When choosing a boiler system for industrial heating or steam generation, businesses often weigh options like coal-fired, gas-fired, and electric systems. However, traditional boiler types can suffer from limited fuel flexibility, higher emissions, and complex maintenance requirements. For facilities without access to natural gas or in need of high energy density fuels, industrial oil-fired boilers offer a powerful alternative. Understanding their key advantages over traditional boilers is essential for industries seeking efficiency, flexibility, and reliability.
The main advantages of an industrial oil-fired boiler over traditional boilers include higher thermal efficiency, greater fuel energy density, cleaner combustion compared to coal, quicker startup times, and more compact system design. Oil-fired boilers are also easier to install in remote areas, offer better control over combustion, and require less ash handling compared to coal-fired systems. These features make them an ideal choice for industries with demanding steam or heat requirements but limited fuel supply options.
To help industries make informed decisions, let’s explore the key benefits of oil-fired boilers and how they compare with traditional systems.
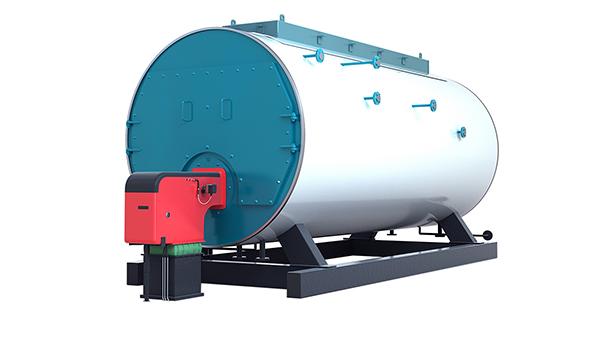
How does an oil-fired boiler achieve higher thermal efficiency than traditional boilers?
In industrial operations where steam and heat are essential, boiler thermal efficiency plays a pivotal role in reducing fuel costs, minimizing emissions, and ensuring consistent output. Traditional boilers—especially those using solid fuels or outdated control methods—often suffer from high heat losses, inefficient combustion, and slow thermal response. By contrast, modern oil-fired boilers are designed with advanced burners, optimized heat exchangers, and precise control systems that collectively enhance combustion and heat recovery, resulting in superior thermal efficiency. But what makes these boilers more efficient than their traditional counterparts?
An oil-fired boiler achieves higher thermal efficiency than traditional boilers by employing optimized atomizing burners for complete fuel combustion, incorporating economizers to recover flue gas heat, maintaining precise air-to-fuel ratios via control systems, and using compact, high-surface-area heat exchangers for maximum energy transfer. This combination reduces flue gas heat loss, enhances combustion stability, and ensures that a greater portion of fuel energy is converted into usable steam or hot water—typically resulting in boiler efficiencies of 88–94%, compared to 70–85% in conventional boilers.
These improvements make oil-fired boilers ideal for applications requiring consistent high-temperature output, low maintenance, and compliance with modern energy and environmental standards.
Key Factors That Enhance Efficiency in Oil-Fired Boilers
Efficiency Factor | How It Works | Resulting Benefit |
---|---|---|
High-performance burner | Atomizes fuel for complete and rapid combustion | Minimizes unburned fuel and CO emissions |
Accurate air-fuel ratio control | Uses sensors and servos to regulate combustion air | Reduces excess air and associated heat loss |
Heat recovery (economizer) | Recovers flue gas heat to preheat feedwater | Lowers fuel consumption and stack temperature |
Condensing capability | Captures latent heat in flue gases in low-temp systems | Boosts efficiency up to 94% |
Optimized boiler geometry | Compact combustion chamber and efficient flow paths | Improves heat transfer to working fluid |
Combustion Efficiency: The Role of Atomization
Oil-fired boilers use pressure jet or rotary cup burners to atomize fuel oil into fine droplets, ensuring better mixing with combustion air.
Feature | Impact on Efficiency |
---|---|
Fine droplet formation | Increases surface area for combustion |
Uniform fuel-air mixing | Leads to more complete combustion |
Stable flame profile | Minimizes flame impingement and heat loss |
Low turndown ratio (as low as 3:1) | Allows efficient operation at varying loads |
Combustion efficiency in modern oil-fired boilers often exceeds 99%, with flue gas O₂ levels maintained at 3–5%, compared to >8% in many older systems.
Heat Transfer Optimization
The combustion chamber, convection tubes, and heat exchangers in modern oil-fired boilers are engineered for maximum surface area exposure and optimal flow velocity.
Component | Design Feature | Benefit |
---|---|---|
Furnace | Large radiant surface | Captures most combustion heat |
Fire-tube or water-tube bundle | Maximized surface area and turbulence | Improves convection heat transfer |
Economizer | Located in flue gas path | Recovers residual heat for feedwater preheating |
Condenser (if applicable) | Cools flue gas below dew point | Recovers latent heat |
Use of Economizers
An economizer is critical for boosting boiler efficiency by 3–7% by capturing sensible heat from exhaust gases. It preheats feedwater entering the boiler, reducing the thermal input needed to reach steam generation temperatures.
Metric | Value |
---|---|
Flue gas inlet temp | 250–350°C |
Feedwater outlet temp | 100–140°C |
Energy savings (fuel) | 3–7% |
Typical boiler efficiency gain | 2–4 percentage points |
Emission Reduction and Fuel Economy
Modern oil-fired boilers achieve lower emissions and higher energy conversion due to controlled combustion and efficient heat recovery.
Comparison Metric | Traditional Boiler | Modern Oil-Fired Boiler |
---|---|---|
Boiler Efficiency | 70–85% | 88–94% |
Excess Air (% O₂) | >8% | 3–5% |
Stack Temperature | >250°C | 140–180°C (or lower) |
CO Emissions | >200 ppm | <50 ppm |
Unburned Fuel Loss | 2–4% | <1% |
Advanced Control Systems and Automation
Digital controllers, oxygen trim systems, and remote monitoring features help maintain real-time combustion optimization.
Control Feature | Efficiency Benefit |
---|---|
O₂ sensors with trim control | Maintain ideal air-fuel ratio |
Modulating burner control | Adjusts firing rate with load demand |
Boiler sequencing | Operates multiple boilers based on demand |
Remote diagnostics and alerts | Prevents efficiency drop due to faults |
These controls prevent overshooting, cycling losses, and ensure efficient turndown at partial loads.
Case Study: 10 TPH Industrial Oil-Fired Boiler Upgrade
A textile plant upgraded from a 20-year-old fire-tube boiler (81% efficiency) to a modern three-pass oil-fired boiler with economizer and electronic controls.
