Choosing the right capacity and size of an industrial oil-fired boiler is crucial to ensuring efficient operations, energy cost savings, and system longevity. Many businesses either oversize their boilers—leading to wasted fuel and higher maintenance costs—or undersize them, resulting in inadequate heating, system stress, and downtime. Without a detailed assessment of process requirements and load conditions, selecting the wrong boiler capacity can negatively impact productivity and ROI.
The capacity and size of an industrial oil-fired boiler you need depend on factors such as your process steam or hot water demand (measured in kg/hr or BTU/hr), peak load requirements, operating pressure, fuel availability, system efficiency, and site space constraints. Boiler capacity should ideally match the maximum expected load with a small safety margin to avoid energy waste. Accurate sizing requires a professional load calculation considering production cycles, seasonal demand fluctuations, and future expansion plans.
Selecting the right boiler size requires a tailored approach based on your specific operational profile. Read on to learn how to determine the optimal configuration for your facility.
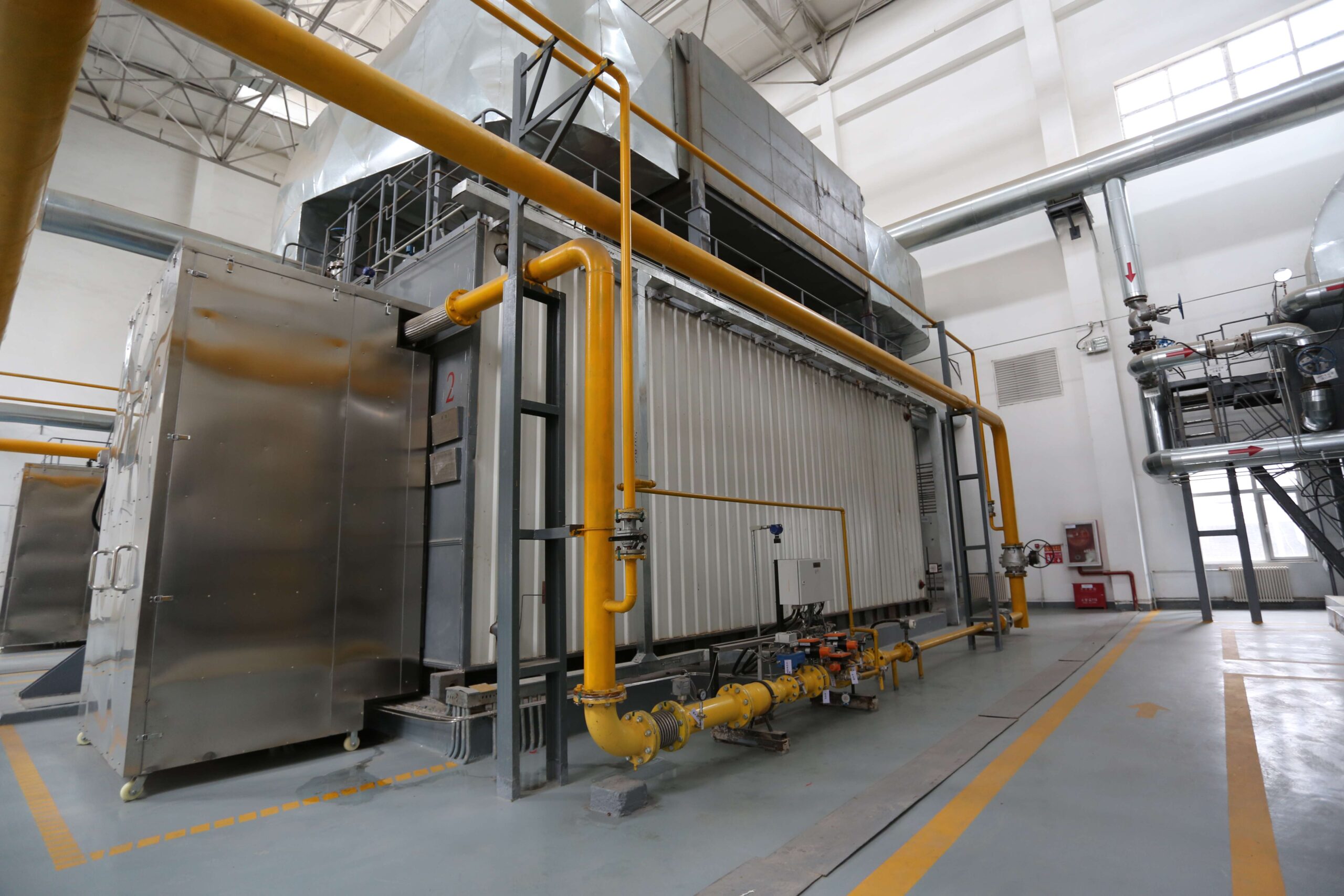
What factors determine the required capacity of an industrial oil-fired boiler?
Choosing the correct capacity for an industrial oil-fired boiler is essential to ensure that it delivers adequate steam or hot water for the intended processes without underperforming or wasting energy. If undersized, the boiler can cause production delays, equipment strain, and safety issues. If oversized, it may lead to energy inefficiencies, short cycling, and higher capital and operational costs. To strike the right balance, engineers must evaluate a combination of technical, operational, and environmental factors based on site-specific demands and boiler system characteristics.
The required capacity of an industrial oil-fired boiler is determined by factors such as total process steam or hot water demand, peak and average load requirements, operating pressure and temperature, type of industrial application, fuel calorific value, thermal efficiency of the boiler, system losses, and potential future expansion needs. Accurate capacity planning also considers daily and seasonal load variation, redundancy requirements, and compliance with safety and performance standards to ensure both energy efficiency and operational reliability.
Let’s explore each of these capacity-defining parameters in technical depth.
1. Total Heat or Steam Demand
The first and most important factor is the total energy or steam demand of the processes that the boiler will serve.
Process Type | Typical Steam Requirement Range (kg/h) |
---|---|
Food Processing | 500–15,000 |
Pharmaceutical Production | 1,000–20,000 |
Chemical Manufacturing | 2,000–50,000 |
Textile Dyeing | 1,500–25,000 |
Refining and Petrochemicals | 5,000–100,000+ |
Boiler capacity is usually rated in tons per hour (TPH) for steam or megawatts (MW) for hot water. A detailed heat balance of all thermal systems is typically conducted to define this value.
2. Peak vs. Average Load
Steam or thermal demand varies throughout the day or production cycle. Capacity should accommodate peak loads without consistently operating far below it.
Load Parameter | Impact on Boiler Size |
---|---|
Peak Load (Max Demand) | Sets minimum boiler capacity requirement |
Average Load | Affects fuel efficiency optimization |
Load Fluctuation Pattern | Determines if modulating or staged firing needed |
Oversizing by 10–25% for safety and reliability is common, but excessive oversizing leads to short-cycling and inefficiency.
