
Pellet Boiler (fully modulating) | 88–92% | Best efficiency, low ash, clean burn |
Real-World Example: Effect of Efficiency on Boiler Sizing
Hospital Heating Plant
Heat demand: 1,200 kW
Fuel: wood chips, CV = 3.5 kWh/kg
Option A: 75% efficient boiler → needs 1,600 kW capacity
Option B: 90% efficient boiler → needs only 1,333 kW capacity
Result:
Option B used less fuel, needed smaller silos, fewer feed augers, and 20% less emissions
Payback of high-efficiency system achieved in 2.8 years
Summary
Combustion efficiency isn’t just a performance metric—it’s a design-defining factor in biomass boiler sizing. It governs how much usable heat you can extract from your fuel and determines how big the boiler needs to be to meet demand. Higher efficiency means a smaller boiler, lower fuel costs, fewer emissions, and better ROI. Overlooking this variable leads to oversized or undersized systems, wasted fuel, and operational headaches. Always evaluate real-world combustion efficiency when calculating boiler capacity—it’s the single most important efficiency factor for sustainable and smart biomass heating systems.
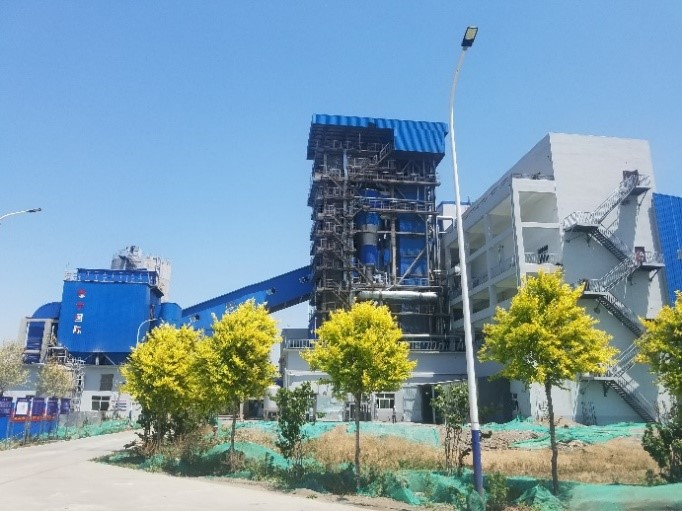
How Do Pressure, Temperature, and Process Duration Impact Sizing Decisions?
Selecting the right size for an industrial steam or biomass boiler involves more than just total heat or steam demand. If the operating pressure, required temperature, and process duration are not factored into the sizing decision, the result can be an inefficient or incapable system that either fails to meet production targets or wastes energy through poor thermal match. These three variables influence everything from boiler volume to steam generation rate and reserve capacity. They also dictate material choices, startup cycles, and buffer requirements. Ignoring them can lead to underpowered boilers, bottlenecked processes, and compliance issues—especially in critical or batch-based operations.
Operating pressure, process temperature, and duration significantly affect boiler sizing because they determine steam energy content, response speed, reserve capacity, and load profiles. Higher pressures and temperatures require more energy input and stronger boiler construction, while short or batch durations demand rapid output and thermal responsiveness. Sizing decisions must therefore balance total energy need with the rate and timing of delivery based on specific operating conditions.
These parameters are vital, particularly in industries like food processing, pharmaceuticals, chemicals, and district heating, where both volume and quality of heat or steam are critical.
Higher steam pressure reduces the boiler size required for the same thermal output.False
Higher pressure steam contains more energy per unit mass, but generating it requires more energy input, stronger construction, and larger system capacity, not smaller.
The Role of Pressure in Boiler Sizing
Steam pressure influences the enthalpy (usable energy) of steam and determines the structural and thermal load the boiler must handle.
