When designing or upgrading a power generation facility, selecting the correct capacity and size of an industrial power plant boiler is one of the most critical decisions you’ll make. An oversized boiler leads to energy waste, increased emissions, and higher capital costs, while an undersized unit can result in unreliable performance, production losses, and overloading of auxiliary equipment. To achieve optimal output, efficiency, and operational stability, it’s vital to tailor boiler sizing precisely to your plant’s energy demands and operational profile.
The capacity and size of an industrial power plant boiler you need depend on multiple factors, including the desired electrical output (MW), steam flow rate (tons/hour), operating pressure and temperature, fuel type, turbine specifications, plant load patterns, and auxiliary heat loads. Proper boiler sizing requires a detailed thermal balance, accounting for peak and base load scenarios, redundancy requirements, and plant scalability. A well-sized boiler ensures high combustion efficiency, turbine compatibility, and long-term operational reliability.
Below is a breakdown of the most important sizing factors to help you select the right power plant boiler.
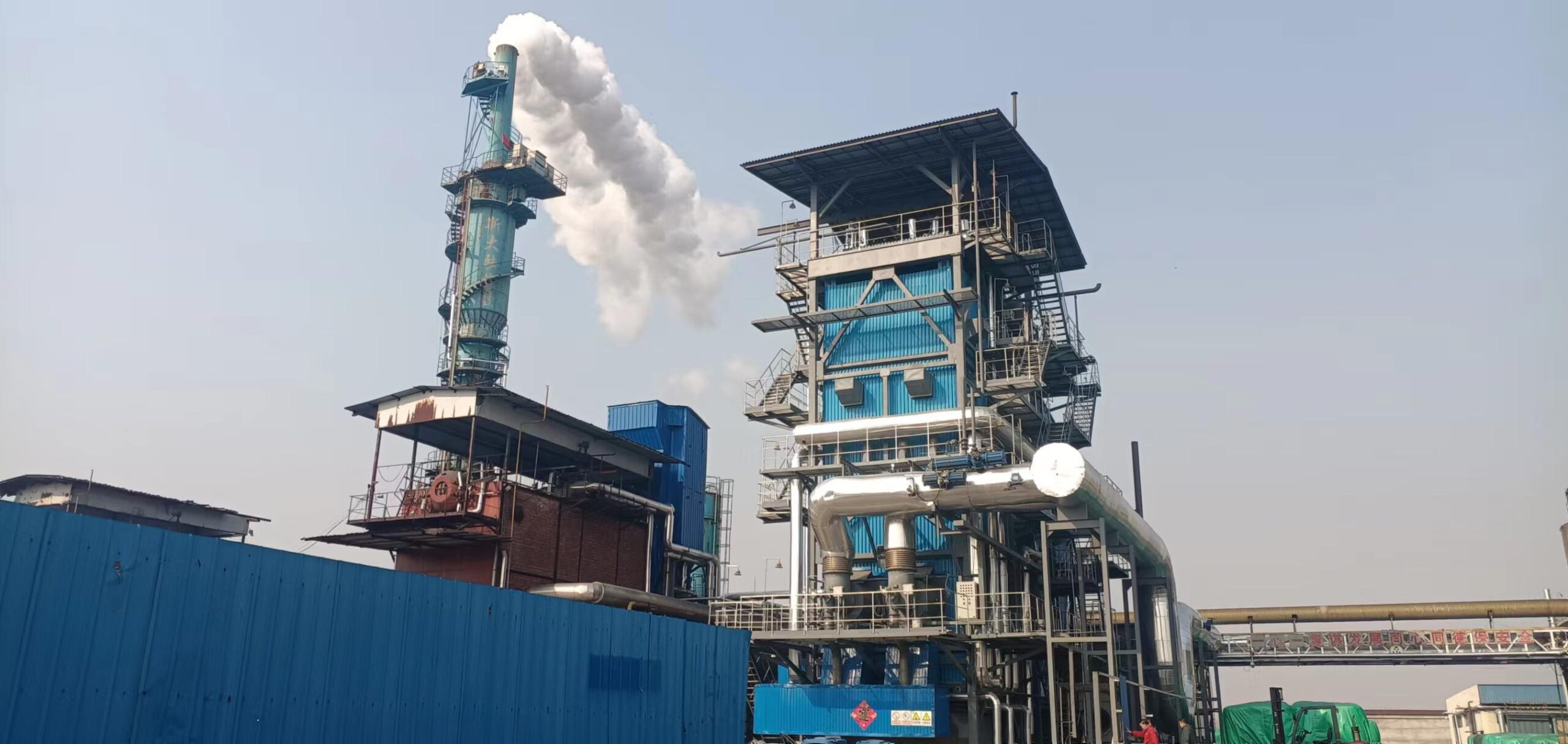
How Do You Calculate Boiler Size Based on Turbine and Steam Generation Requirements?
When designing a steam boiler system to drive turbines and support industrial operations, accurate boiler sizing is critical. If the boiler is too small, it won’t generate enough steam to run your turbine or meet other heat demands—leading to lost power, production downtime, or safety risks. On the other hand, oversizing wastes fuel, increases emissions, and shortens equipment life. Many users find the sizing process too technical, especially when dealing with complex formulas and thermodynamic charts. But don’t worry—you can calculate boiler size reliably using a simple step-by-step method based on practical values like turbine power, steam flow, and pressure level.
To size a boiler based on turbine and steam requirements, first estimate the steam flow needed by the turbine using its power output and efficiency. Then add any additional steam demand for heating, sterilization, or other processes. Finally, apply a safety margin (10–15%) to cover losses and variability. This gives you the total steam flow the boiler must produce, which determines its required output in tons per hour (TPH) or kilowatts (kW).
This method avoids complex math and helps you choose a reliable, right-sized boiler to power your turbine and operations.
