Industrial oil-fired boilers play a vital role in various industries, providing high-efficiency steam and hot water for manufacturing, processing, and power generation. However, inefficiencies, high fuel costs, and maintenance issues can arise if businesses do not fully understand the critical components of these systems. A thorough knowledge of their core parts helps in optimizing performance, reducing fuel consumption, and ensuring regulatory compliance.
The core components of an industrial oil-fired boiler include the burner, combustion chamber, heat exchanger, fuel supply system, exhaust system, and control unit. Each component is essential for ensuring efficient fuel combustion, effective heat transfer, and minimal emissions. Modern oil-fired boilers integrate advanced combustion technologies to improve energy efficiency, enhance safety, and meet environmental regulations.
To ensure optimal efficiency, cost-effectiveness, and longevity, industries must understand how each of these components functions and interacts. Below, we explore the essential parts of an industrial oil-fired boiler in detail.
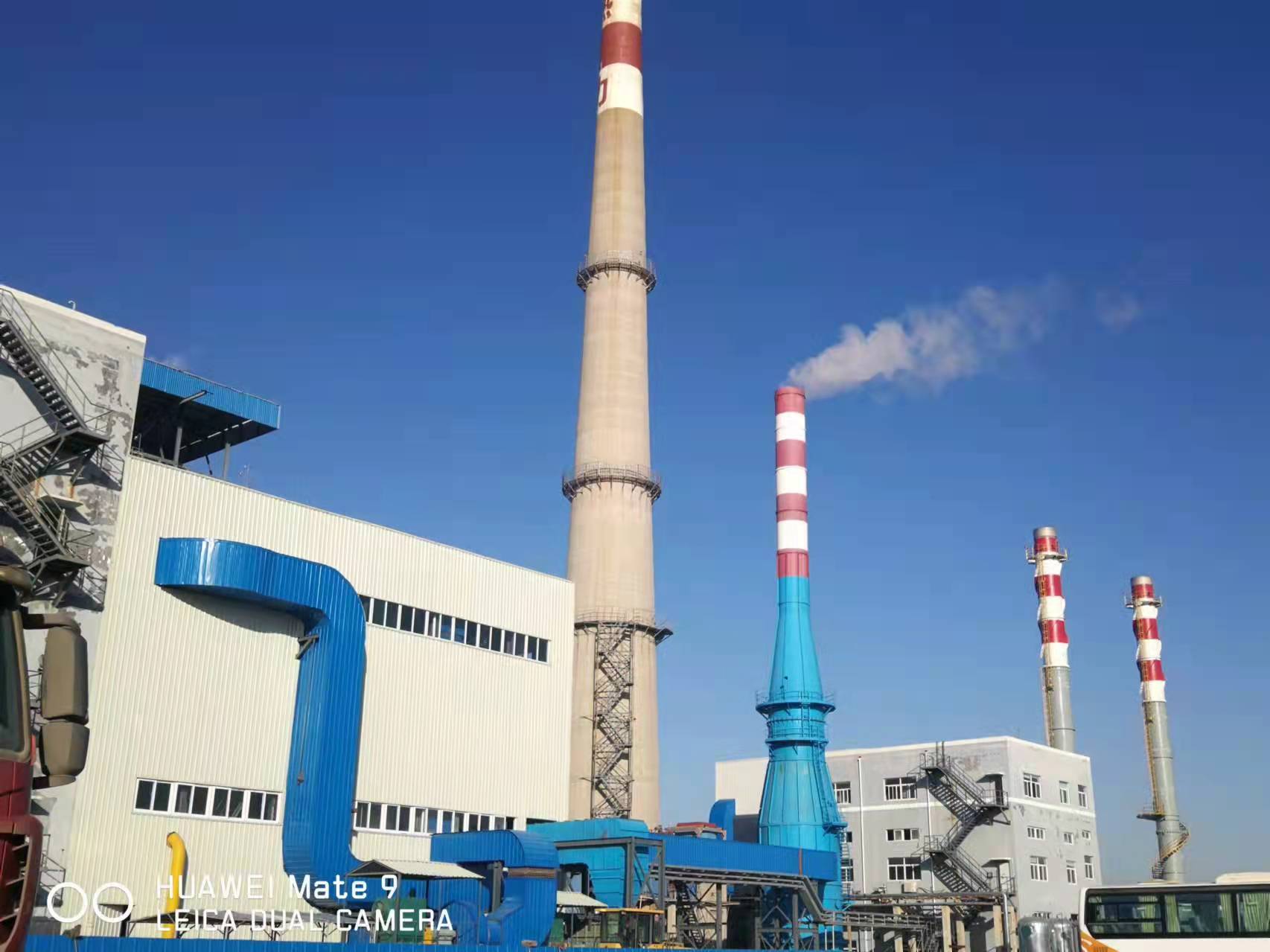
What Is the Function of the Burner in an Industrial Oil-Fired Boiler?
Industrial oil-fired boilers rely on burners as a critical component for efficient fuel combustion. Without a properly functioning burner, the boiler’s efficiency drops, fuel consumption increases, and emissions rise, leading to higher operational costs and environmental concerns.
The burner in an industrial oil-fired boiler is responsible for atomizing fuel oil, mixing it with air, and igniting the mixture to create a controlled flame for heat generation. This process ensures efficient combustion, optimal heat transfer, and reduced emissions, enhancing boiler performance and fuel efficiency.
By integrating advanced burner designs, automated control systems, and precise fuel-air regulation, modern oil-fired boilers achieve higher efficiency, lower fuel waste, and improved emissions compliance.
1. Key Functions of an Oil-Fired Boiler Burner
Burners in industrial oil-fired boilers play a crucial role in energy conversion.
A. Fuel Atomization and Injection
✅ Breaks down liquid fuel oil into fine droplets for better mixing with air.
✅ Ensures complete combustion and minimizes unburned fuel losses.
B. Air-Fuel Mixture Control
✅ Precisely regulates air and fuel proportions for optimal combustion efficiency.
✅ Prevents excess air, which reduces efficiency, and incomplete combustion, which increases emissions.
C. Stable and Controlled Flame Generation
✅ Produces a stable flame for consistent heat transfer.
✅ Maintains steady steam production in industrial processes.
Function | Purpose | Efficiency Impact |
---|---|---|
Fuel Atomization | Creates fine fuel droplets | Improves combustion quality |
Air-Fuel Control | Regulates mixture ratio | Reduces energy loss |
Flame Stabilization | Ensures steady heat output | Prevents temperature fluctuations |
2. Types of Burners Used in Oil-Fired Boilers
Modern industrial oil-fired boilers use different burner designs to enhance performance.
A. Pressure Jet Burners
✅ Uses high-pressure fuel injection to atomize oil.
✅ Common in large industrial applications due to high efficiency.