Steam Pressure (bar) | Enthalpy of Steam (kJ/kg) | Boiler Impact |
---|---|---|
4 | ~2,740 | Lower energy density, less material stress |
8 | ~2,770 | Balanced load, common industrial level |
12 | ~2,790 | Higher energy per kg, stronger construction |
20+ | ~2,800+ | Higher shell strength, thicker walls, more energy |
Why it matters:
To produce steam at higher pressure, you must:
Use more energy input per kg of steam
Size for greater flow rate if process demand is time-sensitive
Account for flash steam potential and blowdown losses
Boiler Design Adjustments for Pressure
Parameter | High-Pressure Steam (>10 bar) | Low-Pressure Steam (<5 bar) |
---|---|---|
Shell thickness | Increased | Standard |
Safety valve pressure | Higher | Lower |
Steam drum & blowdown | Larger | Smaller |
Steam trap systems | More complex | Simpler |
Low-pressure boilers are easier and less costly to construct than high-pressure boilers.True
Lower pressure operation reduces material requirements, welding specifications, and certification demands, lowering initial capital costs.
How Process Temperature Affects Boiler Sizing
Steam temperature is a function of pressure—saturated steam has a direct pressure-temperature relationship:
Steam Pressure (bar) | Saturation Temp (°C) |
---|---|
3 | 134 |
6 | 158 |
10 | 184 |
16 | 201 |
But some processes demand superheated steam (above saturation point), which requires additional heat input beyond boiling. This impacts:
Boiler surface area
Fuel usage
Steam line insulation
Example:
A food sterilizer needing steam at 180°C would require ~9 bar saturated pressure. The boiler must be capable of generating sufficient pressure AND maintaining thermal output, especially if sudden demand occurs.
Process Duration and Load Profiling
Not all steam systems operate continuously. Many industrial processes are batch-based, cyclical, or intermittent. This affects how you size your boiler:
H3: Key Duration Scenarios
Scenario | Impact on Sizing |
---|---|
Short burst load | Requires fast ramp-up, possible oversizing or buffer |
Long, steady operation | Enables base-load sizing, avoids peaks |
High variability | Suggests modular or hybrid systems |
Daily Operation Load Curve Example
Time Period | Average Load (kW) | Peak Load (kW) | Process Note |
---|---|---|---|
6am–10am | 300 | 500 | Startup cycle |
10am–4pm | 400 | 450 | Steady operation |
4pm–6pm | 600 | 700 | Sterilization surge |
6pm–12am | 200 | 300 | Low production or standby |
In this example, a boiler sized only for average load (e.g., 400 kW) would fall short during sterilization cycles.
Solutions:
Size boiler for base + part peak, add thermal buffer
Use dual-boiler setup (one for base, one for peak)
Integrate smart modulation and load balancing controls
Sizing Chart: Pressure, Temperature & Duration Impact
Factor | Low Range | High Range | Sizing Outcome |
---|---|---|---|
Pressure | 3–5 bar | 10–20 bar | Stronger shell, more blowdown |
Temperature | <150°C | 180–220°C | Superheater required, more fuel |
Process Duration | Continuous (≥18 hrs/day) | Intermittent (2–4 hrs/day) | Buffer tank or hybrid system recommended |
Load Fluctuation | Steady (±10%) | Variable (±50%) | Modular or staged boiler needed |
Real-World Application: Chemical Plant Steam Demand
Operating Pressure: 12 bar
Steam Temperature: 190°C
Duration: 10-hour shift with 3 process peaks
Steam requirement: 2,000 kg/h average, 2,800 kg/h peak
Sizing solution:
Boiler: 2,400 kg/h capacity (base + 20% buffer)
Auxiliary electric boiler: 800 kg/h (on-demand)
Condensate recovery and steam accumulator used to smooth spikes
Summary
Pressure, temperature, and process duration are not just engineering afterthoughts—they are core variables that determine boiler size, configuration, and control strategy. Higher pressures and temperatures increase energy input needs and equipment strength. Short or unpredictable process durations demand faster response and additional capacity buffers. Only by fully considering these factors can you select a boiler that consistently meets performance needs without excessive cost, waste, or risk. Smart sizing means designing for how, when, and under what conditions your process consumes heat—not just how much.