Boiler size is calculated by combining turbine steam flow and all other process steam needs, then applying a safety factor.True
Boiler capacity must meet total steam demand, including turbine and process usage, and allow for system losses and load changes.
Step-by-Step: How to Calculate Boiler Size (No Complex Formulas)
✅ Step 1: Determine the Steam Needed by the Turbine
Steam turbines require a steady steam flow to generate electricity. A good rule of thumb:
For every 1,000 kW of power, the turbine needs around 14,000 to 16,000 kg of steam per hour (at high pressure like 40–60 bar)
If you’re not sure, use 15,000 kg/h per MW as a safe estimate
Example:
If your turbine is rated at 3 MW (3,000 kW), estimated steam requirement is:
3 × 15,000 = 45,000 kg/h
✅ Step 2: Add Other Steam Usage
Now list all other processes that need steam:
Process Area | Steam Use (kg/h) |
---|---|
Food processing line | 5,000 |
Water heating & washing | 3,000 |
Building heat network | 4,000 |
Total Extra Demand | 12,000 kg/h |
Add this to the turbine’s steam demand:
45,000 + 12,000 = 57,000 kg/h
✅ Step 3: Include a Safety Margin (10–15%)
Why? Steam demand may vary due to:
Startups or shutdowns
Pipe heat loss
Unmeasured system leaks
Apply 15% margin:
57,000 kg/h × 1.15 = 65,550 kg/h
This is your final boiler sizing target.
Convert to Boiler Output Units
Most industrial boilers are rated in tons per hour (TPH) of steam.
Steam Flow (kg/h) | Boiler Size (TPH) |
---|---|
10,000 | 10 TPH |
25,000 | 25 TPH |
65,000 | 65 TPH |
In the example above, you would need a 65 TPH boiler, or two 35 TPH boilers in parallel for flexibility.
Boiler Sizing Summary Table (Quick Reference)
Turbine Output (MW) | Estimated Steam (kg/h) | + Process Steam (kg/h) | Total Boiler Size (TPH) |
---|---|---|---|
1 MW | 15,000 | 5,000 | ~23 TPH |
2 MW | 30,000 | 10,000 | ~46 TPH |
3 MW | 45,000 | 12,000 | ~65 TPH |
5 MW | 75,000 | 15,000 | ~105 TPH |
Add 10–15% for system margin
Additional Considerations
Factor | Why It Matters |
---|---|
Steam Pressure | Higher pressure = more energy per kg, may reduce flow |
Feedwater Temperature | Colder water requires more energy to reach steam |
Turbine Efficiency | Less efficient = needs more steam |
Condensate Recovery | Improves efficiency and reduces fuel use |
Backup Capacity | Consider extra boiler or dual-fuel option |
Real-Life Example: Dairy Plant with Cogeneration
Steam turbine: 2 MW
Process steam demand: 10,000 kg/h
Calculated boiler size:
Turbine: 2 × 15,000 = 30,000 kg/h
Total with process = 40,000 kg/h
With margin = 46,000 kg/h
Installed boiler: 50 TPH
Backup: One 15 TPH oil-fired boiler
Result:
Consistent power generation
Reliable heating for pasteurization
18% lower fuel consumption vs. old oversized boiler
Summary
Calculating boiler size based on turbine and steam generation needs doesn’t have to involve difficult formulas. Use practical estimates of steam flow per MW of turbine power, add all other steam uses, and apply a reasonable safety margin. Convert that flow to TPH and choose a boiler (or modular setup) that matches this output. The result: a right-sized boiler system that supports your turbine, process steam users, and energy efficiency goals—without overbuilding or risking underperformance.
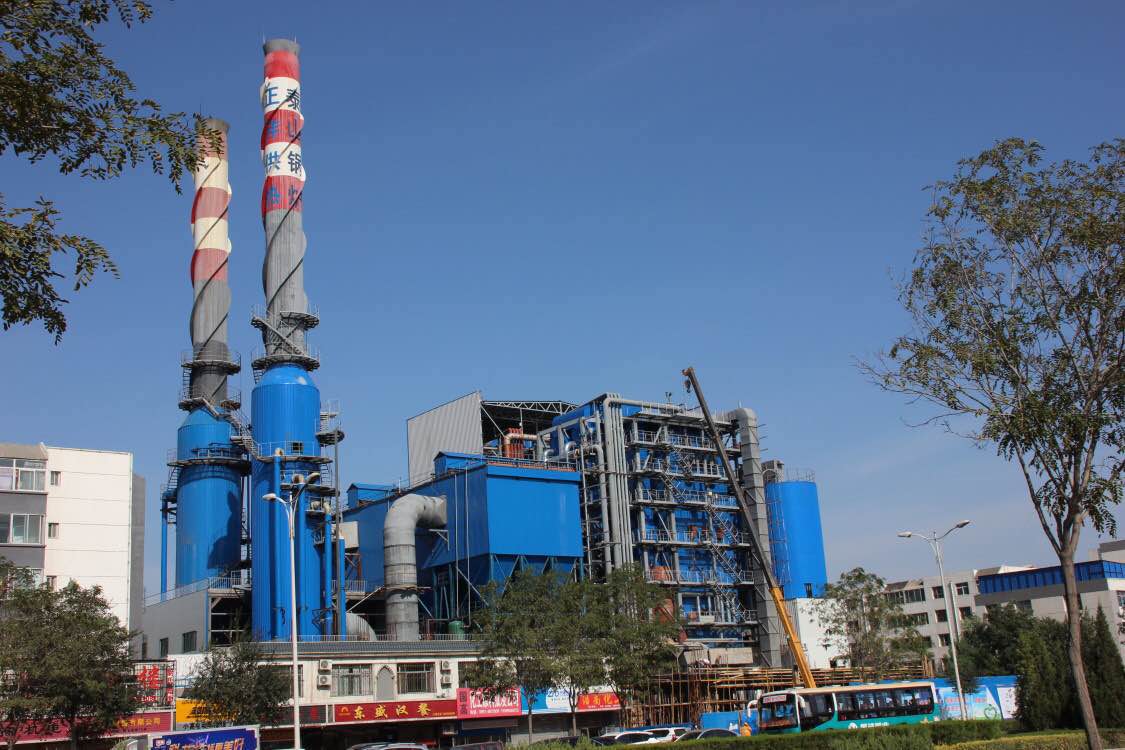
What Steam Pressure, Temperature, and Flow Rates Are Required for Your Power Output Goals?