3. Operating Pressure and Temperature
Higher steam pressure and temperature require more energy input, thus affecting boiler capacity selection.
Pressure Range | Steam Enthalpy (kcal/kg) | Capacity Adjustment |
---|---|---|
Low Pressure (≤10 bar) | ~660–690 | Baseline |
Medium (11–25 bar) | ~700–740 | +5–10% |
High (25–60 bar) | ~750–780 | +10–15% |
The boiler must generate not just volume, but the right energy level per kg of steam, impacting burner size and fuel flow rate.
4. Boiler Thermal Efficiency
Boiler efficiency significantly affects fuel-to-output conversion.
Efficiency (%) | Fuel Utilization | Capacity Impact |
---|---|---|
85% (standard oil) | Higher fuel input required | May oversize slightly |
90–93% (modern) | Optimized capacity | Closer match to demand |
>95% (condensing) | Maximum output per kg fuel | Smaller unit, lower cost |
Formula to estimate oil consumption:
Boiler Capacity (kg/h) = (Process Steam Demand in kg/h) ÷ Boiler Efficiency
5. Fuel Type and Calorific Value
Different grades of oil—such as LDO (Light Diesel Oil), HFO (Heavy Fuel Oil), or Kerosene—have different energy densities.
Fuel Type | Calorific Value (kcal/kg) |
---|---|
LDO | ~10,000–10,500 |
HFO | ~9,500–10,000 |
Kerosene | ~10,800–11,000 |
Lower CV fuels require higher input volumes, which may necessitate upsizing the burner and combustion chamber to meet demand.
6. Application Type and Process Continuity
Different industrial operations have unique duty cycles:
Application | Load Type | Capacity Implication |
---|---|---|
Batch Process (textile) | Cyclical | May need storage or rapid response |
Continuous Process | Steady | Base-load sizing ideal |
Redundant/Backup Role | Intermittent | Lower capacity or modular setup |
Continuous processes favor single large boiler, while variable operations may benefit from multiple smaller units (modular).
7. System Heat Losses
Losses through piping, blowdown, start-up purging, and radiation add to total capacity needs.
Loss Category | Typical Range (%) |
---|---|
Radiation Losses | 1–2% |
Blowdown | 2–5% |
Distribution Losses | 5–10% |
Total losses can add 10–15% to actual capacity demand, especially in large campuses or long pipe networks.
8. Redundancy and Future Scalability
Some operations require N+1 redundancy (one extra boiler on standby) for uninterrupted service.
Redundancy Requirement | Capacity Planning Strategy |
---|---|
No Redundancy | One boiler at full capacity |
N+1 Redundancy | Two or more units sharing total |
Expansion Anticipated | Design for 20–30% future increase |
Real-World Example: Textile Dyeing Plant in Turkey
Steam Requirement: 7,000 kg/h
Operating Pressure: 12 bar
Fuel: LDO
Process Type: Cyclical (3 shifts)
Efficiency: 89%
Blowdown and pipe losses: 10%
Calculated Boiler Capacity:
(7,000 kg/h ÷ 0.89) × 1.10 (losses) ≈ 8,653 kg/h → Rounded to 9 TPH
Chosen configuration:
Two 5 TPH oil-fired boilers (N+1 setup for flexibility)
Summary: Key Capacity Planning Factors for Oil-Fired Boilers
Factor | Role in Sizing the Boiler Unit |
---|---|
Total Steam/Heat Demand | Primary determinant of output capacity |
Peak vs. Average Load | Affects burner modulation and system stability |
Operating Pressure/Temperature | Impacts enthalpy and required energy input |
Boiler Efficiency | Defines how much fuel converts into usable output |
Fuel Calorific Value | Determines burner sizing and oil flow requirements |
Process Type | Batch vs. continuous changes thermal load pattern |
System Losses | Adds reserve capacity for reliability |
Redundancy/Future Growth | Influences modular vs. oversize boiler selection |
A precise capacity calculation ensures operational efficiency, safety, and lifecycle economy, making it a critical step in any industrial oil-fired boiler installation or upgrade.
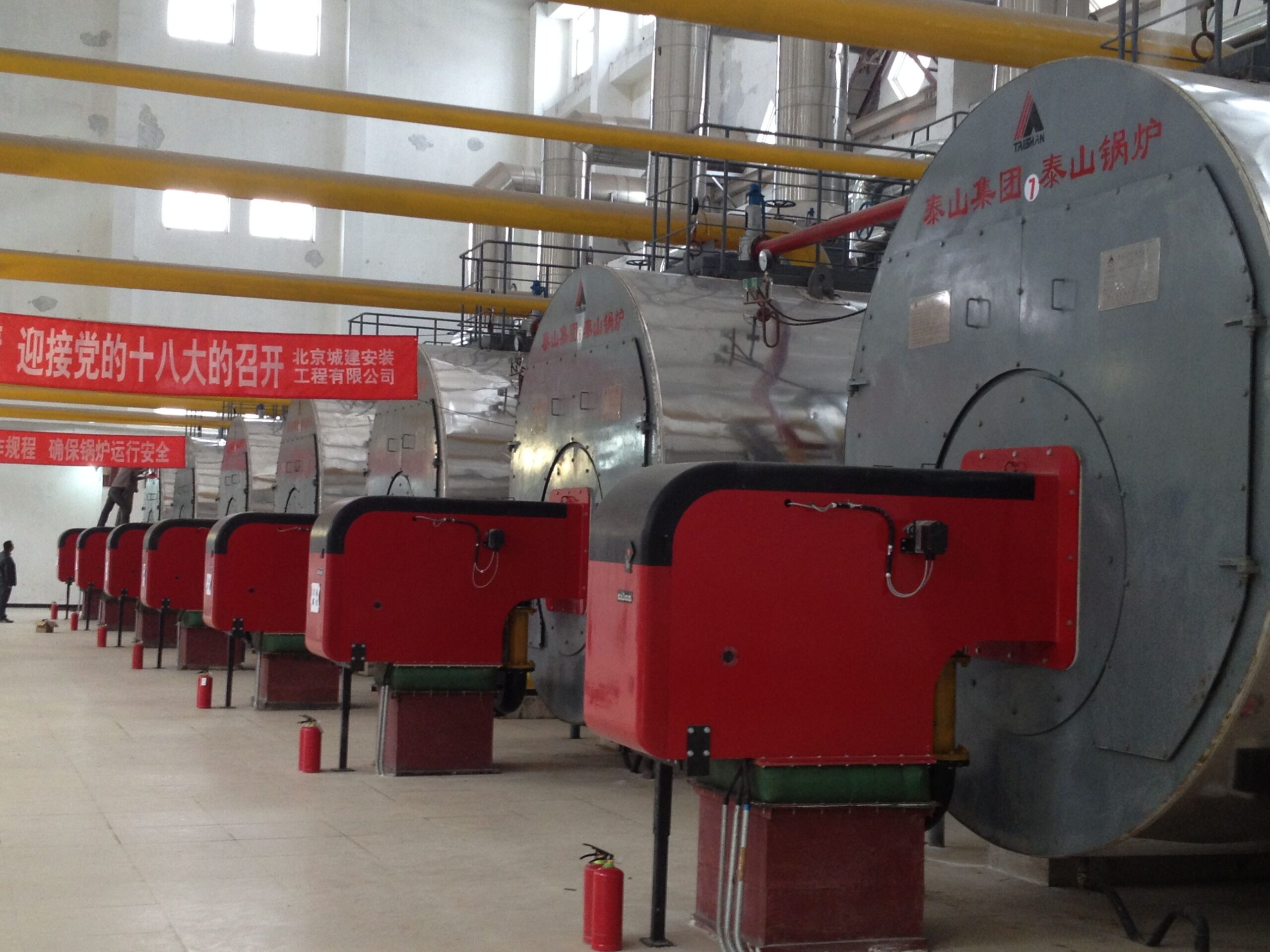
How do you calculate boiler size based on steam or hot water demand?