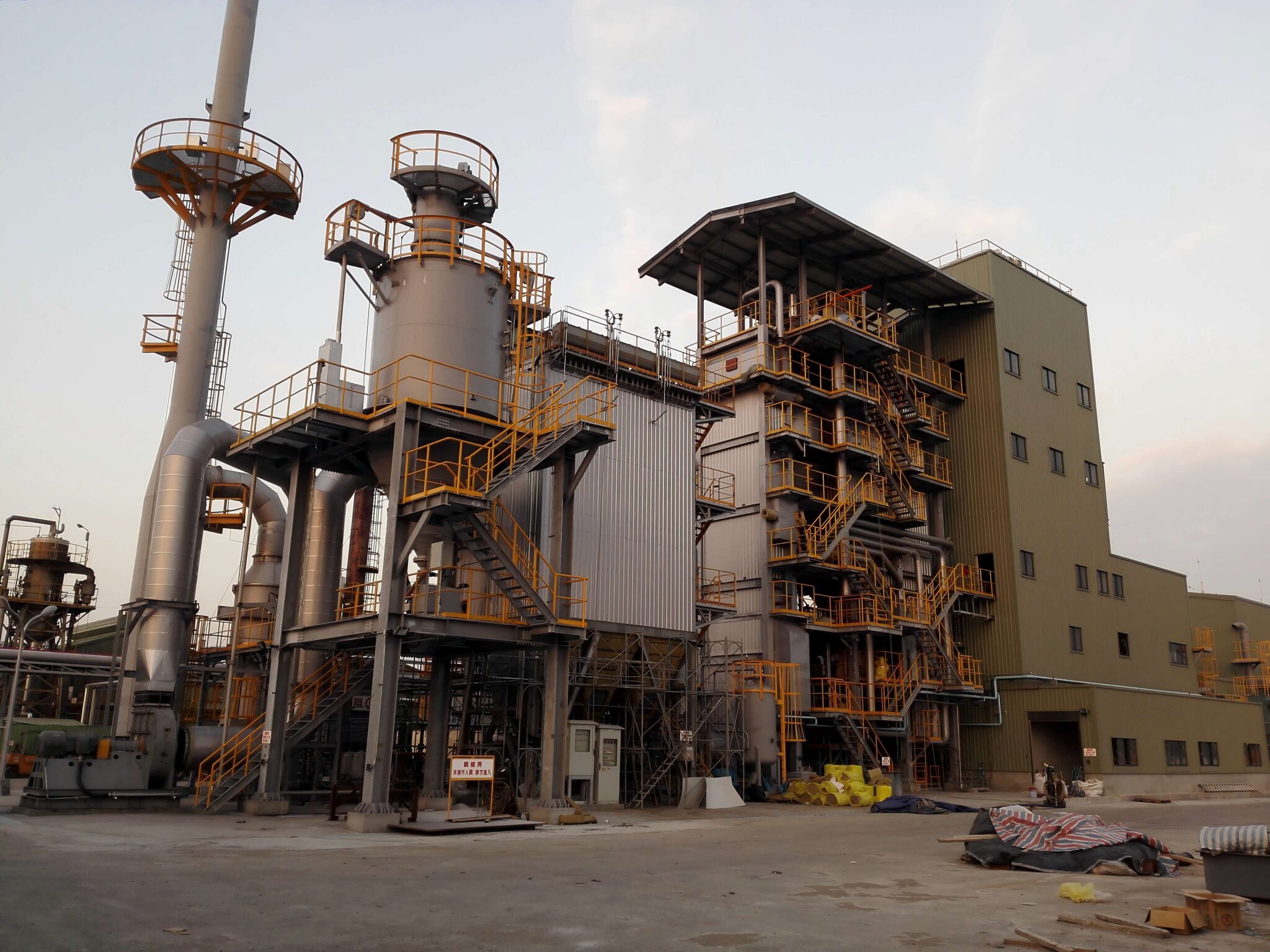
What Are the Implications of Seasonal and Load Variation on Boiler Capacity?