When designing a steam-based power generation system, one of the most important engineering tasks is selecting the right steam pressure, temperature, and flow rate to meet your power output target. These three parameters determine how much energy the turbine receives and how efficiently that energy is converted into electricity. If the steam pressure or temperature is too low, the turbine won’t generate enough power. If the flow rate is undersized, it will limit production during peak demand. Properly balancing all three ensures that the boiler, turbine, and generator work together efficiently.
To meet specific power output goals, the steam system must deliver the correct combination of pressure (typically 30–130 bar), temperature (350–540°C), and flow rate (kg/h), depending on the turbine’s design and efficiency. Higher pressure and temperature steam produces more power per kilogram, while total flow rate determines how much total energy reaches the turbine. These parameters must be matched to the generator capacity and boiler output for optimal performance.
Understanding how these values relate helps you size your system effectively, avoid underperformance, and design a flexible, scalable power solution.
Higher steam pressure and temperature result in more power output from the same mass flow rate.True
Superheated high-pressure steam has greater enthalpy, allowing more energy to be extracted by the turbine for each unit of steam.
Typical Steam Parameters for Power Generation
Power Output (kW) | Steam Pressure (bar) | Steam Temperature (°C) | Steam Flow (kg/h) | System Type |
---|---|---|---|---|
500 kW | 20–35 | 350–400 | 7,000–8,500 | Small industrial CHP |
1,000 kW (1 MW) | 40–60 | 450–480 | 13,000–16,000 | Medium turbine |
3,000 kW (3 MW) | 60–80 | 480–500 | 40,000–48,000 | High-efficiency plant |
5,000 kW (5 MW) | 80–100 | 500–520 | 65,000–75,000 | Commercial-scale turbine |
10,000 kW (10 MW) | 100–130 | 520–540 | 130,000–150,000 | Utility-grade system |
These numbers are estimates for condensing steam turbines operating with ~80–85% efficiency.
Pressure and Temperature Guidelines
✅ Steam Pressure
Common pressure levels:
Low: 10–20 bar (for heating or low-efficiency generation)
Medium: 40–60 bar (general industrial power use)
High: 80–130 bar (modern high-output turbines)
Higher pressure = higher enthalpy = more energy per kg of steam
Boiler design must match pressure rating (ASME, EN standards)
✅ Steam Temperature
Dry saturated steam is enough for low-pressure turbines
Superheated steam (450–540°C) is required for high-performance turbines
High temp reduces condensation and improves turbine blade life
✅ Flow Rate
The steam mass flow (kg/h) defines total available energy
Must be continuous, especially in turbine-driven systems
Higher flow = higher power, but also needs more boiler capacity
Boiler-Turbine Matching Table (Simplified)
Power Output Goal | Required Boiler Output (TPH) | Boiler Pressure (bar) | Turbine Steam Inlet Temp (°C) |
---|---|---|---|
1 MW | 15–16 TPH | 40–60 | 450°C |
3 MW | 45–50 TPH | 60–80 | 480°C |
5 MW | 70–75 TPH | 80–100 | 500°C |
10 MW | 140–150 TPH | 110–130 | 520°C |
Additional Considerations
Design Factor | Effect on Steam Parameters |
---|---|
Turbine efficiency (isentropic) | Affects required flow for given output |
Condenser pressure (exhaust) | Lower exhaust pressure increases efficiency |
Boiler superheater capacity | Limits max temperature delivered to turbine |
Load profile (peak vs base) | May require flexible flow control or dual boilers |
Case Study: Biomass Cogeneration System – 3 MW Output
Turbine rating: 3 MW condensing
Steam required: ~45,000 kg/h
Steam pressure: 65 bar
Steam temperature: 480°C
Boiler type: High-pressure water tube boiler
Backup system: 15 TPH gas-fired boiler for process-only operation
Result:
85% uptime
Fuel flexibility (biomass + backup)
Integrated with district heating in winter
Summary
To achieve your target power output from a steam turbine, your boiler and steam system must deliver the correct pressure, temperature, and flow rate consistently. Higher power levels require higher steam parameters and greater flow. Matching these to the turbine’s design specification ensures that the system operates efficiently, safely, and within regulatory standards. Whether you’re designing for 1 MW or 10 MW, your power starts with properly engineered steam.

How Does Fuel Type and Calorific Value Influence Boiler Design and Capacity?
One of the most important factors in designing an industrial boiler is the type of fuel and its calorific value (CV)—that is, how much energy the fuel provides per kilogram. Different fuels (like coal, biomass, oil, or gas) burn differently, deliver different amounts of energy, and leave different residues. If a boiler is designed for one type of fuel, and a lower-energy fuel is used without proper adjustments, it will not reach its target heat output, and problems like incomplete combustion, high emissions, or even flameouts can occur. On the other hand, using a higher-CV fuel in a system not designed for it can damage components or overheat surfaces. Therefore, boiler size, furnace volume, combustion air, and material selection must all be tailored to the fuel’s properties and energy density.
Fuel type and calorific value influence boiler design and capacity by determining how much energy is released during combustion, the volume of fuel required, and the furnace and heat exchange surface area needed to achieve the desired output. Low-CV fuels like wet biomass require larger combustion chambers and higher feed rates, while high-CV fuels like natural gas or oil need compact designs with controlled burn zones. Each fuel also produces specific ash, moisture, and emission profiles, which affect the boiler’s material selection, combustion system, and emission control needs.