Selecting the right size for a steam or hot water boiler is crucial to ensure reliable, efficient, and cost-effective thermal energy delivery. An undersized boiler may struggle to meet peak demand, resulting in process disruptions or safety risks. Conversely, an oversized boiler can lead to poor fuel efficiency, short cycling, and unnecessary capital expenditure. Proper sizing begins with a precise assessment of the actual energy demand, and applies proven thermodynamic formulas and system-specific adjustments.
Boiler size is calculated based on the total heat or steam demand of the processes it serves. For steam boilers, the required size is determined by calculating the total mass flow of steam (usually in kg/h or TPH), factoring in enthalpy requirements, boiler efficiency, and system losses. For hot water boilers, sizing is based on the required thermal output (in kW or BTU/hr), calculated from flow rate and temperature rise. Adjustments are made for peak demand, operating pressure, and expected system losses to ensure reliable performance under all conditions.
Let’s walk through the calculation process step-by-step for both steam and hot water systems.
🔹 Part 1: Sizing for Steam Boilers
Step 1: Determine Process Steam Requirement
Estimate or measure the total steam load needed across all equipment, usually in kg/h (kilograms per hour).
Formula (Total Steam Load):
Total Steam Load (kg/h) = Σ Steam required by all processes/equipment
Example:
Autoclave: 1,200 kg/h
Heat exchangers: 3,000 kg/h
Cleaning/CIP: 800 kg/h
Total Steam Demand = 5,000 kg/h
Step 2: Factor in Boiler Efficiency
The boiler cannot convert 100% of input fuel to steam. Adjust steam output to account for efficiency losses.
Formula:
Required Boiler Output (kg/h) = Total Steam Demand ÷ Boiler Efficiency
Assumption: Boiler Efficiency = 88% (0.88)
5,000 ÷ 0.88 = 5,681.8 kg/h
Step 3: Account for System Losses (Piping, Blowdown, Radiation)
Add 10–15% to account for:
Pipe heat losses
Boiler blowdown
Steam trap and valve inefficiencies
Final Capacity = Required Output × 1.10 (for 10% loss)
5,681.8 × 1.10 = 6,250 kg/h
✅ Final Boiler Size = 6,250 kg/h (≈6.25 TPH)
You may round up to the nearest standard boiler rating—e.g., select a 7 TPH steam boiler for redundancy and future growth.
🔹 Part 2: Sizing for Hot Water Boilers
Step 1: Determine Flow Rate and Temperature Rise
Hot water boiler output is based on heating water from an inlet to outlet temperature at a certain flow rate.
Formula (kW):
Q (kW) = m × Cp × ΔT
Where:
Q = Boiler capacity in kilowatts
m = Flow rate in kg/s (1 L/s ≈ 1 kg/s for water)
Cp = Specific heat of water ≈ 4.18 kJ/kg°C
ΔT = Temperature rise (°C)
Example:
Flow: 10,000 liters/hour = 2.78 L/s
Inlet temp: 60°C
Outlet temp: 90°C
ΔT = 30°C
Q = 2.78 × 4.18 × 30 ≈ 349.6 kW
Step 2: Factor in Boiler Efficiency
Net Boiler Size = Q ÷ Efficiency
349.6 ÷ 0.88 ≈ 397.3 kW
Step 3: Add System Losses (Optional)
Add 10% for losses:
397.3 × 1.10 = 437.1 kW
✅ Final Boiler Size = ~440 kW hot water boiler
🔹 Boiler Sizing Quick Reference Table
Application | Common Sizing Unit | Typical Range |
---|---|---|
Small Food Plant (Steam) | kg/h or TPH | 500–2,000 kg/h (0.5–2 TPH) |
Textile Factory (Steam) | kg/h or TPH | 3,000–10,000 kg/h |
Large Factory (Hot Water) | kW or MW | 300 kW – 2 MW |
District Heating | kW or MW | 500 kW – 10 MW+ |
🔹 Other Considerations in Boiler Sizing
Factor | Impact on Size |
---|---|
Peak Load vs. Average Load | Determines turndown or modular design |
Modulating vs. Staged Burner | Improves efficiency under variable demand |
Future Expansion | Consider oversizing or modular design |
Altitude and Ambient Temp | Affects combustion efficiency and output |
Standby Redundancy (N+1) | May require multiple boilers or larger unit |
Real-World Case Study: Dairy Processing Plant
Steam required: 8,000 kg/h
Operating pressure: 10 bar
Boiler efficiency: 90%
Piping/blowdown losses: 12%
8,000 ÷ 0.90 = 8,889
8,889 × 1.12 = 9,955 → Rounded to **10 TPH boiler**
Summary: Key Steps to Accurately Size a Boiler
Step | Action |
---|---|
1. Assess Thermal Demand | Measure total steam or hot water need |
2. Adjust for Efficiency | Factor in typical boiler thermal efficiency |
3. Include Losses | Add margin for piping, radiation, and blowdown |
4. Factor Process Type | Consider batch vs. continuous and seasonal demand |
5. Add Safety/Expansion | Include future growth or install modular systems |
Correctly sizing your boiler ensures maximum efficiency, minimal downtime, and long-term operational savings, making it a cornerstone decision in any industrial thermal energy project.