Many industrial and commercial boiler systems are either grossly oversized or chronically underpowered—not because of miscalculated heat demand, but due to a failure to account for seasonal fluctuations and load variation throughout the year. These two dynamics can have a massive impact on energy use patterns, boiler cycling behavior, and overall system performance. In heating-dominated climates or facilities with peak-and-trough production schedules, boiler systems must be designed to adapt. If seasonal variation is ignored, boilers run inefficiently for most of the year. If peak loads are taken as the only benchmark, system oversizing leads to excessive fuel use, high emissions, and degraded equipment. Understanding these fluctuations is key to designing a flexible, efficient, and reliable boiler plant.
Seasonal and load variations directly affect boiler capacity selection by creating mismatches between actual heat demand and boiler output during different times of the year or day. During low-load seasons or off-peak hours, oversized boilers operate inefficiently, cycling frequently and increasing emissions. During peak seasons or sudden demand surges, undersized boilers may fail to meet demand. Correct capacity planning involves sizing for base loads, integrating auxiliary or modular boilers for peaks, and using buffer tanks to smooth demand fluctuations.
These factors are especially critical in climates with cold winters, industries with batch operations, and district heating systems. Let’s explore how to design boiler systems that adapt to changing load conditions.
Oversized boilers perform better because they can handle all potential loads without issues.False
Oversized boilers operate inefficiently during low demand periods, leading to poor combustion, increased cycling, higher maintenance, and energy waste.
Understanding Seasonal Load Variation
H3: How Seasonal Demand Affects Boiler Operation
Seasonal variation is typically driven by changes in outdoor temperature, solar gain, and heating demand. In colder months, the demand for space heating and hot water increases significantly, while in warmer months, it drops off.
Season | Typical Boiler Load (as % of peak) |
---|---|
Winter (Dec–Feb) | 100% |
Spring (Mar–May) | 60–80% |
Summer (Jun–Aug) | 20–40% |
Autumn (Sep–Nov) | 60–80% |
H3: Real Impact on Boiler Performance
Boilers sized to meet winter peak loads may:
Short cycle during spring/summer
Operate well below rated efficiency
Fail to reach ideal flue gas temperatures
Increase stack losses and maintenance needs
In contrast, boilers sized only for summer or average loads may:
Fail to meet winter heating or steam process demand
Cause production delays or temperature control issues
Load Variation: Daily and Weekly Demand Shifts
Beyond seasonal variation, intra-day and weekly load fluctuations impact boiler performance. These are typical in:
Food processing with batch shifts
Laundries and sterilization facilities
Schools and hospitals (weekday vs. weekend demand)
District heating systems (morning and evening spikes)
Example: Weekly Load Profile (in kW)
Hour | Monday–Friday | Saturday | Sunday |
---|---|---|---|
6:00 | 100 | 80 | 60 |
9:00 | 400 | 200 | 150 |
12:00 | 600 (peak) | 300 | 200 |
18:00 | 300 | 150 | 100 |
23:00 | 100 | 60 | 50 |
Implications:
If sized for 600 kW, boiler will run at 20–30% capacity for most hours
If sized for 200 kW, boiler cannot meet peak loads without help
Design Solutions for Load Variation
H3: Use of Modular Boiler Systems
Modular boiler banks allow sequential operation of multiple smaller boilers. Benefits include:
High turndown ratio
Energy efficiency during part-load operation
Load matching through smart control