Results:
Boiler efficiency increased to 92.4%
Annual fuel savings: ~58,000 liters
CO₂ emissions reduced by ~150 tons/year
Payback period: 18 months
Thermal Efficiency Enhancement Summary
Feature | Efficiency Contribution |
---|---|
Complete combustion | +2–3% |
Economizer heat recovery | +3–5% |
Air-fuel ratio control | +1–2% |
Lower stack loss | +2–4% |
Condensing heat recovery (optional) | +5–7% (only in low-temp systems) |
Final Thoughts
Modern oil-fired boilers are engineered for thermal precision and energy optimization. Through efficient atomization, controlled combustion, and strategic heat recovery, they far outperform traditional boilers in terms of fuel economy, emissions, and reliability. For facilities aiming to reduce operational costs while ensuring regulatory compliance and process consistency, upgrading to a high-efficiency oil-fired boiler is a smart and impactful investment.
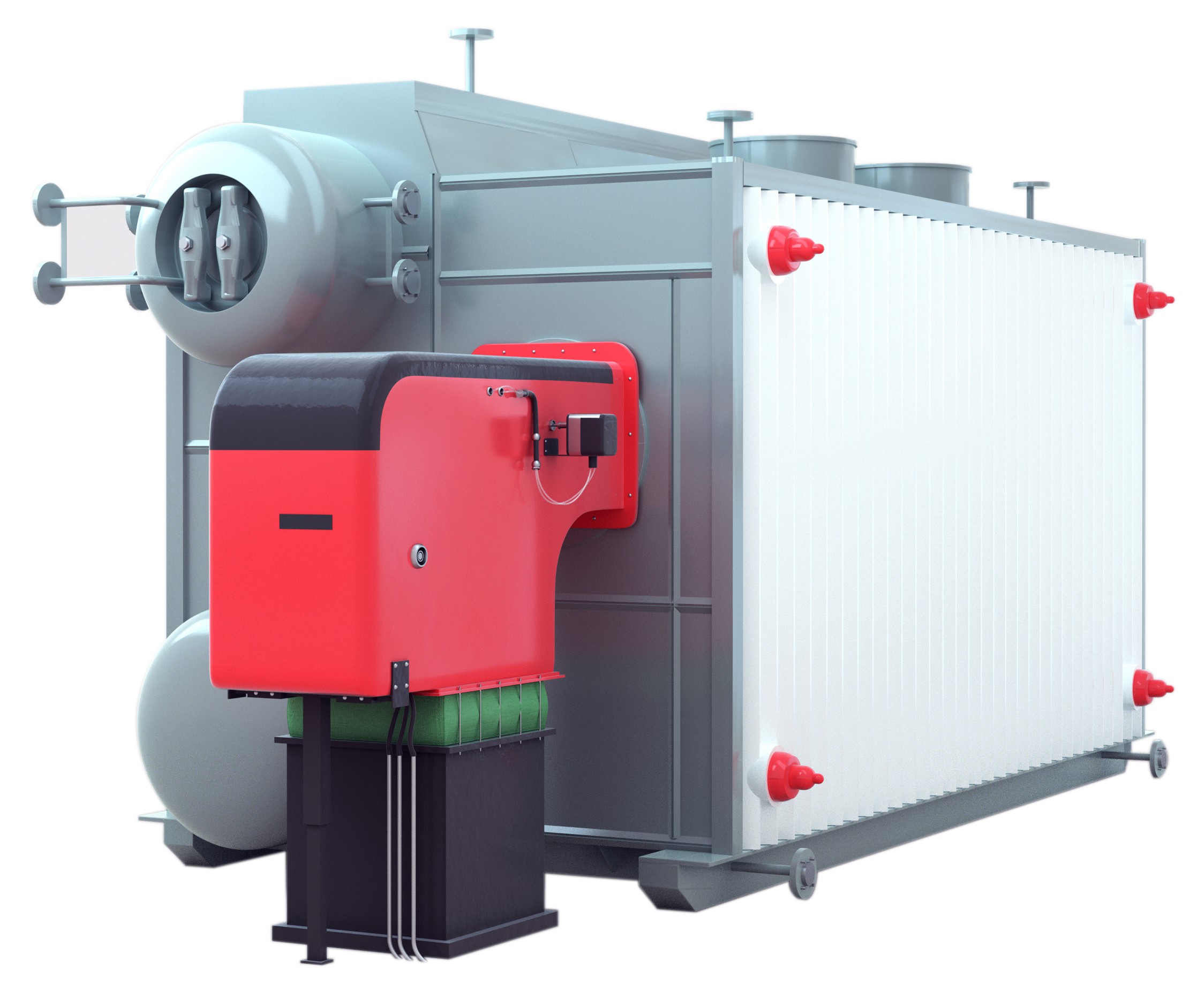
What makes fuel oil more energy-dense and transportable than other fuels?
When selecting a fuel for industrial boilers or energy systems, two key factors come into play: energy density and logistical practicality. While solid fuels like coal and biomass are bulky and less uniform, and gaseous fuels like natural gas require pressurized systems or pipelines, fuel oil offers a balanced solution—high in energy per unit volume and easy to store, handle, and transport. These properties have made fuel oil a preferred energy source for sectors needing mobile, reliable, and compact energy solutions.
Fuel oil is more energy-dense and transportable than other fuels because it contains a high concentration of hydrocarbons in a compact liquid form, offering 42–45 MJ/kg of energy, and up to 38–40 MJ/liter in volumetric terms. Its liquid state at ambient temperatures enables easy pumping, storage in tanks, and bulk transport by rail, road, or ship without the need for pressurization or specialized infrastructure. This combination of high calorific value, flowability, and logistical flexibility makes fuel oil exceptionally efficient and practical for industrial and remote energy applications.
From powering thermal power plants to being the go-to backup fuel in critical operations, fuel oil’s physical and chemical advantages translate into real-world operational and economic benefits.
Energy Density: Mass and Volume Comparison
Fuel oil’s energy density surpasses most solid and gaseous fuels when measured by both weight and volume.
Table: Energy Density Comparison by Fuel Type
Fuel Type | Energy per kg (MJ/kg) | Energy per liter (MJ/liter) | State |
---|---|---|---|
Fuel Oil (No. 2, No. 6) | 42–45 | 38–40 | Liquid |
Natural Gas | ~55 | ~0.037 (at STP) | Gas |
Coal (bituminous) | 24–30 | ~18–20 | Solid |
Wood (dry) | 15–18 | ~7–9 | Solid |
Propane | 46 | ~25 | Gas (liquid under pressure) |
Diesel | 43 | ~36 | Liquid |
Fuel oil offers nearly double the volumetric energy density of propane and more than four times that of wood, making it ideal for space-limited applications.