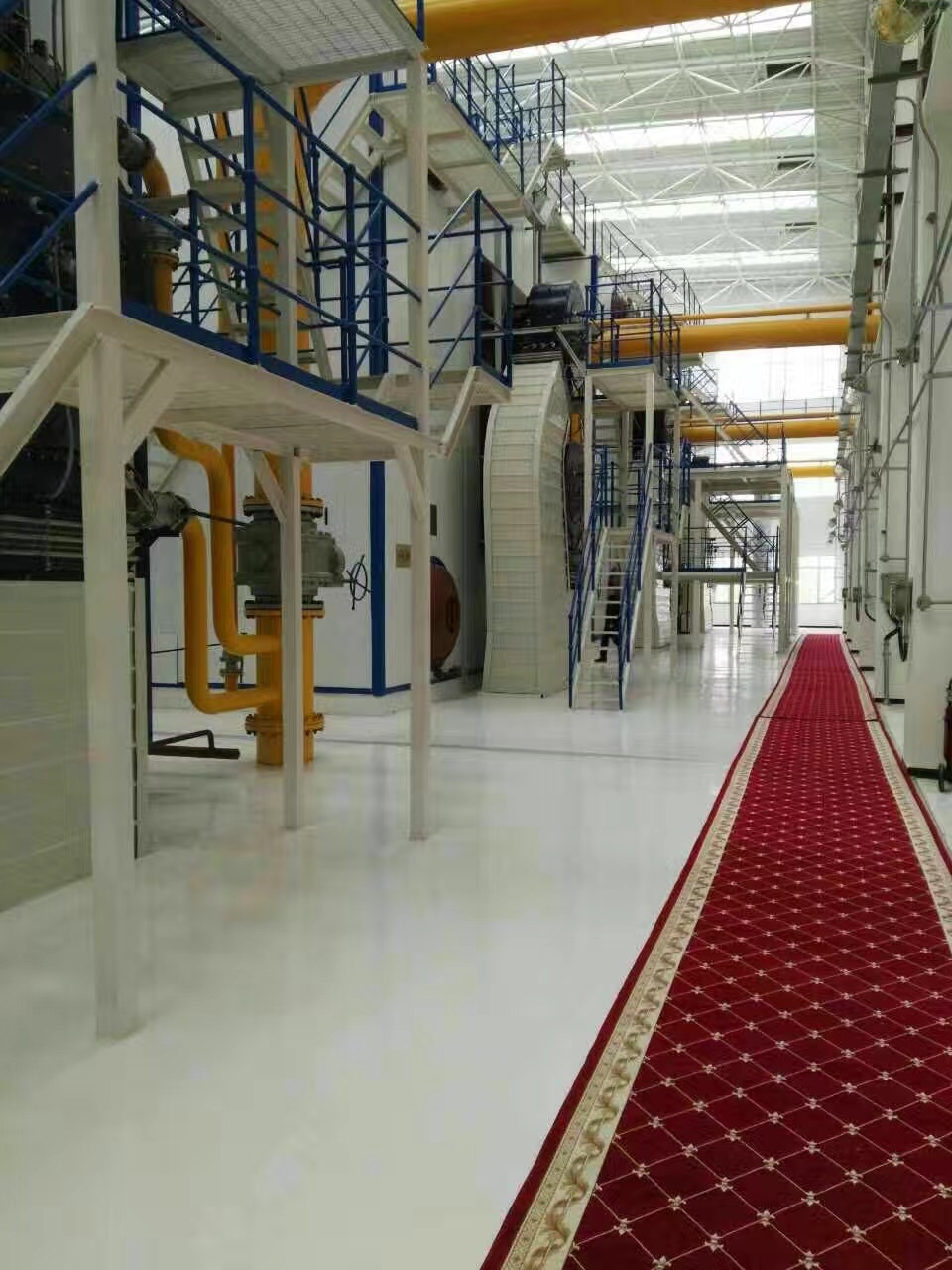
What is the difference between rated capacity and actual load demand?
When selecting or evaluating an industrial boiler, it is essential to distinguish between rated capacity and actual load demand—two terms that define how a boiler is designed to operate versus how it operates in real-world conditions. Misunderstanding or overlooking this distinction can lead to system oversizing, underutilization, operational inefficiencies, or even reliability issues. Engineers, operators, and plant managers must assess both parameters to ensure the boiler performs efficiently, economically, and safely.
Rated capacity is the maximum output a boiler is engineered to deliver under standardized operating conditions—typically measured in kg/h, TPH, or kW—while actual load demand refers to the real, fluctuating thermal or steam requirement of the facility based on process needs, time of day, season, or production cycle. Rated capacity is a fixed design specification, whereas actual demand varies and is influenced by operational behavior. The mismatch between these two values affects fuel efficiency, boiler cycling, emissions, and total operating cost.
Understanding both parameters enables optimal boiler sizing, energy management, and system control.
🔹 1. What is Rated Capacity?
Rated capacity (also known as nominal capacity or design output) is the maximum output the boiler can safely and continuously provide under specified design conditions.
Parameter | Description |
---|---|
Units | kg/h, tons per hour (TPH), kW, or BTU/hr |
Basis | 100% full-load operation at rated pressure and temperature |
Defined By | Boiler manufacturer and certification standards |
Use Case | Used in specification sheets, procurement, and sizing |
Example:
A boiler rated at 6 TPH at 10 bar pressure means it can produce 6,000 kg of steam per hour at the designed pressure continuously.
🔹 2. What is Actual Load Demand?
Actual load demand refers to the real-time or average requirement for thermal energy or steam as driven by production processes or building operations.
Parameter | Description |
---|---|
Units | kg/h (steam), kW (hot water), or % of rated capacity |
Basis | Measured during real operation (daily, hourly, seasonal) |
Use Case | Used in performance analysis, control logic, fuel budgeting |
Example:
If a 6 TPH boiler operates at 3 TPH for most of the day, then actual load demand is 50% of the rated capacity.
🔹 3. Key Differences Overview
Aspect | Rated Capacity | Actual Load Demand |
---|---|---|
Definition | Boiler’s maximum continuous output | Real-time energy or steam requirement |
Determination | Fixed by design and certification | Varies by process, time, and season |
Usage in Engineering | For system sizing, procurement | For control strategy, fuel planning |
Flexibility | Fixed | Dynamic and variable |
Measurement | Static (nameplate rating) | Real-time (meters, sensors, DCS) |
🔹 4. Why the Difference Matters
A. Oversized Boilers (Rated capacity >> actual demand)
Low efficiency due to cycling and incomplete combustion
Increased fuel consumption per kg of steam
Shorter equipment lifespan (more start-stops)
Underutilized investment
B. Undersized Boilers (Rated capacity << peak demand)
Inability to meet process load during peak times
Production interruptions or safety trips
Overheating and pressure instability
Accelerated wear due to overloading
🔹 5. How to Balance the Two for Efficiency
Strategy | Description |
---|---|
Turn-down Ratio Consideration | Choose a boiler with a wide modulation range |
Modular Boiler Systems | Multiple smaller units to match varying loads |
Load Profiling and Logging | Measure actual demand over time for better sizing |
Boiler Controls Optimization | Match firing rate with real-time demand |
Thermal Storage Integration | Buffering to smooth load spikes |
Real-World Example: Food Processing Plant
Boiler rated capacity: 8 TPH
Average actual demand: 4.5 TPH
Peak demand: 6.8 TPH
Actual usage profile: 40% of time at 60% load, 40% at 80% load, 20% at full load
Outcome:
Boiler often runs below efficient range
Proposed change: switch to 2 x 4 TPH modular system with one in standby
Summary: Rated Capacity vs. Actual Load Demand
Comparison Area | Rated Capacity | Actual Load Demand |
---|---|---|
Fixed or Variable | Fixed (design spec) | Variable (usage-based) |
Measured or Stated | Nameplate value | Monitored with flow and pressure data |
Role in Planning | Used for initial sizing | Used for operational tuning |
Efficiency Implication | Defines maximum efficiency potential | Affects real-world efficiency |
Best Practice | Design with margin (10–20%) | Monitor and match with control systems |
To operate at peak efficiency and reliability, boiler systems must be sized for rated capacity that closely matches actual demand, with built-in flexibility to manage fluctuations—ensuring that capital investment is right-sized and energy performance is optimized.