This fuel-dependent design principle ensures optimal combustion efficiency, safety, and regulatory compliance.
Different fuel types can be used in the same boiler without design changes as long as they have similar heat outputs. False
Even if calorific values are similar, fuel characteristics like burn rate, ash content, and moisture require specific boiler designs for stable, clean, and efficient combustion.
Fuel Type Comparison: Key Properties
Fuel Type | Typical Calorific Value (MJ/kg) | Moisture (%) | Ash Content (%) | Burn Behavior |
---|---|---|---|---|
Bituminous Coal | 24–32 | 2–12 | 10–20 | Steady flame, moderate slag |
Lignite | 9–18 | 30–50 | 15–40 | High ash, high moisture |
Biomass (Wood Chips) | 9–16 | 20–55 | 1–6 | Fast burn, variable energy |
Biomass (Pellets) | 16–19 | 8–12 | <1 | Uniform, clean combustion |
Fuel Oil | 40–42 | <1 | Trace | High heat, compact flame |
Natural Gas | 48–50 | 0 | 0 | Clean, precise combustion |
Calorific value is measured as net (LHV) for practical boiler sizing, since it excludes energy lost as latent heat from moisture.
How Calorific Value Affects Boiler Size and Capacity
✅ Lower CV → More Fuel Volume Needed → Larger Boiler
For a fixed heat output (say 10,000 kW), the amount of fuel required changes dramatically:
Fuel | Calorific Value (MJ/kg) | Fuel Needed (kg/h) |
---|---|---|
Natural Gas | 50 | ~720 |
Bituminous Coal | 28 | ~1,300 |
Biomass (Wet) | 10 | ~3,600 |
This means:
Furnace must be larger for low-CV fuels to allow complete combustion
Feeding system must be faster to supply higher volumes
Ash and moisture handling systems must be more robust
Boilers using low-calorific fuels require larger combustion chambers and higher fuel input rates to maintain output.True
More fuel must be burned to reach the same energy level, requiring more space, air, and time in the furnace.
Boiler Design Impacts by Fuel Type
🔥 1. Furnace Size and Volume
Biomass and lignite need large combustion chambers due to:
Lower flame temperatures
Higher residence time
Larger fuel particle size
🔥 2. Air and Flue Gas System
Low-CV fuels produce more flue gas volume per MW of heat
Requires:
Larger air fans
Higher stack flow capacity
Advanced oxygen trim controls
🔥 3. Ash and Slag Handling
Coal and lignite produce heavy ash loads → Ash hoppers, screw conveyors
Biomass can form clinkers → needs refractory linings and grate agitators
🔥 4. Heat Exchange Surface
Low-CV fuels create more gas volume → larger superheaters, economizers
High-CV fuels need compact, high-heat-rate surfaces
Boiler Sizing Example by Fuel Type (for 10 MW Output)
Fuel Type | Fuel Flow (kg/h) | Boiler Volume (Est. m³) | Ash System Complexity |
---|---|---|---|
Natural Gas | ~720 | Small | Minimal |
Fuel Oil | ~880 | Small | Minimal |
Bituminous Coal | ~1,300 | Medium | Moderate |
Lignite | ~3,600 | Large | High |
Biomass (Wet Chips) | ~3,800 | Very Large | Very High |
Matching Fuel to Boiler Type
Fuel Type | Preferred Boiler Type | Why? |
---|---|---|
Natural Gas | Fire-tube, condensing | Precise flame control, compact size |
Bituminous Coal | Pulverized coal (PC), CFB | High heat density, moderate slagging |
Lignite | CFB or Fluidized Bed | Tolerates high moisture and ash |
Biomass | Grate-fired, Fluidized Bed | Handles large volume, varied quality |
Fuel Oil | Fire-tube or water-tube, compact | Fast ignition, clean flame |
Case Study: Biomass to Coal Conversion – 15 TPH Boiler
Original fuel: Wood chips (CV = 12 MJ/kg, 40% moisture)
Target fuel: Bituminous coal (CV = 28 MJ/kg, 10% ash)
Challenges:
Overheating of furnace walls due to hotter flame
Ash buildup in grate
Boiler efficiency improved from 74% to 86%
Adaptations:
Reduced primary air volume
Installed additional tube shields
Modified ash scrapers
Tuned flue gas velocity to prevent erosion
Summary
The type of fuel and its calorific value have a direct and significant impact on how a boiler is designed and sized. Lower-energy fuels require more combustion space, more fuel per hour, and more robust ash handling, while higher-energy fuels offer compact, cleaner-burning solutions. Choosing the right boiler type and customizing its internal systems based on the fuel ensures combustion efficiency, safety, and cost-effectiveness. In any industrial application, designing the boiler around the fuel—not the other way around—is essential for success.
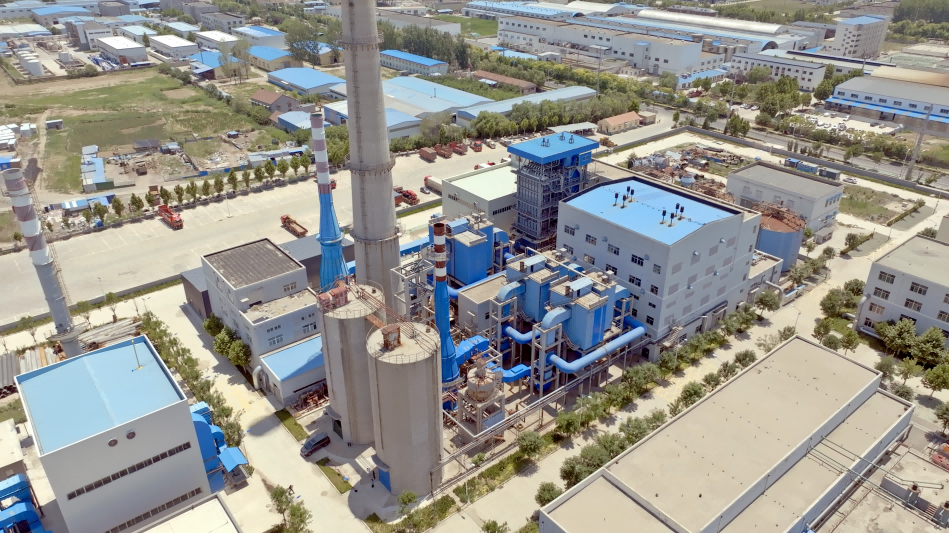
What Role Do Peak Load Conditions and Load Fluctuation Patterns Play in Sizing Decisions?