Why Fuel Oil Is More Energy-Dense
Fuel oil is derived from crude oil via fractional distillation and contains:
Long-chain hydrocarbons (C10–C20+)
High hydrogen-to-carbon ratios
Low moisture and inert content
These attributes contribute to:
Property | Effect on Energy Density |
---|---|
Low oxygen/moisture | No dilution of calorific content |
Hydrocarbon saturation | High enthalpy release during combustion |
Liquid-phase compactness | More mass per unit volume compared to solids |
Transportability Advantages
Unlike natural gas, which requires pipeline infrastructure or high-pressure containers, and coal, which requires bulky handling and loading systems, fuel oil is:
Easily pumpable through pipelines, hoses, and meters
Storable in above-ground or underground tanks
Shippable via road tankers, rail cars, barges, and sea-going vessels
Infrastructure Requirements Comparison
Fuel | Transport Medium | Onsite Storage | Delivery Flexibility |
---|---|---|---|
Fuel Oil | Tankers, pipelines | Steel tanks | High (anywhere accessible) |
Natural Gas | Pipelines, LNG trucks | Pressurized tanks | Limited to gas grid or special setup |
Coal | Rail cars, trucks, barges | Silos, bunkers | Requires heavy equipment |
Biomass Pellets | Bulk carriers, trucks | Sheds, silos | Subject to spoilage, lower density |
Fuel oil can be metered, preheated, and automated for continuous supply with minimal manual handling, making it suitable for automation and remote locations.
Flowability and Storage Behavior
Characteristic | Advantage in Transport and Use |
---|---|
Liquid at ambient temp | No special pressurization required |
Low vapor pressure | Safer handling, less evaporative loss |
Viscosity manageable | Can be pumped with standard or heated systems |
Long shelf life | Stable for extended storage (esp. heavy oils) |
Fuel oils like No. 2 (diesel-like) or No. 6 (heavy) vary in viscosity, but all can be pumped, measured, and burned using industrial burner systems with preheating.
Use in Industrial and Mobile Energy Systems
Because of its energy density and portability, fuel oil is widely used in:
Backup power systems (hospitals, data centers, airports)
Remote industrial boilers (mines, isolated plants)
Ships and marine engines (heavy fuel oil in slow-speed diesels)
Oil-fired power stations (where natural gas is unavailable)
Real-World Example: Fuel Oil vs. Coal in Remote Boiler
A remote textile plant in northern Africa replaced a coal-fired boiler with an oil-fired system due to:
Fuel oil’s compact storage requirement
Simplified supply chain via truck deliveries
Cleaner combustion and reduced ash disposal
Result:
Reduced fuel storage footprint by 70%
Cut fuel delivery frequency in half
Improved boiler start-up times and load response
Emissions and Combustion Performance
Fuel oil, when burned with proper controls, produces:
Lower particulate emissions than coal
Less ash handling and residue
Moderate NOx and SOx (which can be managed with control systems)
Cleaner variants like low-sulfur fuel oil (LSFO) or ultra-low sulfur heating oil (ULSHO) are now commonly available to reduce environmental impact.
Summary: What Sets Fuel Oil Apart
Property | Fuel Oil Advantage |
---|---|
Energy per liter | Very high (up to 40 MJ/liter) |
Transportability | No pressure or special container required |
Storage ease | Long-term tank storage without degradation |
Combustion control | Stable flame, high thermal response |
Infrastructure simplicity | Easy to implement in off-grid or mobile systems |
Fuel oil’s high energy content, liquid phase, and ease of transport make it a uniquely efficient and versatile fuel—especially in scenarios where grid gas is unavailable, logistics are challenging, or uninterrupted high-output energy is essential.
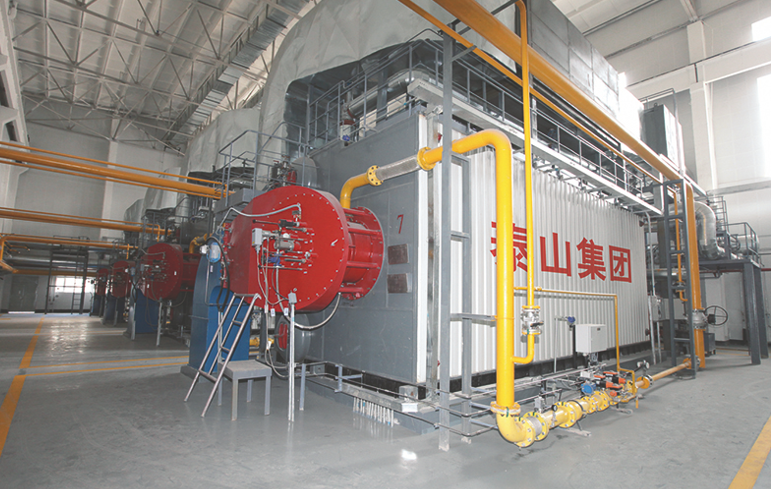
How do oil-fired boilers compare to coal-fired boilers in terms of emissions and maintenance?
As environmental regulations tighten and industries seek cleaner, more efficient energy sources, the choice between oil-fired and coal-fired boilers becomes increasingly critical. While both systems serve the same function—generating steam or hot water for industrial processes—their emission profiles and maintenance requirements differ significantly. Choosing the wrong system can lead to increased operational downtime, excessive environmental compliance costs, or even regulatory penalties. This article offers a detailed technical comparison between these two boiler types, helping stakeholders make informed decisions based on environmental impact and operational demands.
Oil-fired boilers produce significantly lower emissions and require less intensive maintenance compared to coal-fired boilers. Emissions such as particulate matter, sulfur dioxide (SO₂), and ash are substantially reduced due to the cleaner-burning nature of fuel oil. Maintenance is also simplified, as oil combustion produces no solid residues like slag or bottom ash, eliminating the need for mechanical ash handling systems, soot blowers, and frequent shutdowns for cleaning. This makes oil-fired boilers more environmentally friendly and operationally efficient, particularly in regions with strict emissions standards.
This fundamental difference stems from the physical and chemical properties of the fuels themselves and how they combust within the boiler.
Emission Profile Comparison
Emission Type | Coal-Fired Boiler | Oil-Fired Boiler |
---|---|---|
Particulate Matter (PM) | High (fly ash, soot) | Low (minimal soot with clean-burning oils) |
Sulfur Dioxide (SO₂) | High, depending on coal sulfur content | Moderate to low (depending on fuel grade) |
Nitrogen Oxides (NOx) | Moderate to high (thermal + fuel NOx) | Moderate (can be managed with low-NOx burners) |
Carbon Monoxide (CO) | Can spike during incomplete combustion | Typically lower due to more complete combustion |
Carbon Dioxide (CO₂) | High (due to carbon-heavy solid fuel) | Slightly lower for equivalent output |
Heavy Metals | May include mercury, arsenic, etc. | Generally negligible |
Graph: SO₂ and PM Emissions (g/GJ Energy Output)
Emission (g/GJ)
|
| Coal Oil
| SO₂ ██████ ███
| PM █████ █
| NOx █████ ███
| CO ██ █
Coal combustion emits 10–20 times more particulates than oil.
Sulfur emissions are heavily dependent on coal origin; oil can be filtered/refined for low sulfur levels (e.g., LSFO or ULSHO).