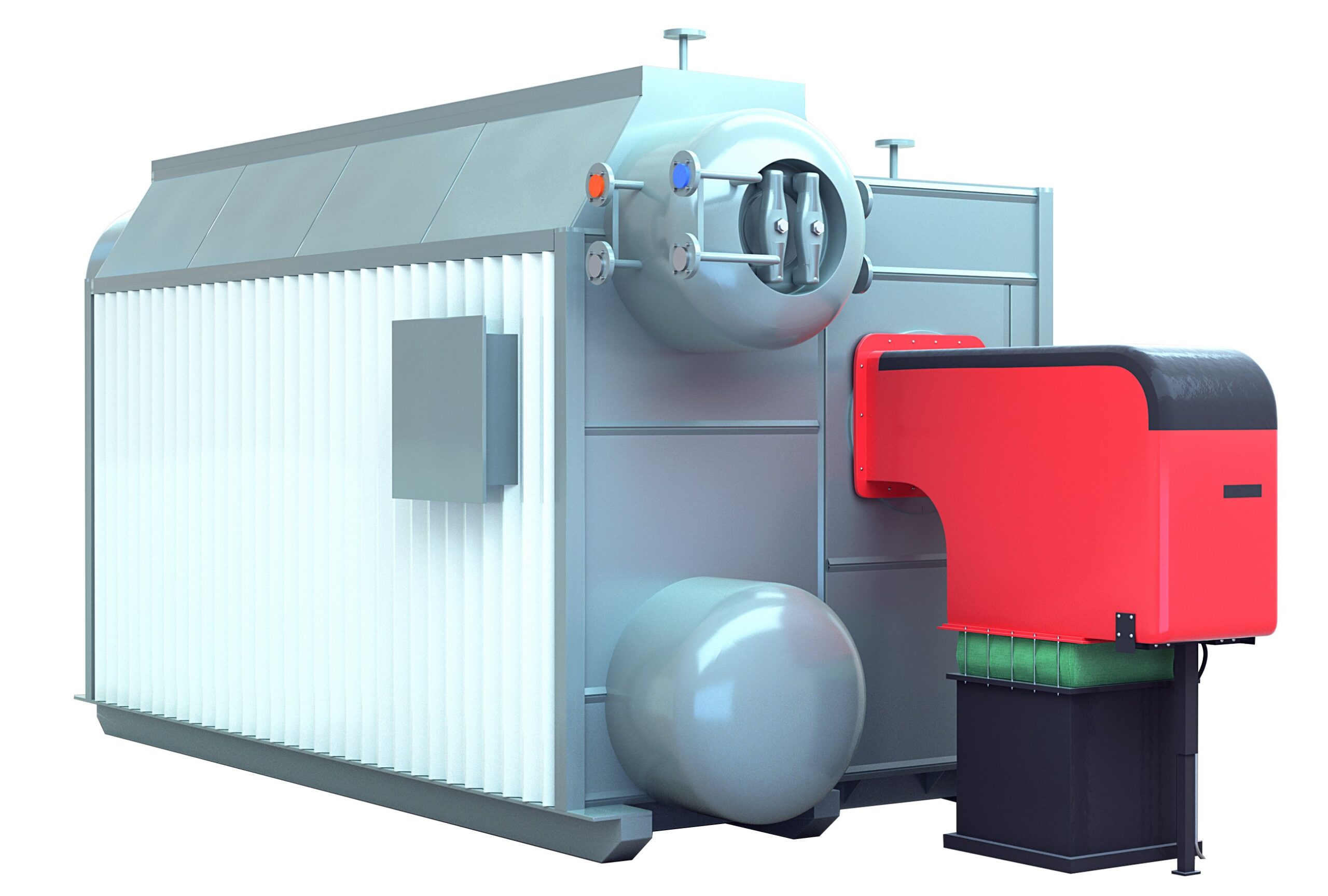
Why is boiler turndown ratio important for capacity selection?
When selecting a boiler for an industrial application, capacity is just one part of the equation. Another critical performance metric that is often overlooked—but highly influential—is the turndown ratio. This value determines how effectively a boiler can adjust its output to match real-time demand. A poorly matched turndown ratio can lead to inefficient cycling, energy waste, wear and tear, and higher fuel costs. Conversely, a properly chosen turndown ratio allows the boiler to modulate output precisely, keeping efficiency high across variable load profiles.
The turndown ratio of a boiler is important for capacity selection because it indicates how well the boiler can reduce its firing rate in response to lower steam or heat demands. A high turndown ratio allows the boiler to operate efficiently at both full and partial loads without frequent cycling, maintaining stable temperatures, minimizing fuel waste, and reducing mechanical stress. When selecting boiler capacity, understanding turndown ratio ensures that the system can adapt to real-world load fluctuations while delivering optimal performance and efficiency.
Let’s explore why this metric is crucial and how it influences boiler system design and sizing.
🔹 What is Turndown Ratio?
The turndown ratio is the ratio between a boiler’s maximum and minimum stable firing rate.
Formula:
Turndown Ratio = Maximum Firing Rate ÷ Minimum Firing Rate
Turndown Ratio | Meaning |
---|---|
10:1 | Boiler can reduce to 10% of full output |
5:1 | Minimum output is 20% of full capacity |
3:1 | Boiler modulates down to 33% |
Example:
A 6 TPH boiler with a 5:1 turndown ratio can operate from 6 TPH down to 1.2 TPH without cycling.
🔹 Why Does Turndown Ratio Matter?
1. Matches Variable Load Demand
In most industrial environments, thermal load is not constant—it fluctuates based on:
Time of day
Process batch cycles
Equipment operation schedules
Seasonal variation
A boiler with a limited turndown can only operate efficiently at high loads. At lower demand, it may:
Short cycle (on/off frequently)
Overshoot pressure or temperature
Consume excess fuel during start-up purges
2. Improves Fuel Efficiency
When a boiler must shut down and restart repeatedly:
Pre-purge blows heated air out
Reheating the furnace uses extra fuel
Combustion conditions become inconsistent
A high turndown ratio keeps the boiler running longer at lower loads, minimizing these inefficiencies.