B. Rotary Cup Burners
✅ Uses a rotating cup to break fuel into fine mist.
✅ Suitable for low-viscosity fuels and offers stable combustion.
C. Steam or Air-Assisted Burners
✅ Uses compressed air or steam to atomize heavy oils.
✅ Ideal for burning residual fuels with higher viscosity.
Burner Type | Fuel Compatibility | Efficiency |
---|---|---|
Pressure Jet | Light & medium oils | High |
Rotary Cup | Light oils | Medium |
Steam/Air-Assisted | Heavy & residual oils | High |
3. How Modern Burners Improve Efficiency and Reduce Emissions
A. Low NOx Burner Technology
✅ Reduces nitrogen oxide (NOx) emissions by controlling flame temperature.
✅ Uses staged combustion and flue gas recirculation to lower NOx levels.
B. Oxygen Trim Control
✅ Continuously monitors oxygen levels in flue gases.
✅ Adjusts air supply to prevent excess air and maximize efficiency.
C. Advanced Flame Monitoring & Control
✅ Uses infrared and ultraviolet sensors to detect flame stability.
✅ Prevents fuel wastage and unburned hydrocarbons.
Technology | Efficiency Gain | Emissions Reduction |
---|---|---|
Low NOx Burner | 5-10% | Reduces NOx emissions |
Oxygen Trim Control | 2-6% | Minimizes excess air losses |
Flame Monitoring | 3-7% | Prevents fuel wastage |
4. Challenges in Burner Operation and Maintenance
Despite their efficiency, burners require regular maintenance to prevent performance issues.
A. Fuel Quality Issues
❌ Impurities in oil can clog nozzles and reduce combustion efficiency.
✅ Solution: Use proper filtration systems and preheat heavy fuels.
B. Burner Fouling and Deposits
❌ Soot and carbon buildup reduce flame efficiency.
✅ Solution: Regular burner cleaning and airflow adjustments.
C. Wear and Tear of Components
❌ Nozzle erosion and fan degradation impact performance.
✅ Solution: Routine inspection and replacement of worn-out parts.
Challenge | Solution | Impact on Efficiency |
---|---|---|
Fuel Impurities | Filtration & preheating | Prevents nozzle clogging |
Burner Fouling | Regular cleaning | Maintains steady combustion |
Component Wear | Timely replacement | Prevents unexpected failures |
5. Future Trends in Oil Burner Technology
Burner technology is continuously evolving to meet stricter efficiency and emission standards.
A. AI-Based Burner Optimization
✅ Uses machine learning to predict fuel demand and optimize combustion.
✅ Adjusts burner settings in real time to maximize efficiency.
B. Hybrid Burners (Multi-Fuel Capability)
✅ Designed to switch between oil, gas, and alternative fuels.
✅ Enhances fuel flexibility and reduces dependence on fossil fuels.
C. Ultra-Low Emission Burners
✅ Uses advanced air staging and recirculation techniques.
✅ Minimizes CO2 and NOx emissions, aligning with environmental regulations.
Future Technology | Efficiency Impact | Environmental Benefit |
---|---|---|
AI Optimization | 8-12% | Reduces fuel wastage |
Multi-Fuel Burners | 5-10% | Enhances fuel flexibility |
Ultra-Low NOx Burners | 10-20% | Meets stricter emission standards |
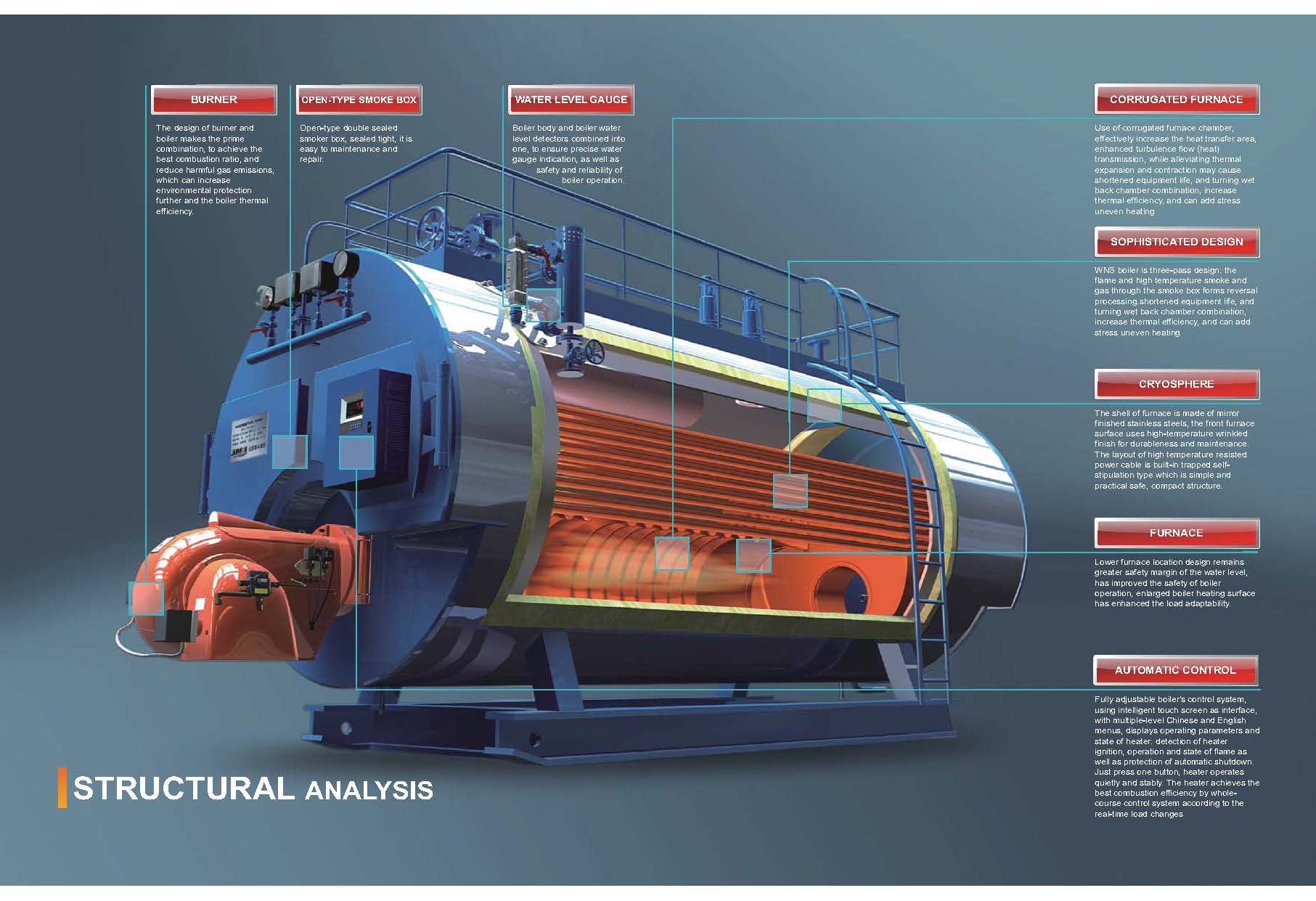
How Does the Combustion Chamber Contribute to Heat Generation?