Maintenance Requirements Comparison
Maintenance Task | Coal-Fired Boiler | Oil-Fired Boiler |
---|---|---|
Ash Handling | Requires bottom ash and fly ash systems | None (no solid combustion residue) |
Soot Blowing | Required frequently (daily or weekly) | Rarely needed (only with heavy oil) |
Grate or Bed Maintenance | Frequent cleaning or replacement | Not applicable |
Tube Fouling & Cleaning | High due to slag and ash deposition | Low (minimal deposit formation) |
Burner Maintenance | Mechanical wear due to solid fuel feed | Less mechanical complexity |
Emission Control Systems | ESPs, baghouses, FGD scrubbers | Simpler systems or none needed |
Coal-fired systems are inherently more complex, requiring multiple auxiliary systems for ash, fuel feeding, and emissions mitigation.
Boiler Design and Lifecycle Implications
Feature | Coal-Fired Boiler | Oil-Fired Boiler |
---|---|---|
Startup Time | Slower (requires bed heating, drying) | Faster (liquid fuel ignites easily) |
Footprint | Larger due to auxiliary equipment | More compact |
Thermal Response Time | Slower | Faster load-following ability |
System Complexity | High (multiple sub-systems) | Lower complexity |
Operational Downtime | Higher due to slagging, ash handling | Lower (clean combustion, fewer shutdowns) |
Maintenance Cost (annual) | High (labor-intensive) | Lower (automated and cleaner systems) |
Environmental Compliance and Fuel Flexibility
Coal-Fired Boilers
Require electrostatic precipitators (ESP), flue gas desulfurization (FGD) units, and selective catalytic reduction (SCR) for full environmental compliance.
Must manage ash disposal, often subject to landfill regulations.
Susceptible to fuel quality variability, impacting emissions and maintenance.
Oil-Fired Boilers
Use low-NOx burners and oxygen trim controls for emissions reduction.
Can switch between standard, low-sulfur, or ultra-low sulfur oils to meet local air quality laws.
Easier to upgrade for biofuel compatibility or dual-fuel operation (e.g., gas and oil).
Real-World Case Study: Hospital Boiler Room Conversion
A 600-bed hospital in Germany converted from a 3 MW coal-fired boiler to a 2.8 MW oil-fired condensing boiler system:
Metric | Before (Coal) | After (Oil) |
---|---|---|
Boiler Efficiency | 76% | 91% |
Particulate Emissions | 120 mg/Nm³ | <15 mg/Nm³ |
Annual Maintenance Downtime | 22 days/year | 6 days/year |
Fuel Storage and Handling Cost | High (manual and mechanized) | Moderate (automated pumping) |
Operator Labor Demand | 3 full-time technicians | 1 part-time operator |
Result: A 40% drop in maintenance costs and 30% reduction in total emissions, while achieving improved load response for variable hospital steam demand.
Summary: Oil vs. Coal Boilers at a Glance
Criteria | Oil-Fired Boiler | Coal-Fired Boiler |
---|---|---|
Emissions (PM, SO₂, CO) | Lower | Higher |
Ash Generation | None | Significant (requires handling systems) |
Maintenance Intensity | Low | High |
Fuel Handling Complexity | Simple (liquid pumping) | Complex (solid feed, crushers, conveyors) |
Environmental Compliance | Easier | Requires extensive emission controls |
Operational Flexibility | High (good for load variation) | Moderate to low |
Upfront Capital Cost | Moderate | Higher due to auxiliary systems |
Oil-fired boilers present a cleaner, lower-maintenance, and more regulation-friendly solution for industrial users compared to coal-fired units. As industries shift toward decarbonization and automation, oil-fired systems offer a transitional advantage—especially when natural gas is unavailable or unreliable.
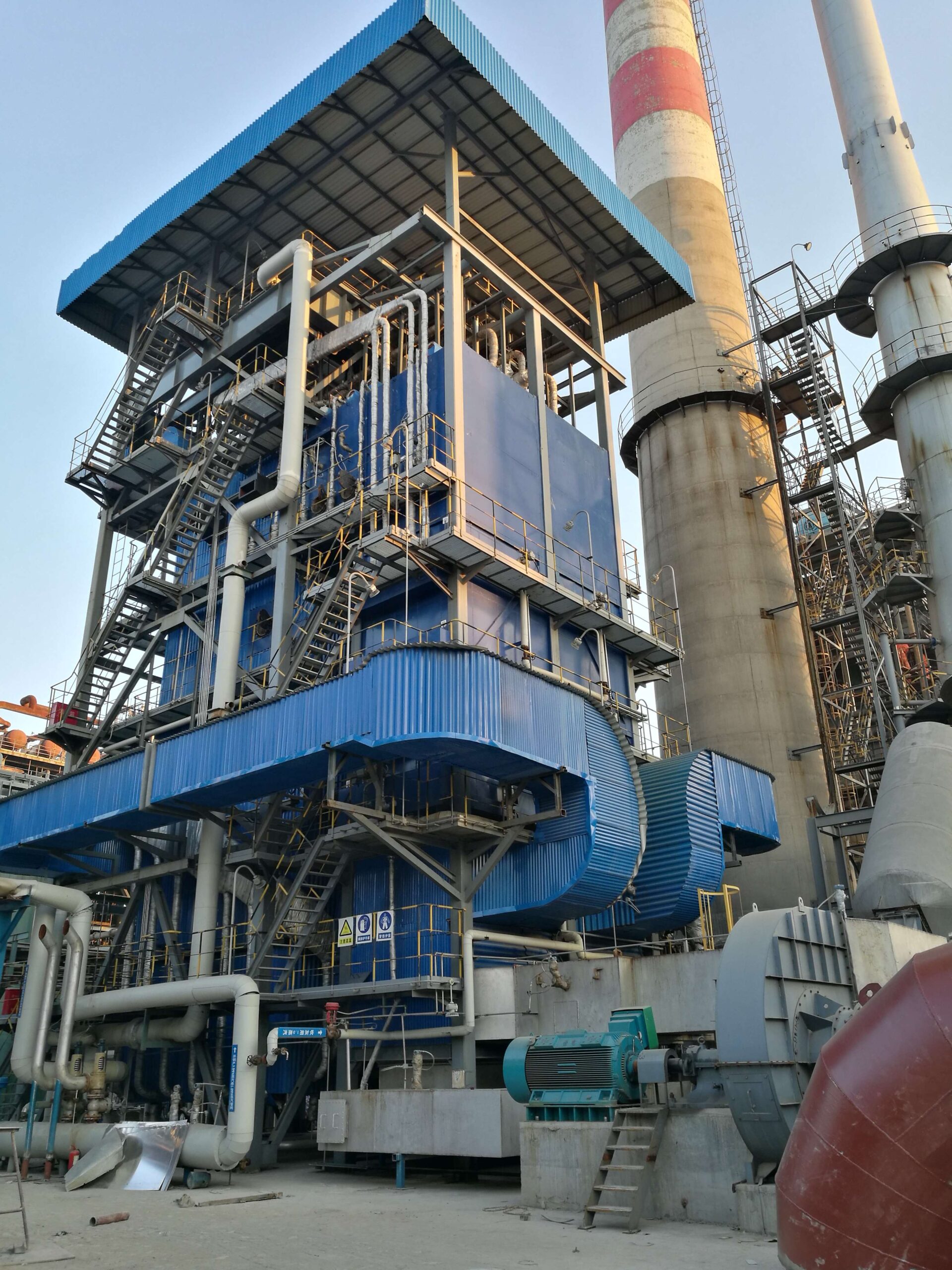
Why are oil-fired systems more suitable for remote or off-grid industrial applications?