3. Reduces Equipment Wear
Frequent cycling causes:
Repeated thermal expansion/contraction of parts
Stress on control systems
More frequent service intervals
Higher turndown reduces mechanical wear and extends component lifespan (especially for burners and refractory).
🔹 Typical Turndown Ratios by Boiler Type
Boiler Type | Typical Turndown Ratio | Comments |
---|---|---|
Industrial Gas/Oil (modulating burner) | 5:1 to 10:1 | Standard for high-performance systems |
On/Off Fire Tube | 1:1 | No modulation; inefficient for low loads |
Dual-stage Burners | 2:1 or 3:1 | Limited steps—better than on/off |
High-Turndown Condensing | 10:1 to 15:1 | Ideal for broad load ranges |
🔹 Impact on Boiler Capacity Selection
When Turndown is Too Low:
Boiler must be oversized to meet peak, but performs poorly at low load
Frequent cycling during off-peak hours
Fuel waste and increased emissions
When Turndown is High Enough:
Boiler modulates to match load without stopping
Consistent combustion quality
Maintains design efficiency across operating range
🔹 Real-World Example: Textile Dyeing Plant
Peak steam demand: 6 TPH
Off-peak average demand: 2 TPH
Selected boiler: 6 TPH unit with 3:1 turndown
Min output: 2 TPH — barely meets off-peak without cycling
📌 Upgrade to 5:1 turndown allows stable operation down to 1.2 TPH →
Result:
8% improvement in fuel efficiency
50% reduction in burner startups
ROI on modulating burner: <1.5 years
🔹 Summary: Importance of Turndown Ratio in Capacity Planning
Design Consideration | Turndown Ratio Impact |
---|---|
Load Variability | Handles fluctuations without performance drop |
Energy Efficiency | Reduces cycling and purge losses |
Equipment Longevity | Prevents wear from frequent shutdowns |
Safety and Control Stability | Maintains consistent pressure and temperature |
System Flexibility | Allows better matching of load profiles |
Selecting a boiler with the right turndown ratio is as important as choosing the right capacity. It ensures the boiler runs efficiently and reliably across the full spectrum of demand—maximizing performance and minimizing cost over its operational lifetime.
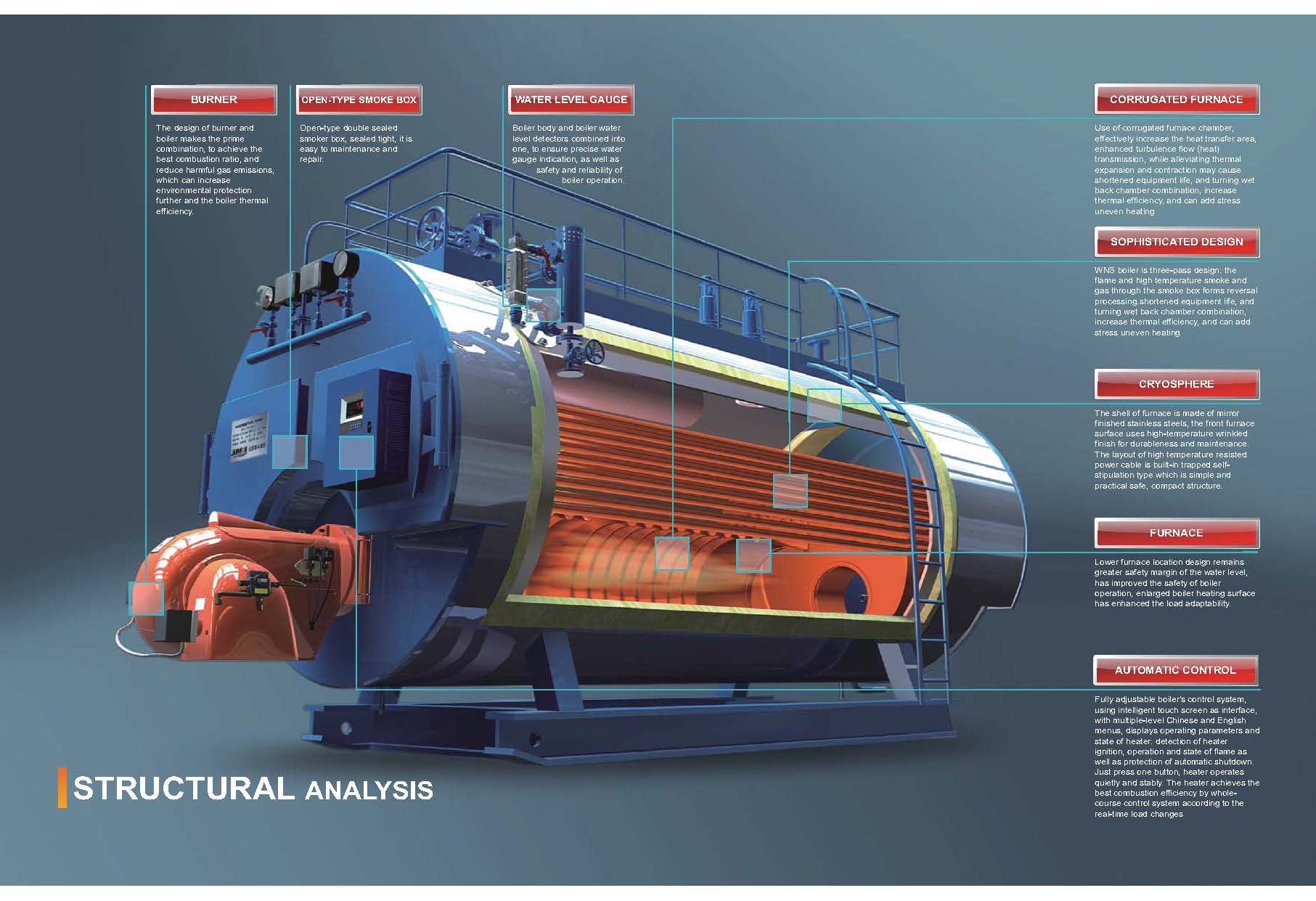
How does future expansion affect boiler sizing decisions?
Boiler systems are a long-term investment—often designed to operate reliably for 20–30 years or more. During this time, most industrial operations undergo significant changes: increased production capacity, new process lines, seasonal demand growth, or expansion into additional facilities. If the boiler is not sized with this in mind, future growth may require costly retrofits, shutdowns, or complete replacements. Therefore, boiler sizing must account not only for current demand but also for expected growth trajectories in both output and operational complexity.
Future expansion affects boiler sizing decisions by requiring additional capacity reserves, modular system flexibility, or space allocation to accommodate growing steam or thermal demand without compromising efficiency or safety. Incorporating potential growth into the initial design ensures the boiler system can scale with operational needs, avoiding premature obsolescence, oversized upfront investments, or costly system overhauls. Strategic planning includes installing extra capacity margin, designing for modular expansion, and configuring control systems to manage future load additions effectively.