The combustion chamber is the core component of an industrial boiler where fuel combustion occurs, generating heat energy for steam production. Its design directly impacts boiler efficiency, fuel consumption, and emission levels. A well-optimized combustion chamber maximizes heat transfer, minimizes fuel wastage, and ensures complete combustion, enhancing overall system performance.
1. Functions of the Combustion Chamber in Heat Generation
The combustion chamber plays a vital role in heat production by facilitating efficient fuel combustion.
A. Fuel-Air Mixing for Complete Combustion
✅ Precisely blends fuel and air to achieve optimal combustion efficiency.
✅ Prevents incomplete combustion, which can lead to heat loss and higher emissions.
B. High-Temperature Heat Transfer
✅ Converts chemical energy from fuel into thermal energy.
✅ Transfers heat to boiler water through radiation and convection, producing high-pressure steam.
C. Flame Stabilization for Consistent Heating
✅ Ensures a steady and controlled flame to maintain uniform heat distribution.
✅ Reduces temperature fluctuations, preventing thermal stress on boiler components.
Function | Purpose | Impact on Heat Generation |
---|---|---|
Fuel-Air Mixing | Ensures complete combustion | Maximizes energy conversion |
Heat Transfer | Transfers thermal energy to water | Generates steam efficiently |
Flame Stabilization | Maintains steady combustion | Reduces temperature variations |
2. Key Components of a Combustion Chamber
A combustion chamber consists of multiple elements designed to enhance heat generation.
A. Burner Assembly
✅ Injects fuel into the chamber in an atomized form for efficient burning.
✅ Regulates the fuel-air ratio for optimal combustion conditions.
B. Refractory Lining
✅ High-temperature insulating material that retains heat within the chamber.
✅ Protects the boiler structure from thermal damage and reduces heat loss.
C. Air and Gas Flow Control
✅ Manages the supply of combustion air to maintain efficiency.
✅ Ensures proper exhaust gas flow to prevent heat buildup and pressure imbalances.
Component | Function | Benefit |
---|---|---|
Burner | Fuel injection and mixing | Efficient combustion |
Refractory Lining | Insulation and heat retention | Reduces energy loss |
Air/Gas Flow | Controls combustion atmosphere | Improves efficiency |
3. Factors Affecting Combustion Chamber Efficiency
Several factors influence how effectively a combustion chamber generates heat.
A. Fuel Quality and Atomization
✅ High-quality fuel with low moisture and consistent calorific value burns efficiently.
✅ Proper atomization ensures fine fuel droplets, enhancing the combustion process.
B. Air-Fuel Ratio Control
✅ Precise air regulation prevents excess oxygen (which reduces efficiency) and unburned fuel (which increases waste).
✅ Advanced oxygen sensors and trim systems optimize air input dynamically.
C. Chamber Design and Insulation
✅ A well-designed chamber with optimized flame pathways maximizes heat transfer.
✅ Proper insulation reduces heat dissipation losses, keeping temperatures stable.
Factor | Effect on Efficiency | Optimization Strategy |
---|---|---|
Fuel Quality | Higher calorific value = more heat | Use refined fuel & preheating |
Air-Fuel Ratio | Prevents incomplete combustion | Install oxygen trim controls |
Chamber Insulation | Minimizes heat loss | Use high-quality refractory materials |
4. How Modern Combustion Chambers Enhance Performance
A. Low NOx Combustion Technology
✅ Uses staged combustion and flue gas recirculation to lower nitrogen oxide (NOx) emissions.
✅ Reduces excess air demand, improving heat generation efficiency.
B. High-Efficiency Heat Transfer Designs
✅ Incorporates multi-pass flame paths to maximize radiation and convective heat absorption.
✅ Improves steam production rate with minimal fuel consumption.
C. Smart Combustion Control Systems
✅ Uses AI-driven sensors to adjust fuel injection, air supply, and temperature in real time.
✅ Prevents overheating or inefficient burning, ensuring optimal heat output.
Technology | Efficiency Impact | Operational Benefit |
---|---|---|
Low NOx Combustion | 5-10% increase | Reduces emissions |
Multi-Pass Heat Transfer | 8-12% gain | Maximizes energy use |
AI Combustion Control | 10-15% gain | Adjusts real-time settings |
5. Challenges in Combustion Chamber Operation
Despite advancements, some challenges impact combustion chamber performance.
A. Soot and Carbon Deposits
❌ Excess carbon buildup reduces heat transfer efficiency.
✅ Solution: Implement regular cleaning and soot blowers.
B. Thermal Stress and Cracking
❌ Extreme temperature variations cause cracks in the refractory lining.
✅ Solution: Use high-durability refractory materials and gradual heating during startup.
C. Improper Fuel-Air Mixing
❌ Uneven air distribution leads to hot spots and uneven combustion.
✅ Solution: Install advanced burner designs and dynamic air control systems.
Issue | Impact | Solution |
---|---|---|
Carbon Deposits | Lowers heat transfer | Regular cleaning & soot blowers |
Thermal Stress | Cracks refractory walls | Use high-durability materials |
Poor Air Mixing | Uneven flame distribution | Advanced burner control |
6. Future Innovations in Combustion Chamber Design
A. Ultra-Low Emission Combustion
✅ Uses oxygen-enriched combustion to burn fuel more cleanly and efficiently.
✅ Reduces carbon footprint without sacrificing performance.
B. Hybrid Combustion Systems
✅ Allows switching between fossil fuels and biofuels to enhance sustainability.
✅ Adapts to changing fuel availability and cost variations.
C. AI-Powered Self-Learning Burners
✅ Uses real-time data analytics to adjust air and fuel inputs dynamically.
✅ Prevents combustion inefficiencies and heat losses.