Operating industrial facilities in remote or off-grid locations poses unique challenges—especially when it comes to energy supply, infrastructure availability, and operational reliability. In such environments, choosing the right boiler or heating system can mean the difference between continuous productivity and costly downtimes. Traditional solid fuel systems like coal or biomass often require extensive support infrastructure and labor, while gaseous fuels like natural gas depend on grid connections or complex storage methods. Oil-fired systems, on the other hand, are self-contained, highly energy-dense, and easy to deploy, making them ideal for isolated or infrastructure-scarce environments.
Oil-fired systems are more suitable for remote or off-grid industrial applications because they offer high energy density in a portable liquid form, require minimal on-site infrastructure, and are capable of operating independently of fuel grids or complex handling systems. With simplified logistics, fast start-up times, automated controls, and low maintenance requirements, oil-fired boilers provide a reliable and scalable solution for remote industries like mining, construction, remote manufacturing, agriculture, and military bases.
Their versatility, coupled with long fuel storage life and adaptability to harsh climates, gives oil-fired systems a logistical and operational edge over other boiler technologies in off-grid scenarios.
Key Reasons Oil-Fired Systems Excel in Remote Locations
Advantage | Why It Matters in Remote Applications |
---|---|
High Energy Density | Allows longer operation with less fuel volume |
Liquid Fuel Transportability | Easily delivered by trucks, rail, or ship to any location |
No Need for Fuel Grid Access | Independent of natural gas pipelines or electrical grids |
Compact Infrastructure | No need for coal yards, crushers, or gas compression |
Fast Installation and Setup | Skid-mounted or modular options deploy quickly |
Ease of Automation | Remote control and monitoring possible |
Reliable Operation in Harsh Climates | Performs well in cold or hot environments |
Flexible Load Response | Adapts to changing industrial demand with ease |
Energy Density and Fuel Logistics
Oil-based fuels like No. 2 and No. 6 fuel oil contain 38–40 MJ per liter, far exceeding the volumetric energy content of coal, wood, or compressed gases. This high energy density translates to:
Smaller storage footprint
Longer runtime per delivery
Fewer refueling trips, saving logistics cost
Fuel Type | Energy per Liter (MJ/l) | Storage Complexity | Transport Method |
---|---|---|---|
Fuel Oil | 38–40 | Simple tank | Tanker truck, ISO container |
Diesel | ~36 | Simple tank | Truck or barge |
Propane (LPG) | ~25 | Pressurized tank | Cylinder or bulk tank |
Coal | ~18 | Large yard or silo | Railcar or barge |
Biomass | ~7–10 | Bulky storage | Truck with material handling |
Remote facilities typically set up above-ground double-walled tanks or underground fuel storage, often with enough capacity for weeks or even months of autonomous operation.
Operational Independence and Reliability
Oil-fired systems can be run in standalone configurations, often featuring:
Integral fuel pumping and preheating
Built-in safety shutdowns and controls
Onboard diagnostics and alarm systems
Generator synchronization (for co-gen applications)
These features enable round-the-clock operation without local grid support—ideal for:
Mining sites in deserts, tundra, or jungles
Construction sites with temporary facilities
Remote power generation for camps, labs, or hospitals
Maintenance Simplicity and Low Labor Demand
Unlike coal systems (which need ash handling, grate cleaning, and fuel feeding systems), oil-fired boilers:
Produce no solid waste or bottom ash
Require minimal soot cleaning (especially with clean-burning fuel oils)
Include fully automated burners with high turndown ratios
Use standard piping and metering for fuel management
Maintenance Task | Coal-Fired Boiler | Oil-Fired Boiler |
---|---|---|
Ash Removal | Daily/weekly | None |
Fuel Feed Maintenance | Mechanical systems | Simple pumps and filters |
Soot Blowing | Regular | Occasional (low soot) |
Staff Needed | 2–3 operators/shift | 1 operator or remote-only |
This simplicity allows oil-fired systems to run with minimal staff—crucial in remote regions where skilled labor is scarce or expensive.
Compatibility with Auxiliary Power and Renewables
Oil-fired boilers can integrate seamlessly with:
Diesel generators for hybrid heat-and-power systems
Solar heating or thermal storage systems for efficiency gains
Remote monitoring platforms for real-time control via satellite or cellular
They can also function as backup systems in off-grid microgrids, ensuring uninterrupted thermal energy during periods of solar or wind intermittency.
Real-World Example: Oil-Fired Boiler in Arctic Mining Camp
A mining company operating in the Arctic used dual 1.5 MW oil-fired boilers to provide heating and process steam.
Challenges addressed:
No grid connection within 300 km
Extreme cold (−40°C)
Unstable supply of coal and wood pellets
System Design:
100,000-liter fuel oil tank with delivery by winter ice road
Fully enclosed boiler container with remote access
Integrated backup generator system
Results:
Achieved >90% efficiency even in subzero conditions
Operated autonomously for 3 months without onsite intervention
Reduced logistical burden by 50% compared to previous biomass system
Summary: Why Oil-Fired Systems Are Ideal for Remote Industry
Performance Factor | Oil-Fired System Advantage |
---|---|
Fuel Availability | Transportable anywhere by standard means |
Energy Density | Long runtime with compact fuel storage |
Startup and Response | Fast ignition, excellent load-following |
Infrastructure Needs | Minimal (no grid, conveyors, or ash systems) |
Automation Compatibility | Easily integrated with SCADA or remote control platforms |
Environmental Control | Cleaner than coal/biomass with manageable emissions |
Oil-fired boiler systems provide a robust, scalable, and efficient heating solution for off-grid industries. Their ability to operate independently with minimal infrastructure and labor makes them especially well-suited for remote locations where uptime, fuel flexibility, and deployment speed are mission-critical.