Let’s explore how to plan boiler sizing for both present performance and future scalability.
🔹 Why Is Planning for Expansion Important?
Factor | Risk Without Expansion Planning |
---|---|
Business Growth | Boiler undersized for new product lines |
Production Volume Increases | Steam/hot water shortfall during peak loads |
Utility Grid Changes | Need for on-site power generation (CHP) |
Energy Policy Adjustments | Missed opportunity for renewable integration |
Facility Additions | Retrofit complications and costly shutdowns |
Boiler systems that lack scalability can quickly become performance bottlenecks.
🔹 Key Strategies for Boiler Sizing with Future Growth in Mind
1. Capacity Margin Addition (Over-Sizing)
One approach is to add a percentage buffer over current demand:
Growth Type | Recommended Capacity Margin |
---|---|
Stable operations | +10–15% |
Moderate expansion expected | +20–30% |
Aggressive growth plans | +30–50% or modular configuration |
Example:
Current demand: 5 TPH
Anticipated growth: 20% in 3 years
Boiler sized for 6 TPH minimum, or 7 TPH for safety and optimization
✅ Pros:
No additional installation needed
Simple control and piping layout
❌ Cons:
Lower efficiency at partial load
Higher upfront investment
2. Modular Boiler Design
Instead of a single large boiler, install multiple smaller units that can be added or rotated based on demand.
Configuration | Flexibility Benefit |
---|---|
2 × 4 TPH boilers | Starts with 1 unit, adds 2nd as needed |
3 × 3 TPH boilers | Redundancy, load sharing, expand easily |
Skid-mounted or containerized units | Scalable with plug-and-play installation |
✅ Pros:
High turndown ratio
Redundancy and reliability
Matches seasonal or batch operations
❌ Cons:
Higher complexity in controls and layout
3. Infrastructure Pre-Design
Even if only one boiler is installed initially, piping, wiring, and floor space can be laid out for future boilers.
Infrastructure Element | Scalable Planning Strategy |
---|---|
Steam header | Oversize to support future flow volumes |
Fuel line and tanks | Include ports and sizing for extra burners |
Control system | Choose PLC/DCS with modular I/O capability |
Foundation and floor space | Allow room for future boiler modules |
🔹 Real-World Scenario: Dairy Expansion Plan
Current Production:
6 TPH steam demand
Future Plan:New pasteurization line to add 3 TPH in 2 years
Initial Setup:
Install 2 × 5 TPH boilers
Only one operates at start, second added as needed
Controls designed for full-load automation across both units
Results:
12% lower energy use during startup phase
Expansion implemented in <48 hours without shutdown
Payback time shortened by avoiding costly system redesign
🔹 Tools for Planning Future Load
Tool or Methodology | How It Helps |
---|---|
Load Profiling Studies | Predict future demand based on production trends |
Process Simulation | Models new lines and energy impact |
GIS and P&ID Design Tools | Plan physical layout for scalability |
SCADA/PLC Data Monitoring | Real-time load trends inform when to expand |
Summary: Future Expansion’s Role in Boiler Sizing
Planning Element | Impact on Boiler System Design |
---|---|
Expected Growth Rate | Drives margin or modular planning |
Load Curve Shape | Influences need for redundancy or high turndown |
Infrastructure Scalability | Reduces future retrofit costs and downtime |
Modular vs. Single Unit | Defines flexibility for staged commissioning |
Control System Design | Enables future integration of new capacity seamlessly |
Planning for future expansion ensures your boiler investment is long-term-ready, cost-effective, and operationally flexible. A boiler system built for today and tomorrow supports business continuity, energy optimization, and strategic growth.
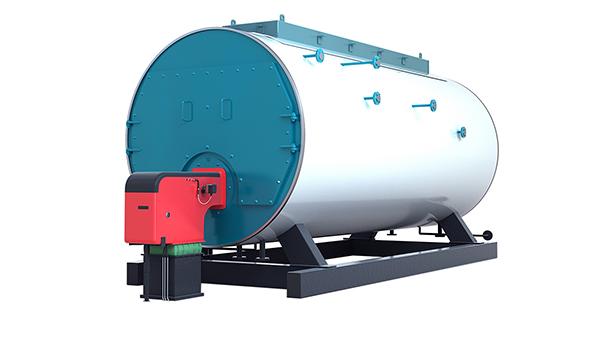
What physical space and installation considerations should be factored into sizing?
When planning for the installation of an industrial boiler, selecting the correct output capacity is just one part of the equation. The physical space and installation environment are equally crucial for ensuring safe, efficient, and maintainable operation. A boiler system that’s too large for its space can cause layout bottlenecks, safety violations, access issues, and increased installation costs, while an improperly installed unit—regardless of capacity—can lead to reduced performance and compliance risks. For long-term success, the boiler must not only fit its thermal role, but also its mechanical and spatial context.
Physical space and installation considerations that must be factored into boiler sizing include floor space availability, ceiling height, required clearances for maintenance and access, structural support, flue gas venting pathways, fuel storage and delivery zones, piping layout, ventilation requirements, and room for future expansion. A boiler’s footprint, burner protrusions, auxiliary equipment, and safety zones must all be coordinated with the building’s architectural and engineering constraints to ensure safe, code-compliant, and service-friendly installation.
Here’s a detailed breakdown of the spatial and installation planning factors that impact boiler sizing and selection.
🔹 1. Boiler Footprint and Dimensions
Each boiler has a defined length × width × height, typically specified by the manufacturer based on capacity and type.
Capacity Range | Approx. Boiler Footprint (L×W) |
---|---|
1–2 TPH (small shell type) | ~2.5 m × 1.5 m |
3–6 TPH (medium industrial) | ~4.5 m × 2.5 m |
10–20 TPH (large firetube or water tube) | ~7–12 m × 3–5 m |
Include space for:
Burner (may protrude up to 1 m)
Front/rear access doors
Ash or blowdown handling equipment
Ancillary systems (pumps, deaerators, feed tanks)
🔹 2. Clearances for Access and Maintenance
Boiler maintenance requires unobstructed access for personnel and tools.
Component | Minimum Recommended Clearance |
---|---|
Front (burner side) | 1.5–2.0 m (burner access and removal) |
Rear (manhole or door) | 1.0–1.5 m |
Sides | 0.8–1.2 m |
Top | 1.5 m (for lifting, piping, inspection) |
Failing to provide sufficient clearance can:
Delay servicing
Invalidate warranties
Create safety hazards
🔹 3. Floor Load and Structural Support
Larger boilers may weigh 10–60 tons or more when filled with water.