Future Trend | Efficiency Benefit | Environmental Impact |
---|---|---|
Oxygen-Enriched Combustion | 10-15% gain | Lower CO2 emissions |
Hybrid Fuel Compatibility | 8-12% increase | Greater fuel flexibility |
AI-Driven Burners | 12-18% boost | Minimizes energy waste |
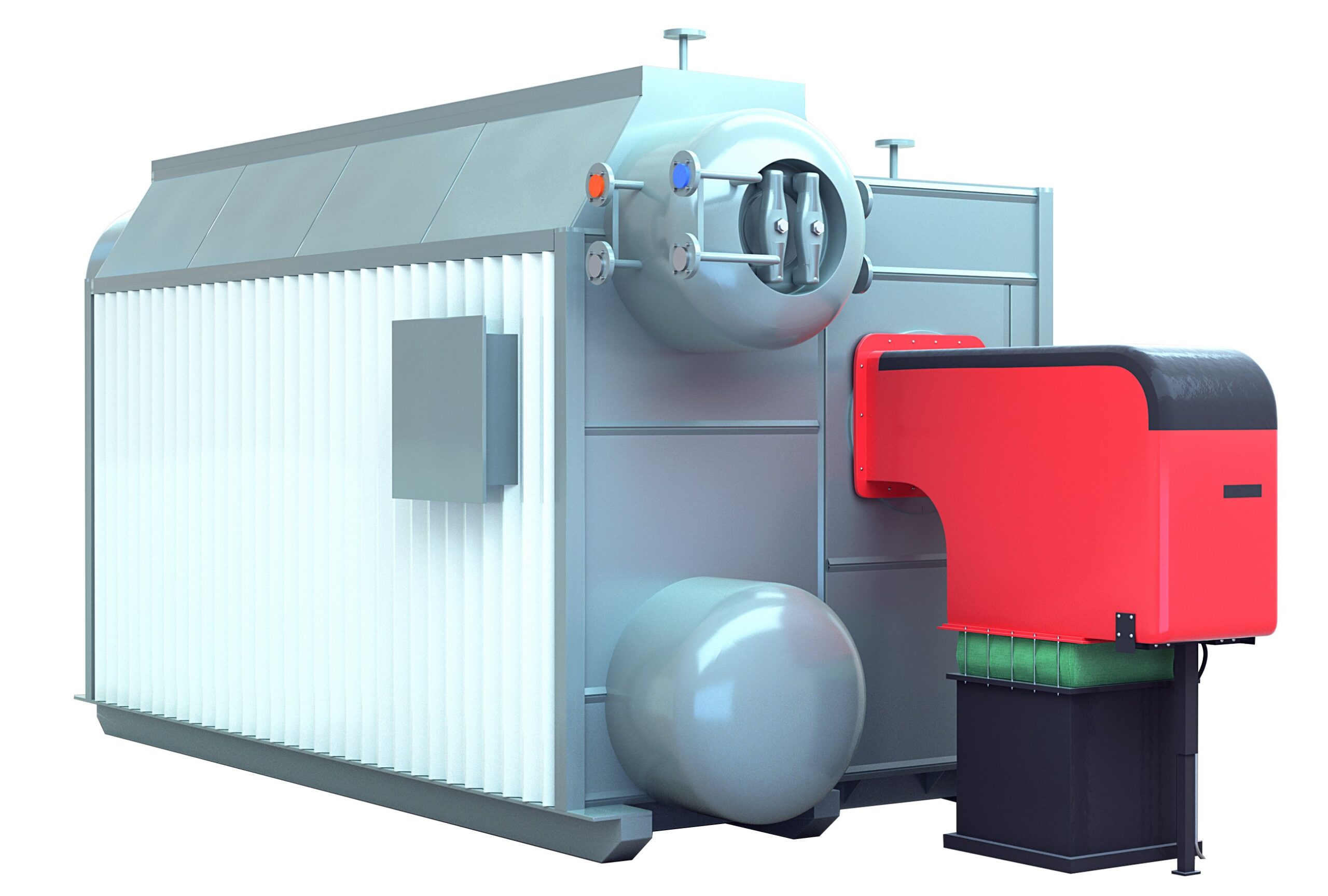
What Role Does the Heat Exchanger Play in Steam and Hot Water Production?
The heat exchanger is a critical component in steam and hot water production, responsible for transferring thermal energy from a heat source to water. It ensures efficient energy utilization, temperature regulation, and system longevity. An optimized heat exchanger enhances boiler efficiency, reduces fuel consumption, and maintains consistent steam or hot water supply.
1. Functions of a Heat Exchanger in Steam and Hot Water Production
The heat exchanger plays a fundamental role in thermal energy conversion within a boiler system.
A. Heat Transfer from Combustion Gases to Water
✅ Extracts thermal energy from hot flue gases generated during fuel combustion.
✅ Transfers this heat to water, converting it into steam or hot water.
B. Temperature Regulation for Process Efficiency
✅ Maintains optimal water temperature levels, preventing overheating or energy loss.
✅ Controls steam pressure to meet industrial process requirements.
C. Energy Conservation and Fuel Efficiency
✅ Maximizes heat absorption, reducing fuel consumption and operational costs.
✅ Enhances thermal efficiency, leading to improved boiler performance.
Function | Purpose | Impact on Steam & Hot Water Production |
---|---|---|
Heat Transfer | Converts fuel energy into thermal energy | Generates high-efficiency steam & hot water |
Temperature Regulation | Maintains stable thermal output | Prevents overheating & improves system control |
Energy Conservation | Reduces heat loss & fuel wastage | Enhances fuel economy & performance |
2. Types of Heat Exchangers in Steam and Hot Water Systems
There are several types of heat exchangers designed for different industrial applications.
A. Shell-and-Tube Heat Exchangers
✅ Composed of multiple tubes enclosed within a cylindrical shell.
✅ Hot gases flow over the tubes, transferring heat to water inside the tubes.
B. Plate Heat Exchangers
✅ Uses thin metal plates with high surface area for efficient heat exchange.
✅ Suitable for compact systems requiring rapid heat transfer.
C. Fin-Tube Heat Exchangers
✅ Incorporates extended surface fins to enhance heat absorption and transfer.
✅ Common in high-efficiency boiler applications.
Heat Exchanger Type | Structure | Efficiency | Common Application |
---|---|---|---|
Shell-and-Tube | Cylindrical shell with multiple tubes | High | Large-scale steam production |
Plate | Metal plates with narrow channels | Very High | Hot water heating |
Fin-Tube | Tubes with extended fin surfaces | Moderate-High | High-efficiency boilers |
3. How the Heat Exchanger Enhances System Efficiency
Several design factors contribute to the effectiveness of a heat exchanger in a steam and hot water system.
A. Optimized Heat Transfer Surface Area
✅ Larger surface areas allow greater heat absorption and faster temperature rise.
✅ Multi-pass designs increase contact time between water and heat source.
B. Efficient Fluid Flow Management
✅ Ensures uniform heat distribution, preventing localized overheating.
✅ Uses baffles and flow control valves to regulate heat transfer.
C. Condensation and Heat Recovery
✅ Captures latent heat from steam condensation, improving efficiency.
✅ Reduces wasted thermal energy, leading to lower fuel consumption.
Efficiency Factor | Effect on Performance | Optimization Strategy |
---|---|---|
Large Heat Transfer Surface | Increases heat absorption | Use finned or plate exchangers |
Uniform Fluid Flow | Prevents overheating & cold spots | Install flow regulation systems |
Heat Recovery | Reduces energy loss | Integrate economizers & condensate recovery |
4. Challenges in Heat Exchanger Operation
Despite their advantages, heat exchangers face operational challenges that impact performance.