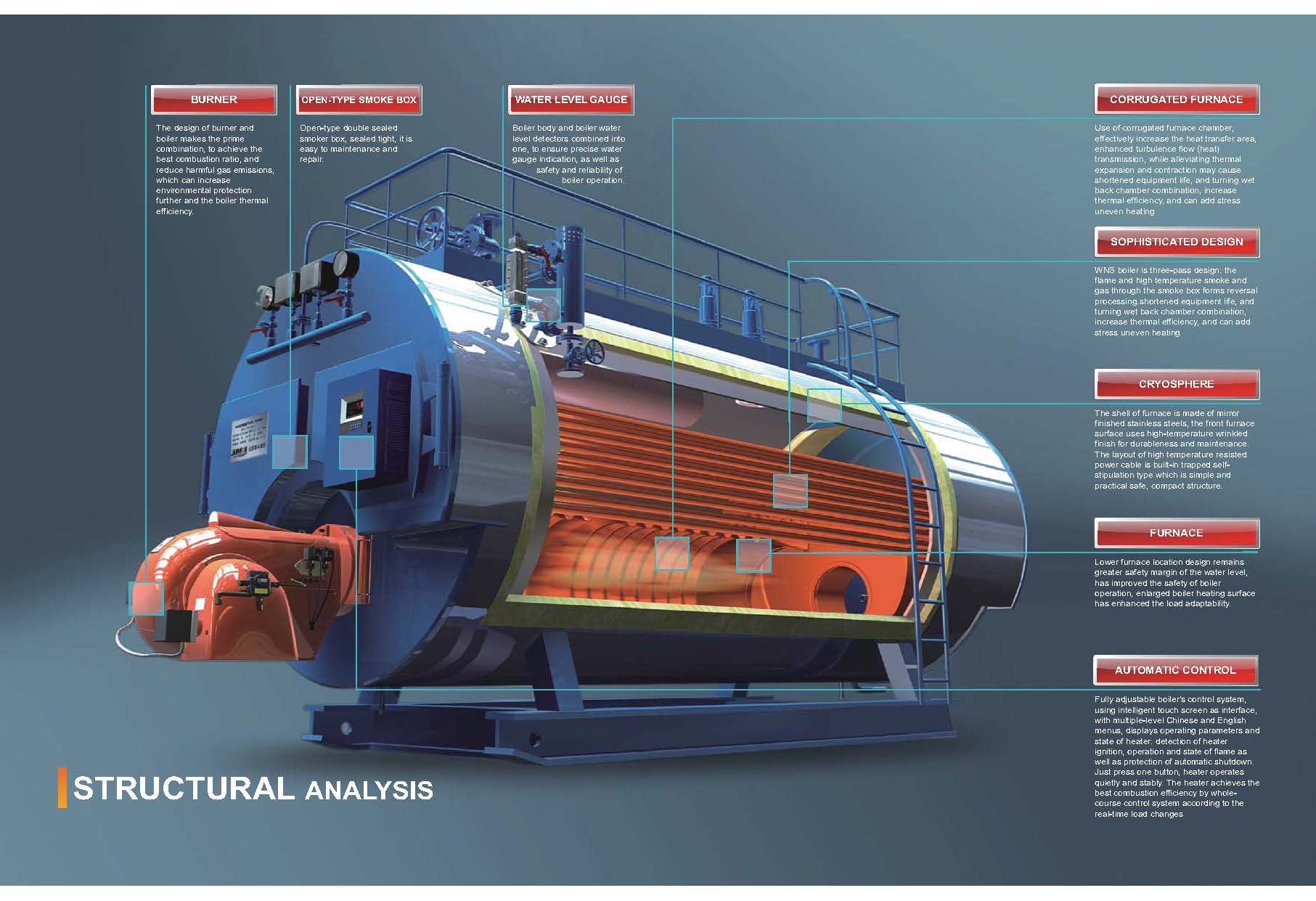
What advantages do oil-fired boilers offer in terms of startup speed and operational control?
In industries where thermal energy is integral to operations—such as manufacturing, food processing, power generation, or remote facilities—the ability to start a boiler quickly and control its output accurately is vital. Delays in startup or inability to match demand fluctuations can result in lost productivity, fuel waste, and process inefficiencies. Compared to traditional solid fuel systems like coal or biomass, oil-fired boilers deliver superior responsiveness, streamlined startup procedures, and precise modulation—making them ideal for operations requiring flexibility, automation, and rapid thermal output.
Oil-fired boilers offer significant advantages in startup speed and operational control due to their ability to ignite quickly, modulate burner output efficiently, and integrate with modern automation systems. These systems can reach full operating pressure within 10–30 minutes, feature high turndown ratios for precise load matching, and maintain consistent steam or hot water delivery with minimal operator intervention. Their fast response and control flexibility make them ideal for dynamic industrial processes, standby applications, and energy systems with variable demands.
This quick-start capability and automated load adaptation reduce downtime, save fuel, and improve system reliability—especially where thermal demand fluctuates or fast recovery is essential.
Fast Startup Capability: How and Why It Matters
Startup Stage | Oil-Fired Boiler Advantage |
---|---|
Fuel Ignition | Liquid fuel atomizes and ignites instantly |
Boiler Warm-Up | Efficient radiant and convective heat transfer |
Steam Pressure Buildup | Rapid heat generation with minimal thermal lag |
Automation Integration | Programmable preheat and purge cycles for safe startup |
Oil-fired boilers use pressure jet or rotary burners that can ignite in seconds and ramp up to full output quickly. Unlike coal or biomass systems that require bed preheating, solid fuel feeding, and ash clearing, oil systems are:
Self-priming with integral fuel pumps
Equipped with electronic ignition systems
Pre-configured for automated startup sequences
Typical Startup Times
Boiler Type | Cold Start (minutes) | Warm Start (minutes) |
---|---|---|
Oil-Fired Boiler | 15–30 | 5–15 |
Gas-Fired Boiler | 10–20 | 5–10 |
Coal-Fired Boiler | 90–180 | 45–60 |
Biomass Boiler | 60–120 | 30–45 |
Fast startup is especially critical in:
Backup steam systems for hospitals or data centers
Batch processing industries with intermittent steam needs
District heating that follows daily load profiles
Advanced Operational Control: Precise and Responsive
Oil-fired systems excel in modulation and turndown control, which enables them to adjust thermal output based on real-time demand.
Key Features Enabling Control:
Feature | Benefit |
---|---|
High Turndown Ratio (up to 10:1) | Maintains efficiency across wide load range |
Modulating Burners | Adjust flame size and heat output without cycling |
O₂ Trim Systems | Keeps combustion optimized for different load levels |
PID Control Loops | Regulates steam pressure, temperature, and feedwater |
Remote Monitoring/SCADA Integration | Enables offsite control and fault diagnostics |
Example: Turndown Ratio Comparison
Boiler Type | Typical Turndown Ratio |
---|---|
Oil-Fired | 5:1 to 10:1 |
Gas-Fired | 10:1 or higher |
Coal-Fired | 2:1 to 4:1 |
Biomass | 1.5:1 to 3:1 |
High turndown minimizes on-off cycling, which in turn:
Reduces thermal stress
Prolongs component life
Lowers fuel consumption
Consistent Output and Load Matching
Oil-fired boilers can adjust seamlessly to variable steam or hot water demands—making them suitable for:
Process heating
Textile and dyeing operations
Sterilization systems
Greenhouses and climate control
With real-time sensor feedback, the control system regulates:
Fuel flow rate
Combustion air
Steam or water temperature
Pressure setpoints
The result is stable energy delivery even under load fluctuations.