Boiler sizing is not just about meeting an average daily demand. If your system can’t handle peak load conditions or adapt to frequent load fluctuations, you’ll face performance problems like pressure drops, inefficient cycling, or system stress. Designing purely for average conditions risks underperformance during critical demand spikes. Conversely, oversizing for infrequent peaks wastes fuel, increases emissions, and shortens equipment life. That’s why understanding your load profile—including daily, weekly, and seasonal variations—is essential for right-sizing your boiler system to achieve efficiency, reliability, and scalability.
Peak load conditions and load fluctuation patterns are crucial in boiler sizing decisions because they determine whether the system can handle demand spikes and respond flexibly to variable loads without sacrificing efficiency. Boilers must be sized not only for average usage but also for peak requirements and load variability. This often leads to modular or hybrid designs that maintain efficiency at low loads while delivering full output when needed. Ignoring these factors results in oversized or underperforming systems, frequent cycling, and high operational costs.
Proper boiler sizing means planning for both the highest and most frequent load scenarios.
Peak load conditions should always dictate boiler sizing without considering load fluctuation.False
While peak load must be accounted for, a system sized only for peak demand without addressing fluctuation will be oversized for most operating hours, reducing efficiency.
What Is Peak Load and Why It Matters?
Peak load is the highest steam or heat demand your system will experience—typically:
During startup of production lines
During winter heating for buildings
In sterilization or batch processes
During turbine load increases
If the boiler can’t meet the peak load:
Steam pressure may drop
Critical equipment can malfunction
Production or power output may stall
But sizing for peak only leads to an oversized system that runs inefficiently 90% of the time.
Understanding Load Fluctuation Patterns
Typical Types of Load Fluctuation:
Pattern Type | Example Application | Sizing Implication |
---|---|---|
Daily variation | Schools, hospitals | Morning peak, evening low → turndown needed |
Batch process spikes | Breweries, sterilization lines | Short-term high demand → need fast ramp-up |
Seasonal variation | District heating, food plants | Winter/summer swing → modular sizing preferred |
Continuous process | Paper mill, chemical plant | Steady load → Base load sizing is optimal |
A well-designed system handles both peaks and valleys efficiently.
Visualizing Load Profile: Example for Food Factory
Hour of Day | Steam Demand (kg/h) |
---|---|
6:00 | 1,000 |
9:00 | 6,000 (peak sterilization) |
12:00 | 4,500 |
15:00 | 3,000 |
20:00 | 2,000 |
24:00 | 500 |
Sizing Only for 6,000 kg/h = 75% of boiler’s life in low-load condition
→ Frequent cycling, lower efficiency, and high O&M costs.
Smart Sizing Strategy: Balance Peak and Average Loads
Sizing Method | Approach | Pros | Cons |
---|---|---|---|
Peak-only sizing | Size to match highest possible demand | No performance risk during spikes | Oversized, inefficient at low loads |
Average load sizing | Size based on mean demand | High efficiency most of the time | Fails under peak conditions |
Modular/hybrid sizing | Base boiler for average, + auxiliary for peaks | Best of both worlds | Higher CAPEX, complex controls |
Buffer-assisted sizing | Use thermal storage to meet short peaks | Reduces boiler oversizing | Requires space and insulation |
Modular Boiler Plant Example: 20 TPH Peak Load System
Component | Capacity | Role |
---|---|---|
Base Boiler 1 | 10 TPH | Handles continuous base load |
Auxiliary Boiler 2 | 5 TPH | Activates during day peaks |
Auxiliary Boiler 3 | 5 TPH | Redundancy + peak support |
Buffer Tank | 15,000 liters | Stores heat for demand spikes |
Modularity improves turndown ratio, fuel economy, and system resilience.
Modular boiler systems provide better response to fluctuating loads than single large units.True
Multiple smaller boilers can be sequenced to match real-time demand, improving efficiency and avoiding cycling at low loads.
Real-World Case: Municipal District Heating Plant
Average Load: 10 MW
Winter Peak Load: 18 MW
Summer Load: 3 MW
Final Configuration:
2 × 6 MW biomass boilers (base load)
1 × 8 MW gas-fired boiler (peak, backup)
Smart load management system
Results:
Peak demand fully covered
Year-round operation at optimal efficiency
Fuel savings of 22% compared to oversized system
Recommendations for Load-Aware Sizing
Condition | Recommendation |
---|---|
Highly variable load | Use modular or hybrid system |
Short peak durations | Use buffer tanks to cover spikes |
Long peak periods (winter) | Install auxiliary boilers sized for peaks |
Frequent on/off cycling | Add VFDs and auto-controls to modulate load |
Budget constraints | Size for 85–90% of peak + add future capacity |
Summary
Boiler sizing must take into account both peak load conditions and daily/seasonal load fluctuation patterns. Sizing only for the average leads to system failures during demand spikes. Sizing only for the peak results in inefficiencies most of the time. The optimal approach is to balance the two, using modular boilers, thermal buffers, and intelligent controls to match output to demand in real time. With the right load-aware design, your boiler system becomes not only reliable—but flexible, efficient, and future-proof.