A. Fouling and Scaling Build-Up
❌ Mineral deposits and soot reduce heat transfer efficiency.
✅ Solution: Regular cleaning and descaling with chemical treatments.
B. Corrosion and Material Degradation
❌ Exposure to high-temperature and corrosive gases weakens components.
✅ Solution: Use corrosion-resistant alloys and protective coatings.
C. Pressure Drop and Flow Restrictions
❌ Accumulated deposits lead to reduced water flow and uneven heating.
✅ Solution: Install automatic blowdown and monitoring systems.
Issue | Impact on Efficiency | Solution |
---|---|---|
Fouling & Scaling | Lowers heat transfer | Regular cleaning & water treatment |
Corrosion | Weakens components | Use high-quality alloys |
Flow Restrictions | Uneven heating | Implement automatic monitoring |
5. Future Advancements in Heat Exchanger Technology
Technological innovations are enhancing heat exchanger performance for steam and hot water production.
A. High-Efficiency Condensing Heat Exchangers
✅ Recaptures waste heat from exhaust gases for additional energy savings.
✅ Increases fuel efficiency by 10-15% compared to conventional designs.
B. Smart Sensor Monitoring for Predictive Maintenance
✅ Uses IoT-based sensors to track temperature, pressure, and fouling rates.
✅ Reduces unplanned shutdowns through real-time diagnostics.
C. Nanotechnology-Coated Heat Exchangers
✅ Nano-coatings reduce fouling and corrosion, extending lifespan.
✅ Improves heat transfer rates by minimizing surface resistance.
Innovation | Efficiency Impact | Operational Benefit |
---|---|---|
Condensing Heat Exchangers | 10-15% gain | Reduces fuel consumption |
Smart Sensor Monitoring | 8-12% gain | Prevents failures & improves reliability |
Nano-Coatings | 12-18% boost | Minimizes fouling & corrosion |
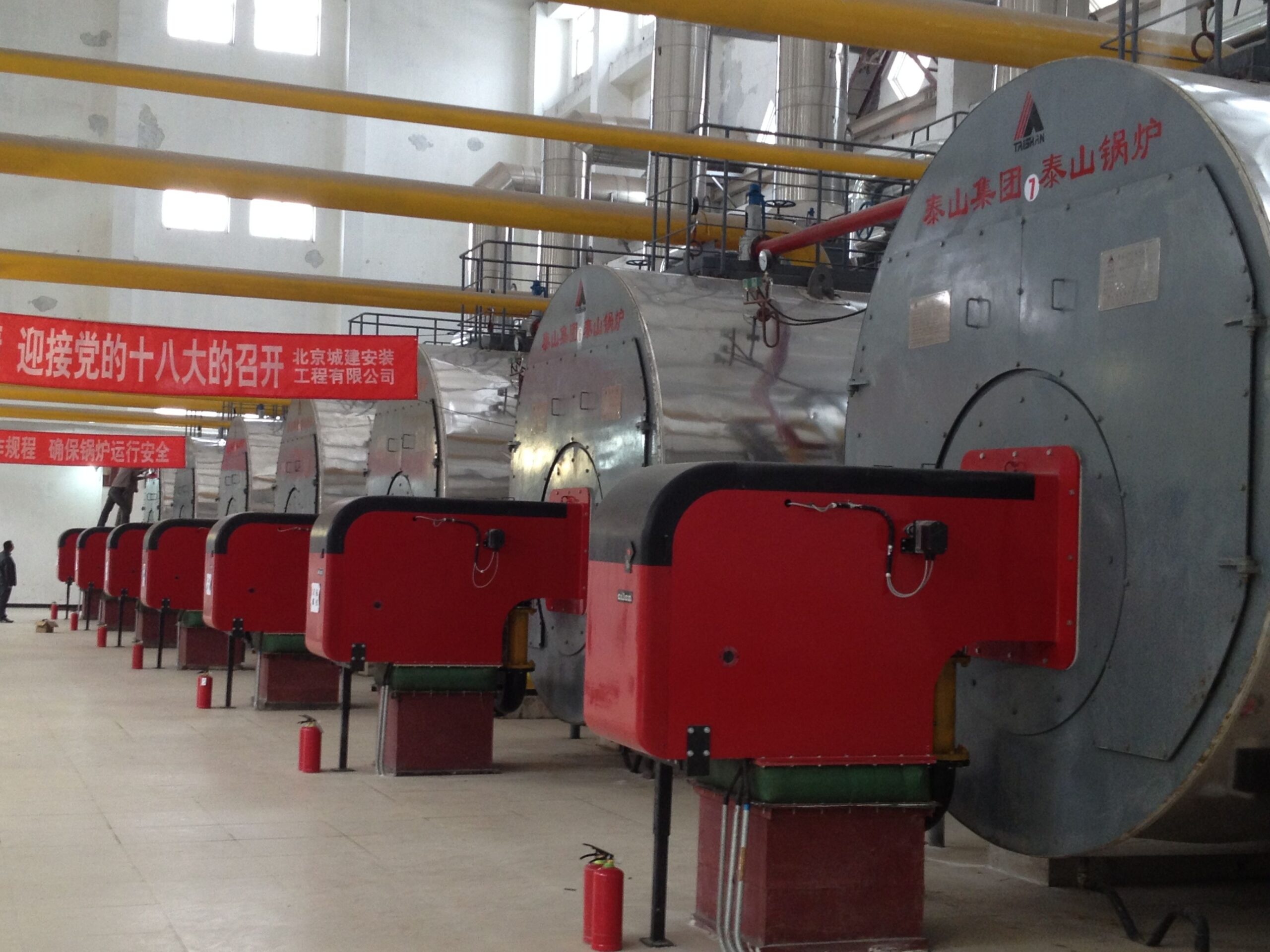
How Does the Fuel Supply System Ensure Efficient Operation?
The fuel supply system is a critical component in industrial boilers and power generation systems. It ensures a consistent, controlled, and efficient delivery of fuel to maintain stable combustion, optimize energy output, and minimize waste. By integrating automated handling, precise metering, and real-time monitoring, fuel supply systems maximize operational efficiency, reduce emissions, and enhance cost-effectiveness.
1. Key Functions of the Fuel Supply System
The fuel supply system is responsible for fuel storage, transportation, metering, and regulation to ensure efficient energy generation.
A. Fuel Storage and Handling
✅ Maintains adequate fuel reserves for continuous operation.
✅ Uses sealed tanks or silos to prevent contamination and degradation.
B. Fuel Transportation to the Boiler
✅ Transfers fuel from storage units to combustion chambers via conveyors, pumps, or pipelines.
✅ Utilizes automated fuel feeders for consistent delivery rates.