Integration with Smart Control Systems
Modern oil-fired boilers support full integration with:
DCS (Distributed Control Systems)
PLC-based controllers
SCADA platforms
IoT-based monitoring dashboards
These systems offer:
Automation Function | Benefit |
---|---|
Auto Start/Stop Logic | Schedule-based or demand-based startup |
Alarm and Fault Logging | Improves diagnostics and response times |
Energy Usage Reports | Helps optimize fuel efficiency |
Remote Access Capability | Enables offsite control in remote or critical locations |
Case Example: Pharmaceutical Plant Steam System
A pharmaceutical manufacturer replaced a coal-fired boiler with a 4 TPH oil-fired unit featuring:
High-speed burner
8:1 turndown
PLC-based pressure/temperature controls
Results:
Steam availability reduced from 90 to 20 minutes after shutdown
Steam pressure fluctuation ±0.2 bar (vs. ±1.0 bar before)
Fuel savings of ~12% due to better modulation
Operator time reduced by 50% due to automation
Summary of Startup and Control Advantages
Performance Area | Oil-Fired Boiler Advantage |
---|---|
Startup Speed | Quick ignition and pressure build-up |
Modulation Range | High turndown for precise load matching |
System Responsiveness | Fast thermal response and minimal lag |
Ease of Automation | Seamless integration with modern control systems |
Operational Stability | Consistent output with minimal cycling |
Fuel Flexibility | Switchable between different grades (e.g., LSFO, diesel) |
Oil-fired boilers are an ideal solution for operations where time-to-steam, control precision, and operational agility are key success factors. Whether serving as a primary or backup boiler, their fast and flexible performance reduces downtime, increases process control, and supports modern energy management strategies.
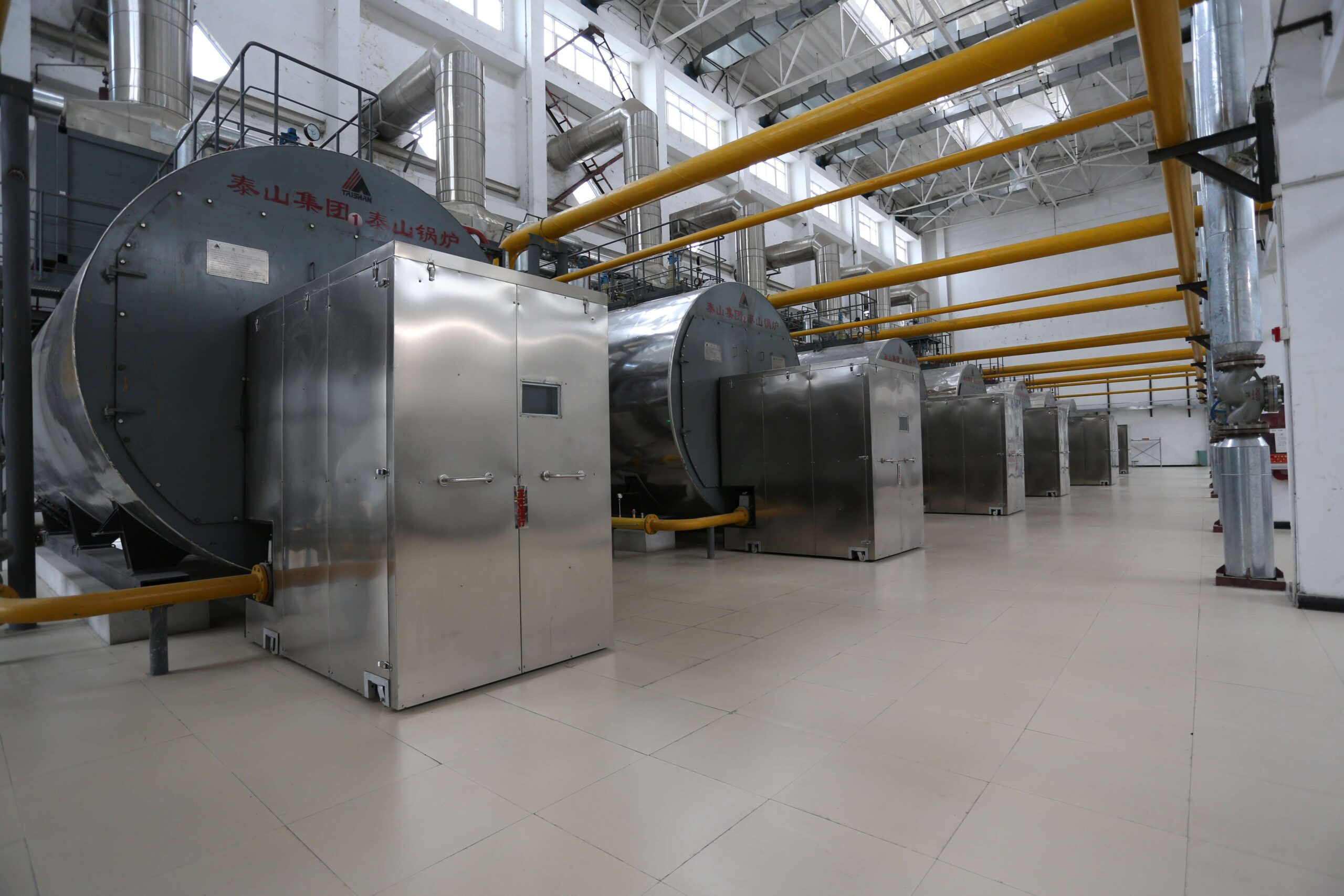
How does the compact design of oil-fired boilers benefit industrial plant layouts?
In industrial settings, every square meter of floor space matters. Whether in food processing, textiles, pharmaceuticals, chemicals, or district heating systems, plant designers and engineers seek equipment that delivers performance without occupying excessive space or requiring costly structural modifications. In this context, oil-fired boilers offer a significant advantage over their solid fuel or gas-fired counterparts: a compact, modular, and self-contained design that simplifies integration, reduces installation time, and optimizes space utilization in both new and retrofit applications.
The compact design of oil-fired boilers benefits industrial plant layouts by minimizing floor space requirements, simplifying system installation, and allowing for flexible positioning of auxiliary components like fuel tanks and control panels. Their modular structure enables easy integration into tight mechanical rooms or process areas without compromising output, and their vertical or horizontal configurations support a range of layout strategies. This space efficiency reduces construction costs, improves workflow circulation, and allows room for future system expansion or added equipment.
In this article, we’ll explore how the physical structure, component arrangement, and design philosophy of oil-fired boilers translate into practical advantages for industrial plant engineering.