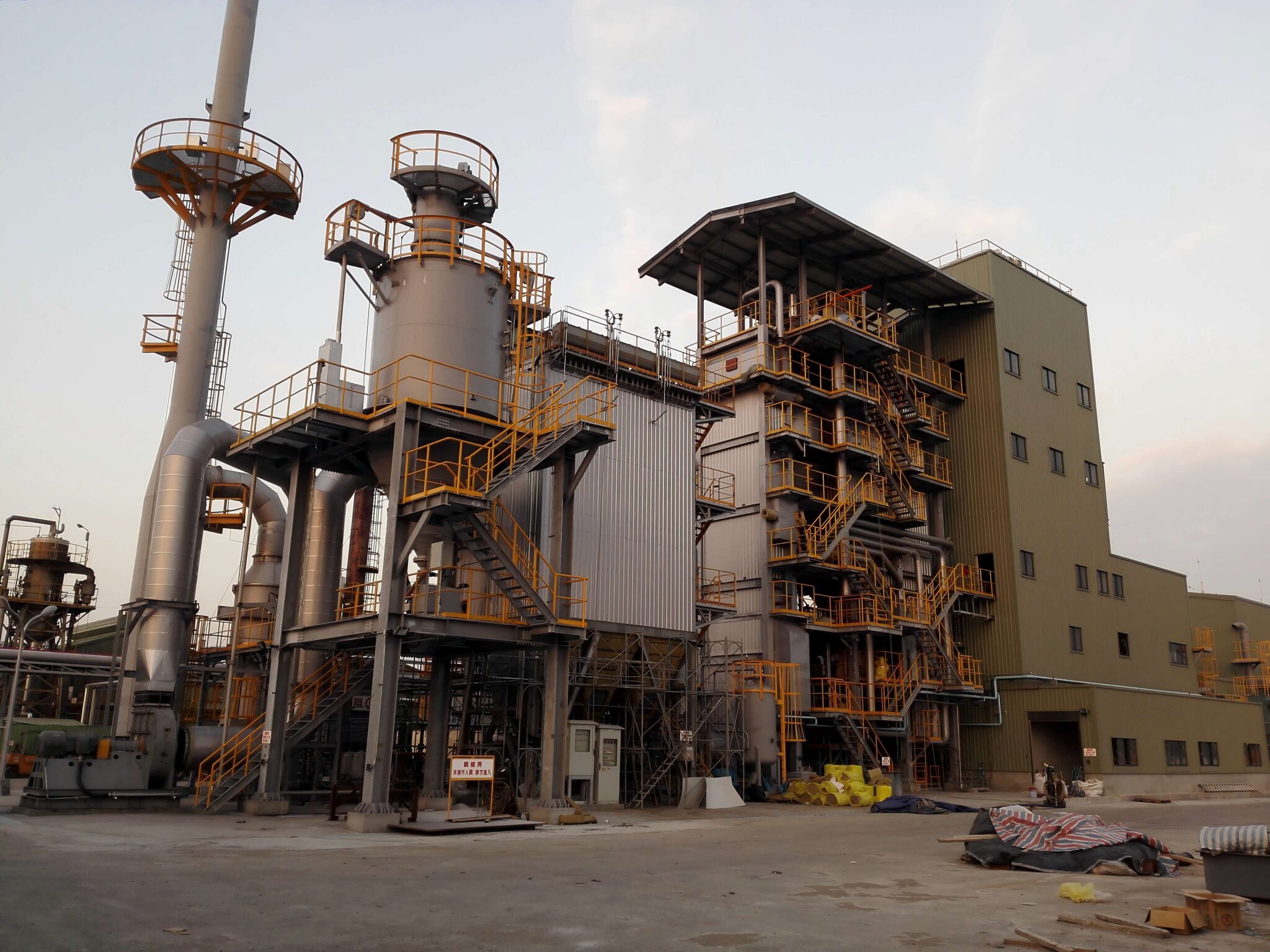
How Should Future Expansion, Modularity, or Backup Capacity Be Considered?
One of the biggest mistakes in boiler system design is only sizing for current demand without considering future growth, operational flexibility, or system reliability. Many industries expand production lines, add facilities, or increase operating shifts—but their boiler systems weren’t designed to scale, resulting in underperformance, costly retrofits, or full system replacements. Others lack backup capacity, meaning one unexpected failure can halt production entirely. A smart boiler system must support modular upgrades, provide redundancy, and leave room—both physically and technically—for future expansion.
Future expansion, modularity, and backup capacity must be considered in boiler system design to ensure operational continuity, scalable growth, and efficient performance over the system’s lifecycle. Expansion readiness involves designing infrastructure for higher future loads, modularity enables load-matched operation and energy savings, and backup capacity ensures reliability during maintenance or emergencies. Together, they protect productivity, lower long-term costs, and prevent premature obsolescence.
These elements transform your boiler from a fixed system into a resilient thermal platform.
Designing a boiler system for current needs only is the most cost-effective approach.False
This short-term approach can lead to costly upgrades, downtime, or early replacement when operations expand. Planning for future capacity and backup ensures long-term value.
Why Plan for Future Expansion?
Reason | Potential Change |
---|---|
Business growth | More buildings, process lines, or shifts |
Regulatory demands | Need for higher efficiency or emissions control |
Sustainability upgrades | Adding solar preheat, CHP, or biogas |
Example:
Current heat load = 10 MW
Planned expansion = +6 MW within 5 years
If you don’t plan now, retrofitting will be disruptive and expensive
Design Tip:
Size headers, flues, controls, and boiler house footprint to allow an extra unit later
Benefits of Modularity in Boiler Systems
What is Modularity?
Using multiple smaller boilers instead of one large one:
Operate sequentially or simultaneously
Adjust output to match real-time demand
Turn off unneeded units to save fuel
Advantages:
Feature | Modular Boilers | Single Large Boiler |
---|---|---|
Load matching | Excellent | Poor (leads to cycling) |
Redundancy | Yes (N+1 possible) | No redundancy |
Maintenance flexibility | Keep running during repairs | Requires full shutdown |
Scalability | Easy to add units | Difficult to expand |
Example: Instead of 1 × 10 TPH boiler, install 2 × 5 TPH or 3 × 3.5 TPH boilers
Modular boiler systems are more energy-efficient during partial load conditions.True
Modular setups allow only the required number of boilers to operate at optimal load, reducing fuel waste and thermal losses.