C. Precise Fuel Metering and Regulation
✅ Ensures the correct amount of fuel is supplied based on system demand.
✅ Prevents fuel overloading or underfeeding, which can affect combustion stability.
D. Safety and Emission Control
✅ Monitors fuel pressure, temperature, and flow rates to avoid system failures.
✅ Incorporates filters, separators, and safety shutoffs to prevent contamination and hazards.
Function | Role in Efficiency | Impact on Operation |
---|---|---|
Fuel Storage | Ensures fuel availability | Prevents supply shortages |
Fuel Transport | Delivers fuel smoothly to burners | Avoids combustion disruptions |
Fuel Metering | Controls fuel input | Optimizes combustion & minimizes waste |
Safety Monitoring | Detects leaks & prevents hazards | Reduces risks & improves reliability |
2. Types of Fuel Supply Systems in Industrial Applications
Different industries use fuel supply systems tailored to specific energy needs.
A. Solid Fuel Supply Systems (Coal, Biomass, Wood Chips)
✅ Uses conveyors, augers, or pneumatic systems to transport fuel.
✅ Includes crushers and feeders for size reduction and controlled feeding.
B. Liquid Fuel Supply Systems (Heavy Oil, Diesel, Kerosene)
✅ Employs pumps, pipelines, and preheaters for efficient oil transport.
✅ Uses fuel filters to remove impurities, ensuring cleaner combustion.
C. Gaseous Fuel Supply Systems (Natural Gas, LPG, Biogas)
✅ Delivers fuel through pressurized pipelines and safety valves.
✅ Incorporates pressure regulators and flow meters for consistent gas flow.
Fuel Type | Supply Method | Efficiency Consideration |
---|---|---|
Solid Fuels | Conveyor & auger feeders | Requires size control & steady feed |
Liquid Fuels | Pumps & filters | Needs preheating & impurity removal |
Gaseous Fuels | Pipelines & regulators | Requires precise pressure control |
3. Optimizing Fuel Supply for Maximum Efficiency
To achieve high operational efficiency, fuel supply systems must be optimized for consistent delivery, proper combustion, and minimal waste.
A. Fuel Preprocessing and Conditioning
✅ Coal and biomass are pulverized or dried to improve combustion efficiency.
✅ Heavy oils are preheated to reduce viscosity for smooth flow.
✅ Gas fuels are pressure-regulated for stable burning.
B. Automated Fuel Feeding Systems
✅ Uses smart sensors and real-time monitoring to adjust fuel flow based on demand.
✅ Prevents over-fueling, which causes excessive emissions, and under-fueling, which leads to incomplete combustion.
C. Advanced Control and Monitoring Technologies
✅ SCADA and IoT systems track fuel flow rates, pressure levels, and temperature changes.
✅ AI-based predictive maintenance reduces fuel wastage and prevents unexpected breakdowns.
Optimization Method | Impact on Efficiency | Benefit |
---|---|---|
Fuel Preprocessing | Enhances combustion | Reduces emissions & fuel consumption |
Automated Fuel Feeding | Adjusts supply dynamically | Prevents energy losses |
Smart Monitoring | Detects inefficiencies | Prevents downtime & improves reliability |
4. Challenges and Solutions in Fuel Supply Management
Despite technological advancements, fuel supply systems face operational challenges.
A. Fuel Quality Variability
❌ Inconsistent fuel properties can lead to unstable combustion.
✅ Solution: Implement fuel quality monitoring and preprocessing techniques.
B. Supply Disruptions and Shortages
❌ Delivery delays or supply chain issues can halt production.
✅ Solution: Maintain adequate fuel reserves and backup systems.
C. Equipment Wear and Tear
❌ Pipelines, pumps, and conveyors degrade over time, affecting performance.
✅ Solution: Implement regular maintenance and condition monitoring.
Issue | Impact on Fuel Efficiency | Solution |
---|---|---|
Fuel Variability | Causes combustion instability | Use fuel homogenization techniques |
Supply Disruptions | Leads to operational downtime | Maintain backup storage |
Equipment Wear | Reduces fuel flow efficiency | Conduct preventive maintenance |
5. Future Trends in Fuel Supply System Optimization
Advancements in fuel supply technology continue to improve system efficiency.
A. AI-Powered Fuel Flow Optimization
✅ Uses machine learning to predict fuel demand and adjust flow rates automatically.
✅ Reduces fuel waste and energy losses.
B. Integration of Renewable Fuels
✅ Expanding the use of biofuels, hydrogen, and synthetic gases in industrial fuel supply systems.
✅ Decreases dependence on fossil fuels and reduces carbon footprint.
C. Smart Fuel Storage and Management Systems
✅ Automated fuel inventory tracking ensures efficient supply chain management.
✅ Reduces fuel wastage and operational inefficiencies.
Innovation | Efficiency Impact | Operational Benefit |
---|---|---|
AI-Powered Fuel Flow | 10-15% improvement | Reduces fuel consumption |
Renewable Fuel Integration | 20-30% emissions reduction | Enhances sustainability |
Smart Storage Systems | 12-18% efficiency gain | Minimizes supply risks |
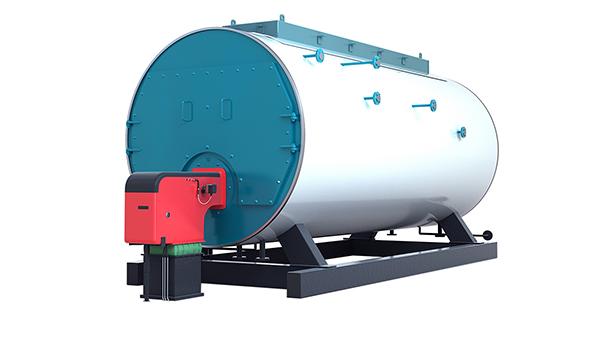
What Is the Purpose of the Exhaust System in an Oil-Fired Boiler?
An oil-fired boiler’s exhaust system is crucial for removing combustion byproducts, ensuring safe operation, and maintaining regulatory compliance. This system manages flue gases, recovers heat energy, and reduces harmful emissions. Without a properly functioning exhaust system, an oil-fired boiler could experience inefficiency, increased emissions, and safety hazards.
1. Key Functions of the Exhaust System
The exhaust system in an oil-fired boiler serves multiple essential functions to ensure efficiency, safety, and environmental compliance.
A. Safe Removal of Combustion Gases
✅ Channels flue gases, including carbon dioxide (CO₂), nitrogen oxides (NOx), sulfur oxides (SOx), and unburned hydrocarbons, away from the boiler.
✅ Prevents toxic gas buildup, reducing the risk of workplace hazards.
B. Emission Reduction and Pollution Control
✅ Uses filters, scrubbers, and catalytic converters to limit particulate matter, sulfur compounds, and nitrogen oxides.