Key Features of Compact Oil-Fired Boiler Design
Design Element | Compact Advantage |
---|---|
Horizontal or Vertical Shell | Offers flexible footprint options (long/narrow or tall/compact) |
Integrated Burner and Control Panel | Reduces external space demand and wiring clutter |
No Solid Fuel Handling | Eliminates need for conveyors, hoppers, and ash pits |
Pre-assembled Skid Units | Enables plug-and-play installation in constrained environments |
Modular Auxiliary Placement | External fuel tanks, pumps, and softeners can be repositioned |
Comparison: Space Requirement by Boiler Type
Boiler Type | Approx. Footprint per 1 TPH (tons/hour) of Steam Output |
---|---|
Oil-Fired Boiler | 6–8 m² (single unit + service space) |
Gas-Fired Boiler | 8–10 m² (includes gas piping and safety zones) |
Coal-Fired Boiler | 15–20 m² (requires ash system, fuel yard, air preheater) |
Biomass Boiler | 18–25 m² (includes storage, feeder, and ash handling) |
Oil-fired boilers are often 50–70% smaller in footprint compared to solid fuel boilers of the same capacity.
Installation and Integration Benefits
A. Faster Installation
Compact oil-fired boilers are typically delivered pre-assembled or as modular packages, which include:
Boiler shell
Burner
Control panel
Feedwater system
Pumps and safety valves
This shortens installation time from weeks to days, minimizes field welding and pipe fitting, and simplifies alignment.
B. Flexible Placement
Oil-fired units can be installed:
In basement mechanical rooms
On elevated platforms above process equipment
Inside containerized boiler houses
In rooftop enclosures for high-rise facilities
C. Lightweight and Structural Advantage
Due to the absence of heavy ash handling systems or refractory-lined furnaces, oil-fired boilers weigh less, making them suitable for installation on mezzanines or structural floors with moderate load capacity.
Boiler Type | Weight per MW (approx.) | Structural Load Planning Required |
---|---|---|
Oil-Fired | ~5–7 tons | Low to moderate |
Coal-Fired | 10–20 tons | High (due to heavy base and silos) |
Biomass | 15–25 tons | Very high |
Auxiliary Systems: Separable and Scalable
Unlike solid fuel systems that require centralized storage and handling zones, oil-fired systems allow for decentralized auxiliary equipment, such as:
Component | Placement Flexibility |
---|---|
Fuel Oil Tanks | Underground, outdoor, or rooftop tanks |
Preheaters | Inline or skid-mounted near fuel pumps |
Control Panels | Wall-mounted or integrated on boiler skid |
Water Softeners | Standalone with minimal plumbing distance |
This design flexibility allows project engineers to optimize equipment positioning based on process flow, access needs, or zoning requirements.
Real-World Example: Retrofit in a Pharmaceutical Plant
A pharmaceutical facility in Singapore needed to replace its aging gas-fired boiler within a tight mechanical room footprint.
Challenge:
Only 3 meters of vertical clearance
Limited access for delivery and lifting equipment
Demand for minimum 2 TPH steam output
Solution:
A compact oil-fired horizontal boiler (2.5 TPH capacity) with integrated burner
Preassembled on a steel skid
Installed using a rolling dolly system in 2 days
External LSFO tank placed 15 meters away on outdoor platform
Result:
20% increase in usable floor area
5-hour startup to full operation
30% shorter installation time vs. previous plan for a vertical biomass boiler
Summary: Layout and Engineering Advantages
Benefit Category | Oil-Fired Boiler Contribution |
---|---|
Floor Space Efficiency | Small footprint suits compact or high-cost floor areas |
Installation Flexibility | Horizontal/vertical and modular options support space planning |
Auxiliary System Freedom | Decentralized fuel/storage simplifies mechanical zoning |
Retrofit Compatibility | Replaces older units without major structural modification |
Ease of Maintenance | Better access to burner, control panels, and inspection ports |
Oil-fired boilers offer a powerful mix of thermal performance, automation, and space efficiency. Their compact design enables industrial facilities to optimize floor plans, reduce installation costs, and simplify plant operations—without sacrificing output or safety. For engineers and plant managers, this translates into smarter use of capital, faster deployment, and more room for growth.
🔍 Conclusion
Industrial oil-fired boilers provide a reliable, efficient, and flexible heating solution for facilities that require high thermal performance but may lack access to gas or want to avoid coal’s environmental drawbacks. Their cleaner combustion, faster startup, simplified operation, and higher energy density make them superior to many traditional boiler systems in various industrial scenarios. Understanding these advantages allows businesses to maximize return on investment and reduce operational risks.
📞 Contact Us
💡 Considering an oil-fired boiler for your facility? Our engineering experts can help you compare options and implement the best system for your application, ensuring efficiency, compliance, and cost-effectiveness.
🔹 Contact us today to discover how oil-fired boiler technology can elevate your operations! 🛢🔥
FAQ
What makes industrial oil-fired boilers more efficient than traditional boilers?
Industrial oil-fired boilers are designed with modern burners and heat exchangers that ensure complete combustion and optimal heat transfer, resulting in higher thermal efficiency and reduced fuel consumption compared to older boiler systems.
How do oil-fired boilers provide cleaner combustion?
Oil-fired boilers use advanced burner technology to produce more complete combustion, reducing emissions of smoke, soot, and unburned hydrocarbons compared to traditional coal-fired boilers.
Are oil-fired boilers easier to maintain than older systems?
Yes, modern oil-fired boilers have fewer moving parts, better control systems, and cleaner combustion processes, leading to reduced maintenance needs and longer operational life.
What is the fuel flexibility of oil-fired boilers?
Many industrial oil-fired boilers can operate on various types of fuel oil, such as diesel, kerosene, or heavy fuel oil, offering flexibility depending on availability and cost.
Why are oil-fired boilers suitable for industries without natural gas access?
Oil-fired boilers are an excellent alternative in areas where natural gas infrastructure is unavailable, providing reliable and consistent heating or steam generation without dependency on a gas supply.
References
Benefits of Oil-Fired Boilers – https://www.energy.gov
Efficiency of Modern Boiler Systems – https://www.sciencedirect.com
Oil Boiler Emission Advantages – https://www.epa.gov
Comparison of Boiler Types – https://www.researchgate.net
Oil-Fired Boiler Maintenance Guide – https://www.bioenergyconsult.com
Industrial Heating with Fuel Oil – https://www.mdpi.com
Choosing the Right Boiler System – https://www.energysavingtrust.org.uk
Fuel Flexibility in Industrial Boilers – https://www.iea.org
Industrial Boiler Technology Developments – https://www.automation.com
Oil-Fired Boiler Operation in Industry – https://www.sciencedirect.com
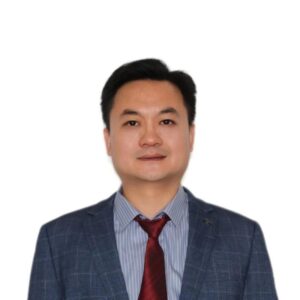