Scenario | Single Boiler (600 kW) | Modular (3×200 kW) |
---|---|---|
Peak Load | Handled easily | All modules operate |
Medium Load (300) | Runs at 50% (low efficiency) | Two modules operate |
Low Load (100) | Short cycling | One module operates |
H3: Buffer Tanks for Thermal Storage
Thermal buffers store excess heat during low load and release it during peak demand. Especially useful for:
Biomass boilers with slow response time
Facilities with short process bursts
Intermittent steam applications
Sizing Rule:
Buffer tank volume (liters) ≈ 15–25 liters per kW of boiler output
H3: Auxiliary Boiler Integration
For seasonal or peak demand coverage, auxiliary boilers:
Use fossil fuels or electricity
Start up quickly
Run only during spikes
This allows:
Primary biomass or base-load boiler to remain small
Full coverage without over-investment
Visual Comparison: Sizing Approaches
Sizing Approach | Pros | Cons |
---|---|---|
Peak Load Only (Oversize) | Covers all demands | Inefficient most of the year |
Average Load Sizing | Efficient year-round | Fails during peak demand |
Base Load + Buffer + Aux | Efficient + scalable | More complex system |
Modular Boiler Plant | Adaptive and energy-saving | Higher capital and control cost |
Real-World Case Study: School District Heating
Heat Demand:
Winter peak: 1,200 kW
Spring/fall: 700–800 kW
Summer (DHW only): 150–200 kW
Solution:
Biomass boiler: 800 kW for base load
Buffer tank: 12,000 liters
LPG auxiliary boiler: 500 kW
Load control via BMS (Building Management System)
Results:
85% of annual heat covered by biomass
Peak handled smoothly by buffer and LPG unit
28% fuel cost reduction and improved emissions profile
Summary
Seasonal and load variation are essential considerations in boiler capacity planning. Without accounting for these fluctuations, even the best-calculated systems will suffer from inefficiency, wear, and unmet demand. The key is to size for the base load, then supplement using modular boilers, thermal buffers, or auxiliary systems. This hybrid, flexible approach ensures high combustion efficiency, extended boiler life, and stable thermal output—no matter the time of year or day. A well-sized boiler is not just a match for peak performance—it’s a smart response to changing demand.
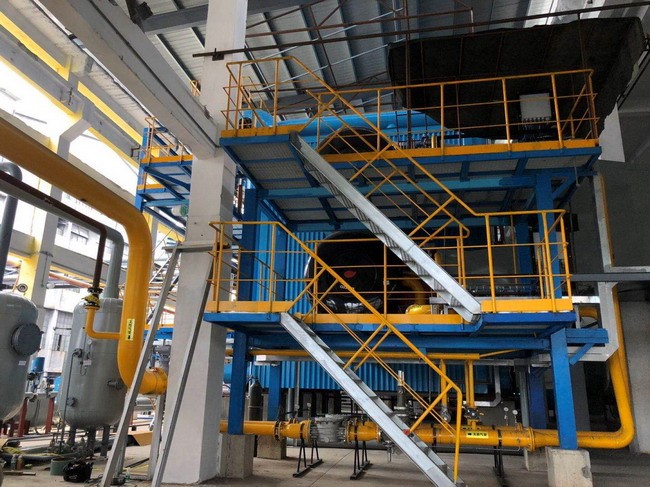
How Should Future Expansion and Hybrid System Integration Influence Sizing Strategy?
Boiler systems designed only for today’s needs often become tomorrow’s limitations. Facilities that neglect to account for future expansion or the integration of hybrid heating systems may face costly upgrades, energy inefficiencies, or downtime when scaling becomes necessary. As more industries transition to renewable energy and diversified energy sources, boiler sizing must go beyond short-term load calculations. Whether it’s planning for an additional production line, a new building wing, or solar and heat pump integration, future readiness requires strategic oversizing, modularity, and flexible control systems. The challenge is to balance current efficiency with future scalability—and that begins at the design stage.
Future expansion and hybrid system integration directly influence boiler sizing by requiring modular, scalable designs that can accommodate increased loads or renewable energy inputs over time. Boilers should be sized to handle current base loads efficiently, with capacity for extensions either through modular additions or auxiliary systems. Hybrid readiness also demands integration of control systems that can switch or blend heat sources (e.g., biomass, gas, solar) depending on availability, cost, and load profile. This approach prevents system bottlenecks and avoids overinvestment in unnecessary capacity upfront.