✅ Meets environmental regulations such as EPA, EU emission standards, and ISO requirements.
C. Heat Recovery for Energy Efficiency
✅ Recovers heat from flue gases using economizers and heat exchangers to improve boiler efficiency.
✅ Reduces fuel consumption by preheating feedwater or air intake.
Function | Role in Boiler Operation | Efficiency Impact |
---|---|---|
Flue Gas Removal | Prevents toxic buildup | Ensures safe combustion |
Emission Control | Reduces pollutants | Meets regulatory compliance |
Heat Recovery | Improves fuel efficiency | Lowers operating costs |
2. Main Components of an Oil-Fired Boiler Exhaust System
The exhaust system consists of multiple components that work together to ensure efficient and compliant operation.
A. Flue Gas Stack (Chimney)
✅ Directs combustion gases safely into the atmosphere.
✅ Designed for proper height and diameter to optimize gas dispersion and prevent backpressure.
B. Economizer (Heat Recovery Unit)
✅ Captures waste heat from flue gases to preheat boiler feedwater.
✅ Enhances fuel efficiency by 5–10%, reducing operational costs.
C. Air Preheater
✅ Uses flue gas heat to pre-warm combustion air, increasing thermal efficiency.
✅ Improves fuel-to-air mixing, reducing excess fuel consumption.
D. Flue Gas Scrubber and Particulate Filters
✅ Removes SOx, NOx, and particulate matter using chemical reactions and filtration.
✅ Ensures compliance with environmental regulations.
E. Draft Fan (Induced Draft and Forced Draft Fans)
✅ Controls the movement of exhaust gases to maintain proper air-to-fuel ratios.
✅ Prevents flue gas backflow, maintaining consistent pressure.
Component | Function | Efficiency Benefit |
---|---|---|
Flue Gas Stack | Expels gases into the air | Prevents hazardous gas buildup |
Economizer | Recovers heat | Increases fuel efficiency by 5-10% |
Air Preheater | Preheats combustion air | Reduces fuel consumption |
Scrubber & Filters | Removes pollutants | Improves air quality & compliance |
Draft Fan | Regulates exhaust flow | Maintains combustion stability |
3. Importance of Heat Recovery in Exhaust Systems
Recovering heat from flue gases is one of the most effective ways to improve boiler efficiency.
A. How Heat Recovery Works
✅ Economizers transfer flue gas heat to incoming feedwater, reducing energy loss.
✅ Air preheaters increase combustion air temperature, reducing fuel demand.
✅ Condensing heat exchangers extract additional heat by cooling flue gases below the dew point, capturing latent heat.
B. Energy Efficiency Gains
✅ Standard heat recovery increases efficiency by 5–10%.
✅ Advanced condensing economizers boost efficiency by 15–20%, especially in high-moisture fuel combustion.
Heat Recovery Method | Efficiency Improvement | Fuel Savings |
---|---|---|
Economizer | 5-10% | Moderate |
Air Preheater | 5-7% | Significant |
Condensing Heat Exchanger | 15-20% | High |
4. Environmental Compliance and Emission Reduction
Exhaust systems help oil-fired boilers meet strict environmental regulations by controlling air pollutants.
A. Pollutants in Flue Gases
✅ Sulfur oxides (SOx): Formed from sulfur in fuel oil, contributing to acid rain.
✅ Nitrogen oxides (NOx): Produced at high combustion temperatures, leading to smog formation.
✅ Particulate matter (PM): Includes soot, ash, and unburned hydrocarbons.
B. Emission Control Technologies
✅ Scrubbers: Use chemical reactions to remove SOx and NOx.
✅ Electrostatic Precipitators (ESP): Capture fine particulates from exhaust gases.
✅ Selective Catalytic Reduction (SCR): Converts NOx into harmless nitrogen and water vapor.
Pollutant | Source | Control Method |
---|---|---|
Sulfur Oxides (SOx) | Sulfur in fuel oil | Wet scrubbers |
Nitrogen Oxides (NOx) | High combustion temps | SCR system |
Particulate Matter (PM) | Incomplete combustion | ESP filters |
5. Challenges and Solutions in Exhaust System Management
Despite advanced designs, exhaust systems face operational challenges that must be addressed.
A. Corrosion and Scaling
❌ High-temperature gases and acidic condensation cause metal degradation.
✅ Solution: Use corrosion-resistant materials and install drainage systems for condensation.
B. Backpressure Issues
❌ Improper stack height or fan failure can cause inefficient exhaust flow.
✅ Solution: Use variable-speed draft fans to regulate pressure and airflow.
C. High Operating Costs for Emission Controls
❌ Scrubber systems and filters require maintenance and energy input.
✅ Solution: Implement heat recovery to offset costs and adopt automated monitoring systems.
Issue | Impact on Efficiency | Solution |
---|---|---|
Corrosion | Reduces component lifespan | Use corrosion-resistant materials |
Backpressure | Decreases combustion efficiency | Install draft fans & adjust stack design |
High Emission Control Costs | Increases operational expenses | Integrate heat recovery systems |
6. Future Trends in Oil-Fired Boiler Exhaust Systems
Innovations are shaping the future of exhaust system efficiency and sustainability.
A. Smart Exhaust Monitoring Systems
✅ Uses IoT sensors to track emission levels and optimize air-to-fuel ratios in real-time.
✅ Reduces fuel consumption and enhances compliance.
B. Advanced Heat Recovery Systems
✅ Developments in nano-coated heat exchangers improve heat recovery rates.
✅ Supercritical steam technology increases efficiency in industrial plants.
C. Transition to Cleaner Fuels
✅ Adoption of low-sulfur fuel oils and biofuel blends reduces emissions.
✅ Carbon capture and storage (CCS) technologies are emerging as long-term emission control solutions.
Innovation | Benefit |
---|---|
Smart Exhaust Monitoring | Real-time optimization & lower emissions |
Advanced Heat Recovery | Increased fuel efficiency |
Cleaner Fuel Transition | Lower environmental impact |
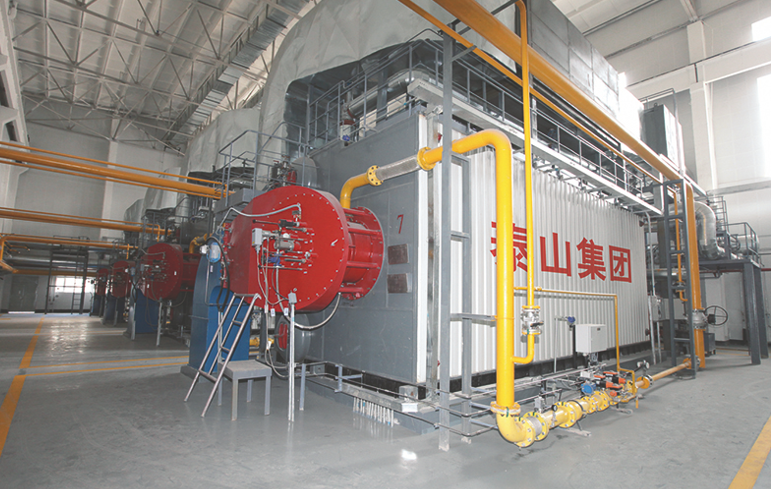
How Do Modern Control Systems Enhance Efficiency and Safety in Industrial Boilers?