Boiler Capacity | Approx. Operating Weight |
---|---|
5 TPH fire-tube | 8–12 tons |
10 TPH water-tube | 18–25 tons |
20+ TPH multi-drum | 40–60+ tons |
Floor must:
Support static and dynamic loads
Be reinforced concrete (≥3000 psi)
Accommodate vibration isolation pads
🔹 4. Utility and Piping Layout
Boiler sizing influences the volume of steam/water/fuel being handled, which directly impacts:
Utility | Installation Requirement |
---|---|
Fuel lines | Correct diameter and pressure regulation |
Steam headers | Sized for peak flow, low-pressure drop |
Condensate return | Must accommodate return lag volume |
Feedwater tanks | Scaled with TPH + redundancy buffer |
Larger capacity boilers often require dual feedwater lines, separate softeners, and higher head pumps.
🔹 5. Flue Gas Venting and Chimney Sizing
More capacity = higher flue gas volumes.
Boiler Capacity | Approx. Chimney Diameter Range |
---|---|
1–2 TPH | 250–400 mm |
5 TPH | 500–700 mm |
10+ TPH | 800–1200 mm |
Venting considerations:
Horizontal space for economizer and ductwork
Vertical clearance (≥3 m above roofline)
Access platform for stack inspections
🔹 6. Combustion Air and Ventilation
Larger boilers require forced draft fans and sufficient intake air.
Requirement | Sizing Rule |
---|---|
Combustion air volume | ~15 m³ of air per kg of fuel burned |
Room ventilation openings | 1:1 ratio with air demand (with backup fan) |
Louver placement | Inlet at low level, outlet high for draft |
Poor ventilation causes:
Incomplete combustion
Overheating
Safety hazards (CO buildup)
🔹 7. Fuel Storage and Delivery
For oil or biomass boilers, installation space must include:
Fuel Type | Storage Requirement |
---|---|
Fuel Oil (HFO/LDO) | Bunded storage tanks + day tank (1–2 m³) |
Wood Chips | Hopper + conveyor or auger system |
Pellets | Silo or bag feed system |
Also consider:
Tank refilling truck access
Leak containment and fire zoning
🔹 8. Future Expansion Provisions
If sizing with future load growth in mind, allow:
Expansion Element | Installation Preparation |
---|---|
Space for second boiler | Minimum 50–100% floor reserve |
Header connection ports | Stubbed or valved connections |
Electrical control panels | Modular PLC with open capacity |
🔹 9. Compliance with Codes and Safety Standards
Ensure layout adheres to:
NFPA 85 (USA) or BS EN 12952/12953 (EU) for boiler safety
OSHA access and egress standards
Local fire separation distances
Emergency stop and fire suppression systems
Real-World Installation Plan: Manufacturing Plant
Boiler Requirement:
8 TPH oil-fired steam boiler
Available Room Dimensions:12 m × 6 m × 5 m ceiling
Key Considerations:Boiler footprint: 5.5 m × 2.8 m
Burner protrusion: 0.8 m
Access doors: Front 1.8 m, sides 1.0 m
Chimney to rooftop via adjacent wall
2 m reserved for future 4 TPH modular boiler
Final Layout:
One corner reserved for fuel tanks
Electrical control panel wall-mounted
Expansion-ready skid and header in place
Fire extinguisher system compliant with NFPA 86
Summary: Space & Installation Factors in Boiler Sizing
Consideration Area | Key Design Actions |
---|---|
Footprint & Dimensions | Match boiler size with physical floor space |
Maintenance Access | Reserve clearance for servicing and inspection |
Structural Support | Reinforce floors for weight and vibration |
Piping & Utilities | Design headers and fuel lines for flow and future use |
Ventilation & Chimney | Ensure airflow and exhaust are safely routed |
Fuel Storage & Handling | Integrate with system footprint and delivery access |
Compliance & Safety | Meet codes, fire safety, and emergency protocols |
Scalability | Leave room and interfaces for capacity expansion |
Properly factoring in physical space and installation constraints during boiler sizing prevents future operational headaches, enhances safety, and maximizes long-term return on investment—ensuring your boiler system is not only powerful, but also practical.
🔍 Conclusion
Correctly sizing your industrial oil-fired boiler is key to maximizing efficiency, minimizing fuel consumption, and ensuring reliable performance. By considering actual load profiles, peak demands, turndown ratios, and potential future needs, you can avoid common pitfalls associated with over- or under-sizing. A well-sized boiler not only delivers optimal energy output but also extends equipment life and reduces total cost of ownership.
📞 Contact Us
💡 Need help selecting the right boiler capacity for your facility? Our engineering team provides expert assessments to ensure you choose a boiler system that perfectly fits your operational needs.
🔹 Contact us today to get a custom boiler sizing consultation for your industry! ⚙️🔥
FAQ
How do you determine the capacity of an industrial oil-fired boiler?
Boiler capacity is typically determined based on the required steam output or thermal load of the industrial process. It’s measured in tons/hour (TPH) for steam or BTU/hr for thermal energy, and should match or slightly exceed peak demand to ensure efficiency and reliability.
What factors affect the sizing of an oil-fired boiler?
Key factors include the process heating requirement, number of connected systems, steam pressure needs, feedwater temperature, ambient conditions, and expected operating hours.
What is the typical capacity range for industrial oil-fired boilers?
Industrial oil-fired boilers commonly range from 0.5 TPH to 50 TPH for steam applications, and from 0.3 million to over 100 million BTU/hr for hot water systems, depending on application scale.
Why is correct boiler sizing important?
An undersized boiler can’t meet demand, causing inefficiencies and downtime. An oversized boiler wastes energy, operates at reduced efficiency, and increases fuel costs and emissions. Correct sizing ensures optimal performance and cost-effectiveness.
Can boiler capacity be customized for specific applications?
Yes, manufacturers can custom design boilers based on unique operational needs such as low or high-pressure steam, modular capacity, fuel variations, or space limitations. Consulting with an engineer is advised for precise calculations.
References
Boiler Sizing and Selection Guide – https://www.energy.gov
Steam Boiler Capacity Calculation – https://www.sciencedirect.com
Industrial Heating Load Estimation – https://www.researchgate.net
Choosing the Right Industrial Boiler – https://www.bioenergyconsult.com
Oil-Fired Boiler Capacity Range – https://www.epa.gov
Hot Water Boiler Sizing Tips – https://www.energysavingtrust.org.uk
Boiler Efficiency and Fuel Consumption – https://www.mdpi.com
Industrial Boiler System Design – https://www.iea.org
Best Practices for Boiler Sizing – https://www.automation.com
Oil Boiler Installation & Sizing – https://www.sciencedirect.com
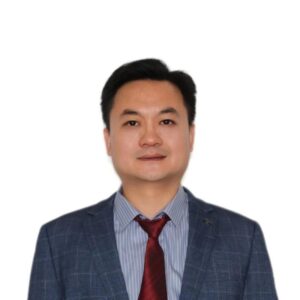