This strategy is especially important for industries growing in stages, public institutions with phased developments, and any facility aiming to reduce carbon emissions over the long term.
Sizing a boiler system only for current demand is the most efficient and cost-effective approach.False
While sizing strictly for current demand may reduce initial capital costs, it risks under-sizing the system when future loads are added. Strategic modular sizing enables long-term flexibility and cost savings.
Planning for Future Expansion: Why It Matters
Industrial and commercial facilities often undergo staged expansions:
Additional buildings or zones
New production equipment
Increased occupancy or throughput
If boiler capacity cannot accommodate this growth, consequences include:
Inconsistent temperatures
Steam shortages during peak
Need for full plant shutdown to upgrade system
H3: Future-Proofing Boiler Design
Smart sizing strategy means:
Installing a modular boiler system (e.g., 2 × 300 kW units instead of 1 × 600 kW)
Leaving physical space for a third or fourth unit
Using valved headers or manifolds for quick integration
Choosing controls with expansion capability
Factor | Fixed Sizing Risk | Modular/Future-Ready Benefit |
---|---|---|
Plant growth | Full system replacement | Just add another boiler |
Equipment failure | Downtime | Load shifted to other units |
Operational flexibility | One size fits none | Match demand efficiently |
Load spikes | Limited response | Easily engage extra module |
Hybrid System Integration: The New Normal
What is a Hybrid Boiler System?
A hybrid system combines two or more heat sources:
Biomass + solar thermal
Heat pumps + gas boilers
CHP + electric backup
Biomass + heat recovery + thermal storage
Each source can be optimized for:
Fuel cost
Emissions profile
Availability
Seasonal efficiency
Why it matters for sizing:
Reduces need for a single, oversized boiler
Enables dynamic load sharing
Makes use of renewable sources during low-load periods
Allows heat prioritization algorithms to balance cost and CO₂
Hybrid heating systems allow boiler capacity to be optimized for base load, improving overall efficiency.True
By handling base load with the primary boiler and managing peaks or variable loads with auxiliary sources, hybrid systems maintain efficient operation across seasons and load conditions.
Practical Sizing Strategy for Hybrid + Expansion-Ready Systems
H3: Step 1 – Identify Base and Future Loads
Load Type | Current (kW) | Future (kW) | Strategy |
---|---|---|---|
Space heating | 400 | 600 | Size base unit for 400, leave space for extra 200 |
Process steam | 500 | 800 | Use 2 × 400 kW modules |
DHW | 100 | 120 | Integrate solar or heat pump |
H3: Step 2 – Choose Modular, Scalable Boiler Units
Total Design Load (Future) | Initial Boiler Setup | Expansion Plan |
---|---|---|
1,000 kW | 2 × 300 kW | Add 1 × 400 kW as needed |
800 kg/h steam | 1 × 600 kg/h | Add 1 × 200 kg/h module |
H3: Step 3 – Integrate Hybrid Inputs via Smart Controls
Biomass boiler sized for 60–80% base load
Gas or electric backup boiler for peaks
Solar thermal preheats feedwater or storage
Heat pump covers shoulder seasons
Control system must:
Monitor outdoor temperature, fuel availability
Prioritize lowest-cost or renewable source
Automatically switch or blend sources
Interface with BMS or SCADA systems
System Diagram Example
A hybrid-ready biomass system might include:
Component | Function |
---|---|
Biomass boiler (500 kW) | Base load, 24/7 operation |
Gas boiler (300 kW) | Backup/peak load |
Solar collectors (50 m²) | Preheat for DHW or buffer |
Buffer tank (10,000 L) | Stores surplus heat during solar hours |
PLC control system | Manages source prioritization and safety |
Real-World Example: Public Hospital Heating Plant
Initial heat demand: 900 kW
Future demand (new wing): 1,300 kW
Hybrid system:
Biomass boiler: 900 kW (base)
Buffer tank: 15,000 liters
Gas boiler: 500 kW (peak/backup)
Solar preheat system (seasonal support)
Controls:
Predictive logic based on weather and load
Remote monitoring for performance optimization
Results:
High efficiency during all load conditions
Easy upgrade during expansion—no new boiler shutdown
Annual CO₂ emissions reduced by 48%
Payback in 4.2 years
Summary
Sizing a boiler system with future expansion and hybrid integration in mind is no longer optional—it’s a strategic necessity. As industries seek decarbonization, flexibility, and scalability, boiler systems must evolve into modular, multi-source platforms. Designing for base load, leaving physical and control headroom, and integrating renewable or auxiliary systems ensures that today’s investments remain viable tomorrow. It’s not just about installing a boiler—it’s about building a dynamic heat infrastructure that can grow, adapt, and optimize itself as your needs and energy landscape evolve.