Industrial boilers are complex systems that require precise control to operate efficiently and safely. Modern control systems leverage automation, real-time monitoring, and advanced sensors to enhance performance, reduce fuel consumption, and minimize risks. Without an intelligent control system, a boiler can suffer from inefficiencies, safety hazards, and excessive emissions, leading to higher operational costs and environmental non-compliance.
1. Key Functions of Modern Boiler Control Systems
Modern control systems provide several critical functions that optimize performance, ensure safety, and comply with regulations.
A. Automation for Efficiency Optimization
✅ Automated Fuel-Air Ratio Control: Adjusts fuel and air supply dynamically for optimal combustion efficiency.
✅ Load Regulation: Adapts boiler operation to real-time demand fluctuations, reducing energy waste.
B. Real-Time Monitoring and Data Analysis
✅ Continuous Temperature and Pressure Monitoring: Ensures stable operations by preventing overheating or pressure drops.
✅ Predictive Maintenance Alerts: Uses AI and IoT to detect potential failures before they occur, reducing downtime.
C. Safety Enhancements and Emergency Shutdown
✅ Automatic Safety Shutdown Mechanisms: Detects abnormal conditions like high pressure or low water levels and shuts down the system to prevent explosions.
✅ Remote Monitoring & Control: Enables real-time adjustments and emergency response through cloud-based interfaces.
Function | Impact on Efficiency | Impact on Safety |
---|---|---|
Fuel-Air Ratio Control | Reduces fuel wastage | Prevents incomplete combustion |
Load Regulation | Adapts to demand | Prevents overheating |
Temperature Monitoring | Optimizes heat transfer | Avoids thermal stress damage |
Predictive Maintenance | Reduces downtime | Prevents equipment failure |
Emergency Shutdown | Prevents explosions | Ensures operator safety |
2. Components of a Modern Boiler Control System
Modern control systems integrate multiple components to ensure precise regulation, real-time diagnostics, and automation.
A. Programmable Logic Controller (PLC) & Distributed Control System (DCS)
✅ Automates operations, eliminating manual errors.
✅ Manages fuel input, water levels, and exhaust gas emissions with precision.
B. Smart Sensors and IoT Devices
✅ Measure pressure, temperature, flow rate, and emissions in real-time.
✅ Transmit data to a central control unit for continuous optimization.
C. Human-Machine Interface (HMI) & Remote Monitoring
✅ Allows operators to monitor system performance from a control room or remotely.
✅ Displays real-time alerts and diagnostics to detect anomalies early.
D. Advanced Safety Systems
✅ Failsafe mechanisms prevent hazardous situations like pressure surges or flameouts.
✅ Emergency shutdown protocols stop operations when safety thresholds are exceeded.
Component | Function | Impact on Operations |
---|---|---|
PLC/DCS | Automates control | Improves consistency & efficiency |
IoT Sensors | Monitors real-time data | Enables predictive maintenance |
HMI & Remote Control | Provides real-time alerts | Reduces manual monitoring workload |
Safety Systems | Prevents hazardous conditions | Enhances workplace safety |
3. Efficiency Gains from Modern Control Systems
A well-optimized control system reduces energy consumption, minimizes downtime, and improves fuel efficiency.
A. Fuel Efficiency Improvements
✅ Optimized combustion controls reduce excess air and unburned fuel losses.
✅ Heat recovery integration adjusts steam production based on demand.
B. Reduced Downtime and Maintenance Costs
✅ Predictive analytics detect minor faults before they cause failures.
✅ Automated scheduling ensures timely maintenance, preventing costly breakdowns.
C. Energy Savings Through Smart Load Management
✅ Adjusts boiler output based on real-time demand to reduce unnecessary fuel consumption.
✅ Integrates with smart grids to optimize energy use based on peak and off-peak hours.
Efficiency Factor | Benefit | Cost Savings |
---|---|---|
Combustion Optimization | Reduces fuel waste | 5-15% fuel cost reduction |
Predictive Maintenance | Prevents failures | 20-30% lower maintenance costs |
Load Management | Matches demand | Reduces excess fuel use |
4. Safety Enhancements with Smart Boiler Controls
Modern control systems integrate advanced safety features to prevent accidents and ensure operational stability.
A. Automatic Fault Detection and Alarms
✅ Detects leaks, pressure surges, and flame irregularities before they escalate.
✅ Triggers alarms and automated shutdowns to prevent accidents.
B. Redundancy and Backup Systems
✅ Failsafe mechanisms ensure continued operation during sensor malfunctions.
✅ Backup power and redundant controllers prevent system crashes.
C. Compliance with Safety Regulations
✅ Ensures adherence to OSHA, ASME, and NFPA codes for industrial boiler operation.
✅ Automated reporting tools simplify compliance documentation.
Safety Feature | Function | Impact on Risk Reduction |
---|---|---|
Automatic Fault Detection | Identifies issues early | Prevents explosions & shutdowns |
Redundancy Systems | Backup for critical functions | Ensures continuous operation |
Regulatory Compliance | Monitors safety standards | Avoids legal penalties |
5. Future Trends in Boiler Control Systems
The future of boiler control systems is driven by AI, automation, and digital twin technology.
A. AI-Powered Predictive Maintenance
✅ AI algorithms analyze data patterns to predict failures before they occur.
✅ Self-learning systems optimize fuel-to-air ratios based on historical performance.
B. Digital Twin Technology for Real-Time Simulation
✅ Creates a virtual model of the boiler to simulate efficiency and safety scenarios.
✅ Helps operators test control settings without risking real-world failures.
C. Cloud-Based Remote Monitoring & Blockchain Integration
✅ Allows global access to boiler performance data, enhancing multi-site management.
✅ Blockchain ensures secure data logging, preventing manipulation of operational records.
Innovation | Advantage | Implementation Impact |
---|---|---|
AI-Powered Analytics | Predicts failures | Reduces unplanned downtime |
Digital Twin Simulation | Tests scenarios safely | Improves operational training |
Cloud-Based Monitoring | Enables remote access | Enhances efficiency & reporting |
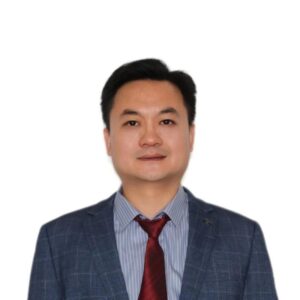