Importance of Backup Capacity
Backup capacity ensures the boiler plant can:
Maintain operations during a breakdown
Meet demand during maintenance or inspection
Comply with safety and insurance policies
Types of Backup Systems:
Backup Strategy | How It Works |
---|---|
N+1 Configuration | One extra boiler installed (e.g. 3 for 2-load) |
Auxiliary Fuel Boiler | Secondary unit using gas or oil |
Mobile/temporary unit | Emergency rental connection |
Industries like hospitals, data centers, and food processing often require 100% backup
Boiler Layout and Infrastructure for Expansion
Component | Design for Expansion |
---|---|
Steam headers | Sized for full future load |
Chimneys/flue ducts | With connection stubs for future units |
Water treatment plant | Capacity for additional boiler feedwater |
Electrical systems | Panel space and breakers for new units |
Control systems (PLC/SCADA) | Expandable to handle more loops and sensors |
Boiler house | Physical room and foundations for new equipment |
Real-World Case: Pharma Plant Expansion Plan
Initial demand: 8 TPH
Future target: 12 TPH within 3 years
Solution:
Installed 2 × 5 TPH steam boilers
Reserved pipe, flue, and BMS capacity for 1 more unit
Control system designed for 4 boiler inputs
Result:
Smooth future expansion with zero downtime
Load sharing between units increased annual fuel savings by 17%
Enabled maintenance rotation without production interruption
Smart Design Strategies
Scenario | Recommended Strategy |
---|---|
Uncertain growth plans | Modular design + space for 1 extra unit |
High reliability required | N+1 backup boiler (hot or cold standby) |
High load fluctuation | Mix of base and peak-load boilers |
Limited initial budget | Install for 80% of peak + pre-install headers and controls |
Decarbonization in future | Use a hybrid-ready system (biomass + gas + solar preheat) |
Summary
In today’s industrial landscape, where scalability, reliability, and sustainability are essential, designing a boiler system with future expansion, modularity, and backup in mind is no longer optional—it’s strategic. Anticipating growth, integrating modularity, and ensuring redundancy allow your boiler plant to evolve with your operations without disruption. This approach not only reduces total cost of ownership but also enhances energy efficiency and operational uptime. Whether you’re building a new facility or upgrading an old one, a future-proof boiler system means you’re always ready for what’s next.
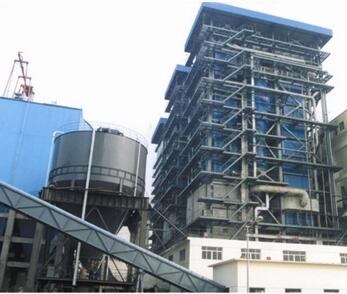
What Are the Physical Space and Infrastructure Constraints for Installing a High-Capacity Boiler?
When planning to install a high-capacity industrial boiler—whether for process steam, power generation, or district heating—the most underestimated challenge is often the physical space and infrastructure required to support it. Boilers in the 20 TPH, 50 TPH, or even 100 TPH class are massive, both in size and utility needs. Many retrofitted or older plants lack sufficient room for combustion air, flue gas handling, access clearance, or proper load-bearing structures. Failing to evaluate these site-specific constraints leads to costly modifications, project delays, or operational risks. Therefore, accurate infrastructure planning and space allocation are as essential as boiler selection itself.
Installing a high-capacity boiler requires detailed planning around physical space, structural support, piping layout, ventilation, emissions stack routing, access for maintenance, and utilities like fuel, water, power, and blowdown systems. These constraints directly affect the feasibility, cost, and safety of installation. Boiler rooms must provide sufficient floor space, ceiling height, equipment clearance, and access pathways, while the facility’s structural and utility systems must be designed to support high heat loads, large volumes of fluid, and heavy mechanical loads.
Ignoring these physical and infrastructural needs can result in major design rework, safety non-compliance, or reduced operational reliability.
All industrial boiler systems can be installed in existing mechanical rooms with minimal modifications.False
High-capacity boilers often exceed the floor load, ceiling clearance, ventilation, and service access capabilities of existing rooms, requiring structural reinforcements or expanded footprints.
Physical Footprint and Space Requirements
Key Dimensions for High-Capacity Boilers (Typical Ranges)
Boiler Capacity (TPH) | Length (m) | Width (m) | Height (m) | Required Floor Area (m²) |
---|---|---|---|---|
10 TPH | 5–6 | 2.5–3 | 4–5 | 15–20 |
20 TPH | 7–8 | 3–4 | 5–6 | 25–32 |
50 TPH | 9–11 | 4.5–5.5 | 7–9 | 45–60 |
100 TPH | 12–15 | 6–8 | 10–12 | 80–120 |
Note: These dimensions exclude additional area for fuel handling, pumps, economizers, air preheaters, water treatment systems, and access clearances.
Clearance Requirements
Area | Clearance (m) |
---|---|
Front (for burner access) | 2.0–2.5 |
Rear (for flue outlet) | 1.5–2.0 |
Sides (service access) | 1.2 minimum |
Top (for lifting/maintenance) | 1.5–3.0 (above unit) |
Design Tip: Include full boiler pull space in at least one direction.
Infrastructure Systems That Constrain Boiler Installation
1. Structural Load Capacity
Boilers are extremely heavy:
A 50 TPH boiler with water may weigh >80–100 tons
Floor must support point loads from feet, skids, or base frames
Reinforced concrete slabs typically required with vibration isolation
2. Fuel Handling and Delivery
Fuel Type | Infrastructure Needs |
---|---|
Natural Gas | Piping from pressure-reducing station, safe zones, explosion venting |
Oil (diesel, HFO) | Day tanks, unloading bays, bund walls, fire-rated separation |
Coal/Biomass | Conveyor systems, silos, dust collection, fuel feeders |
Ensure fuel delivery paths and fire separation walls comply with NFPA or local codes.