🔍 Conclusion
Properly sizing your industrial biomass boiler is key to maximizing fuel efficiency, ensuring production reliability, and achieving environmental targets. By thoroughly assessing your heat load profile, fuel type, and operational dynamics, you can select a boiler that delivers consistent performance and long-term cost savings. Avoid generic estimations—let your sizing be based on real data and expert insight.
📞 Contact Us
💡 Need help sizing the perfect biomass boiler for your plant? Our technical specialists provide custom load analysis, fuel evaluation, and system design to ensure you choose the most efficient and future-ready solution.
🔹 Get in touch today and let us help you build a biomass system that fits your exact needs! 🌱🔥📐
FAQ
How is the capacity of an industrial biomass boiler calculated?
Biomass boiler capacity is based on your facility’s steam or hot water demand. It’s measured in tons per hour (TPH) for steam or in million BTU/hr (MMBtu/hr) for thermal energy. Accurate sizing considers peak demand, fuel energy value, and load variations.
What is the typical capacity range for industrial biomass boilers?
Industrial biomass boilers typically range from 0.5 TPH to over 100 TPH for steam generation and from 1 to 100+ million BTU/hr for hot water or heat applications. The exact range depends on process size, industry, and fuel type.
What factors affect biomass boiler sizing?
Factors include fuel type and moisture content, heating value, system efficiency, combustion technology, steam pressure/temperature needs, and daily operational hours. These determine the correct boiler size for reliable performance.
Why is proper sizing critical for biomass boilers?
Oversized boilers result in low efficiency and higher capital costs. Undersized units fail to meet load demand. Proper sizing ensures optimal combustion, fuel economy, and system longevity.
Can biomass boilers be customized for different fuel types or applications?
Yes. Biomass boilers can be engineered for specific fuels like wood chips, pellets, agricultural waste, or RDF. Designs vary based on ash content, fuel flow rate, and combustion behavior for each application.
References
Biomass Boiler Sizing and Selection Guide – https://www.energy.gov
Steam Demand Estimation for Industrial Boilers – https://www.sciencedirect.com
Fuel Properties and Boiler Design – https://www.researchgate.net
Sizing Biomass Heating Systems – https://www.bioenergyconsult.com
Boiler Efficiency and Fuel Impact – https://www.epa.gov
Thermal Load Calculations for Industry – https://www.mdpi.com
Biomass Combustion Technologies – https://www.energysavingtrust.org.uk
IEA Biomass Boiler Reports – https://www.iea.org
Customized Biomass Boiler Design – https://www.automation.com
Boiler System Performance Optimization – https://www.sciencedirect.com
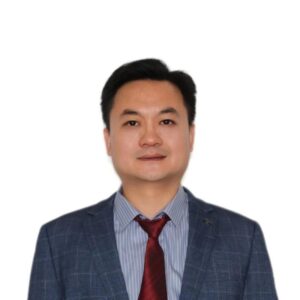