3. Water Supply and Treatment
High-capacity boilers consume large volumes of treated water:
Deaerator, softener, RO, or DM plant space required
Sizing Rule:
~1.3 m³ of make-up water per TPH of steam/day
Space needed for:
Water storage tanks
Pump skid platforms
Chemical dosing systems
4. Blowdown and Drain Systems
Intermittent and continuous blowdown needs:
Blowdown tank or flash vessel
Sewer connection or reuse system
Ensure sloped drain piping and thermal expansion control
5. Power and Control Systems
System | Requirements |
---|---|
Burner management | ATEX-rated panels in explosive environments |
Electrical room | Separate, dust-free, and conditioned |
Cables and PLC systems | Shielded and fire-rated routing |
Emissions and Ventilation Considerations
Stack and Flue Routing
Capacity | Flue Diameter (mm) | Stack Height (m) |
---|---|---|
10 TPH | 500–600 | 15–20 |
50 TPH | 800–1,000 | 25–35 |
100 TPH | 1,200–1,400 | 35–50 |
Must consider:
Draft fans or induced draft (ID) systems
Stack placement relative to building height
Wind load and seismic design
Combustion Air and Ventilation
Large combustion air volumes required:
1–1.2 m³/min of air per kg of fuel
Ventilation system must:
Prevent overheating
Ensure positive pressure zones
Comply with ASME CSD-1, NFPA 85, or EN 12953
Real-World Case: 50 TPH Biomass Boiler Retrofit
Plant Type: Pulp and paper mill
Site Limitations: Low ceiling (6.5 m), weak foundation, no space for silo
Solutions:
Custom skid with lower boiler height
Reinforced slab under boiler footprint
Separate fuel house with automated belt feed
Pipe bridge for steam and water circuits
Result:
Operational within 7 months
Compliant with air and safety codes
22-year projected lifecycle with modular ash handling
Planning Guidelines for High-Capacity Installations
Constraint | Planning Action |
---|---|
Confined footprint | Consider vertical boiler design or adjacent boiler house |
Poor structural support | Add concrete slab or isolated platform foundation |
Limited stack height | Use flue gas treatment + fan-assisted stack |
Fuel delivery space shortage | Relocate tanks or silos outdoors with weatherproofing |
High moisture in room | Install dehumidifiers and insulation |
Summary
High-capacity boilers bring with them significant physical and infrastructure constraints that go far beyond just floor space. They require careful planning of clearances, structural loads, flue systems, utilities, and access zones. Whether installing a 20 TPH unit or a 100 TPH powerhouse, success depends on the integration of architectural, mechanical, and electrical planning. When designed correctly, your boiler system becomes not only high-performing—but also safe, maintainable, and future-ready.
🔍 Conclusion
Sizing an industrial power plant boiler is a complex engineering task that must align with your turbine system, fuel source, process requirements, and long-term energy goals. A correctly sized boiler delivers maximum efficiency, stable power output, and low operating costs, while minimizing the risk of energy waste or equipment damage. Always base your sizing decision on comprehensive thermal analysis and performance modeling tailored to your specific plant conditions.
📞 Contact Us
💡 Need expert assistance with boiler sizing for your power plant project? Our engineering team specializes in customized boiler design, capacity calculation, and full system integration for power generation applications.
🔹 Contact us today for a professional consultation and unlock the full potential of your power plant boiler system! ⚡🔥📊
FAQ
How is the capacity of an industrial power plant boiler calculated?
Boiler capacity is based on the amount of steam or thermal energy required for power generation. It’s typically measured in tons per hour (TPH) for steam or in megawatts (MW) for thermal output, depending on plant size and energy demand.
What is the typical capacity range for power plant boilers?
Industrial power plant boilers range from 20 TPH to over 800 TPH for steam generation, and from 10 MW to 500+ MW for thermal power output, depending on the type of fuel and electricity production scale.
What factors influence power plant boiler sizing?
Key factors include desired steam output, operating pressure and temperature, fuel type and calorific value, plant load profile, redundancy requirements, and efficiency targets. Environmental compliance and fuel flexibility also affect sizing decisions.
Why is correct sizing critical for power plant boilers?
Oversized boilers increase capital and operational costs, while undersized boilers fail to meet power demands, causing inefficiencies and outages. Proper sizing ensures optimal performance, fuel savings, and regulatory compliance.
Can power plant boilers be customized for specific industrial needs?
Yes, boilers are often custom-engineered to meet the plant’s unique steam conditions, fuel supply, site limitations, and emission standards. Options like supercritical or subcritical designs are selected based on efficiency goals.
References
Boiler Sizing for Power Generation – https://www.energy.gov
Steam Boiler Capacity and Design Guide – https://www.sciencedirect.com
Power Plant Steam Demand Calculations – https://www.researchgate.net
Fuel Type & Boiler Output Relationship – https://www.bioenergyconsult.com
Thermal Efficiency in Power Plant Boilers – https://www.epa.gov
Industrial Boiler Load Matching – https://www.mdpi.com
Boiler Sizing and Emission Control – https://www.energysavingtrust.org.uk
Supercritical Boiler Design – https://www.iea.org
Customized Power Plant Boiler Solutions – https://www.automation.com
Large-Scale Boiler Design for Power Plants – https://www.sciencedirect.com
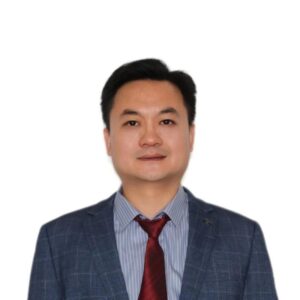